チョコ停など現場の実態を「見える化」して、設備稼働率をアップし、機会損失を削減
精密機器製造業D社様
年商:250億
背景
生産性の向上やコストダウンといった要望を受け、設備の自動化が当たり前となった製造現場。
しかし、ここでしっかり把握しておかなければならないのが、チョコ停の有無。
回数次第ではかえって設備稼働率やコストの低下を招きかねないため、考えられる全ての原因を抽出、解析し、根本的な不具合の改善が不可欠となっています。
課題・問題
売上ダウンの要因を究明したところ、製造工程に問題が……
精密機器製造業D社は、ここ数年、売上の落ち込みが激しく、バランスシートやキャッシュフローが一向に改善されないという悩みを抱えていました。
そこで外部の経営コンサルタントに依頼して原因を究明してみたところ、どうやら問題の根源は製造工程にあるらしいとのこと。
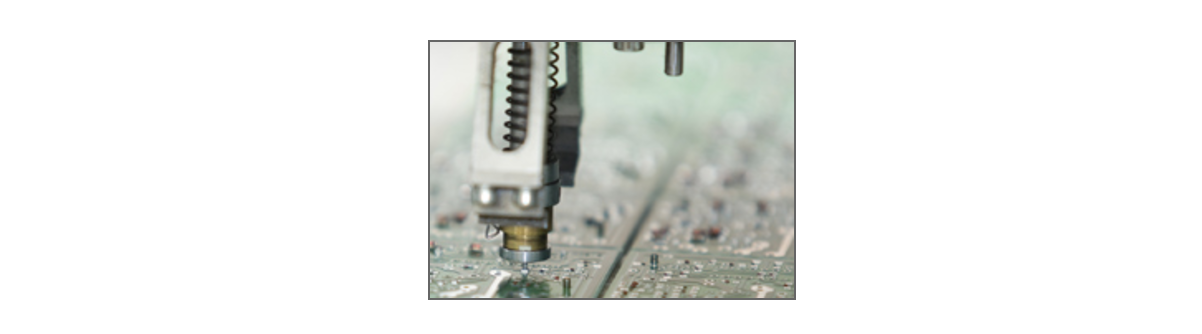
この報告を受け、経営陣に呼び出されて改善策のプランニングを命じられた工場長のK氏でしたが、彼自身も常に現場にいるわけではないために課題の本質が掴めず、何一つ改善への糸口が見いだせずに困り果ててしまいました。
見えない機会損失額は1日50万円! 問題の原因は度重なるチョコ停と判明
そこで、K氏は工場の現場をしばらく監視してみることに。
すると、監視を始めて早々、一時的なトラブルによって設備の停止や空転を招くチョコ停が発生。
後からわかったところによれば、発見から連絡、そして復旧まで、平均10分もかかっている様子。
1日平均30回チョコ停が発生することから、機会損失は50万円/日にも及んでいました。
「折しも、当社では売上の落ち込みが回復しないために製造現場のスタッフを削減したばかり。機会損失分の50万円/日を考えると、スタッフの削減が正しい選択だったのかどうか……」(工場長K氏)。
何とか現状を打破できないものかと、社内で解決に向けた議論が本格的にスタートしました。
課題解決のポイント
1. バランスシート、キャッシュフローがなかなか改善されない
2. 度重なるチョコ停により、稼働率低下と多大な機会損失が発生
3. 人員削減の影響もあり、見落としがちな現場の実態
解決策
解決後の効果・結果
1. コストをかけず、簡単にチョコ停の分析が可能に
2. 設備稼働率・工場スループットを向上し、機会損失も削減
3. 仕掛品を無くし、売上アップを実現
稼働率管理やチョコ停の分析で、製造現場の実態を可視化
本格的な機械の故障とは違い、現場スタッフの手で復旧可能なトラブルとして軽視されがちなチョコ停ですが、頻度次第では深刻な設備稼働率の低下を招き、コスト面での影響も計り知れません。
そこで、D社が打開策として導入を決めたのが、「GLOVIA smart 製造 MES PATCHART」。
経営陣の一人が知人の紹介で見つけてきたこのツールは、稼働率管理やチョコ停の分析が簡単に行えるソリューションツール。
大掛かりなシステム投資なしに、早く、安く導入が可能なことと、既存のシステムとの連携や拡張が容易なこと。
この2点が導入の決め手となりました。
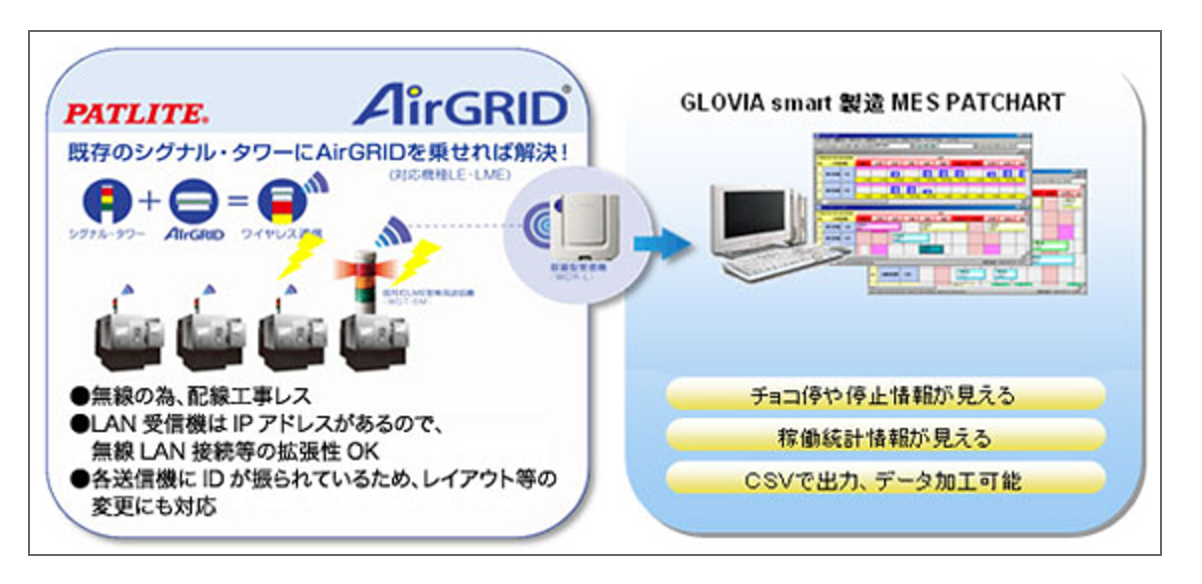
生産停止による機会損失を70%削減し、売上が好転
予算や手間をかけず、設備の稼働状況をタイムリーに自動収集して画面表示する「GLOVIA smart 製造 MES PATCHART」の導入により、製造現場の可視化を実現。
蓄積された設備稼働情報を分析することで、設備稼働率・工場スループットの向上と機会損失の削減が可能になったD社。
具体的には、発見から連絡、復旧までに掛かる時間を60%削減、生産停止による機会損失に至っては実に70%も削減されたそうです。
「仕掛品が無くなり、売上を伸ばすことができました」と笑顔で語る工場長のK氏をはじめ、経営陣も導入を歓迎しています。
出典:『チョコ停など現場の実態を「見える化」して、設備稼働率をアップし、 機会損失を削減』株式会社富士通マーケティング