工場見える化:材料費について考える
現場では材料費を総額ではなく原単位で管理できていますか?
毎月、材料の種類別に使用量総計は現場に記録させているけど。
たしかに生産量が多ければ増え、生産量が少なければ減っている傾向を見ているだけでは、無駄があるのかないのかわからないなぁ。
製品の種類が多い場合、どのように材料費の管理をやればイイのだろうか?
製品ごとに、標準原単位を設定して、それとの差異を管理します。
1.材料費は原単位で管理する
生産活動を鳥の目で俯瞰しお金の流れを意識して判断基準となる指標を考えました。
付加価値、費用、生産性の指標とそれらを算出する項目を挙げました。
生産活動を定量化(指標化)することは、工場を見える化することに他なりません。客観的な工場運営や工場経営ができるようになります。
ここで、管理項目の柱の一つである材料費を考えます。
一般的に材料費は直接材料費と間接材料費に分類されます。
付加価値を算出する際には、主として直接材料費に注目します。
この直接材料費には、製品を直接構成する材料と外部より購入して製品に組み付ける部品があります。
自動車メーカーにとっての鋼板や手作りパン屋さんにとっての小麦粉は前者です。
家具メーカーにとっての取手や鍵などは後者です。
つまり、製品単位あたりの消費量が明確であり、生産量に応じて消費されるモノに注目します。
また、場合によっては、間接材料費や固定費に分類される燃料費なども、もし製品別、設備別に集計が可能であるならば、付加価値を算出するための費用項目に採用してもイイでしょう。
要は現場が自主的にコントロールできる費用項目で、生産量に比例して出費される費用項目を取り上げます。
利益に直結する数値であり、製品単位あたりの消費量を管理します。原単位と表現することもあります。
現場で最も重点的に管理する項目は、この材料費です。
一般的に、製造原価に占める割合が、他の費用項目よりも大きいからです。
下記のグラフは、
- 中小企業の製造業(法人企業)の製造原価内訳の年度別推移
- 製造原価に占める材料費と労務費の割合の年度別推移
です。
2004年から11年間のデータです。(出典:中小企業庁「中小企業実態基本調査報告書」)
全ての業種累計での結果です。
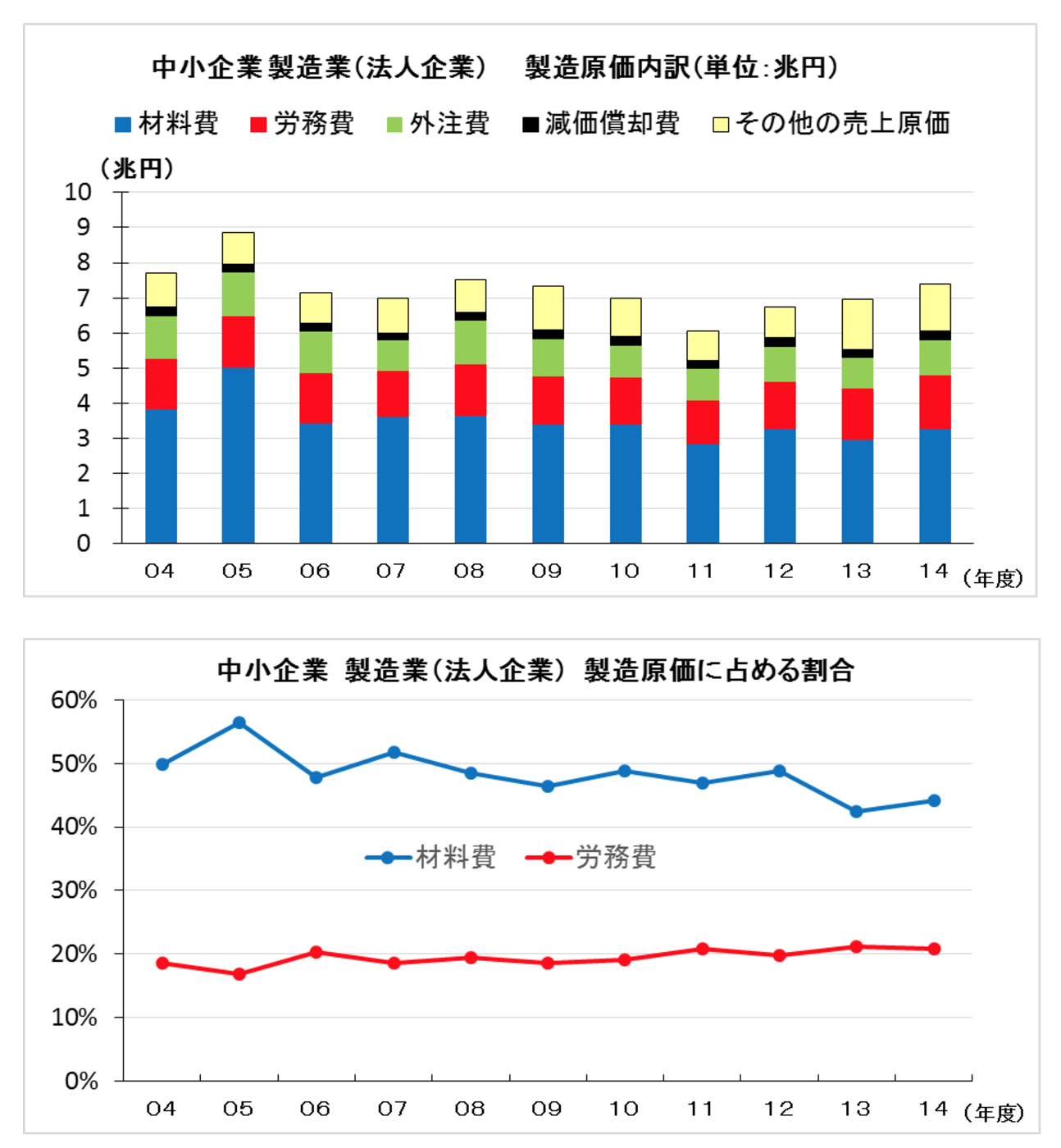
中小企業製造業の平均として、
製造原価に占める材料費は40~50%、
労務費は20%で推移していることがわかります。
2.労務費は付加価値を生み出すための資産と考える
戦後、高度成長期を迎えた頃の日本の製造現場は、現在とくらべれば労働集約的でした。
その結果、製造原価に占める労務費は現在よりも大きかったことが推測されます。
そのため、当時、コストを下げるための視点は、機械化・自動化にありました。
