『改善ぷちセミナー』モーションマインド
※当コンテンツは『面白狩り』の提供でお届けいたします。
1.モーションマインドって何?
モーションマインドなんて聞いたことがないという人の方が多いでしょうね。
でも、これは改善の基本中の基本の考え方(というよりも意識とか態度というニュアンスかな)です。
理屈や手法を学ぶ前に身につけておきたいIEの原点と言うべきものです。
そのIEの創始者と呼ばれる二人のアメリカ人がいます。
一人が、F.W.テイラー(Frederick Winslow Taylor 1856~1915)。
さまざまな功績のある人ですが、簡単に言えば、経営の中に科学の視点を取り入れた最初の人。
もう一人が、F.B.ギルブレス(Frank Bunker Gilbreth 1868~1924)。
この人は、どうしたら仕事がもっと楽になるかを考えた人。
言わば、マジに改善をやった最初の人です。
最初の人って呼ぶのは、それまでだれも現状に疑問を抱かず、何も変えようとしなかったということです。
彼の有名なエピソード……
レンガ積み職人の見習いとなった若きギルブレス。
早く一人前になろうと先輩たちの仕事をじっと観察しました。
みんな熟練の技をもってテキパキ仕事をこなしていきますが、一人として同じやり方の人はいません。
それぞれの先輩から受け継いだ方法を忠実に守っているのでした。
さらに観察を続けて、もっと楽なやり方があることに気付きました。
そのアイディアを親方に話して実際にやってみると、1/3以下の時間でムリなく作業ができました。
こうして、2000年以上の伝統を誇るレンガ積み作業に、一人の若者が大変革をもたらしたのでした。

