【失敗しない!中国ものづくり|第12回】QC工程表に無いところで発見される不良原因
これまでの連載記事
- 第1回:『中国での不良品やトラブルの原因は60%日本人にあり』
- 第2回:『中国人の「問題ない」に潜む3つの意味』
- 第3回:『勝手に変更される金型』
- 第4回:『「機能するから問題ない」の品質感覚』
- 第5回:『「専門学校を出ています」「検査するから問題ない」と言い切る中国人』
- 第6回:『市場で突然割れ始めた液晶モニターのリアカバー』
- 第7回:『市場で突然発生したスポット溶接剥離』
- 第8回:『20%は通じていない!?日本語通訳との会話』
- 第9回:『中国メーカーに確実に伝える情報の出し方』
- 第10回:『春節だけで15%の作業者の入れ替わる製造ライン』
- 第11回:『製造ラインで確認を忘れがちな2つのコト』
- 第12回:『QC工程表に無いところで発見される不良原因』
先回のコラムでは、設備の設定値の確認と作業者の作業順の確認が重要性であることについてお伝えしました。今回は、QC工程表に記載されていないところで発見される不良の原因に関してお伝えします。
仕掛かり中部品の工程間運搬
アルミの押出材で出来た液晶テレビのベゼル(外枠)に細い線状のキズが発生する問題がありました。かなり小さいOKレベルのものがほとんどでしたが、不良率が上がったり不良品レベルが出荷されたりしてしまう可能性もあるため調査することになりました。
この部品は一直線上の押出材の受け入れ検査から始まり、数工程にわたる曲げ加工→研磨→アルマイト処理→数工程の組立という合計39工程で部品が完成されていきます。見た目は単純な形状ながらも、とても手の込んだ部品でした。
まずはこの部品の全行程をQC工程表で確認をすることにしました。手作業の多い部品であったため、作業者の部品の取り扱い次第ではキズの付きそうな工程が多くあると考えられました。しかし実作業を見てみると、どの工程においても作業者自身がキズを付けたことに気付くと考えられ、最終検査まで見過ごされるような小さいキズが付きやすい工程は見つかりませんでした。
このように不良の原因がなかなか見つからないときには、私は製造ラインを漠然と20〜30分見ることにしています。製造ラインで作業者の繰り返し作業を見ていると、ごく稀ではありますが、通常の繰り返し作業には無い作業が突然に起こる場合があるからです。
39工程の、ある一部の工程を数10分見ていたときのことでした。工程の最後部にあるストックされていた部品がリフターで運ばれて行くのでした。この工程は39工程もあるため、工場の2階と3階に別れて製造ラインが設置されていました。3階で作った部品を2階までリフターに乗せて運ぶのでした。この運搬作業は1時間に1回ほど行われていました。
部品は約1m四方の一枚のダンボールに並べて敷き詰められ、それが高さ方向に積まれていました。なるべく多くの部品を一度に運べるように、それぞれの部品の向きを互い違いにしてダンボールに乗せられているのでした。しかし良く見ると、これらの部品同士が接触しているものがありました。特に並べ方は指示されていないようで、作業者が自分の判断で部品同士がぶつからないように効率良く並べているのでした。(図1)
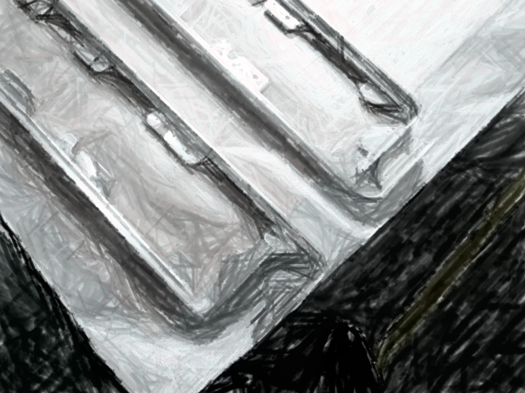
図1 部品同士がぶつからないように並べているが、ぶつかってしまう。
