ドイツの工場ってどんな感じ?〜フエニックス・コンタクト工場潜入記 後編〜
インダストリー4.0の発祥の地、次世代の工場の形を生み出したドイツの工場とはどんな様子なのか?日本との違いはどこなのか?
4月末にドイツで行われた世界最大の産業見本市ハノーバーメッセ。その取材と合わせ、ドイツの産業用機器メーカー大手のフエニックス・コンタクト社の本社工場を見学してきました。
前編では電子機器を製造するフエニックス・コンタクトエレクトロニクス工場を紹介しました。後編では、いよいよ本社工場の様子をご紹介します!
※構内は写真撮影禁止なので、イメージを膨らませてください。。。
フエニックス・コンタクト社ってどんな会社?再び
・1923年創業のドイツ産業用機器メーカー
・日本法人は1987年〜。新横浜にオフィス
・コネクタや端子台など接続機器の世界トップメーカー
・PLCやネットワーク機器も揃え、総商品点数は6万点超
・2017年売上高22億ユーロ(約2900億円)
・従業員数1万6500人
・ものづくりは自前主義。原材料を購入し。一から製品をつくる垂直統合型
いよいよフエニックス・コンタクト社の本丸 ブロンベルグの本社工場へ
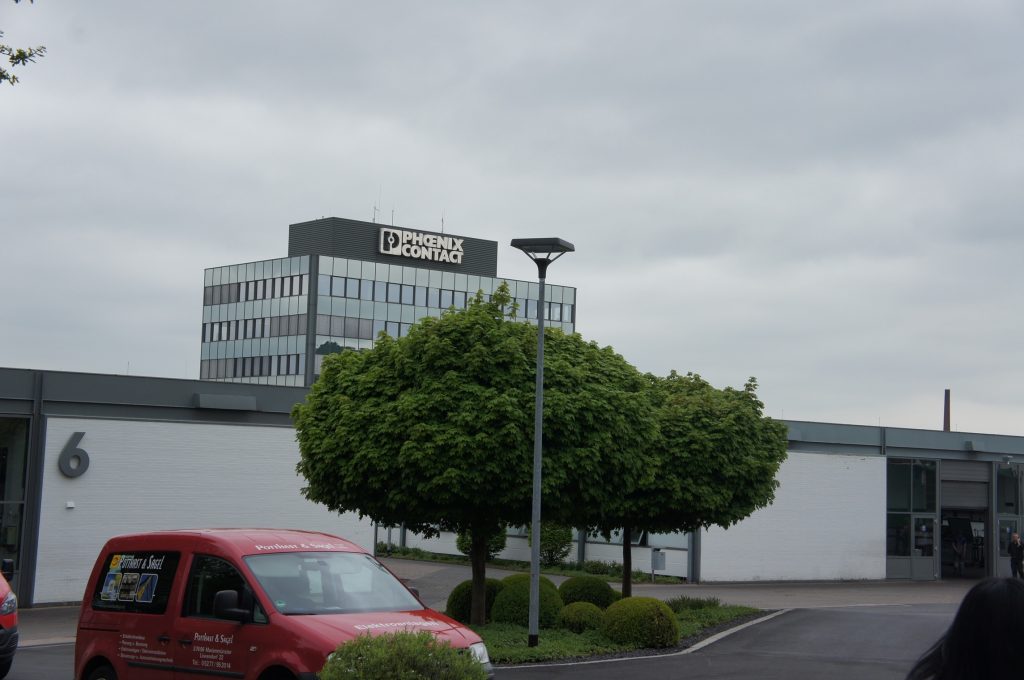
本社工場は37もの建屋からなり、約4500人ほどがここで働いています。樹脂や金属材料の加工・成形工程にはじまり、組み立て、パッケージング、出荷まで、すべてこの工場で行われています。
フエニックス・コンタクト社のものづくりを体現するねじ工場
最初は、本社工場で最も古い建物となる1番工場。今から60年前の1957年に建てられたそうです。ここにはレール端子台の自動組立ラインがあり、1分で84個ものレール端子台を組み立てています。
続いて2番工場。ここはねじ製造を行っている現場で、銅でできた線材を小さく切って、ねじ頭を作り、転造でねじ切りをするというねじ作りに必要な工程が揃っています。M2〜M6のねじを1日700万個まで作れる能力があり、1日に使うねじの数が500万個のすべてをここでまかなっているそうです。
これほど大量のねじを作っていると、ものすごい量の切り屑が出ます。切り屑はボックスに集められてリサイクルに回されますが、1ボックスあたりでだいたい3000〜4000ユーロ(39〜52万円)くらいになるそうです。
自前主義を支える生産技術部門 インダストリー4.0の製造ラインを開発中
続いて見学したのは、機械工学部門が入っている建屋。いわゆる生産技術部門のようで、新しい製造ラインの開発や試作をする場で、この時はインダストリー4.0の製造ラインを作っているところでした。
作っていたラインは、端子台のラインのようで、これまで見た全自動化ラインとは少しだけ趣きが異なっていました。
全自動化ラインがコンベアと直動、空圧と治具でメカ一色だったのに対し、新しく作っていたラインは、メカメカしさはそのままに、カメラやセンサの数が多く、ロボットの姿もちらほら。新しい制御系の技術が加わった感じです。
ツアーガイド曰く、複数の種類の端子台をこのラインで同時に作れるとのことで、操作・管理する技術者には経験が求められるそうです。
またこの建屋は、従業員の訓練にも使われ、機械や制御、プログラミングなどを教えているそうです。
仕掛品のムダを作らない新しいものづくり インダストリー4.0に感動
この生産技術部門では、インダストリー4.0と言ってもいい(はず)の製造装置に出会いました。リール巻きされたケーブルから自動で末端加工を施した製品を作るもので、それを少し紹介します。
ケーブルは、曲げたり伸ばしたりして使うのが当たり前の製品で、そのため柔軟性とある程度の長さがあり、ぐにゃぐにゃと曲がり、角材や棒材のようにピンっとまっすぐに伸びて形状と寸法が常に一定になりません。そのため加工の自動化や機械化がしにくいものの代名詞になっています。
それに対し、線材の切断から皮むき、末端加工、束ね加工までの一連の流れを自動化した最新装置を見せてもらえました。
①リール巻きされたケーブルを装置に引き込む
②治具に巻きつけ、一定の長さでカット。テープで束ねる