どうしたらもっと楽にできるか、どうしたらもっと能率よくできるか、これをいつも意識し探求する姿勢がモーションマインドです。
2.仕事を観察する
青年ギルブレスは、レンガ積みという作業をどんなふうに観察したのでしょうか。
レンガ積みは、次のような2つの単位作業で構成されています。

もう少しよく観察してみると、どんなことをしているのかが見えてきます。

でも、これではまだ何が問題なのかわかりません。
もっとじっくり観察しましょう。

ここまで細かくしたら、人によってやり方の違いが見えてきました。
例えば、Aさんはレンガをモルタルに置いてから位置を調整するのに、Bさんは位置合わせしてからレンガを置いていました。
さらに観察を続けます。
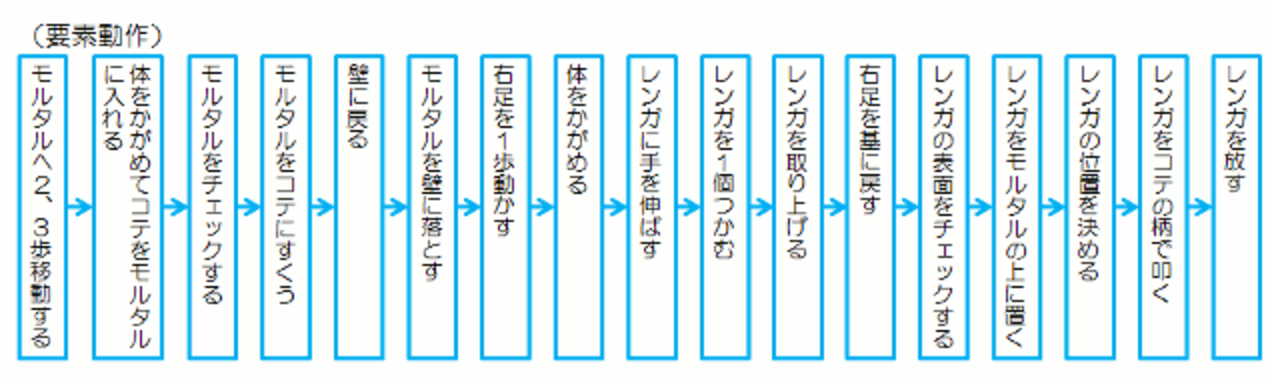
ここまで細かくすると、こうすれば良いのにと思うことがたくさん見つかりました。
みなさんはいかがですか? 考えてみてください(答は文末に)。
現場に出て実際の仕事を観察すること。
それも、ただ漫然と眺めているのではなくて、上の例のようにじっくり観察して動作に細分化していけば、改善の手掛りを得ることができます。
ギルブレスは、こういう見方をみんなができるようになれば良いなあと考えました。
そのアイディアを提供したのが妻のリリアン(Lillian Moller Gilbreth 1878~1972)でした。
彼女は、仕事の中に現れる18の要素動作を記号化して、誰でも簡単に分析できるようにしたのです。