この会社は他社の液晶テレビのベゼルも製造していました。その製造ラインを見に行ったところ、これらの部品をストックするときには一個ずつ透明な卵ケースのような仕切りで部品同士がぶつからないようになっていました。しかしどういうわけか、私の担当したこの部品には仕切りが無かったのでした。
部品同士が接触して体裁面にキズが付くことを懸念した私はすぐさま日本語通訳を介してラインリーダーと話をし、他社の部品と同じような仕切りを追加してもらうことにしました。これでキズに対してどの程度の効果があったかのデータは取っていませんが、キズの発生を防止できたことは確かでした。
突然現れ作業を手伝う別工程の作業者
前述と同じベゼルの量産が開始された直後のことでした。この部品に取り付けられている約40mm大の板金ブラケットを固定しているビスが、脱落/緩みもしくは斜め打ちの状態で、納品先において不良品として発見されたのでした。早速、原因の調査が始まりました。
ビスは板金ブラケットを貫通してアルミ押出材に留められます。ビスはマシンねじを使用しているので、もちろんアルミ押出材にもタップが切ってあります。アルミ材へマシンねじを留めると斜め打ちになりやすい傾向がありますが、別部品のナットを埋め込むとコストが大幅に上がってしまうため、アルミ材にタップを切りマシンねじを留めていました。
ビスの脱落に関しては、製造ラインの電動ドライバーの締付けトルクを確認し、輸送試験データとともにそのトルクで問題のないことを確認しました。またビス留め忘れの可能性もあるので、ビス留め時に使用する治具に番号を振りビス留め順を指定して員数分のビスが確実に留められるようにしました。(図2)
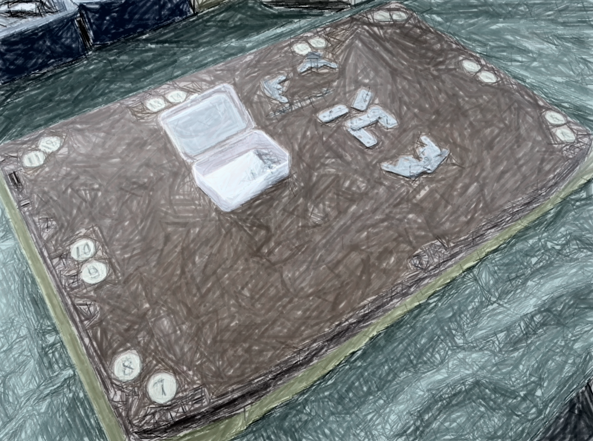
図2 ビス留め順を指定した治具
ビスの緩みに関しては上記と同様の対応になりますが、電動ドライバーの先端に取り付くビットを作業者が指に持ちビスの頭に軽く当ててビスが確実に留められているか確認を行う工程を、ビス留め直後の工程に追加しました。そして問題なく留められているビスには、ビス頭に青い液体のネジロックを塗布し「確認完了」の目印としました。
ビスの斜め打ちに関しては作業者の動作確認を行いましたが、普通に作業をしていれば斜め打ちになることはありませんでした。ロボットを導入するわけにもいかなかったので作業方法はこのままとし、先述のビスの緩みの確認作業と同時に斜め打ちになっていないかを目視で確認することにしました。
これらの確認作業を追加することによって不良品の流出は無くなったのですが、根本的な原因は分からないままでした。検査工程をいくら増やしても根本的な原因を解決しない限り品質は上がらず、また再発の可能性は十分にあるのです。よって継続的に調査を行うことにしました。
私はこのように原因がなかなか判明しない場合には、製造ラインを長時間にわたり観察し何か変化点があるかを確認することにしています。ドラマの刑事の言葉にもありますが、原因は必ず現場にあるのです。製造ラインから少し離れ、ビス留め工程を30〜40分であったか漠然と眺めていたときのことです。突然、ビス留め作業者のラインを挟んだ反対側にもう1人の作業者が現れ作業を始めたのでした。(図3)
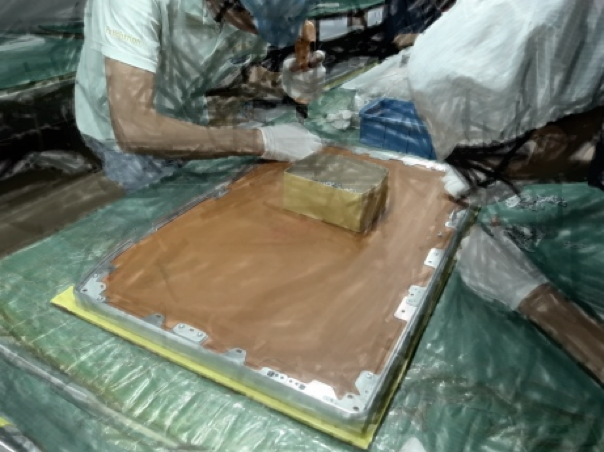
図3 突然現れて作業を手伝う前工程の作業者(右)
製造ラインは各作業者が同じ作業時間(タクトタイム)で自分の作業を完了し、部品を次の工程へと送ります。しかし全行程のタクトタイムが完全に同じになることはなく、また少し作業に手間取ったりすると、自分の作業エリアの前工程側に部品が貯まってしまうことがよくあります。今回の突然現れた作業者はビス留め工程の前工程の作業者であり、ビス留め工程の作業が遅れているのを見つけ、自分は手空き状態になっていたため手伝いに来たのでした。
