【Dの問題】1つずつ作りなさい
※当コンテンツは『面白狩り』の提供でお届けしています。
6.5 1つずつ作りなさい
【問題15】製品の種類が多くて、一つの生産ラインで流すのが難しい。
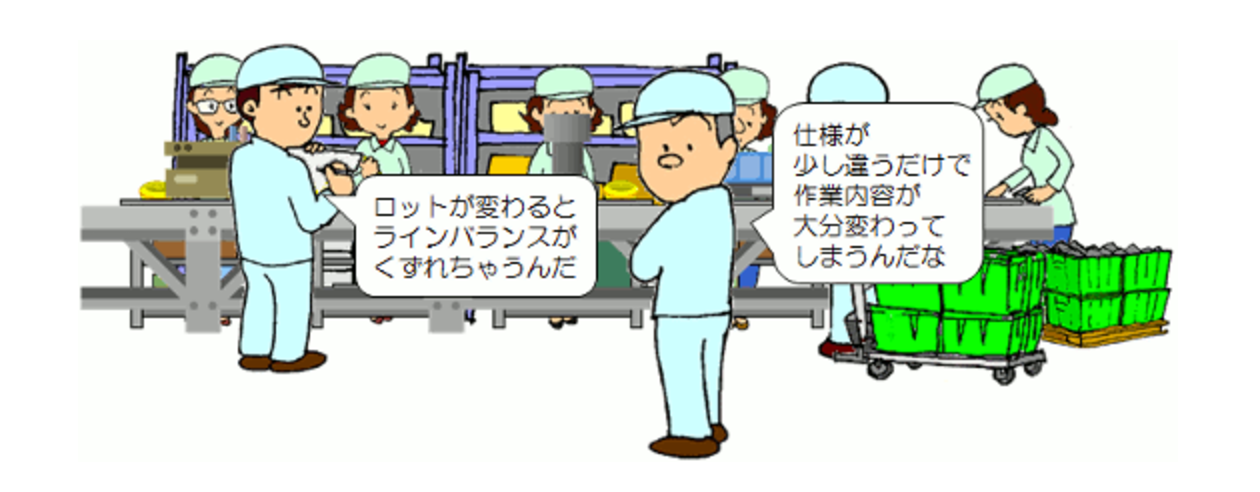
ラインバランシングは研究者によって様々な計算法が提案されています。
しかし、やったことのある人はわかると思いますが、実際に現場で流してみるとなかなか理屈通りにはいきません。
机上で考えるより実際に流しながら試行錯誤を繰り返すことがほとんどです。
また、苦労してラインバランスがとれても、昔の大量生産時代ならともかく、多品種少量が当たり前の現在では、設定したライン編成がすべてのロットに適合することはありません。
