トヨタのMIRAIから責任あるモノづくりを学ぶ
責任あるモノづくりでは、外注丸投げという発想はなく、自ら開発、製造を手掛けて、製造プロセスを把握し品質を見る目を養う、という話です。
1.次世代自動車の動力は?
自動車業界で激しい競争を勝ち抜くために各企業が力を入れて開発している2つの分野。
- 運転支援技術
- 軽量化技術
このうち後者は低燃費が狙いであり、環境にやさしい究極のクルマづくりを目指しています。
ですから、低燃費競争の究極の課題は次世代自動車の動力の主流を見極めることにあります。
化石燃料を燃やして動力を得る内燃機関にとって代わる技術は何か?
自動車産業の裾野は広いので、それらに関連した中小モノづくり企業も多く、環境問題に対応した次世代動力の主流にかかわる事業を持てることは企業の存続と成長へ好影響を及ぼします。
従来までの内燃機関で主流であった部品が不必要になることもある一方、新たに需要が拡大する部品もあるわけで、新規に参入してくる企業も少なからずあるでしょう。
現在、ハイブリット車が普及しつつありますが、市場から求められる環境規制が今後も厳しくなることは明らかであり、ハイブリット車に続く環境配慮車の開発は自動車メーカーにとって生き残りをかけた大きな課題となっています。
現在、候補として考えられるのはプラグインハイブリット車、電気自動車、燃料電池車の3つです。
次世代自動車の動力には何が選ばれるのか、これは今後も注目したいテーマです。
2.トヨタは燃料電池車に力を入れている
トヨタ自動車は2014年12月に燃料電池車の量産車「MIRAI」を国内販売しました。
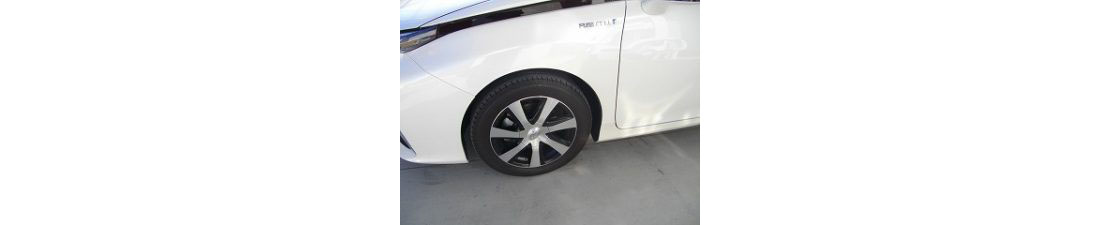
環境問題への対応が求められる中でトヨタが開発に力を入れているのはこの燃料電池車です。
学生時代の実験で水の電気分解というのがありましたが、これは水に電極を通じて通電すると正極、負極から酸素や水素が泡となって出てくる現象でした。
燃料電池の原理は、この水の電気分解の逆で、酸素と水素を反応させて電気を取り出すものであり、副産物は水のみの極めてクリーンな動力です。
燃料電池車もある意味では電気自動車ですが、電池を搭載しているのではなく、水と酸素の化学エネルギーから直接電気を取り出す効率性の高いクリーンな発電設備を搭載している点で電気自動車と性質を異にします。
トヨタ自動車専務役員伊勢清貴氏は「MIRAI」の販売実績及び販売計画について
次のように語っています。
MIRAIの生産台数は2015年に700台でしたが、2016年の年間生産能力は2,000台に増えています。
2017年にはこれを、3,000台へ高める予定です。
さらに、2020年ごろには全世界で年間3万台、日本国内市場向けでは月間1,000台くらいの燃料電池車を生産することを計画しています。
(出典:日経モノづくり2016年7月号)
自動車全体に占める割合はまだまだ小さいですが、10年先、20年先を見通して着実に実績を積み、厳しい環境規制に対応できる量産車に仕上げていくことを目指しています。
そして、この過程で欠かせないのは車自体の開発と共に、燃料電池に関連した新たな部品の品質の確保です。
これまでの動力は内燃機関であり、その分野の知見は膨大な程に積みあがっていますが、自動車に搭載する燃料電池に関する知見はまだまだ不十分。
加えて、ガソリンに代わって、車に充填される「水素」への安全性のイメージを社会へ広める必要もあります。
この水素利用を広める考え方、および燃料電池関連技術への対応方針について、伊勢氏は次のように語っています。
FCVを最初に発売する際には、「水素は危険」というイメージを持たれることを心配しました。
水素は漏らさない工夫はもちろん、水素は空気よりも軽くて拡散しやすいといった基本を忠実に守れば、安全性を担保できます。
(中略)
FCVの心臓部である燃料電池スタックや水素タンクは、トヨタ自動車が開発・製造しています。
これらを自ら手掛けた理由は、量産規模を拡大した時に、品質面で何を押さえれば良いかが分かるからです。
