IoTを簡単スタート!パトライト三田工場 潜入&IoT活用レポート
IoTを現場に導入し、現場の生産性を上げたいと思っていても、
・どこに
・どんな設備を
・どれだけの費用をかけて導入し、
・どう活用すればいいか分からない
こんな状況で、結局のところ、まだ導入に踏み切れていないという企業は多いと思います。
そこで、
セル生産のアセンブリ(組立)工程にIoTを導入し、現場の作業員の生産性の向上に成功した パトライト三田工場 の取り組みをご紹介!IoT導入にあたり、こんなことを目指し、こんなシステムを導入し、こんな風に生産性向上まで持って行ったというステップを見ていきたいと思います。
そもそもパトライトってどんな会社?
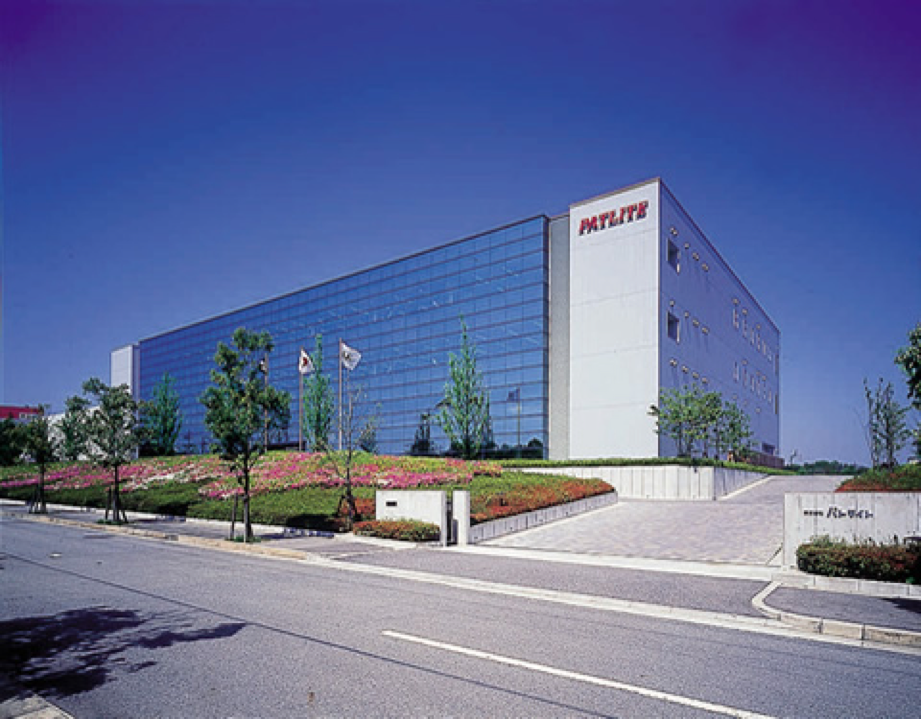
株式会社パトライトは、回転灯や表示灯など警示装置や表示装置を中心とした産業機器メーカーで、大阪市中央区に本社があります。1947年の創業で、2017年に70周年を迎えました。
パトライトと聞くと、ついついパトカーや救急車、消防車などの緊急車両に取り付けられている赤色回転灯や、工場の機械の上部にある赤黄緑の積層表示灯を想像してしまいますが、実はあれは同社の登録商標なんですね。そんなスゴイメーカーです。
ステップ① IoTで何を目指す? ゴールは「魅せる化」
まず同社は工場にIoTを導入する大前提として 「魅せる化」を実現する という目標、方向性を掲げました。
「魅せる化」とは、単に製造現場の情報や工程が透明で分かる「見える化」に止まらず、ユーザーに価値を提供する、喜びを与えられる工場になろうというものです。具体的には、IoTで現場を見える化しつつ、生産管理や基幹システムの受発注や営業情報などとも連携させることによって、ユーザーが欲しい時に、欲しい製品がすぐに手に入る、ニーズにあった製品を作り、提供していけるような仕組みづくりです。
しかし、それを本当に実現しようとしたら膨大な設備投資と時間がかかってしまいます。そのため、まずファーストステップとして取り組んだのが、今回紹介する組立工程におけるIoTの導入と、それによる生産性向上です。具体的には、1分でも多くの組み立て時間を確保すること を目指しました。
ステップ② 具体的に何をする? セルごとの稼働状況の見える化
魅せる化を目指す上で、作業状況の把握とその分析は欠かせません。しかしIoTを導入する際、多くの人を迷わせ、決断を難しくするのが、 どのレベル感でデータを取るか ということ。作業単位で細かくデータを取って分析するのか、それとも大雑把に集める程度にするのか。どちらの方が適切なのか判断できず、結局一歩を踏み出せないという声をよく聞きます。
それに対し、同社が選んだのが後者の「大まかに取る」でした。ただでさえ人不足で困っているところに、データを集める目的で作業者に普段とは別の負荷をかけ、ストレスを感じさせてしまっては元も子もありません。普段通り気持ちよく働いてもらいながら、その裏でデータを収集し、それを改善につなげようという道を選びました。