電動ドライバーは1個しか用意されていません。よってこの前工程の作業者は電動ドライバーの先端に付いているビットをどこからか探し出し、それを指に持ってビスを回してアルミ押出材に仮固定していたのでした。(図4)
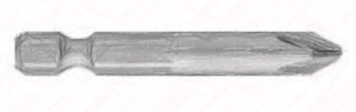
図4 前工程の作業者が使用したビット
これによってビス留め作業者が電動ドライバーでビスを留めるだけの作業になりましたが、これはもちろん作業標準書には記載されていないイレギュラーの作業です。絶対にやってはいけない作業でした。
イレギュラーの作業が生み出した2つの不良
このイレギュラーの作業が先述した2つの不良の原因になっていたのでした。ビスはマシンねじのためビットを指の力だけで回しても、ビス長のほぼ全てが見えなくなるまでアルミ押出材のタップに入り込みます。すると一見して電動ドライバーでビス留めしたのと判別できない状態になってしまうのでした。つまり電動ドライバーを使うビス留め作業者が、自分でビス留めを完了したかしていないかが分からなくなってしまうのでした。これにより、ビス留め忘れが発生していたわけです。
さらに長さが50mmほどのビットを指に持つと、そのビットの短さのために自分の持っているビットがまっすぐになっているのか斜めになっているのかの判別がしにくく、アルミ押出材のタップ穴にビスを斜めにしたままビットを回して入れ込んでしまうのでした。ネジ部が2mmくらい見える程度までしかビスを入れなかった場合、ビスが斜めに入っていることがなかなか判別できなかったのです。そしてこのようにビスが斜めになっていることに気付かない本来のビス留め作業者が電動ドライバーでビスを斜めにしたまま留めてしまうのでした。これでビスの斜め打ちが出来上がるのでした。
QC工程表に無い工程の確認も重要
これらのようにQC工程表に無いところにも不良の発生する原因はあるものです。今回はその典型的なものを2つ紹介しました。
前者の工程間運搬は、一般的な部品でも存在します。塗装工程への運搬や製造ラインから離れた検査工程への運搬などもあります。形状が変形しやすい、キズが付きやすいなどの繊細な部品は運搬工程の確認もするようにしましょう。
後者は非常に珍しい例と思われるかもしれませんが、私はこのような場面によく遭遇しています。製造ラインにおいて作業者の作業をずっと眺めていると、同じ動作を繰り返しているはずの作業者が、突然これまでとちょっと違う動作をする場合があります。それは、設備の設定値の微調整であったり、指定していない作業順を変えただけだったりしますが、これらのような工程に不良の原因が潜んでいる場合が多くあるのです。量産前の製造ラインの確認時や不良品が発生したときには、時間の許す範囲で一つの工程を長時間(20〜30分)にわたり確認することをお勧めします。想像の付かないところに不良の発生原因が潜んでいます。
───────────────────────────────────
~リモート会議だけで中国企業とスマートに仕事を進めるテクニック~
研修の開催ご案内
ローカル部品メーカーの日本語通訳が日々行っている
日本人ではなかなか知り得ないテクニックをお伝えします。
日程と時間:ご希望の日程と時間をご連絡ください。
詳細情報URL:https://roji.global/korona-kennshu2/
───────────────────────────────────