これにギルブレスを逆にしたサーブリッグズ Therbligs(sは記号が複数のため)と名付けたのは有名な話。
言わば、最初のIE手法と言うべきものでした。
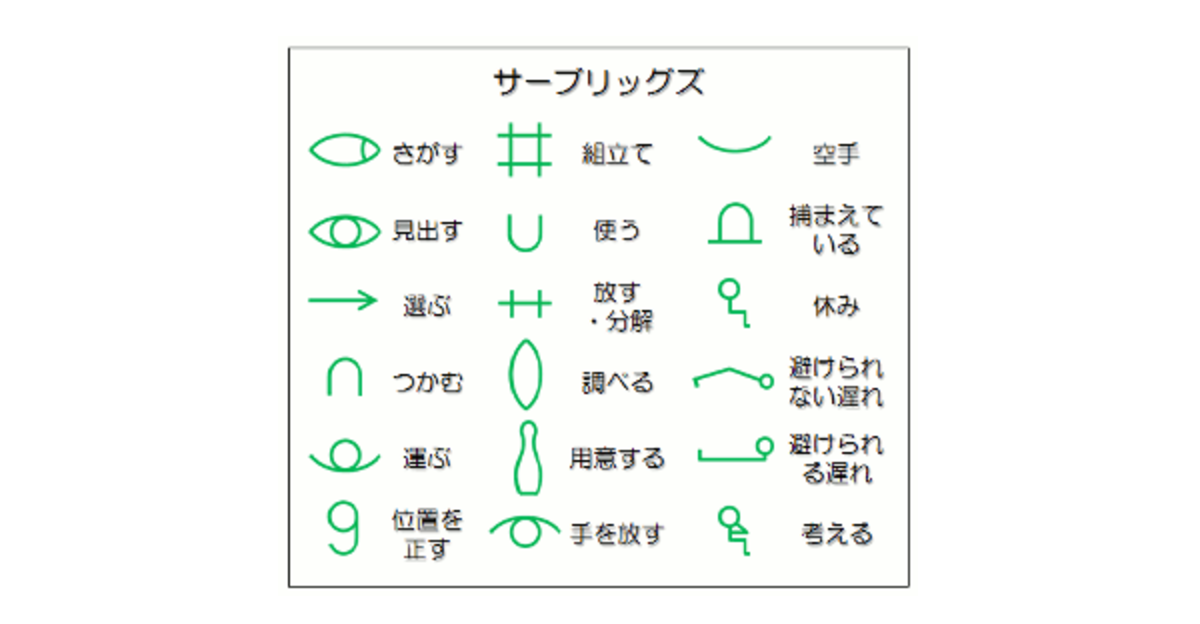
現在はもう、このクラシカルな手法が使われることはありません。
しかし、このギルブレスの観察から学ぶことはとても多いと思います。
実際の仕事を観察する際に、どのように着眼し問題点を見出すのか、大いに参考にしていただきたいのです。
3.PTS法
サーブリッグズが使われなくなった理由の一つがPTS法の開発でした。
PTS法も一般にはあまり馴染みがないと思いますが、IEの手法としては一時期大いに流行したものです。
普通、作業時間というのは人によってばらつくものです。
ところが、「つかむ」とか「手を伸ばす」というような要素動作で見ると、この個人差がほとんどありません。
このことに気付いたのがA.B.シーガー(Asa Bertrand Segur 1886~1975)という技術者でした。
シーガーのアイディアは、あらかじめ動作にかかる正確な時間を設定しておいて、動作分析で現れた各動作の時間値を合計すれば、作業全体の時間が見積もれるのではないか、というものでした。
これが、PTS法(Predetermined Time Standard 既定時間標準法)と呼ばれるものです。
シーガー以降、多くの研究者によって様々なPTS法が提案されましたが、日本ではWF(Work Factor)とMTM(Method Time Measurement)という方法がよく知られています。
下は、MTM2と呼ばれる簡便法による分析例です。