せっかく流れ化でリードタイムの短縮を図ってきたのに、その都度やり直さなくてはならないのは大変ですし、現実的ではありません
そこで、工程の類似した製品を集めて、グループごとにライン編成することを考えます。
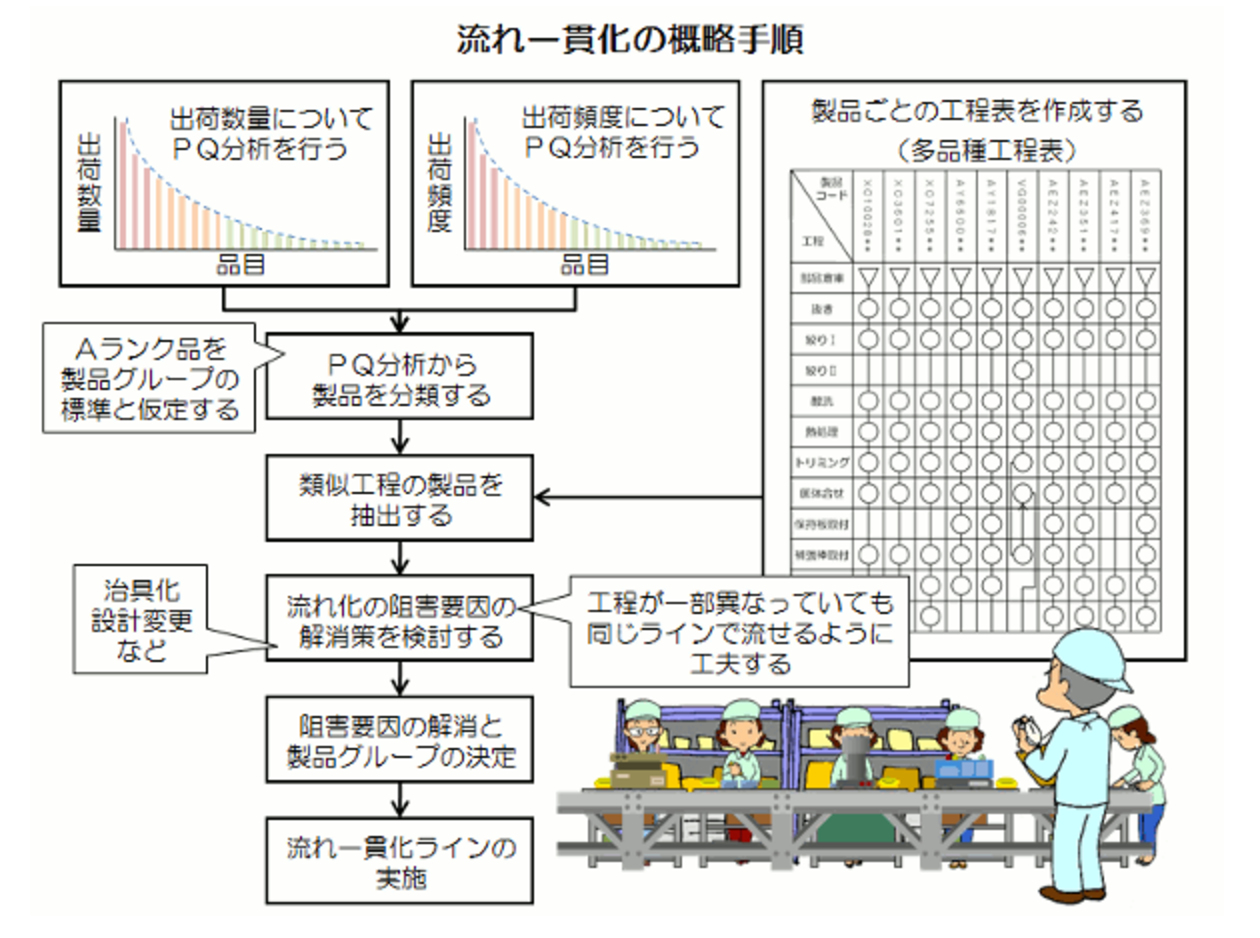
PQ分析を行い、出荷数量と出荷頻度が比較的大きい品種に着目します。
それらの品種と工程の似ているものを抽出して、いくつかの製品グループに層別します。
製品グループごとに生産ラインを設定し、生産計画で同じグループを連続して流すようにして、多様な品種にフレキシブルに対応できる流れ化を実現します。
この流れ一貫化ラインで製品の大半がカバーできればOKです。
