3Dプリンター最新動向と 導入のポイント・ 実用事例|最新ユーザー事例と技術動向に学ぶ withコロナ時代のものづくり
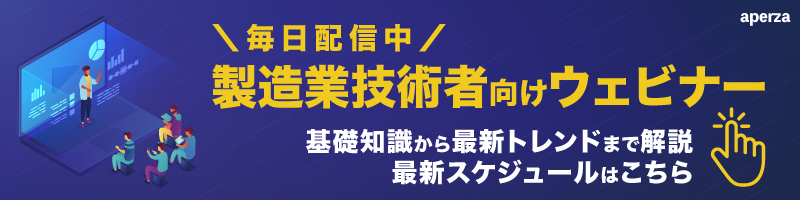
はじめに
コロナウイルスの感染拡大は、製造現場にも大きな影響を与えています。人の移動や対面・接触が大きく制限されたことをきっかけに、従来の労働環境や業務プロセス、生産工程 / 体制を見直し、デジタル化する動きがさまざまな領域・分野で生まれています。
働き方改革への対応や人手不足、熟練労働者の技術伝承といった従来の課題に加え、新型コロナウイルスのような環境変化に対して、製造業の企業はどのように対応していくべきなのか。with / after コロナでの「新しい生活様式」が提唱されるように、製造業における「新しい業務様式」を多くの企業が日々模索しています。
企業が抱えるさまざまな課題に対して、各社では最先端の“デジタルものづくり”どのように「新しい業務用式」として活用しているのか。2020年8月6日に開催したアペルザのオンラインセミナー企画「SFTS TV*」では、“withコロナ時代のものづくり”をテーマに、各種IoTソリューションを手がけるJSR株式会社 澤田さまをお招きし、最新のユーザー事例について伺いました。
本レポートは、その内容をまとめたものになります。
※PDFでもお読みいただけます。こちらからダウンロードください。
合成ゴムなどマテリアルにルーツ 近年は3Dプリンティング事業に注力する JSR株式会社
松本:本日はナビゲーターとしてアペルザより下宮、松本が、そしてキーエンスの生産現場でも経験を持つ、同じくアペルザの中島がコメンテーターとして参加させていただきます。
本日のゲストは、エラストマー、合成樹脂といった材料に加え、3Dプリンティング事業も手がけられているJSR株式会社 澤田様にお越しいただいております。どうぞよろしくお願いいたします。
澤田:よろしくお願いいたします。
松本:3Dプリンタ、そしてデジタルマニュファクチュアリングというテーマで「製造業の新しい業務様式」に迫っていければと思います。早速ですが、中島さん、このテーマいかがでしょうか。
中島:3Dプリンタというと、試作用途が中心で、最終製品に適用するのはまだまだ難しそうなイメージがあります。特に試作でもサイズ感を確認したりだとか、嵌合を調べたりだとか、そういった用途しかないと思っていたのですが、意外と進化してきていることを知ったので、今日はそのあたりの実績を伺っていきたいです。
下宮:では澤田様、会社の紹介をいただいてもよろしいでしょうか。
澤田:JSRは1957年に設立、60数年の歴史を持つ企業です。もともとは日本合成ゴムという社名で、合成ゴムを取り扱っていました。現在は合成樹脂や電子材料、液晶テレビなんかに使われる部材なども取り扱っています。また冒頭にもあったとおり、最近注力しているのが本日のテーマである3Dプリンタ事業です。
従来の3Dプリンタと『Carbon』の違いとは?
