仕組みがなくて生じる無効時間が最大のムダである
仕組みがなくて生じる無効時間が最大の「ムダ」であり、現場にはその「ムダ」の問題解決の見通しを示すことが欠かせない、という話です。
1.「ムダ」を省く
IEの目的は最適(最経済)なワークシステムを設計することにあり、常に全体最適の視点を持つことが欠かせません。
全体最適のための部分最適です。
そして、部分最適としての具体的な取り組みは「ムダ」を省くことです。
「ムダ」の省き方にもカイゼン水準とイノベーション水準があることに留意します。
陸の交通手段として馬車が全盛期の頃……。
より早く、短時間で目的地に着くための手段を考えねばならなかったとします。
- 馬が引きやすいように馬車の荷台を軽量化したり、転がり抵抗が小さい車輪を考えたりするのはカイゼン水準。
- 馬に代わって”自動車”を考えたりするのはイノベーション水準。
発想の視点は使いわけますが、いずれにしても「ムダ」を認識するところからがスタートです。
モノづくり現場の重要な役割のひとつは、この「ムダ」を見つけることです。
「ムダ」を「ムダ」として感じる現場がなければIEは成立しません。
そのために、現場リーダーや各工程のキーパーソンは常に現場の望ましい姿を描く必要があります。
現場が現状と望ましい姿のギャップを認識し、「ムダ」を「ムダ」として感じるようにです。
工場における稼働時間、不稼働時間の分析はモノづくり現場で「ムダ」を探すためのひとつの手段です。
所定労働時間から休憩時間を除いた就業時間が現場の持ち時間です。
この就業時間の内訳を分析すると不稼働要因が色々あることに、改めて気が付きます。
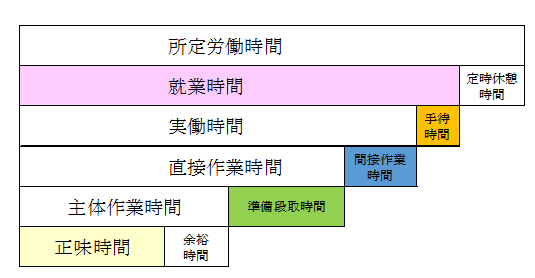
就業時間に占める正味時間を最大化することが、経営者の重要なテーマのひとつであることにも思い至ります。
「不稼働時間」として認識された「ムダ」を除去するためにIEが手法として生かされます。
2.付加価値の視点で「ムダ」を探す
上図では直接に生産活動にかかわる時間、言い換えると顧客へ届けたい「コト」を表す情報を媒体(メディア)に転写する作業である「正味時間」以外を不稼働時間と解釈します。
ですから、上図では直接に素材を加工する時間以外を「ムダ」としています。
直接に素材を「加工」することにかかわる時間を「正味時間」とする考え方は昔も今も、そして将来も変わることはありません。
ただし、「ムダ」の見方や、活動の方向性はドンドン変化していきます。
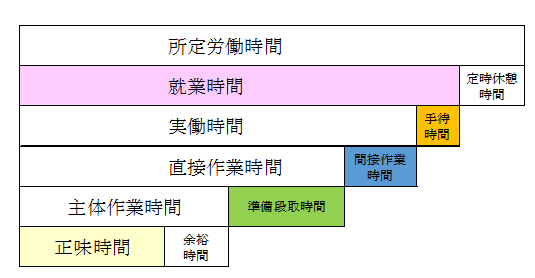
準備段取時間(緑色)を削減しようとするならば、生産ロットを大きくするために受注情報をうまく生産管理に生かす取り組みなどは手段のひとつになります。
しかしながら、今後、中小モノづくり企業の生き残るための戦略となるマスカスタマイゼーションを考えると真逆の取り組みが必要です。
小ロット化しドンドン準備段取回数を増やす。
当然、1回あたりの準備段取時間を減らす取り組みを進めますが、回数が増えた分、トータルの準備段取時間は増えるかもしれません。
その分、正味時間が減り、残業時間が増えるかもしれません。
しかし、顧客の多様な要望へ機動性良く対応することから、単価アップが可能になり付加価値の総額が増えることも期待できます。
必ずしも準備段取時間(緑色)の総時間が増えたからダメとは単純に言えません。
また、今後は現場も付加価値を高める業務が求められます。
モノのインターネント(IoT)の導入により単純作業から解放された現場では現場独自の付加価値創出の取り組みが期待されます。
直接に生産活動とは関係ないため、間接時間(青色)は「ムダ」時間とされていました。
その間接時間が、現場独自の付加価値拡大を目指した活動のために増えていくもしれません。
将来への種まきとなる活動で付加価値を長期的に拡大するならば、「ムダ」とは言えないでしょう。
正味時間の重要性は維持しつつも、その他の不稼働要因への対応方針は考え方を変える必要がありそうです。
そうした視点から考えると、就業時間における「ムダ」の判断基準は、付加価値を生むのか、生まないのか、という点になりそうです。