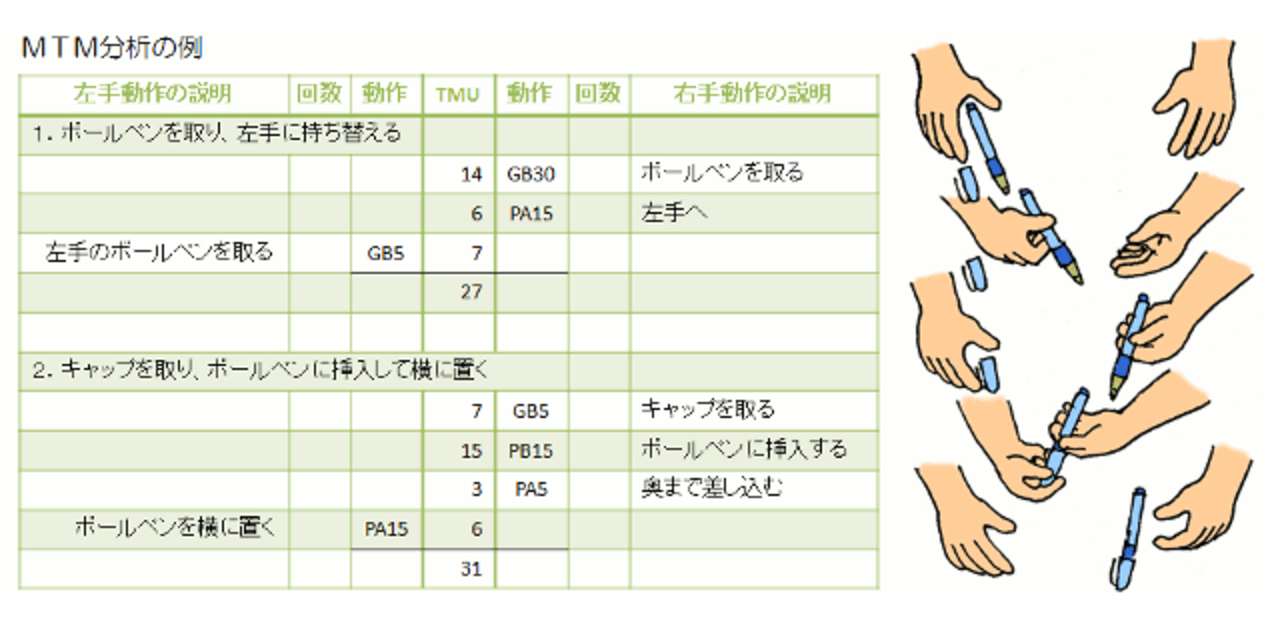
PTS法を使うと、ストップウォッチで実測するよりも正確な時間が得られます。
一方で、正しく使うには細かいルールを習得した資格が必要で、実際の分析には多くの時間と手間がかかります。
つまり、正確性を取るか実用性を取るかの綱引きの中で、次第に学術的な論争と手法の売り込みばかりが目立つようになり、実利を求める経営者の関心が失われてしまいました。
私もPTS法の資格をいくつか持っていますが、その中ではモダプツ(MODAPTS:Modular Arrangement of Predetermined Time Standard)という方法が使いやすいと感じています。
PTS法は動作分析がベースですから、使いこなすことでモーションマインドが自ずと鍛えられている実感はあります。
モダプツは簡単なので、小集団活動で作業改善によく利用されます。
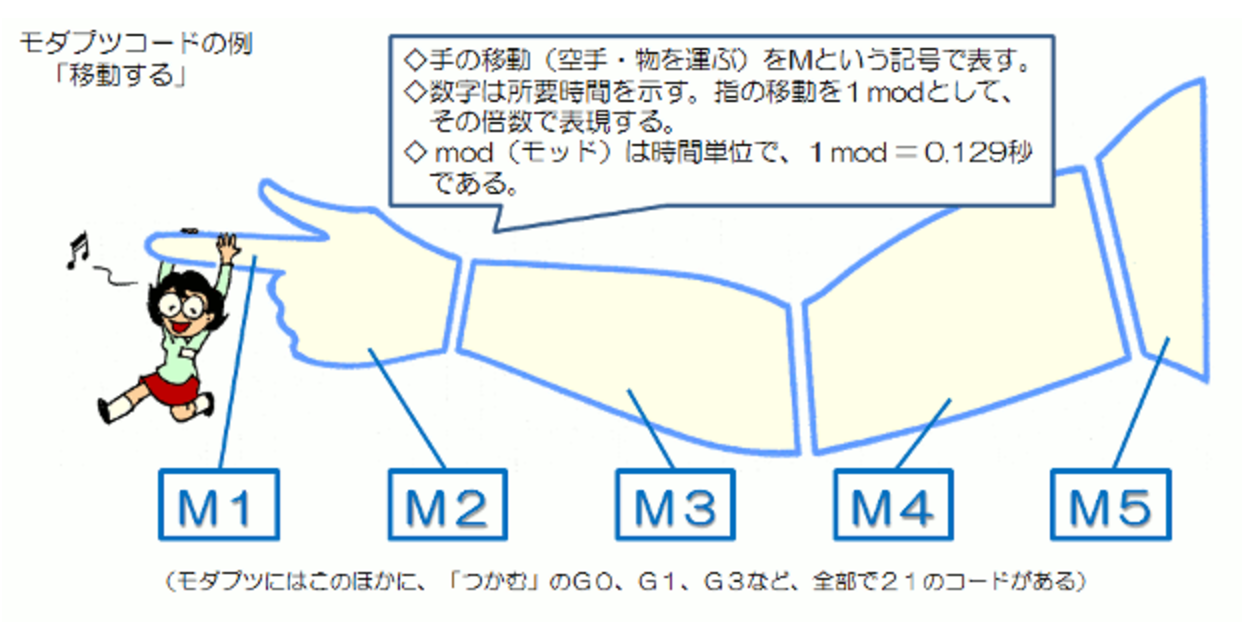
しかし、時間把握に関しては、机上計算で求めるやり方に不信感があるのか、ストップウォッチやビデオを利用して実測する方が手取り早くて安心できるようです(ただし、実測した値がそのまま正しい作業時間である保証はないので注意が必要です)。
4.動作経済の原則
モーションマインドを持って改善を繰り返していくと、だんだん改善のコツのようなものが見えてきます。
そのようなコツをまとめたのが動作経済の原則です。
この原則は体系的と言うより、先人たちが改善した経験から積み重ねてきた虎の巻のようなものです。