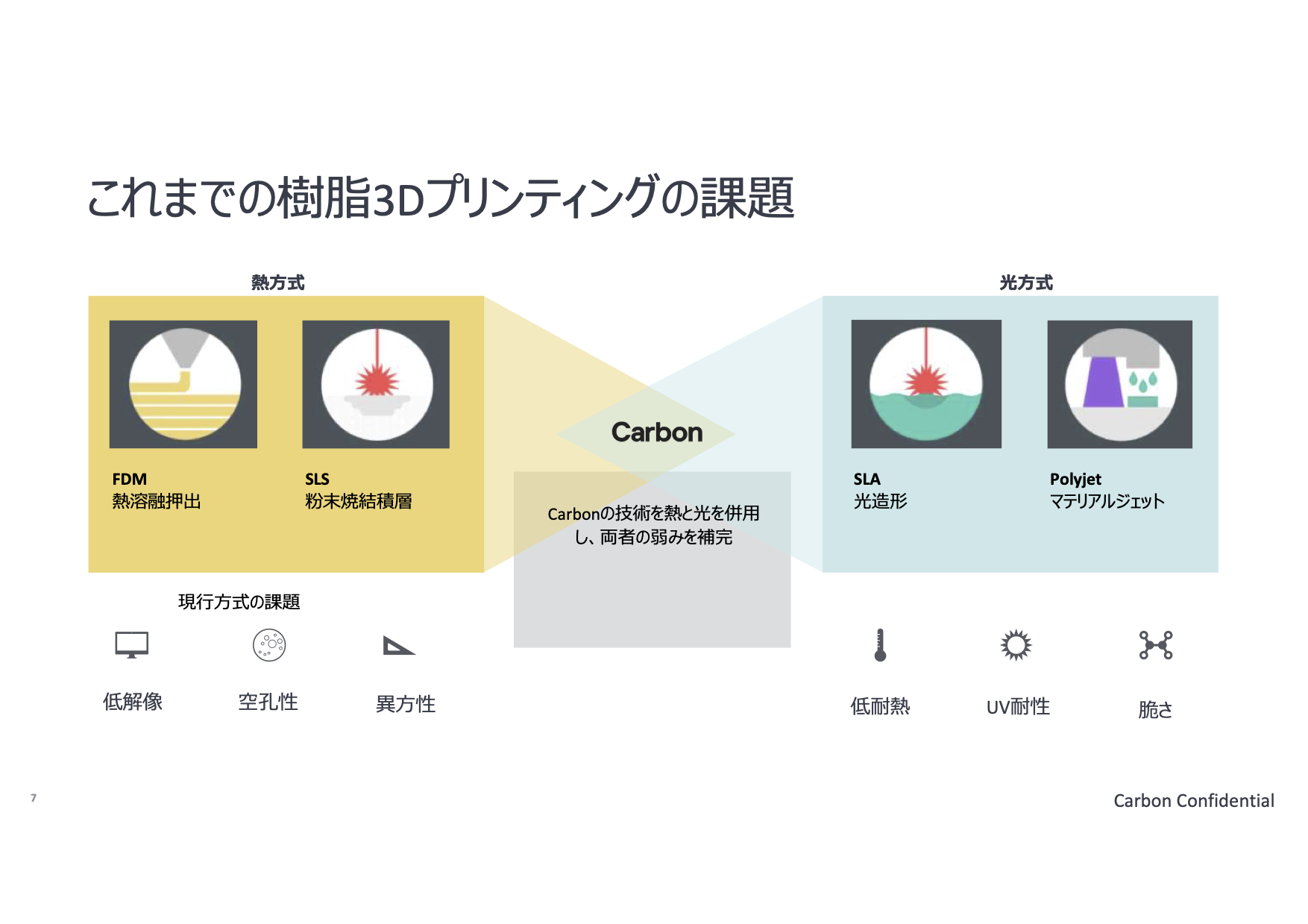
澤田:上記のとおり、樹脂3Dプリンタにはさまざまな方式があります。ポピュラーな「SLA(光造形)」や、粉末の樹脂を溶かして積層していく「SLS」、またデスクトップ型として使える「FDM」など。いずれも「レイヤーを重ねていく」という仕組みが基本にあり、スピードだとか、表面に筋ができるといった共通の課題を持ちます。
中でも特徴的なのが、「強度の異方性」です。一層一層完全に固めて層をつくっていくため、造形方向、すなわち厚み方向の強度が相対的に弱くなります。そうすると、つくった部品の部位によって強度が違うということが起きるので、最終製品には使えません。用途は「形状確認」に限定されてしまいます。
中島:確かに3Dプリンタってそういうイメージですよね。
