データ解析、もうやり尽くしたと思うのはまだ早い
IoTとデータアナリティクスの組み合わせによる製造業の改革に関して「できる手はやり尽くした」と考える担当者もいるかもしれないが、それは早計だ。SASによれば、まだホワイトスペースは残っている。
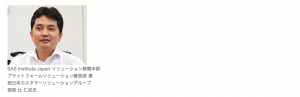
「IoTを活かした次世代のモノ作り」といった見出しがメディアをにぎわせるようになって久しい。各生産工程にセンサーを組み合わせ、ネットワークを介してデータをクラウド上に集約し、ビッグデータ解析技術を用いて「知見」を見出してさらなる品質向上やムダ省きに活かす、というのが典型的なシナリオだ。ここまでいけば、「もうできる手は打った、やり尽くした」と考える担当者もいるのではないだろうか。
だが実際には、まだ「ホワイトスペース」が残っているとSAS Institute Japanの辻仁史氏(ソリューション統轄本部 プラットフォームソリューション統括部兼西日本カスタマーソリューショングループ部長)は指摘する。実際に、IoTとデータアナリティクスを活用して一歩先を行ったかに見える先進的な企業でもなお改善の余地が残されており、そこに手をつけることで実際に成果を出したケースがあるというのだ。
いっそう厳しさを増す環境の中で、いかに熟練作業員のノウハウを伝えるか
常に厳しい状況にさらされながらも創意工夫で乗り切ってきた日本の製造業だが、昨今、環境はさらに厳しさを増しつつある。
1つは、納入先からの標準化、小ロット要求が一段と高くなっていることだ。厳しい品質・納期を満たしながら、どの工場からでも、どの製品でも、よりぴったりしたタイミングでの納品が求められており、サプライヤーにはこれまで以上に高度な品質管理が求められる。
一方で、働く側の環境改善に向けた「働き方改革」の流れが加速している。労働者一人一人にとっては歓迎すべきことだが、これまで「今日だけはちょっと無理してもらえないかな」と残業を依頼するといった形で、フレキシブルに対応できていた要求に応えるのが難しくなってきた。従業員のワークライフバランスを実現しながら、納入先からの要求にいかに応えていくかも、企業としての大きな課題だ。
そして何より大きな課題が人手不足だ。就労人口全体の高齢化と減少に加え、残念ながら「失われた10年」で経験を積むことのできなかった世代がすっぽり抜けており、退職を控えたベテランから中堅・若手へと知識を継承しようにも、伝える先の人材がいないのが実情だ。人手という面では、海外に進出した企業では、ジョブホッピングも難しい課題になっている。現地で従業員を雇用しても、仕事に慣れてきて任せられるようになったころに、もっと待遇のいい別企業にさっと転職されてしまうことが少なくなく、やはり知見の継承が課題になっているのだ。
しかも市場の競争は激しさを増しており、従来型の少品種大量生産では製品のコモディティ化は避けられない。自社ならではの付加価値を高めるには、顧客や市場のニーズに合わせた多品種少量生産へのシフトも不可欠だ。
「こうした中でどうやって、今まで熟練の作業員が経験を踏まえて調整してきた工程の『合わせ込み』の作業を、どう可視化し、伝承していくかが課題になっている」と辻氏は指摘する。その解決策として注目したいのが、エッジコンピューティングとAIの組み合わせだ。
エッジアナリティクスを活用し、自律的に最適化を図る生産プロセスを実現
前述の通り、一歩先行くモノ作りに取り組み始めた企業では、数年前からIoTを組み合わせ、生産工程のさまざまなデータを収集し始めてきた。そこに最先端の統計モデリング手法や機械学習、深層学習を組み合わせることで、いままではベテランの頭の中にしかなかったノウハウを、誰もが分かり、活用できる形で共有できるようになる。結果として、各従業員のスキルに依存することなくいっそうの品質改善につなげ、コスト削減やスループット向上を実現できる、というわけだ。
例えば、Aという工程でαという製品を成形した後にB工程に回し、工程Aではすぐ続けてβという製品を生産する、といったラインが動いている場合、IoTを活用して細かく情報を収集・解析することで、「こんな条件ではこういった不具合が発生しやすい」「αの次にβを生産するなら、設定温度はこうしておくほうがいい」といった、さまざまなノウハウを得ることができた。
