IoTに必要な情報を転写と変形から具体的に考える
IoTのキモはICTの方ではなく、IoTで生かすべき情報の方にある、という話です。
現場でIoTを活かす時に必要なこと、イメージできますか?
製品を情報の束と考え、生産活動全般を情報資源と「転写」「変形」のシステムととらえます。
転写や変形に着目して、IoTに生かす情報を選択します。
どのような情報を獲得し、どのように生かすかは人が決めます。
1.情報通信技術(ICT)は魔法の杖ではない
工場のスマート化では、情報通信技術(ICT)を有効に活用しモノのインターネット(IoT)を実現させます。
リアルの世界のデジタル化や生産活動を通じて時々刻々得られるデータ(ビックデータ)のをフィードバックやフィードフォワードをイメージすると、IoTで具体的にやるべきことが浮かんでくるかもしれません。
標準化はリアルの世界をバーチャルの世界と融合させるためには絶対に欠かせません。
自工程で得られたデータは後ろ向きばかりでなく、前向きにも生かせます。
生産活動を通じて得られるデータが自社製品の付加価値を高めるのにどのような貢献をしてくれるのか、ということを常日頃考え、整理しておくことも必要です。
情報通信技術(ICT)は魔法の杖ではありません。
ICTを導入すれば現場の問題が解決する、と安易に考えてはなりません。
高度化した製造技術、生産技術、情報通信技術、それ自体が現場のポテンシャルの低さをカイゼンして高めてくれるわけではありません。
既存の生産設備、生産システムを使いこなし、使い尽くし、使い倒し、しゃぶり尽くして、初めて見えてくる自社工場の強みと弱みを把握していなければ、何をやっても効果はありません。
投資した経営資源はほとんど無駄になります。
これは、ICTに限らず、新たな技術を導入する時には留意したいことです。
昔、お世話になった外注先の営業担当者の話です。
その外注先で、受注システムを新たに導入することになりました。
受注の度に手書きで伝票に起こす手間を省く事、支店との情報共有化を図る事等を目的としていたようです。