なにせ、モノを造れば売れる時代です。
一人あたりの生産高を高めれば高めるほど儲かった。
ですから、機械化を進め、現場の人数を増やさなくても増産できる体制を目指した。
機械化し、自動化してガンガン生産し、増員ペース以上に生産性を上げながら、生産量を拡大させていった。
なにせ、日本経済が、今では信じられないような成長率で拡大していました。
こうした時代のコスト低減対象は労務費です。
いかに工数をかけないで増産に対応するか。
いわゆる規模の経済で固定費を中心にコストを低減していったわけです。
そして、現在、工作機械をはじめ多くの生産設備が高度化しています。
その結果、多くの工場では生産設備の技術革新やIT化で生産性は向上し、すでに十分に少ない人員体制で生産活動を行っている工場が多いと推察されます。
その結果が20%という数値です。
労務費はコスト削減の対象ではなく、付加価値を生み出すための資産として考え、高付加価値化の活動の効率を上げるという視点を、今後は持ちます。
人財を活かして高付加価値化を推進するという視点です
3.材料費を重点的に管理する
したがって、現在、コスト削減、つまり付加価値拡大のために取りあげるネタの中心は材料費です。
製造原価に占める材料費の割合は40~50%です。
材料費は製造原価に占める割合が大きい上に、原材料価格はグローバル市場の元で大きく変動します。
材料費は、付加価値増減への影響度がとても大きいわけです。
したがって、製造原価に占める材料費の割合を低減すること、つまり原材料の原単位を小さくすることが価格変動への対応力を上げることにもなります。
自動車部品サプライヤーのようなB to Bのビジネスでは、契約上原材料の価格高騰分を製品単価へ転嫁できる場合もあります。
しかし、一般消費者向けのビジネスの場合、材料費高騰分を価格へ転嫁するか否かは経営判断によります。
競合が、材料費高騰分を価格に上乗せしたとします。
一方、自社工場では、原単位低減の効果のおかげで、高騰分を自助努力で吸収できたとします。
競合は値上げしたけれど、自社製品は価格据え置きで対抗した。
勝負の結果は明らかです。
材料費の付加価値へ与えるインパクトは小さくありません。
だから、原価に占める割合の多い材料費は重点的に見ていきたいのです。
原単位という数値で見える化することで、継続的な管理が可能です。
異常時の変化や改善時の効果を客観的にとらえられます。
こうした数値を見続けることで、現場が異常を感知するセンスも磨かれます。
まとめ
製品の種類が多い場合、どのように材料費の管理をやればイイのだろうか?
製品ごとに、標準原単位を設定して、それとの差異を管理する。
材料費が付加価値に与えるインパクトは大きいので原単位で継続的に見続けることが肝要である。