将来的にこれらを外部調達するにしても、開発や製造を経験することで品質を見る目が養われます。
(出典:日経モノづくり2016年7月号)
自ら「製造」することで品質を見る目が養われるという考え方はモノづくりを事業とするうえでとても大切です。
三現主義を通じて獲得されたノウハウほど確固たる経営資源はありません。
トヨタが燃料電池車を普及させるには、並行して、社会での水素利用を拡大させる必要もあり、水素インフラの整備が避けて通れない仕事です。
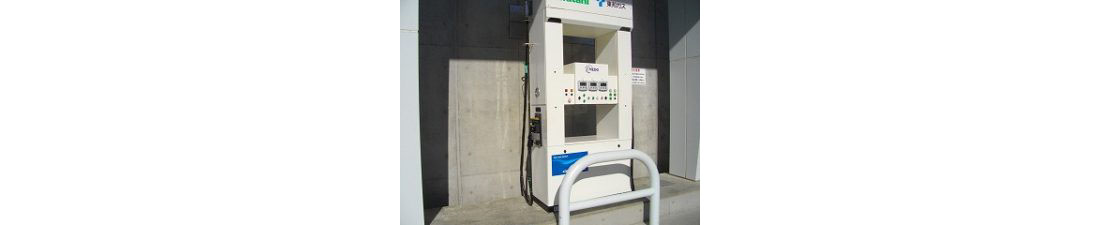
ガソリンに代わって水素を身近な燃料として取り扱うことができるような社会を創出しなければならないわけで、水素の安全性を発信し続ける努力が欠かせません。
そのためには燃料電池に関連した技術にはことごとく熟知した状況を目指す必要があります。
開発当初から自社では手を染めず、他社依存の外注で対応する姿勢では、いざ根本的な問題が持ち上がった場合、トヨタ自身は手も足もでなくなります。
こうした分野の要素技術がキーテクノロジーとなり、そこを他社が握ることにもなりかねません。
そこで、トヨタとしては、まずは、学ぶこと、知ることを目的に、全て自前で開発し製造しています。
責任あるモノづくりでは、欠かせない考え方です。
3.責任あるモノづくるとは何か
完成品のみならず、部品のような「製品」でも、その製品を完結して製造できる技術を有してさえいれば、最終顧客がそれ自体に価値を見出してくれることがあります。
キーとなる重要製品を内製で対応することは、製造プロセスを把握することにつながります。
モノづくりは前工程と後工程の「連鎖」で構成されていると考えるならば、製造プロセスの全体像を把握していることの大切さが理解できます。
そして、それ自体も強みになる。
モノづくりの事業形態のなかには「工場を持たない(ファブレス)」形態もあります。
これは、仕事を時間で評価しない究極の事業形態であり、中小モノづくり企業も目指すべき形態であると考えています。
ただし、モノづくりの現場を全く持たず、全て、最初からモノづくりは外注丸投げ、という事業形態も避けるべきです。
製品の品質は予期しない現象に影響されるものであり、これは、どれほど製造現場のIT化が進もうが変わらない不変の経験則です。
多様な技術が複雑に組み合わさって構成されているのが製造ラインである以上、実際に製造してみないことには見えてこない現象が必ず存在します。
ですから、少なくても試作レベルのモノづくりはできる現場を持っていることが、今後の国内メーカーの望ましい形であると考えています。
つまり、「マザー工場」の考え方です。
新しい技術に挑戦するならばなおさらです。
大量生産したらどのような問題が発生しうるのか、そしてそれが安全へどのような影響を及ぼしかねないのか把握しておくことはモノづくりを事業とする企業の責任です。
メーカーにおける不正行為が散見される昨今、責任あるモノづくりに必要なことを考えたいです。
責任あるモノづくりにおいて、外注丸投げという発想はありません。
戦略的にコストを下げることと責任あるモノづくりを両立させようとするならば、次の2点に留意します。
- 自社製品のキーとなる製造プロセスは、全てに渡って把握、理解する。
- 戦略的に外注化するにしても自社ノウハウが積みあがっていない段階では避ける。
工場オペレーションにおいて、自社製品のキーとなる製造プロセスの標準化作業は、重要な業務のひとつです。
こうして整備された作業標準票は外注化を検討する時に欠かせない道具となります。
トヨタの燃料電池車の開発プロセスから責任あるモノづくるとは何かを学ぶことができます。
まとめ。
責任あるモノづくりでは、外注丸投げという発想はなく、自ら開発、製造を手掛けて、製造プロセスを把握し品質を見る目を養う。
株式会社工場経営研究所 「儲かる工場経営」メルマガ ご登録ください。
毎週火曜日配信中。
https://48auto.biz/koujoukeiei/registp.php?pid=3