③片方の末端の皮を剥き、それぞれの線にばらけさせる
④それぞれの線ごとに末端の皮を剥く
⑤末端にフェルール端子を被せる
⑥被膜とフェルールの境目を保護するための追加工をする
⑦検査したら治具が外れ、完成品箱に移動
と、この一連の流れを一つの製造装置で行っていました。
※その時の私の汚いメモ書きがこちら
通常は、各工程がバラバラにあり、それぞれが加工が終わったもの、いわゆる仕掛品を箱にまとめ、後工程に渡していきます。それが一連の流れとなって完成品が出来上がります。しかしこれだと仕掛品を作る流れになるので、後工程に受け渡すムダ、作業待ちのムダ、作りすぎのムダなどなど、いわゆるトヨタ生産方式でいう 7つのムダ の原因となります。
でも、原材料から一つの装置またはラインですべての加工を行って最終製品までたどり着ければ、仕掛品とそれにまつわるムダがなくなり、最小コストでものづくりができるようになります。
インダストリー4.0はマスカスタマイズで一品生産ができるもの、それがメリットであると思っていましたが、大量生産品であっても最小コストでムダのないものづくりができるというメリットもあるんですね。さらに、工場の製造システムとオフィスの基幹システムとつなげば、需要と供給をイコールにして、在庫ゼロの 製造の最適化 も可能になることが改めて分かりました。
いままでインダストリー4.0やIoTなど色々と見て聞いて勉強してきましたが、今回は目からウロコの新しい気づきと理解を与えていただきました。感謝感謝
150台の射出成型機がズラリ
続いては2万㎡もあるという巨大な34番工場。ここでは150台のプラスチック射出成型機で、プリント基板用コネクタのプラスチック部品を作っています。各機械へはパイプラインによって随時材料が供給され、その使用量は1ヶ月あたり150トンにものぼるそうです。
世界各国へ出荷するための自動倉庫にア然。。。
最後は物流センターの18番へ。
さすがに毎日大量の製品を世界に届けている大手企業だけあり、この本社工場で作られた製品を輸出する際は、空港や港での税関を通す手間を省略できる優遇措置を受けているとのこと。これによりスムーズな流通が可能になっているようです。こうした優遇措置は企業にとっては追い風になりますね。
センター内は厳しいセキュリティゲートを通って入場。一部、ピッキング工程で人で作業がありますが、それ以外はほぼ全自動化されている自動倉庫。高さ何十mもありそうで、一番奥まで見えない奥行きのメカメカしい巨大な棚に20万個もの収納スペースがあるそうです。その中をレールにのった取出機が高速に動き、まさに近未来、SF映画のワンシーンのようでした。
工場見学まとめ
とこんな感じで本社工場の見学が終了。
これでもごく一部で、まだ30以上もの建屋があり、建設中のところもありました。主に製造工程の方ばかりに紹介してきましたが、ほかにも太陽光発電やコージェネ工場全体のエネルギー管理の工夫なども色々ありました。それはまた別の機会で紹介できたらと思います。
一緒にツアーを回った方々からは、特別にすごいものや自社の工場よりも進んでいること、想定外のものというのはなかったけれど、自社の工場以外を見られたのは良かった、勉強になったという声が聞かれました。
私も同感で、ものすごく先進的で、展示会で各社が出しているような最先端の技術があふれているというような感じではありませんでした。それでも、前編にも書いた通り、工場内の明るさの違いや女性の姿、真っ赤で目立つ防災設備、整然とした配線など、普段見ている日本の工場とのちょっとした違いは色々あり、その辺りはとても勉強になり、面白かったと思います。
また、リール巻きからケーブル製品を作る自動製造装置では、インダストリー4.0やこれからの製造に対してこれまでとは違った理解を得ることができました。工場の本質、最適な生産を考える上でも大変勉強になり、とてもいい工場見学でした。フエニックス・コンタクト社の皆さま、ありがとうございました!!
ドイツの工場ってどんな感じ?〜フエニックス・コンタクト工場潜入記 前編〜はこちらから
▼こちらからハノーバーメッセ2018取材フォトレポートをご覧いただけます。