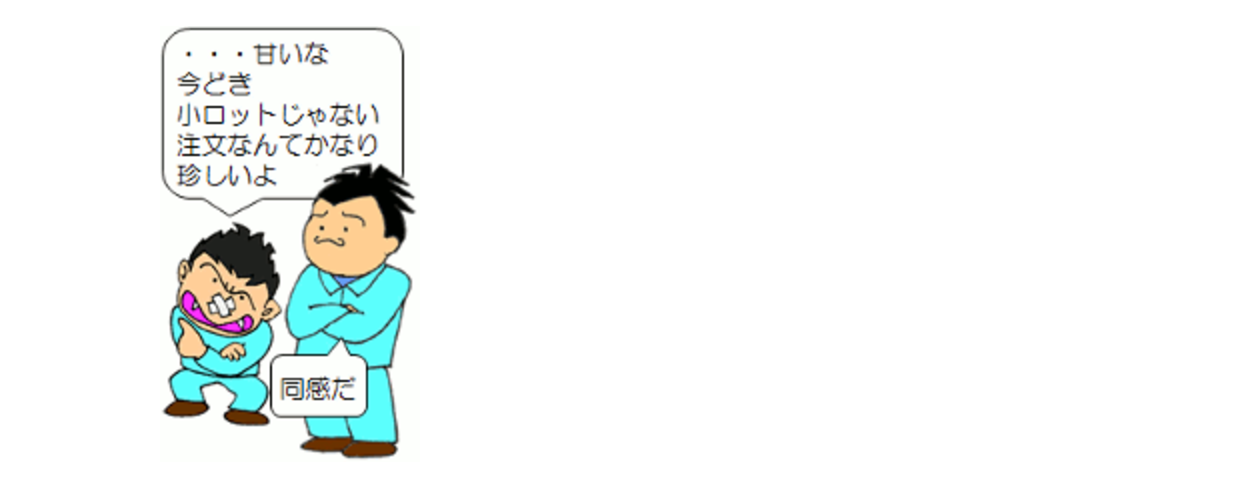
ところがところが……
特殊な小ロット品が多い場合は、旧来の方法でまとめ生産をして、結局、現場の至る所に仕掛品の山ができてしまいます。
でも、ここであきらめてはいけません。
リードタイム短縮の基本は、付加価値を生まない滞留と移動をできるだけなくすことです。
流れ化を図ることでその理想に近づけることができたわけですが、実は、もっと細かく動作レベルで見ると、その流れ化の中にも余計な滞留と移動が潜んでいるのに気付きます。
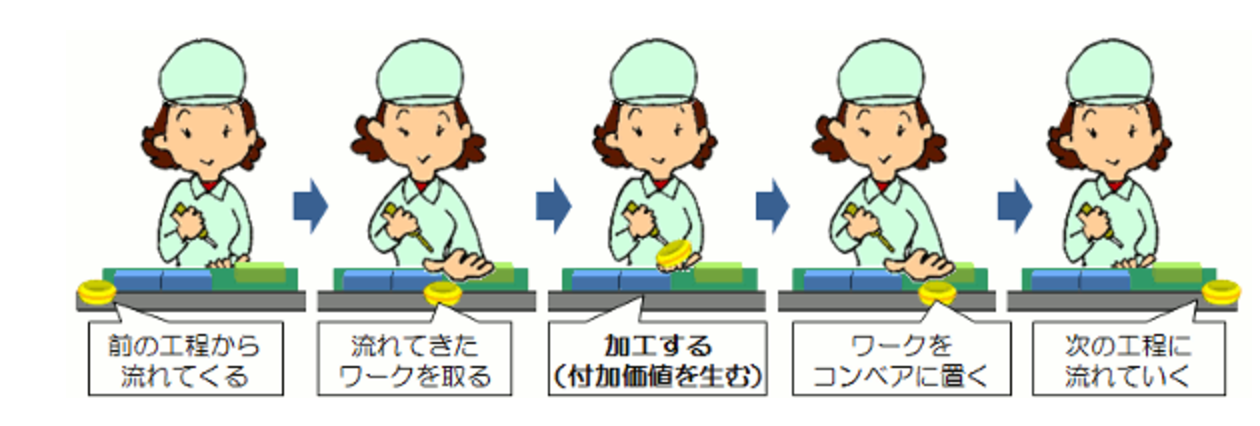
生産ラインが複数の工程に分割されていると、このようなトリオキ動作(取ったり置いたり)が必ず発生します(しかも、面倒なラインバランシングをしなければならない!)。
