COP目標達成のためのトヨタでの具体策|元トヨタマンの目
トヨタ式製造変動費予算実績管理の概要
(製品合格数)……(潤滑油使用量)
1月……29,300個……295L
2月……30,100個……301L
3月……27,600個……240L
4月……27,500個……280L
5月……31,200個……320L
6月……30,900個……319L
計……176,600個……1,755L
1月から6月は1個当り0.00994L(1,755L÷176,600個)使った。
(製品合格数)・(潤滑油使用量)・(前期ベース使用量)・(差異)
7月……33,100個……350L……329L……▲21L
8月……26,700個……295L……265L……▲30L
9月……28,900個……300L……287L……▲13L
10月…… 30,090個……299L……299L……0
11月…… 27,980個……250L……278L……+28L
12月…… 31,000個……249L……308L……+59L
計……177,770個……1,743L……1,767L……+24L
これによる具体的なアクション
7月〜9月は赤字の原因を追究し対策を打たせる。
11月〜12月はどのような改善によって効果が出たのか追求する。
そのために作業者に改善実施項目の創意工夫提案書を出させる。
そうしないと管理項目が細かすぎて、管理者はそれを把握できない。
創意工夫提案書の予想効果をこれにより裏づけすることができる。
作業者も管理者が創意工夫提案書を活用してくれるので提出しがいがある。
このような評価体制のない会社での創意工夫提案制度は、「予想効果で賞金払って終わり」ということになり、賞金ばかり出ていくだけで効果が実感できないもになり、そのうち制度が消滅してしまうことになる。
そもそも、改善なんて、労務費を低減しようと思って施策を打っても、確かに労務費は下がったが、逆に補助材料費が上がってしまった、というようなことばかり起こって、思考錯誤の連続といったものなのだ。
予想効果などというものは、あくまでも神のみぞ知る「予想」であり、今回説明したような原価評価体制を網の目のようにつくり、「実際の低減金額」を把握できなければまったく意味がないと言える。
管理対象費目
生産量の増減に比例して使用量が変動する費目
- 労務費
- 補助材料費
- エネルギー費
- 消耗性工具費
予算の適用
この7月~12月の実績が、次の半年間(1月〜6月)の予算になる。
したがって、一度やった改善は維持し続けなければならなくなる。
トヨタは上記の製造変動費予算実績管理を、管理可能な限りの細部品目にまで適用実施している。
このような数字を毎月示されたら、作業者全員が「もったいない稼働」をせざるを得なくなる。
作業者全員のもったいないが集まれば、大きな改善額になる。
このようなきめ細かな管理を日本の全企業が行なえば、それだけでCOPの目標の多くはクリアできるような気がする。
中国などはゴミの分別もまったくやっていないし、企業についても省エネ意識はないに等しかった。
トヨタや日本がやっていることを横展するだけで、中国の目標などあっと言う間にクリアできると確信している。
私は若い頃、トヨタ工場で、この資料を作る原価マンをしていた。
この資料を現場の工長(係長)の所へ持って行った際、次のようなイヤミを言われた。
「青木、お前はこんなものを毎月持って来るけど、お前はこの原価資料で俺たちをけったくってくる。
そして、『死んだかな?』と思って目をのぞいてきて、まだ生きていると分かると、今度は首を絞めてくる」
この原価資料も、トヨタのように平準化生産が前提となる。
なぜなら、いきあたりばったりの仕掛けをされてしまうと、数字が荒れて管理どころの騒ぎではなくなってしまうからだ。
結局、この製造変動費予算実績管理ができるということが、トヨタ式の体制がきちっと導入されたという証しになる。
トヨタが赤字になったことで、トヨタの評判は地に落ちてしまったが、トヨタとは本当にすごい会社なのだ。
原価資料これは実際に私が担当していた頃の原価資料。
当時はパソコンがなく、すべて手で計算していた。
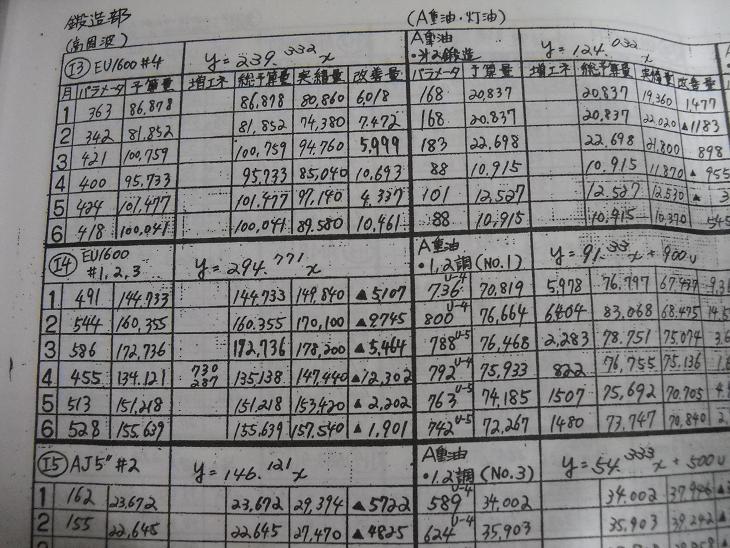
トヨタの改善の進め方
1.『小さな改善』
全員が各自行ない、創意工夫提案書により、上司へ報告する。
2.『中ぐらいな改善』……QCサークル活動
上記、変動費予算管理で赤字が続き、個人の力ではどうにもならない件を取り上げて、集団で対策を考える。
実施した改善に対する効果測定は、すべて変動費予算管理体制によって、原価マンが客観的に算出してくれるため、QCサークルメンバーは改善活動を行なうだけでよい。
3.『大きな改善』……部次長自主研活動
トヨタは毎月、製造トップへ生産能率の当月値の報告会を、各工場持ち回りで開催する。
その際、現場改善事例報告も2つの製造課の現場で行なわれる。
出席は、製造トップ(副社長クラス)、製造関係役員、各工場の部次長といったそうそうたるメンバーだ。
トヨタは巨大な会社なので、製造課など星の数ほどあるので、毎月開催されるとしても、各製造課にしてみれば、5、6年に一度回ってくるぐらいなので、そう驚くことはない。
しかし、いざ発表するとなると、トヨタのそうそうたる方々が対象なので、生はんかな内容では、工場内の事前リハーサルをクリアすることはできない。
そのために、発表が決まった製造課は6ヶ月前から、「部課長自主研」を発足させて改善に取り組む。
この「部課長自主研」とは、工場内の課長以上の管理職の中から数名が指名されてチームを結成し、発表の製造課といっしょに改善活動を行なうのだ。
これには予算もおり、設備投資も伴なう大きな改善を行なうことになる。
半年間、毎週火曜日の午後いっぱいが活動時間に指定されている。
私も何度も行なったが、宿題が出るので休日も出勤してやらねばならないことも多く、非常に大変だった。
この活動についても、効果測定は原価マンが客観的に行なってくれる。
P.S.長谷川慶太郎氏の著作からの抜粋
企業の省エネに関する技術水準を上げていくには、甘い基準でなく、企業が頑張れなければクリアできないような厳しい基準を設けた方がいい。
企業の技術は甘やかすよりも厳しい方が伸びていくのである。
また、そうすることが経済にも好影響を与える。
目下、環境汚染対策技術で世界の先頭に立っているのが日本なのだから、世界的環境保全の風潮が広がっていけばいくほど、日本にとってはプラスになる。
これからの日本には環境保全の風がどんどん吹いてくると言っていい。
日本および日本国民にとって、明るい未来が開けているということである。