澤田:はい。一方で、『Carbon』は写真のとおり断面図が非常になめらか。そして強度もXYZの各方向で異方性のない部品がつくれます。
従来の3Dプリンタは、試作や開発、あるいは個人で使われるケースが多かったのですが、このように材料や部品の制約がなくなってくると用途は広がります。
例えば一つつくっても、一万個つくってもそれほどコストが変わるわけではありません。一箇所で集中生産する必要もないですし、マーケットの近くでつくるなんてこともできる。型をおこす必要もなく、開発の過程でもデジタル技術が使えるようになるので、より早くつくれます。つまり、ものづくりのプロセス、さらにサプライチェーン全体についても大きく変わってくる。そういうポテンシャルを持つ技術です。
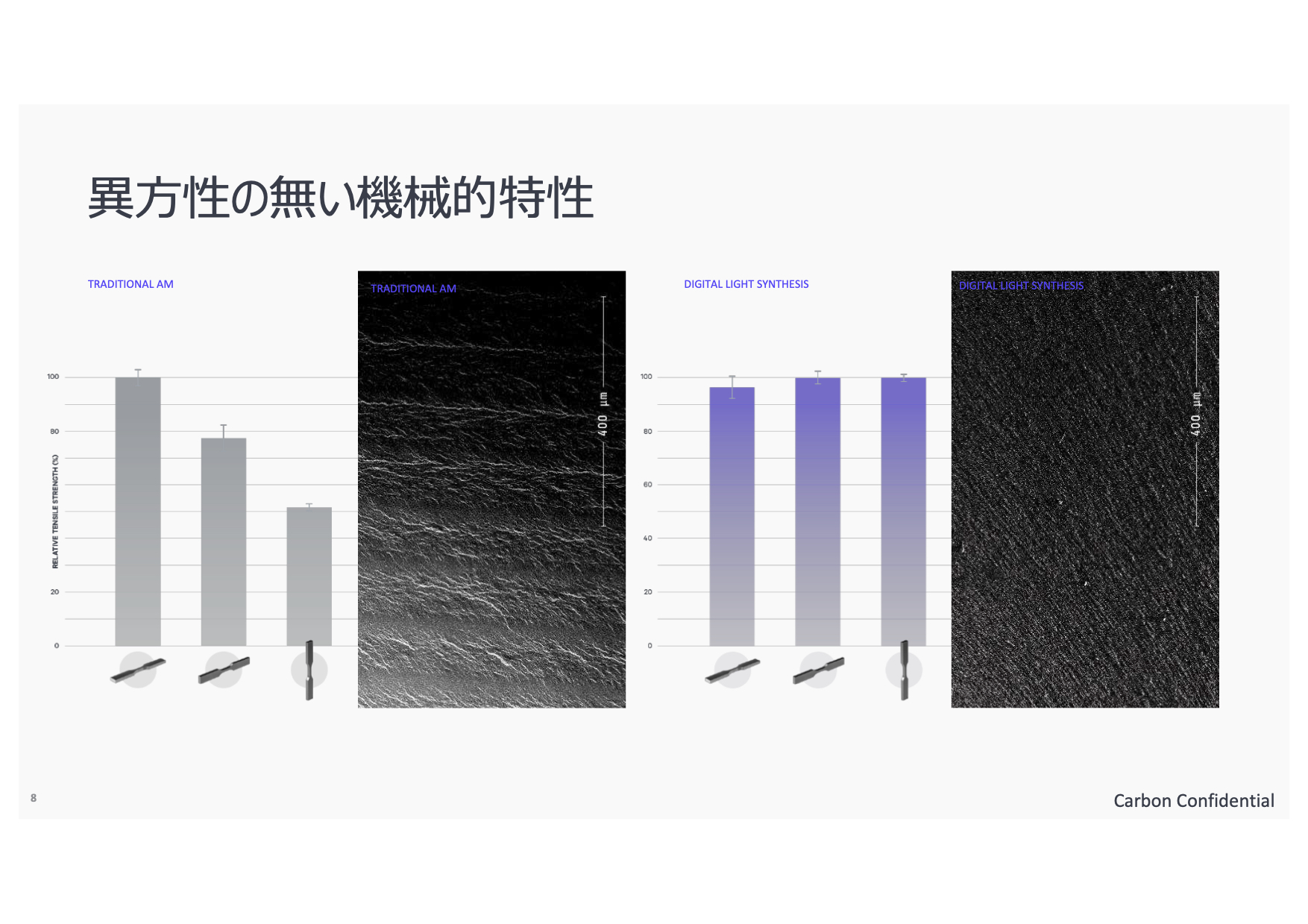