ここで、ちょっと発想の転換をします。
トリオキ動作をなくすということは、次の工程に渡さないということです。
つまり1つずつ最初から最後まで1人で作れば良いのではないか?
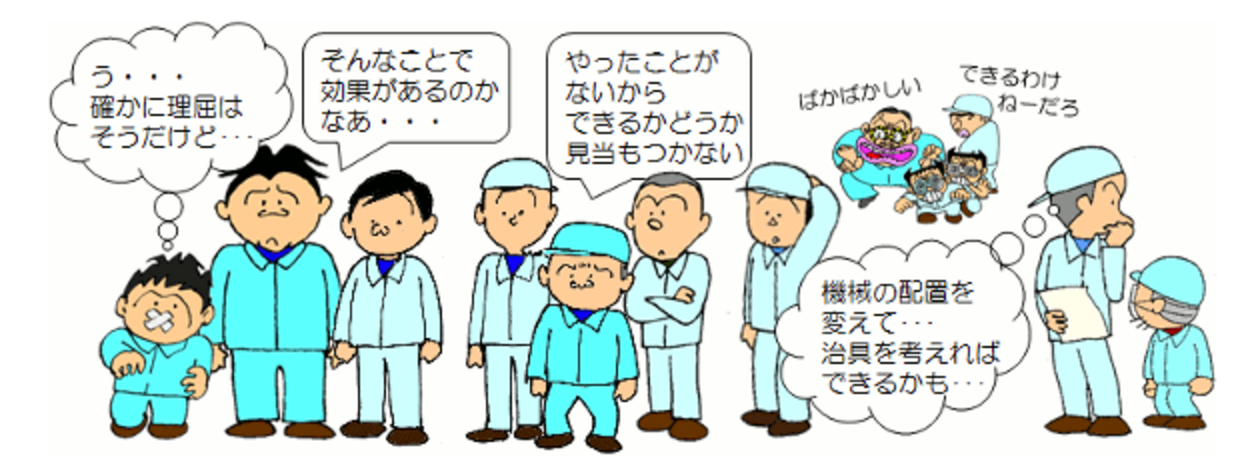
この方法をセル生産と呼びます。
なにか新しいアイディアのように感じますが、実は、機械加工ではとっくに行われている方法です。
例えば……
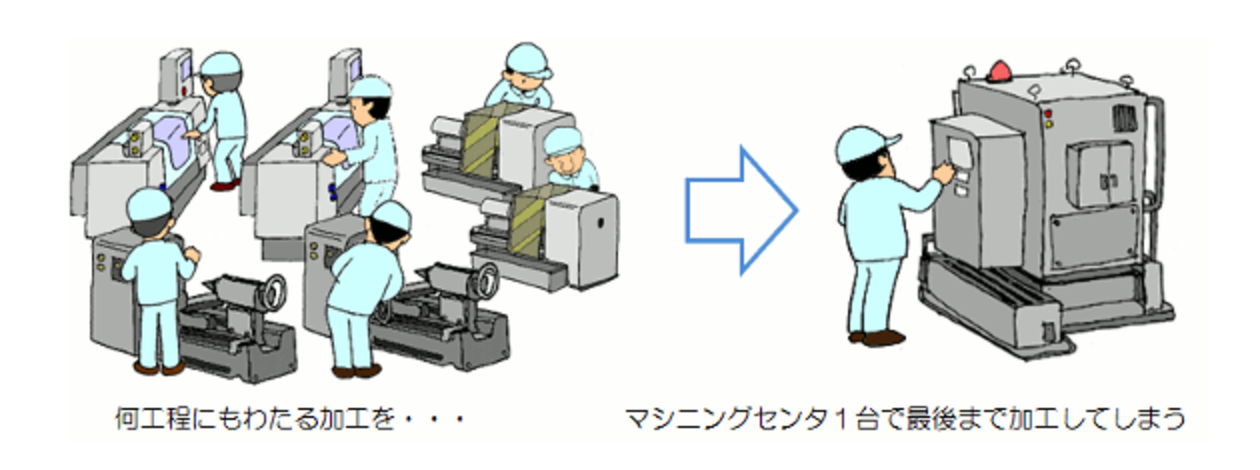
これを人作業でもやろうというところに戸惑うかもしれません。
しかし、技術は常に不可能と思われたことにチャレンジし、進歩してきました。