ただ、得られた知見はあくまで「人」にフィードバックされるもの。実際の生産プロセスに反映するにはこれを生産計画に落とし込んだ上で、製造ラインのPLCを制御するMESやSCADAの再設定、再プログラミングが必要であり、PLCはあくまで「言われた通りに動作するもの」という点に変わりはなかった。
だがもし、工程の切れ目や加工する製品の性質に応じて、現場のPLC側で自律的に、またリアルタイムに変更や調整を行うことができれば、もっと品質を高め、効率的に生産ができるのではないかーーそれを可能にするのが、リアルタイムなエッジアナリティクスだ。
「エッジアナリティクスによって、『こういった条件ではこうすべき』といった事柄を機械に直接伝えることができるようになった。つまり、機械が状態に合わせて自律的に、より柔軟に動けるようになることで、今まで手付かずだったエリアも改善できるようになった」(辻氏)
この「自動制御の最適化」が可能になったのは、ただあらゆるものがつながるだけでなく、エッジコンピューティングの環境がリッチになったためだ。エッジ側、すなわち工程を司るPLCに近い側でもより多くのメモリ、リソースを用意できるようになり、これまでサーバやクラウド側に集約して処理する必要があった機械学習・分析機能を、生産工程のすぐそばに持ってこられるようになった。いわば、前工程や加工状態を踏まえて最適な生産を実現すべく調整する「頭脳」が、PLCのすぐ側に存在できることになる。
こうした進化は、IoT/IIoT自体の普及からも必然的なものだ。エッジ側でつながる機器が増えれば増えるほど、コントロールすべきものが増えてくる。ましてや、各機器が高度化し、一種の「頭脳」を持つようになれば、その管理を人間が手作業で行うのは非現実的であり、自律的に動作するための何らかの仕掛けがなければ、運用管理が破綻しかねない。エッジアナリティクスはそうした側面からも求められていると言う。
まだ改善の余地はある、早くも成果を出した国内企業も存在
長年にわたってデータ解析プラットフォームを提供し、得られた知見を業務の各プロセスに生かし、最適化をシームレスにつなげていく「アナリティクス・ライフサイクル」を提供してきたSAS Institute Japanが、エッジアナリティクス実現のために提供している製品が「SAS Event Streaming Processing」だ(※詳細はこちら)。
これまでのようにセンター側にデータを集約してAIで解析することでもさまざまな知見が得られたが、SAS Event Streaming Processingを活用すればさらに一歩進んで、エッジ側でリアルタイムにデータを分析し、フィードバックに基づいて速やかに制御できる。そんな仕組みを活かすことで、「まだまだ製造業には改善できる余地がある。事実、そうした取り組みを実践した企業もある」と辻氏は述べている。
ただ、それは一朝一夕に実現できるものではない。データ活用の持つ意味を理解し、「アナリティクス・ライフサイクル」という概念を定着させ、人材を育てていくといった取り組みが必要だ。事実、目先が利く企業では、ハードウェアやSAS Institute Japanのプラットフォームを活用した環境やプロセスの整備だけでなく、自社ならではの特性を踏まえてデータを解析できるデータサイエンティストの育成にも着手している。
9月7日に開催される「スマートファクトリーセミナー 2018」(http://pages.fa-products.jp/FASMR1809FAPSmartFactory_LPapply.html)のセッションでは、実際にエッジアナリティクスを活用して工程能力指数を13%向上させるという実績を上げた国内製造業の事例とともに、その効果が紹介される予定だ。ぜひその目で、厳しい状況を打開する「突破口」となりうるエッジアナリティクスとAIの組み合わせのメリットを確かめていただきたい。
Smart Factoryセミナー2018
~活用段階にきたデジタルツインとスマートファクトリー~
2018年9月7日(金) 14時25分~
『リアルタイム分析でまだまだ効率化できる。プロセス改善事例と勘所』
★お申し込みはこちら⇒ http://pages.fa-products.jp/FASMR1809FAPSmartFactory_LPapply.html