工場運営のIoTでは段取り作業にも注目する
IoTの事前準備として段取り作業の“今”を把握し標準化する、という話です。
IoTの事前準備として、“今”を把握できていますか?
優先して把握すべきトコロに気が付きますか?
これから、現場作業の標準化を進めていこうと思っているけど……。
技能伝承のためにも必要なんだけど、それ以上に、将来の望ましい工場の姿を描くためにも必要だろう。
IoTの事前準備のためにも、何を優先して“今”を把握すればイイだろう?
「人とロボットの協業」「生産設備のモジュール化」の2つがドイツでのIoTの流れです。
段取り作業に注目します。
1.IoTを成功させるためにやらねばならないコト
工場のスマート化の目的は生産効率の向上やカスタマイズ化への移行です。
そのためには、まず“今”を知ることです。
高度化するICTをいかに活用しようか?
どのような成功事例があるのだろうか?
自社工場へどのように適用すれば上手くいくだろうか?
こうした情報に意識が向きがちですが、まずは、自社工場では何ができて、何ができないのか、現状を把握することです。
そしてスマート化の目的を明確にします。
IoTの考え方を自社工場にも導入しようと決断したら、まずやるべきことは足元を見つめることです。
三菱UFJリサーチ&コンサルティング(株)が、小規模事業者と中規模事業者を対象に「ITの導入の効果が得られた理由」(複数回答)をアンケートを実施しています。
小規模事業者284社、中規模事業者723社の結果が下表です。〔出典:2012年11月三菱UFJリサーチ&コンサルティング(株) 2013年版中小企業白書〕
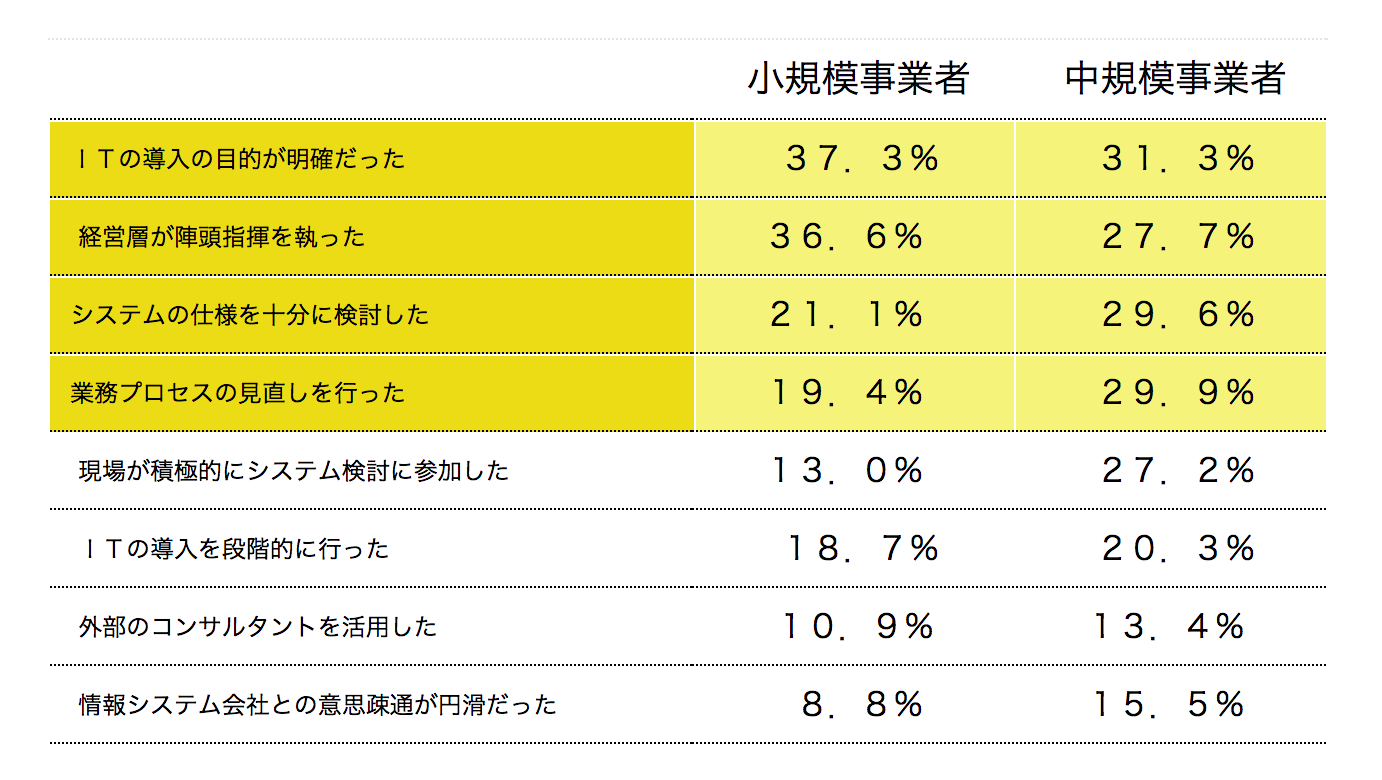
ITを導入する時、どのような視点が抜けると失敗するのか参考になります。
この結果より
・ITの導入の目的・目標があいまい
・経営陣が現場へ丸投げ
・システムの仕様検討が不十分
・業務プロセスの見直しをしない
このような場合、IT投資で失敗のリスクが高まります。
このような状況を避けるには、十分に“今”を知ることです。
そのためノウハウの体系である「標準化」は欠かせません。
既存の生産ライン、設備を使い尽くすことも大切です。
また、イノベーションに向けた自律性を評価する風土を醸成したい。
一方でインダストリー4.0、スマート工場の動向にも注目です。我々中小企業モノづくり工場でやるべきことが見えてきます。
2.ドイツのインダストリー4.0
もはや新興国にコスト競争で勝ち目がないドイツのモノづくり産業にとって、マスカスタマイゼーションは生命線です。
このあたりの事情は日本も同じです。
それには工場で多品種少量生産、変種変量生産に柔軟に対応できなければなりません。
そこで、今のドイツが目指しているスマート工場として2つが挙げられています。