中島:確かに先ほど見せていただいた「強度が変わらない」っていうのは、分かりやすい。用途が一気に広がりそうです。
澤田:『Carbon』に限らず、3Dプリンタでできることが広がっていけば、少しずつ認識が変わってくるんじゃないかと思っています。3Dプリンタというと「開発ツール」のイメージなのですが、あえてここは「デジタルマニュファクチャリング」という新しい定義、カテゴリで呼んでもいいのかなと。
下宮:おもしろいですね。ここから先は対談も挟みつつ、製造現場での事例なんかについても触れていきたいと思います。
先ほどもあったとおり、現在は「試作でちょっと使ってみようかな」というケースが多いのかなと。「数年前に買ったけど社長がおもちゃとして使っているだけ」みたいな話もよく聞きます。技術的な革新も起こっているなかで、もう少し幅広い用途で使えるようになってきていると思うのですが、具体的にどういうところなのか、事例をお聞かせいただけますでしょうか。
澤田:では『Carbon』に限定されるんですが、実際に採用されている領域についてご案内していきたいと思います。コンシューマー向け、自動車、インダストリアルといったカテゴリで分けることもできるのですが、あえて「ものづくりのプロセスを変えていく」という観点で、デザインや開発、そして最終製品の製造はこんなところが変わっていくんだ、というのをお見せしたいと思います。
事例1:技術革新
澤田:ご存知の方も多いかと思いますが、アディダスがミッドソールの量産に3Dプリンタを活用しています。写真のとおりミッドソールが格子構造なんですね。これを我々は「ラティス」と呼んでいます。耐久性も十分にありながら、従来の技術では実現できなかったようなパフォーマンスを発揮できる点がポイントです。