専門のシステム担当者がいなかったので、外部に依頼してシステムを開発しました。
こうして出来上がった受注システムだったのですが、残念ながら、営業現場での使い勝手が悪いのか、なかなか定着しなかったようです。
開発したシステムを活用するよう社長からも指示があったようで、なんとか現場とで使わないと……。
かなり昔の話で、当時、中小企業がこうしたシステムを導入すること自体、とても進歩的だったと思います。
社長も現場の手間を省き、効率化を図ろうと前向きに取り組んだのだと思います。
しかしながら、新たなシステムを導入すれば、即業務改善が図られると思い込んでしまい、現状を反映した現場視点の工夫、変更、仕様等が盛り込まれなかった……。
その結果、社長の思いとは裏腹に「使うこと自体」が目的化してしまい、本末転倒状態になってしまったようです。
どんなに優れたシステムも、現場事情に合致していないとタダの箱という残念な状況になります。
(その後、現場事情を反映させて、そのシステムは改良されたようです)
2.現場の状況を把握しIoTの活かし方を考える
製品を情報の束と考え、生産活動全般を情報資源と「転写」、「変形」のシステムととらえることができます。
ここでプレス加工と穴あけ加工の2つの工程で構成されている生産ラインを想定します。
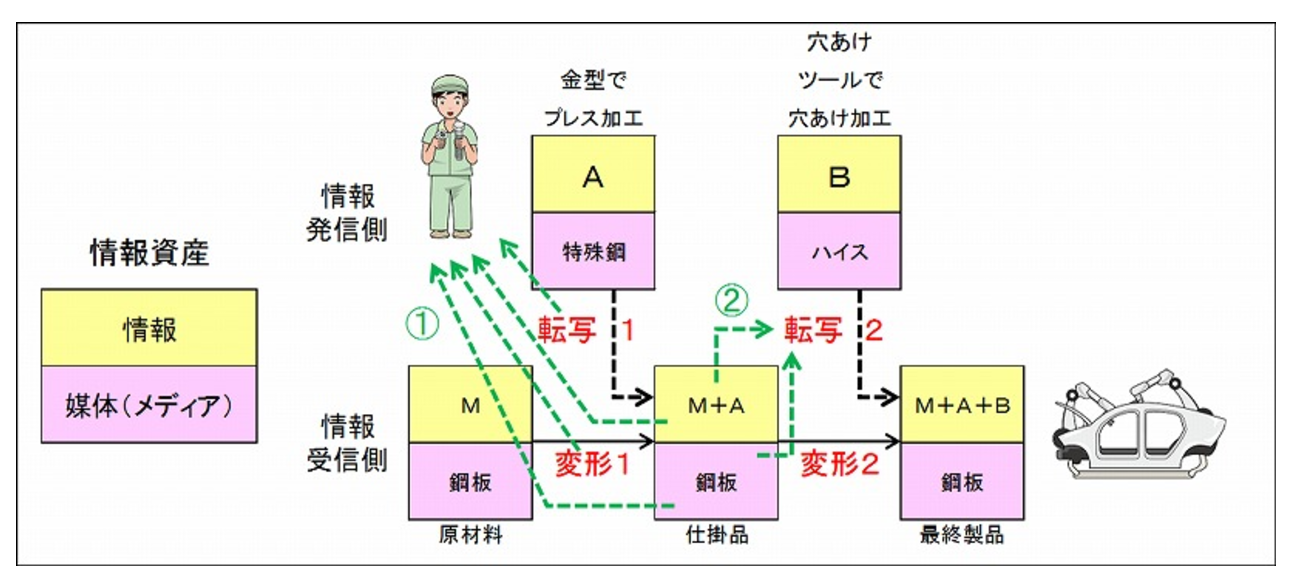
形状情報AとBの2つの情報が媒体(メディア)としての鋼板へ転写されます。
転写1:形状情報Aが金型を取り付けたプレス機によって原材料に転写される。
転写2:形状情報Bが穴あけツールを取り付けた加工機によって仕掛品に転写される。
この結果、鋼板に刻印される情報が2回にわたって変形しています。
変形1:原材料の鋼板に情報Aが加わる。
変形2:仕掛品の鋼板に情報Bが加わる。
このように現状の生産活動は、情報の視点から整理できます。
ここで、生産活動を通じて得られた情報の具体的な活用方法を考えます。
例えば、フィードバックは緑色点線矢印①の束です。
緑色点線矢印は情報の流れを示します。
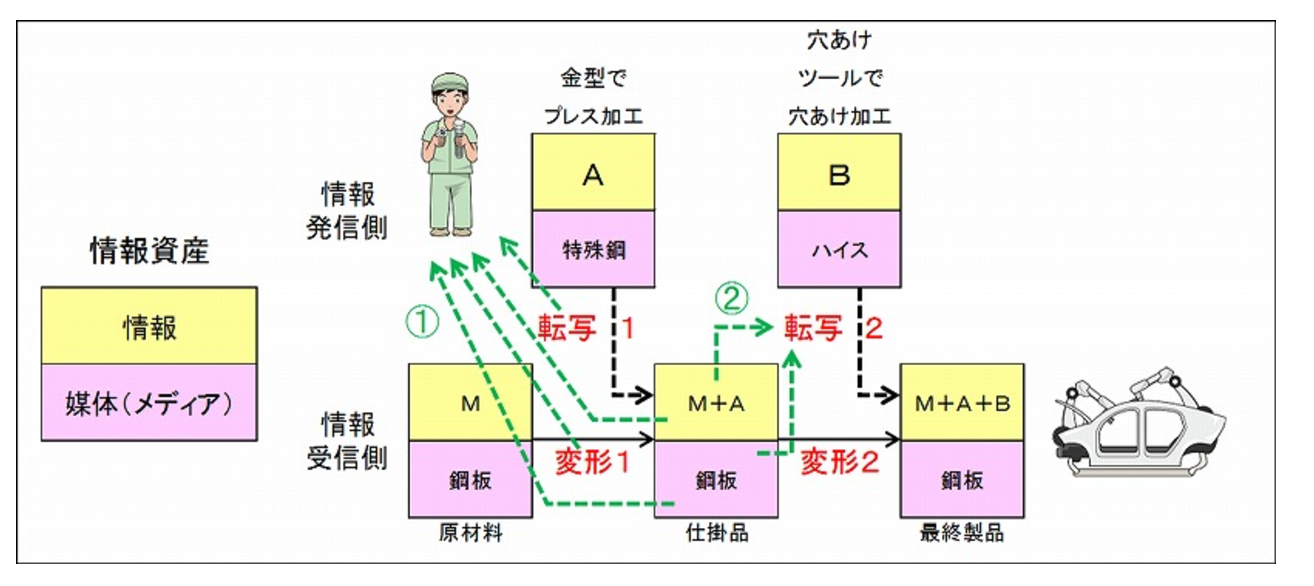