文献に紹介されているものを見ても著者によってさまざまですし、これから新たに加わる原則もあるかもしれません。
また、動作だけでなく、レイアウトや自動化などについての原則もあります。
しかし、これらの原則を知識として覚えるだけでは、使いこなすことは難しいでしょう。
みなさんが実際に改善を行って、その経験から身につけていくこと。
みなさん自身が悩み、考え、体で覚えた生きた原則を持って欲しいのです。
ここではごく一般的な基本原則の一部を紹介します。
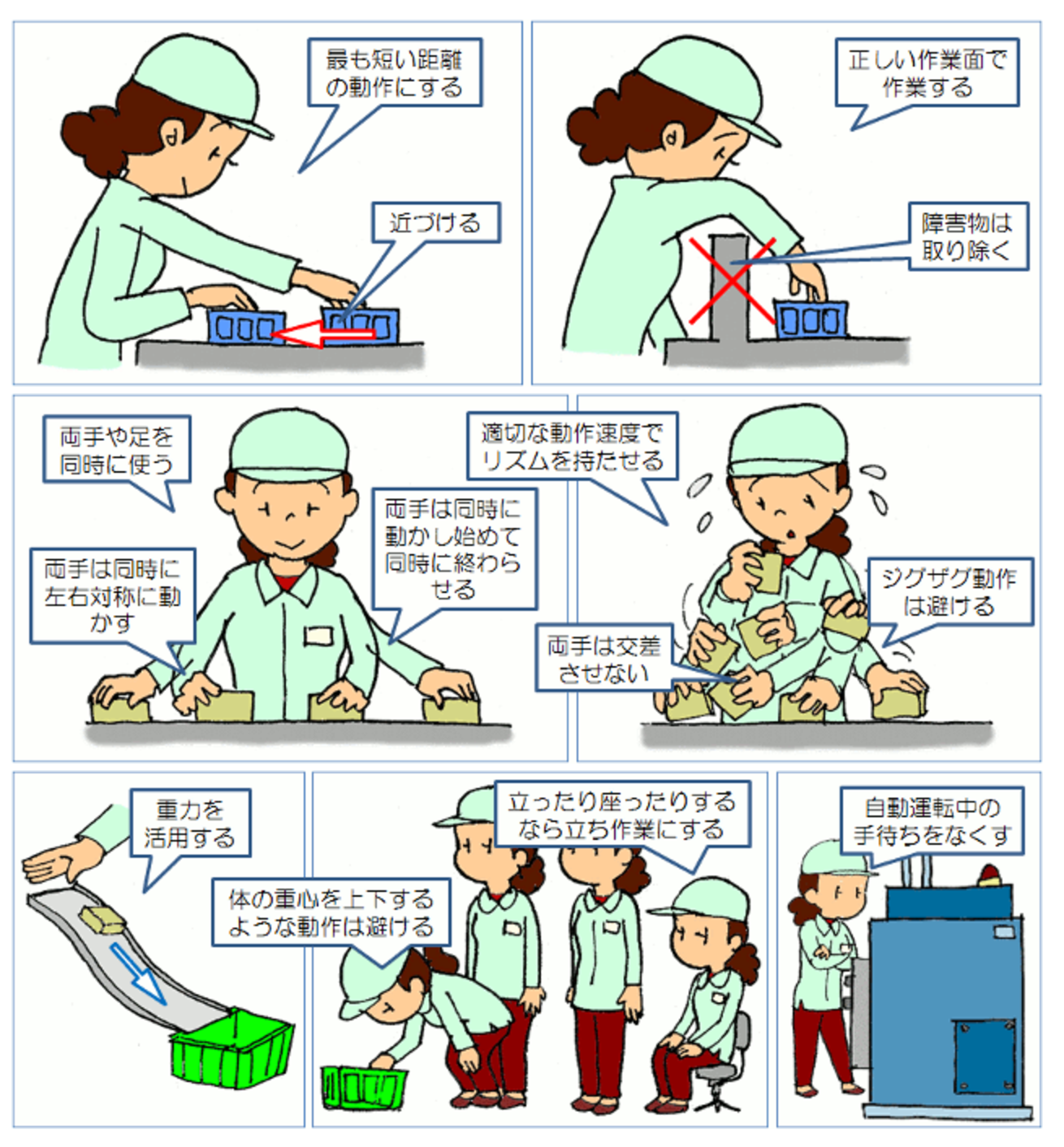
理屈をこねくり回して能書きばかりたれてないで、さっさと現場に行って頭と体を動かしましょう。
5.問題に気付くまで動くな
上の原則を見て、大抵の人が「こんなの当り前じゃないか」と思います。
ところが、そう思う人に限って、現場に出ても目の前にある問題が見えていません。
そして、その当り前が難しいことに気付いていません。
大野耐一さんと言えば、トヨタ生産方式を確立した有名な人です。
私などは講演を2、3回聞いた程度の関わりしかありませんでしたけれど、大野さんのエピソードの中でとても興味深い場面があります。
工場のラインを視察していた大野さんが、ライン長を呼んで来て、目の前の工程の問題を指摘しろと言います。
ライン長が答えられないでいると、大野さんはライン長の立っている床に、チョークで円を描いて、「問題がわかるまでこの円から出ちゃいかんぞ」と言って、去っていったというのです。
このライン長は、問題に気付くまで、長い時間そこに立っていたというウソのような本当の話。
