【IoT等活用事例】複数の成形機データを取得・管理し、迅速な製品情報の追跡等を実現(笠原成形所)
事例のポイント
- 複数メーカの射出成形機と接続可能な⽣産管理システムを導⼊
- 各機械の稼動状態を追跡でき、直近数ヶ⽉の注⽂・⽣産データを分析することで、今後の受注動向の予測や、効率的な製品管理が可能
企業概要
笠原成形所(新潟県南⿂沼市)の主な事業は、⾃動⾞分野のコネクタ部品や、医療分野の内視鏡部品の製造・仕上げ・検査。⼀般的に、射出成形時の型締⼒が100トン以下となる成形品の製造を請け負っている。
従業員に対し、資格取得を奨励。検査部⾨では全員が品質管理検定を取得しており、品質の理解を深め検査に携わることのできる体制としている。
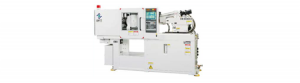
解決を目指した課題
従来、製品製造に関わるさまざまな情報の管理を紙媒体で⾏なっていたため、管理が煩雑となり、⼿間と時間がかかっていた。そのため、各種情報を簡便に管理でき、製品に関わる情報を即座に追跡することができる仕組みを求めていた。
課題への対応
きっかけ・経緯
同社は、12年ほど前に、成形機メーカの展⽰会において、⽣産管理システム「MICS」を提供するムラテック情報システム株式会社と出会った。当時、さまざまなメーカの射出成形機と接続できる⽣産管理ソフトウェアは「MICS」だけであったため、導⼊に踏み切った。
具体的な解決手段
当初は、⽣産管理システム「MICS」を標準パッケージで導⼊していたが、その後、カスタマイズを重ねた。例えば、2014年、15年には「ものづくり・商業・サービス新展開⽀援補助⾦」を活⽤してシステムの改善を⾏った。
その結果、多くの従業員が⾃分でデータ分析までできるような仕組みにシステムが仕上がるなど、同社はIT企業と⼆⼈三脚で⾃社にあったシステムを作り上げてきた。
具体的には、成形品を製造する際の、⾦型のショット信号を取得する機能を有し、そのショット信号等データから、どの製品をどの程度製造しているかを検知し、⽣産管理と紐付けることも可能となった。
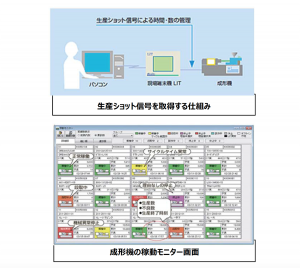
また、複数メーカの成形機について、稼動中、停⽌中等の稼働状況を⾊別に⼀覧にし、画⾯表⽰できるなど、稼動状態を簡単に追跡できる仕組みも構築した。
さらに同社では、従業員が1⼈⼀台タブレット端末を所有しており、その画⾯を通じて「MICS」の情報を閲覧し、製造現場で成形機ごとの使⽤時の注意点や成形計画等を確認できるようになった。また、タブレット端末を活⽤した⽣産指⽰や、確認を⾏なうことも可能となった。
メリット・効果
従来は、さまざまな⽣産に関する情報管理を紙媒体で⾏なっていたため、⼿間とコストがかかっていたが、「MICS」を使い、データで各種⽣産情報を管理することで、情報管理の⼿間とコストを削減するとともに、情報同⼠が繋がり、製品情報を即座に追跡することが可能となった。
また、⽣産データを蓄積することにより、データに基づいた在庫管理が可能になった。例えば、直近数ヶ⽉間の注⽂・⽣産データを分析することで、今後の受注動向の予測が可能となり、それに基づく材料在庫の確保や、製品製造量の調整等、効率的な製品管理が実施できている。
さらに、受注から発注までの全データをシステム内で管理できるようになるため、ISO等の認証取得時の審査においても、⽣産実績の提⽰等をスムーズに対応することが可能となった。
同社では、12年前にシステムを導⼊し、毎年、ムラテック情報システムとともにカスタマイズし続け、徐々に応⽤的な機能をシステム内に導⼊した。
そうした経緯もあり、従業員が抵抗感を受けることなく、現在のシステムに慣れ、⼗分に使いこなすことができている。
出典:経済産業省関東経済産業局「中小ものづくり企業IoT等活用事例集2017」