「人とロボットの協業」「生産設備のモジュール化」
2-1.人とロボットの協業
マスカスタマイゼーションでは、生産ラインで扱う製品仕様数が大幅に増加することが予想されます。
それに伴い、原材料の種類、加工仕様、組み付け部品の種類等が増え、生産プロセスが複雑化します。
現場作業者の判断力・識別力にのみ依存した生産ラインではムリが生じます。
こうした状況は品質低下やクレームに直結するのでヨロシクない。
したがって人間の柔軟性を残しながら、属人的な部分を補うことが必要になります。
そこで、こうしたコンセプトが出てきたのだと推測されます。
現状では人とロボットが協業する場合、ロボットの稼働速度を安全なレベルにまで下げることが、法律で求められています。
すると効率が低下し生産ラインへの導入が難しいので、多くの生産現場ではロボットを柵で囲って人とロボットを分離している。
このあたりは日本の事情と似ています。
ただしこれでは多品種生産の場合、段取りばかり発生し効率のよい対応ができません。
そこで、法律による規制を緩和しつつ、人間とロボットが至近距離で対話しながら、それぞれの良さを活かす協業のスタイルが検討されています。
具体的には下記のような事例があります。
・マスカスタマイゼーションでは、造るモノに合わせて生産ラインをめまぐるしく変化させなければならない。
人は柔軟に対応できるが、特定の場所に固定されたロボットは難しい。
そこで、自律走行する台車にロボットを搭載した。
・人と向かい合わせになって連携しながら作業する双腕型のロボット。
人にぶつかった衝撃を感知すると数ms以内に動作が止まる。
(出典:日経ものづくり2015年6月号)
2-2.生産設備のモジュール化
マスカスタマイゼーションに柔軟に対応するため、生産設備を簡便に入れ替えるのを可能にする考え方です。
「レゴブロック」のように自由に交換可能で、ネットワークに接続したら、ただちに稼働ができる機能を備えた生産設備を発想しています。
「プラグアンドプレイ」で交換できることが特徴です。
現在のパソコンの周辺機器にも同様な機能があります。
昔は周辺機能をパソコンに認識させるためには一度、パソコン本体の電源を落として、再起動させなければならなかった。
生産設備でこれをヤッテイタラ、効率が悪くてショウガナイ。
一部分の設備を交換する度に、生産ラインを止めなければなりません。
今、ドイツではこうしたコンセプトに沿った生産ラインや生産設備の開発が進んでいます。
それも多数の企業が参加して進めています。
そうなると当然、設備と設備の接続部となるインターフェースの共通化が課題です。
インターフェースに関しては、接続部の形状や通信の標準化をベースに検討を進めています。
こうしたところを、ドイツ政府が後押しをしているのでしょう。