原材料の鋼板がプレス加工されて仕掛品になる工程に関する情報です。
・プレス加工時のプレス機、金型の異常の有無
・鋼板に転写された情報Aの品質
・媒体(メディア)としての鋼板のコンディション
・塑性変形過程の異常の有無
4つの情報を獲得できる。
4つの情報にしきい値を設け、判断基準を設定すれば、良し悪しの判断が可能です。
したがって、矢印①の束の情報をもとに、作業者は金型やプレス機の状況を把握でき、未然にトラブルを防止し、メンテの時期を判断できます。
また、フィードフォワードは緑色点線矢印②の束です。
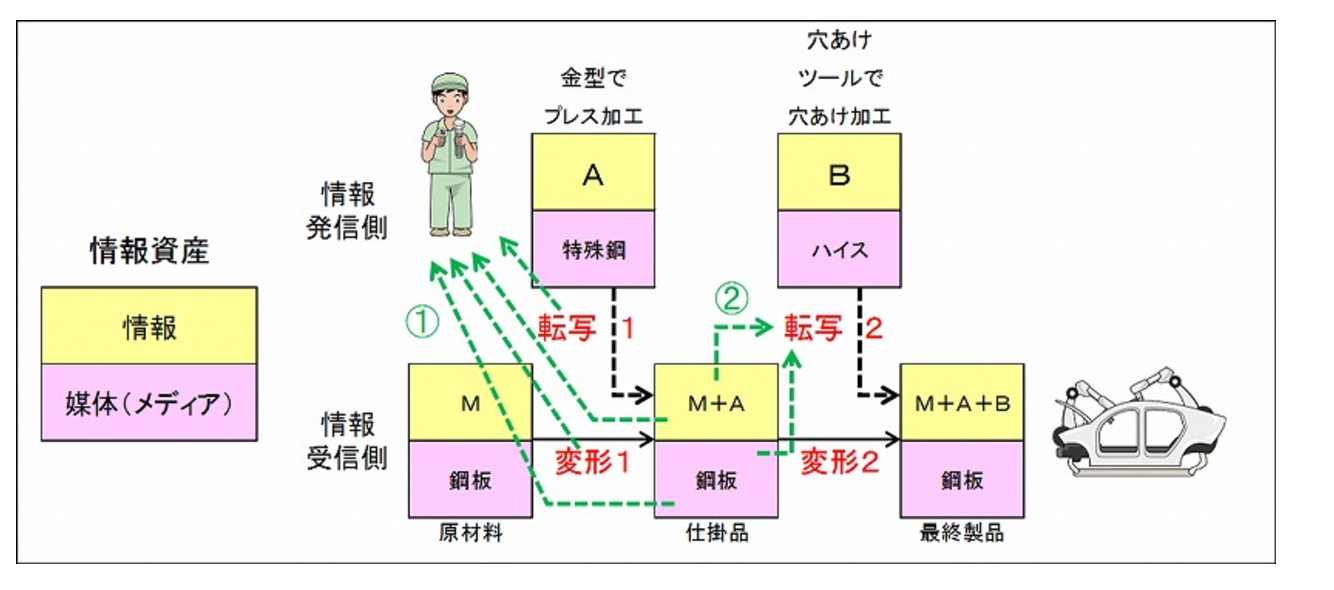
穴あけ工程の直前工程となるプレス工程を終えた仕掛品の品質に関する情報です。
・鋼板に転写された情報Aの品質
・媒体(メディア)としての鋼板のコンディション
こうした情報を穴あけ加工の転写2のプロセスへ反映させることで、品質を安定させることが期待できます。
加工をワークの状況に応じて都度調整できればワークごとの最適加工ができるからです。
具体的には、加工基準部の形状変形を考慮して加工プログラムの原点を調整する等です。
また、標準化を考える時にも「転写」の考え方でもれなく検討できます。
プレス加工を例にとります。
この工程でのキモは情報Aです。
なぜなら、形状情報Aは顧客がコトを感じるために届けたい情報のひとつだからです。
形状情報Aが、正確に鋼板へ転写される条件を整理します。
・金型に刻印されている形状情報Aの品質に問題がないこと。
・金型の媒体(メディア)の品質に問題がないこと。
・転写1の品質を決めるプレス機と稼働プログラムに問題がないこと。
例えば、こうした切り口で整理ができます。
そして、それぞれを実現させるための手順やチェックポイント等を検討して……。
このように、「コト」の観点からも標準化を検討することができます。
3.どのような情報を獲得しどのように生かすか
2015年からホンダが再び自動車レースの最高峰フォーミュラー・ワンに参戦しました。