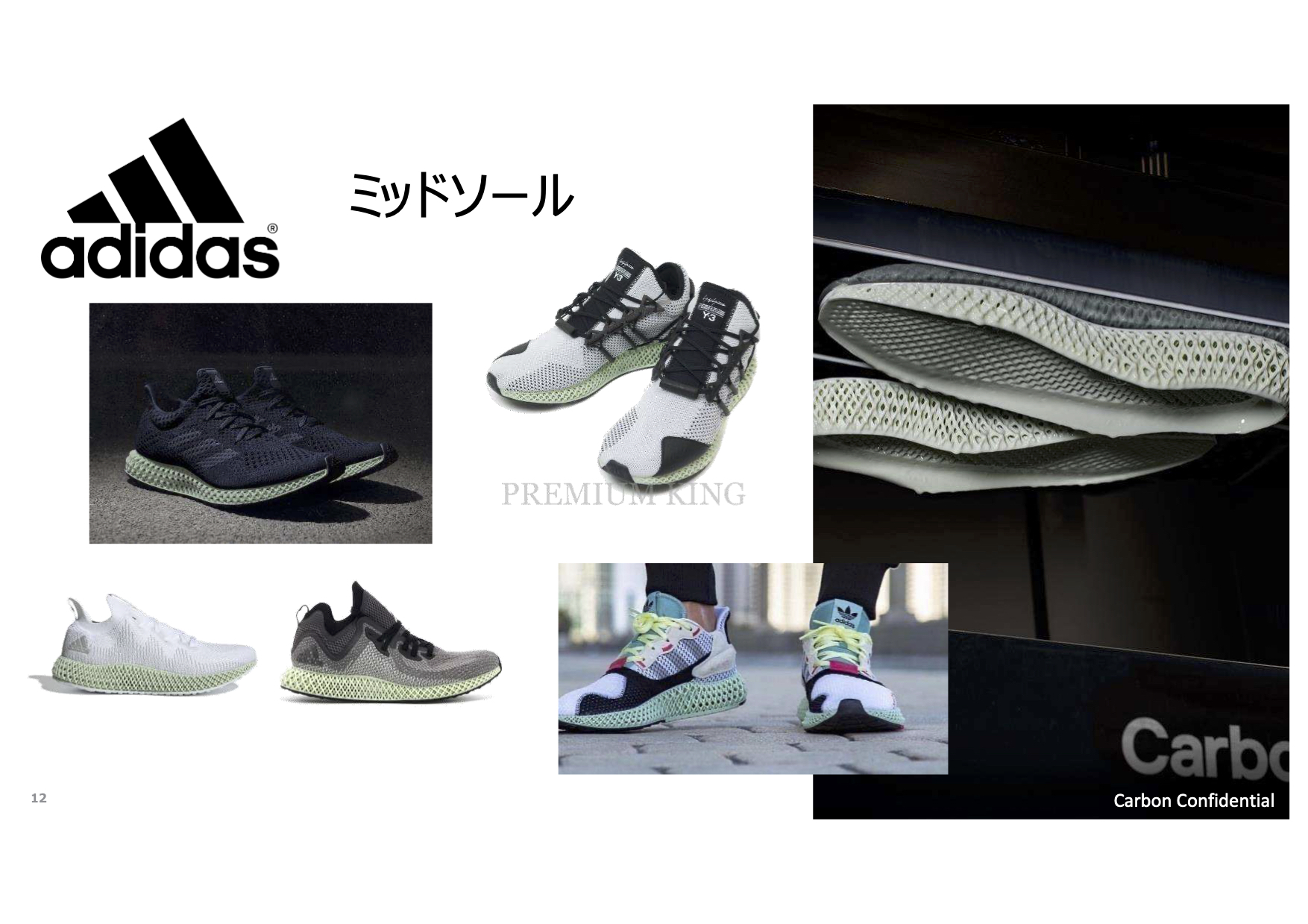
澤田:続いてこちらはアメフトのヘルメットの内装になります。Riddellはアメリカのトップブランドなのですが、もともと選手の頭をスキャンして、内装材を提案するというサービスを実施していました。
選手の脳しんとうなんかが社会問題になったりしましたが、内装材に先ほどの「ラティス」を採用することで衝撃吸収性の向上を実現しています。あとは通気性があるので快適だったり、軽量化にも貢献していますね。
中島:デザイン以外にもメリットがあるんですね。
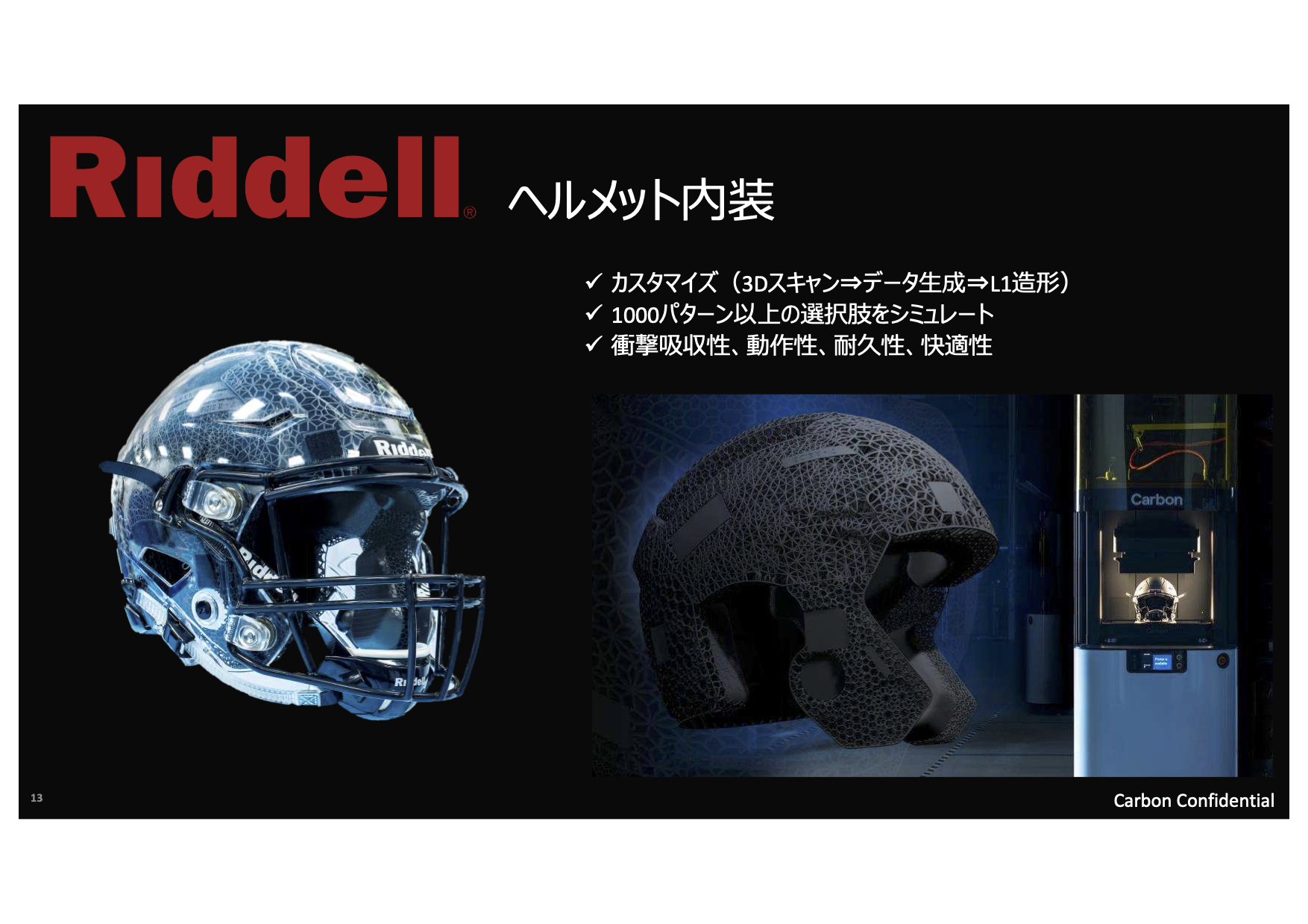