日本は出遅れているので、このあたりの動向が、今後、気になります。(出典:日経ものづくり2015年6月号)
3.我々中小企業モノづくり工場では何に着目すべきか
IoTの本質には生産活動の「自律性」がありました。
さらに「人とロボットの協業」「生産設備のモジュール化」という2つのコンセプトも浮かび上がってきます。
従来の生産革新では、自動化や省エネルギー化の取り組みが中心で、現場視点でした。
これからの生産革新はいかに顧客に選ばれる製品をタイムリーに市場へ届けられるかが、取り組みの中心です。
顧客視点です。
さらに、高付加価値化の切り口として、
・マスカスタマイゼーション
・超短納期化
の2つがあります。
これらも考慮して考えます。
ドイツが目指すインダストリー4.0の2つのコンセプト「人とロボットの協業」「生産設備のモジュール化」で狙うのは柔軟性のある生産ラインです。
・柵で囲われ隔離されていたロボットを人間と同居させ切り替えの柔軟性を高める
・製品に応じた設備の入れ替えの柔軟性を高める
つまり、「段取り時間を究極まで短くする」ことです。
生産リードタイムの短縮がその本質です。
特注生産は個別生産になり、規格品受注生産や見込生産で実施される連続生産に比べれば納期は長くなる傾向にあります。
マスカスタマイゼーションはそのカスタマイズ化に対応しつつ、コストは大量生産並みを維持することが目標です。
したがって、あらゆる種類の製品が生産ラインに流れ始めたら、いかに短時間で出荷できる状態に至るかが注目点です。
そのように考えると、「段取り時間を究極まで短くする」はインダストリー4.0の現場での狙いのひとつとなります。
日本が直面している問題(国内での少子高齢化と国外の新興国による追い上げ)はドイツと似てはいますが、今後のIoT化でドイツと同じような道を歩む必要は、必ずしもないです。
ただ、政府が主導し国を上げて取り組くんでいるドイツの動きは参考になります。
したがって、目指すべき状態の工場を描く手がかりにもなり得ます。
そこで、“今”を知るという論点のうち、「段取り作業」は重視すべき項目です。
今から現場の段取り作業をしっかり把握し見直しをしておけば、「その時」になったら、真っ先に役に立つことが期待できます。
生産リードタイムの短縮がその本質であり、「人とロボットの協業」「生産設備のモジュール化」という2つのコンセプトを実現させるためには必要だからです。
段取り作業や段取り時間は現時点で標準化されていますか?
(また、標準化が出てきました…………。)
まとめ。
IoTの事前準備のために、何を優先して“今”を把握すればイイだろう?
「人とロボットの協業」「生産設備のモジュール化」の2つがドイツでのIoTの流れ。
段取り作業に注目する。
IoTの事前準備として段取り作業の“今”を把握し標準化する。