英マクラーレンにエンジンとパワーユニットを供給していますが、パワーユニットの安定を支えるのがIoTです。
車両に取り付けた150個前後のセンサーで集めるデータを最新システム(日本IBMが開発)で解析し、リアルタイムで燃料の残量や故障の可能性を割り出します。
データをホンダのF1開発拠点、英国のマクラーレンの研究拠点、サーキットの3ヶ所で共有し、最適な給油のタイミングなどのレース本番の戦略立案に役立てたり、蓄積されたデータをシーズン中のパワーユニット改善に活かしています。
(出典:『日本経済新聞』2016年2月24日)
ここで、注目したいのは「車両に取り付けた150個前後のセンサー……」です。
どうやってセンサーの仕様や取り付け位置を決めるのでしょう。
他の誰でもなく、当然にエンジニアが決めています。
ICTの技術は、タイムリーに正確に大量にデータ処理をすることには貢献していますが、データ計測の本質にかかわる計測システムの設計はエンジニアがやっています。
先に、プレス加工と穴あけ加工の2つの工程で構成されている生産ラインを想定しました。
そして、フィードバックやフィードフォワード、標準化に使える情報を整理しました。
これらの情報をデジタル化すれば、人間を介さなくともマシン同士で情報のやり取りが可能となり、IoTが目指している生産ラインの自律性が高まります。
ただし、その一方で、IoTで必要な情報を検討し、選択し、決定しているのは、他でもないその設備を使用するする人、あるいはその設備担当の技術者です。
つまり、IoTに限らず、どのような技術でも、本質的な事項は人が決めます。
ですから、IoTを現場で活用するキモは、ICT技術の方ではなく、IoTで生かすべき情報の方にあります。
どのような情報を獲得し、どのように生かすかです。
それは人が決めます。
まとめ。
製品を情報の束と考え、生産活動全般を情報資源と「転写」「変形」のシステムととらえる。
転写や変形に着目して、IoTに生かす情報を選択する。
どのような情報を獲得し、どのように生かすかは人が決める。
IoTのキモはICT技術の方ではなくIoTで生かすべき情報の方にある。