「だからできない」ではなくて「どうしたらできるか」を考えましょう。
ここが、あなたの会社の技術力の見せどころですよ。
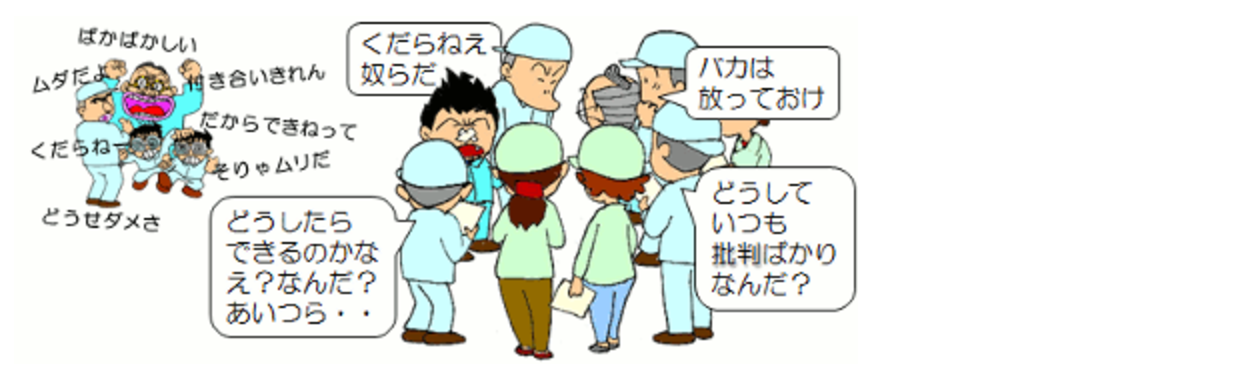
下はセル生産の全体イメージです。
ミルクランで部材を供給し、工程別生産計画で管理工程の進捗と仕掛品(中間部品)の在庫をコントロールします。
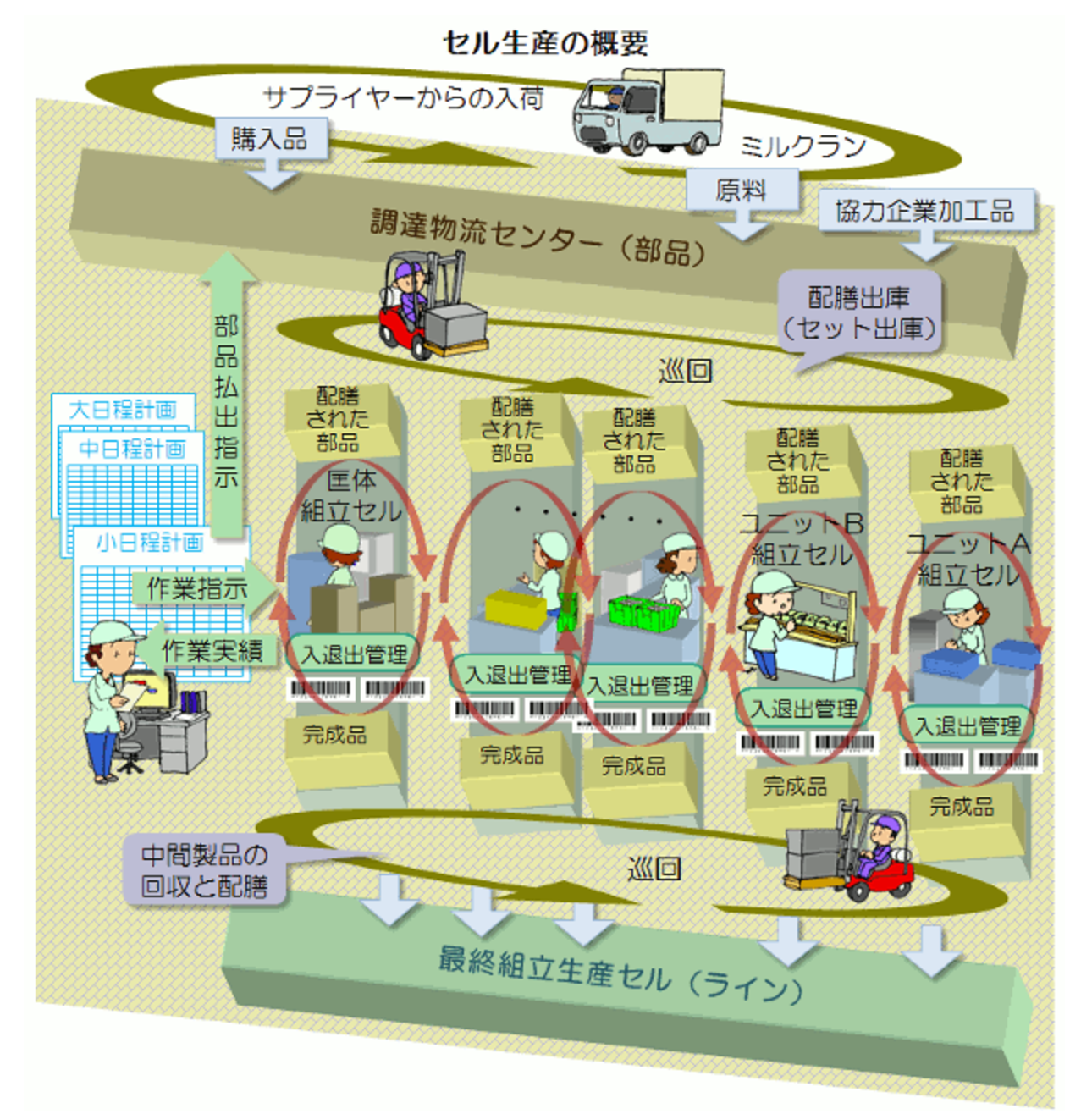
セル生産ではロットサイズの大小を心配する必要はありません。
また、面倒なラインバランシングを行う必要もありません。その代わり段取作業が増えて、その影響が無視できなくなります。
段取りをいかに効率よく行うか。次の課題はこれです。