「モノ」の生産のみではなく、将来的な視点も含めた付加価値創出に着目です。
これからは現場も「モノ」を造りのみならず、「コト」も創出する。付加価値を高める活動こそが求められます。
ですから付加価値を生まない時間こそが排除すべき対象です。
これには大きく2種類あると考えます。
- 真の有効時間(付加価値を生む時間)に(不本意に)付加されてしまう時間
- 管理が悪くて生じる無効時間
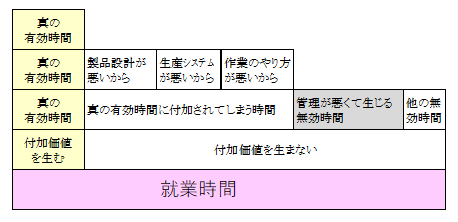
そして、前者はさらに付加される原因によって3つに分類されます。
- 製品設計が悪いから
- 生産システムが悪いから
- 作業のやりかたが悪いから
これは、まさにカイゼンのテーマです。
こうした問題に起因して付加される時間(ムダ)だからです。
まさに部分最適化のターゲットであり、IEを活用します。「ムダ」を省くための王道です。
一方、管理が悪くて生じる無効時間。これは現場ではどうしようもありません。
現場リーダーがフォローし、工場全体の課題として全体最適の視点から仕組みづくりをすることが唯一の解決策です。
これを現場の頑張りに期待しているようでは管理者失格。
全体最適化を目指した仕組みづくりが唯一の解決策であることに留意します。
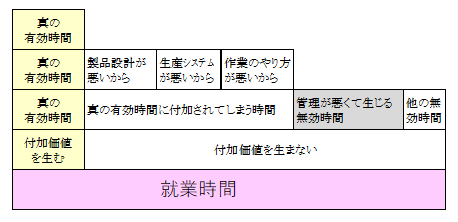
プレス打ち抜き加工を中心にした組み立て工程をもつ金属加工メーカーの現場での話です。
見込生産の定番製品に加えて数種類の受注生産をしていました。
数種類の受注生産製品が突発受注となって生産ラインに混乱を起こさないようにすることが現場からの要望でした。
数種類の受注生産製品のなかで、数量も多いうえに受注から納期までの工数が大変短い製品がありました。
物量から判断すると1ケ月程度の納期が欲しいところを、受注確定が毎度遅く、納期が2〜3週間程度で設定せざるを得ない状況になっていました。
現場からは、受注を早めに確定するように要望がありましたが、お客様がなかなかそう対応してくれないとのことで、納期を遵守するために、最終的にはすべて現場へしわ寄せがきていました。
現場の工程を現場自身が組み直し、残業をしながらの対応でした。
「こうした生産管理上の調整は事務所担当者の間で事前にして欲しいですよね。現場に丸投げはやめてもらいたいです。」
取引上、出入りしていた現場で知り合ったTさんからこんな言葉を聞きました。
残念ながら、仕組みづくりが進んでいない現場でした。仕組みがないしわ寄せが現場に来ていた事例です。
こうした現場では、突発のそうした受注生産が入ると、工程を組み直すムダ、予定外の段取りをするムダ、残業のムダなどの、明らかな「ムダ」が生じます。
このような状況では「管理が悪くて生じる無効時間」それ自体も問題ですが、それ以上に、こうした問題が放置されることによる現場のモチベーション低下の方がより深刻です。
ムダを省く時、カイゼンの対象になる「真の有効時間に付加されてしまう時間」の解消は現場に任せます。
IEの手法を学び、駆使すればできます。
しかし、「管理が悪くて生じる無効時間」については現場はどうしようもありません。
現場リーダーが先頭に立って仕組みづくりをするべきです。
仕組みづくりは、時間がかかるかもしれません。それでも構わないのです。
重要なのはこうした問題を放置せずに、問題解決に向かって工場全体が動いていることを現場に示すことです。
見通しを示された現場は、目の前の少々の困難には頑張って対応します。
避けたいのは問題を放置して、その対応を現場へ丸投げすること。現場から管理者への不信感が生まれます。
最も避けたいことです。
「ムダ」探しは、付加価値を生まない時間のうち、仕組みがなくて生じる無効時間から探します。
現場のやる気にかかわる重要事項であることに留意したいです。
まとめ。
仕組みがなくて生じる無効時間が最大の「ムダ」であり、現場にはその「ムダ」の問題解決の見通しを示すことが欠かせない。
株式会社工場経営研究所 「儲かる工場経営」メルマガ ご登録ください。
毎週火曜日配信中。
https://48auto.biz/koujoukeiei/registp.php?pid=3