こんなふうに現場でモーションマインドを鍛えることで、この会社の強さが培われたんだなあと、感心させられたものです。
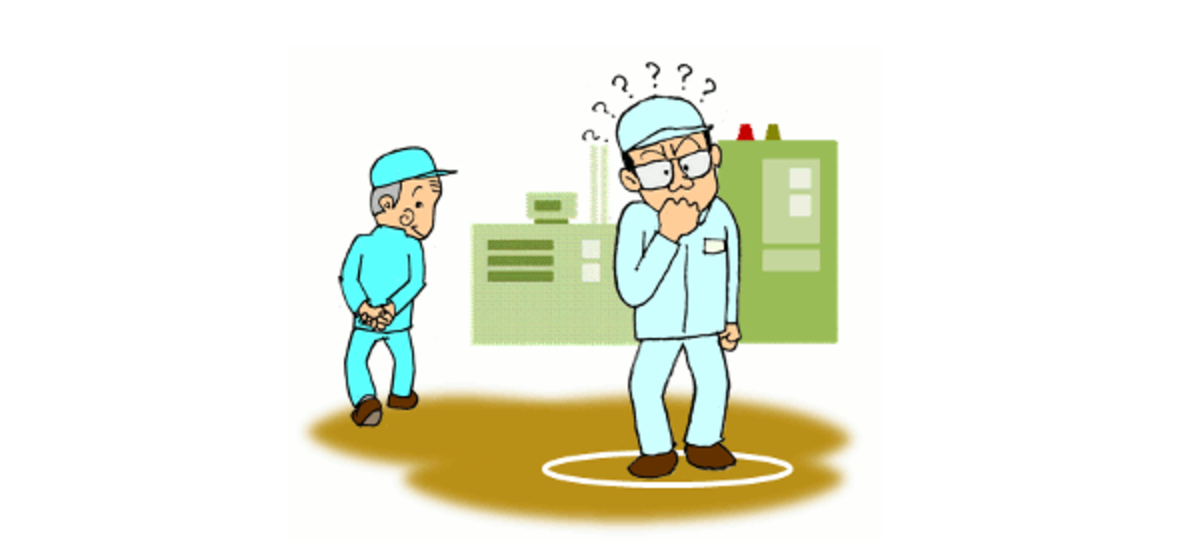
今は、どこの会社もカッコよく仕事をしようとしますから、こういう泥臭くて七面倒臭いことは流行らなくなりました。
下手にこんな真似をしようものならパワハラと受け取られかねません。
また、こんな現場でじっくり観察なんかしなくても、高性能の機械や出来合いのシステムを導入すれば手っ取り早く問題解決できると考えるのでしょう。
機械化が進みITが普及して、手作業での物作りが少なくなったら必要ないと考える経営者もいます。
しかし、いくら機械化が進んでも、人による作業は必ず残ります。
代表的なものは段取作業です。
実際、段取で苦しんでいる会社は非常に多いですし、機械化・オートメ化が進むほどその傾向が強くなります。
むしろ、モーションマインドの重要性はますます高くなっていると言うことができるでしょう。
ギルブレス青年の着眼点は次の通り
①足場を工夫して、作業動作をいつも最適な位置でできるようにした。
……最適作業域の確保
②足場に適当な高さの台を設けて、レンガとモルタルをその上に置くようにした。
……かがむ動作、2、3歩歩く動作をやめた
③使用するレンガの一番きれいな面をそろえて、レンガをあらかじめ木枠に入れておくことにした。
……一つ一つレンガをチェックしなくても済むようにした
④モルタルの調合を工夫して、適正な固さに保てるようにした。
……コテの柄で叩かなくても、手で押しつければ付くようになった。