で、実践したのが、セルごとの稼働状況の見える化。セル内の作業時間を「組み立てている時間」、「セルから離れていた時間」「非稼働時間」に分け、各セルで いつ、どれくらいの頻度と時間があったかを調べて把握することを行いました。
ステップ③ どんな設備で、どうやった? 安価な設備でデータ収集&分析
導入した設備はシンプル。
1セルあたり
・信号化装置 パトライト製「AirGRID WD」 7.5万円
・センサ×2 1万2000円
・信号受信機 25万円
※1台で20セルまで受信できるそうです
・データ集計用PC1台
の計 約34万円
セルの作業範囲にセンサを設置し、AirGRID WDで下の3つの状態を分類した信号に変換して集計。それをディスプレイに表示して見える化しました。
・範囲内にいた =組み立てている時間
・範囲内にいない(範囲外にいた) =セルから離れていた時間
・電源が入っていない =非稼働時間
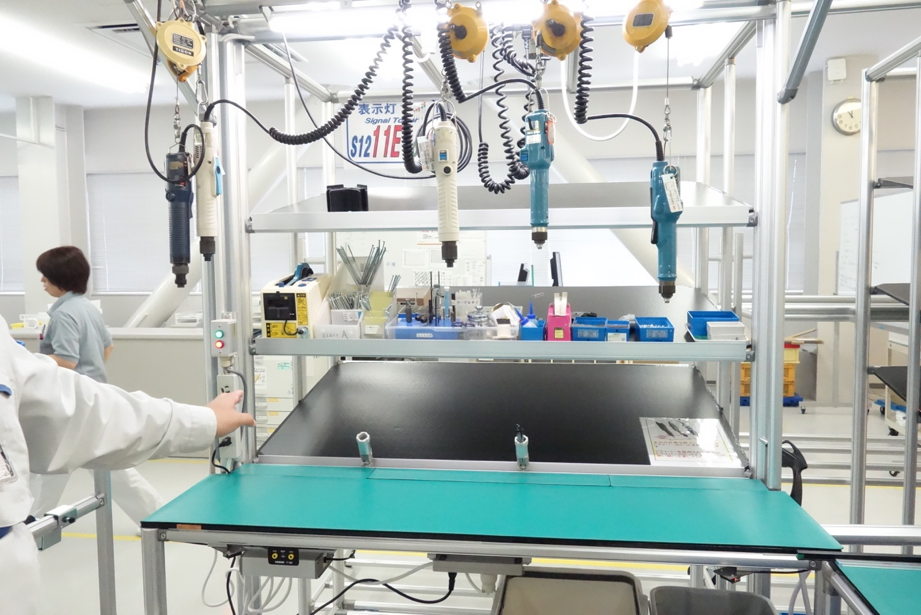
ステップ④ 何が分かった?どうなった? 7.8%ロス削減&4.2%生産性向上
集計の結果分かったのが、範囲内にいない時間が20%もあったこと。本来、組み立て作業に集中すべきところが、なぜか20%もセルを離れている状況でした。
その詳しく分析してみると、部品のピッキングと検査工程でセルを離れることが多かったとのこと。
そこで同社では、部品の供給位置と段取りを見直し、検査工程もセルの作業範囲内に修正。これにより、部品を取りに行く時間が削減し、検査もセル内で場所を移動せずにできるようになりました。結果として、組立に充てられる時間が増え、時間あたりの生産台数を増やすことができたそうです。
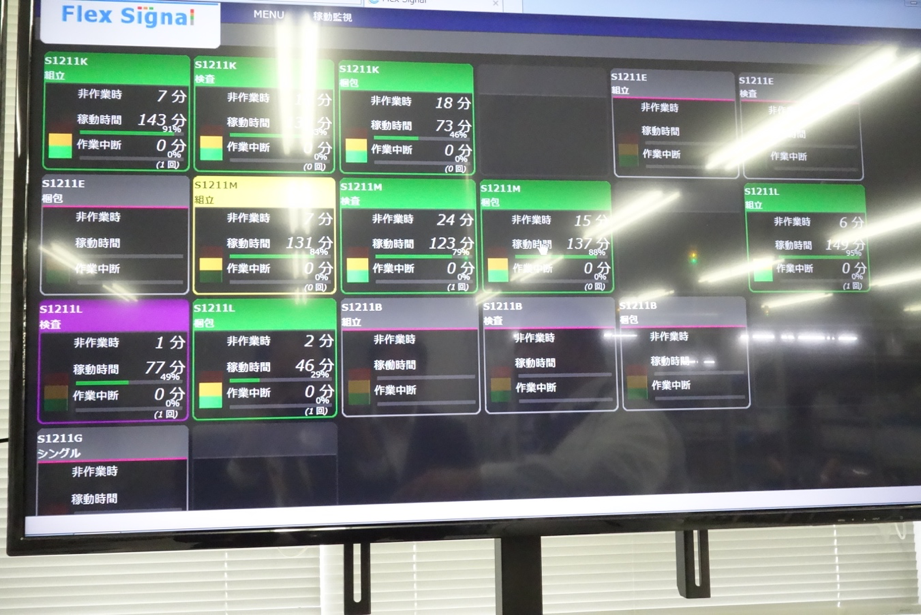
魅せる化に向けて情報の集中管理にも取り組む
ここまでは、あくまで見える化。でも同社のゴールは魅せる化であり、それに向けた取り組みも進めています。
同社では、工場の各種情報を集め、海外を含めた各現場からの結果を集中管理することも行っています。装置やライン、セルの稼動ログだけでなく、部品供給に関係する在庫・入庫の管理でも信号を集中管理することで効率的な供給につなげています。
将来的には生産スケジューラーだけでなく、受発注管理、ERPなどと連携されていくこともイメージしているそうです。
まとめ&総括
パトライト三田工場では、自社がIoTによってどこを目指し、何から始めるのかという第一歩が実現されている現場でした。
まず魅せる化というコンセプトを掲げ、そのファーストステップとして見える化からスタート。最初の難関である、データを取る対象と頻度も自社で設定し、少ない投資で始めていました。
「うちにはそこまでやる体力がない」「すべて設備ができてからやる」という声は多く聞きますが、簡単に始めることができるのだから「まずやる」というのが大事じゃないかなーと思いました。
取材に協力いただきましたパトライト三田工場のみなさま、ありがとうございました!!