生産性と生産リードタイム、どちらを気にしますか?
工場の全体最適化では生産リードタイムに注目したい、という話です。
生産指標のうちで、付加価値を拡大させることとつながり易い指標は何だろうか?
工場経営で持つべきイメージのひとつに「流れ」があります。
製品が滞りなく流れていくイメージです。
投入した資金を一日でも早く、投入した額よりも大きく現金として回収したいからです。
1.実現させたい将来の姿を描くのに問題を認識する
日々の進捗管理で発生した問題は、環境の変化に追随できていない現場の弱いところを指摘しています。
こうした問題は日々のカイゼンのきっかけです。
- 進捗管理で計画対比の遅れを認識する(=問題を認識する)
- 対策管理表で対策のPDCAを廻す
生産計画対比の遅れから問題点を認識し、対策のPDCAを継続的に廻します。
この仕組みが構築されている現場は存続し成長できます。
日々の進捗管理をしながらイノベーションの土台となる情報的経営資源を、しっかりと蓄積しているからです。
ですから、問題点が認識されたら、暫定的に解決すると共に、それを課題に変換して、イノベーションを生む機会とすることは、経営者の大切な仕事です。
目指すべき状態は経営者にしか描けないからです。
目指すべき状態のためには何をすべきか?
問題点を認識したら、実現したい将来の姿への課題を考えるきっかけとします。
2.生産性と生産リードタイムはしっかり切り分けて考える
日々の進捗管理で発見された遅れから認識される問題点の多くは、各工程内でのトラブルです。
- 段取りに時間がかかってしまった。
- 必要な材料が届いていなかった。
- 加工を失敗して、造りなおした。
- 作業者が急に休んで、人手が足りなかった。
等々。
こうしたトラブルが発生すると、生産性が低下し、生産リードタイムが伸びて、納期に遅れが出ます。
ですから、上記のような問題の暫定策として、
- 段取り時間を管理しよう
- 資材の在庫を管理しよう
- 加工作業時のチェックポイントを新たに設けよう
- 突発の休みでも対応できる人員配置を新たに考えよう
という対策案を現場では考えるはずです。
まずは、暫定的にでも、問題を解決しておかないと、日々の生産活動に再び支障をきたす懸念が残るので、当然の対応策です。
ただし、目指すべき状態を設定するためには、もう一歩踏み込んで現場の弱みを把握する必要があります。
そのために、生産性とリードタイムに着目します。
生産性とリードタイムをしっかり切り分けて理解します。
そして、実現させたい将来のためには、どちらを重要視するか、ハッキリさせます。
ここである生産ラインを想定します。
工程1と工程2の2つの工程で構成されている生産ラインです。
- この生産ラインは製品を60個単位でロット生産しています。
- 工程1では作業者が5人で2日掛かっています。
- 工程2では作業者が10人で1日掛かっています。
- 工場全体の生産能力の制約条件があるため、工程1と工程2の間で仕掛品が1日滞留します。
この状況を標準とします。
ここで、工程2で先のようなトラブルが発生し、生産性が低下し、生産リードタイムが伸びたとします。
これらの状況を下表にまとめます。
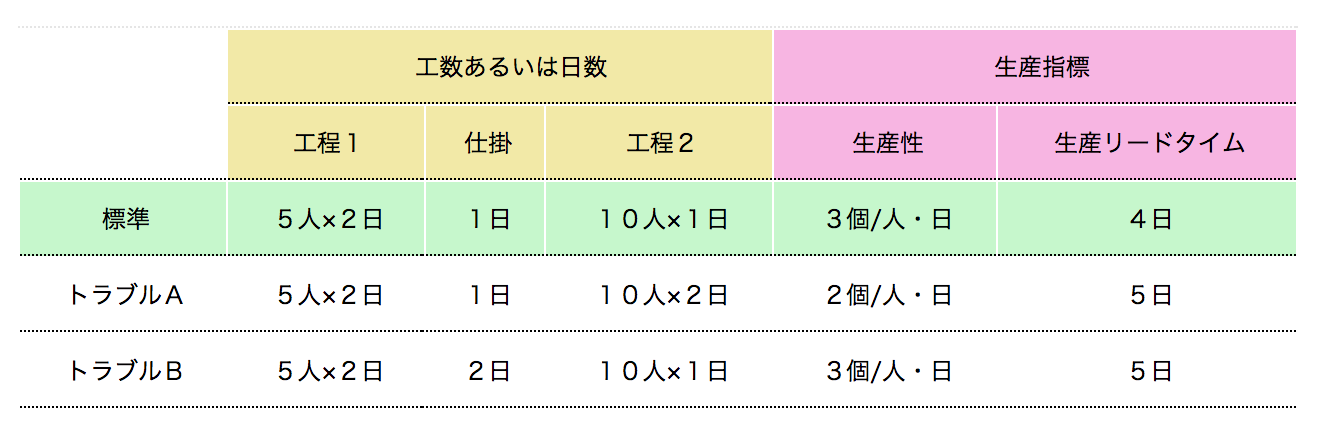
標準に対しトラブルAとBでは、トラブルによる影響の解釈に違いがあります。
トラブルAの解釈ではトラブルによって生産性が低下しています。
トラブルBの解釈ではトラブルによって仕掛の滞留時間が伸びています。
トラブルによる悪化要因を考える上で、生産性と生産リードタイムは、しっかり切り分けて考えます。
自社工場での問題の本質はどこにあるのか?
そこをしっかりと見極めます。
3.工場の全体最適化では生産リードタイムに注目したい
トラブル発生で影響を受ける生産指標の評価が異なってくるトラブルAとトラブルBですが、トラブル自体の発生原因は同じです。
解釈によってトラブルの対策が変わるわけではありません。
ここで、考えたいのは、目指すべき状態をどのように設定するかです。
つまり、生産性と生産リードタイムのどちらを重視すべきか、ということです。
当然、両者とも工場経営では重要な指標です。
ただし、我々は今、付加価値を拡大させ続けようという経営課題を掲げています。
付加価値拡大の視点で考えると、より重視すべき指標があります。
それは、生産リードタイムです。
つまり、発生したトラブルをトラブルBのように解釈したいです。
仕掛品がもともと標準でも1日滞留していていたのに、トラブルのため2日も滞留することになってしまった、と解釈します。
生産リードタイムを重視し、目指すべき状態を設定するのがひとつの方向性です。
理由は複数あります。
1)運転資金の圧縮
2)工場スペース確保
3)現場の連携による一体感の醸成
その他、5Sが進み維持され易くなる、物流が向上するので管理の手間が減る、スッキリした現場は見学したお客様に安心感を与える等々。
モノづくり工場の機能、全般をステップアップさせるからです。
また、業界が驚くほどの短納期にまで極めれば、その納期自体が付加価値を生み出す可能性を高まります。
加えて、直接的、間接的に工場全体の生産性を向上させることも期待できます。
少ない人員で上手く流すにはという考えになれば、結果として各工程の生産性も上がります。
工場経営で持つべきイメージのひとつに「流れ」があります。製品が滞りなく流れていくイメージ。
投入した資金を一日でも早く現金として手元へ回収したいからです。
それも、投入した額より大きくして、より早く回収したい。
工場の全体最適化を考えるにあたっては、生産リードタイムに注目します。
まとめ。
工場経営で持つべきイメージのひとつに「流れ」がある。
製品が滞りなく流れていくイメージ。
投入した資金を一日でも早く、投入した額よりも大きく現金として回収したいからである。
工場の全体最適化では生産リードタイムに注目したい。