澤田:ちょっと変わったところでは、フランスのスタートアップが作っているイヤホンカバーがあります。ユーザーが自分の耳の形をスマホでスキャンして送信すると、自分の耳の形にあったイヤホンカバーが送られてくるという。
中島:おもしろい。「新しい体験」とも言えますね。
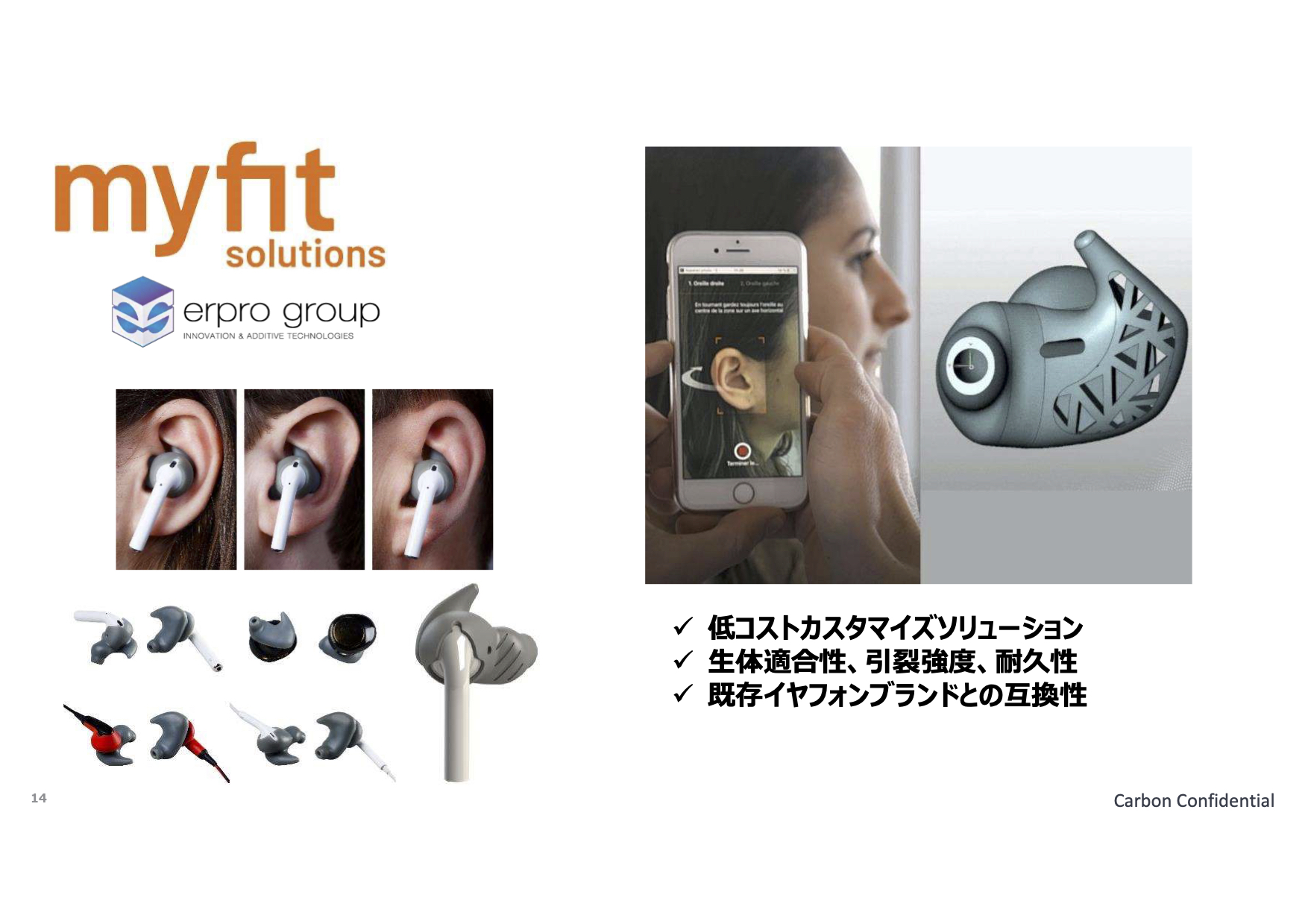
事例2:開発プロセス革新
澤田: 続いてNASAの事例を紹介します。自律飛行して外観検査をするドローンの事例です。打上げまで約1年と開発期間が短く、また宇宙空間は太陽が出れば高温、出なければ低温と温度の課題もありました。そこで選ばれたのが『Carbon』です。
中島:NASAですからかなり厳しい要求基準があって、それを満たすことができた部品ということですよね。
澤田:そうですね。オレンジ色の樹脂部品、実は初めてのアディティブでつくった部品でした。
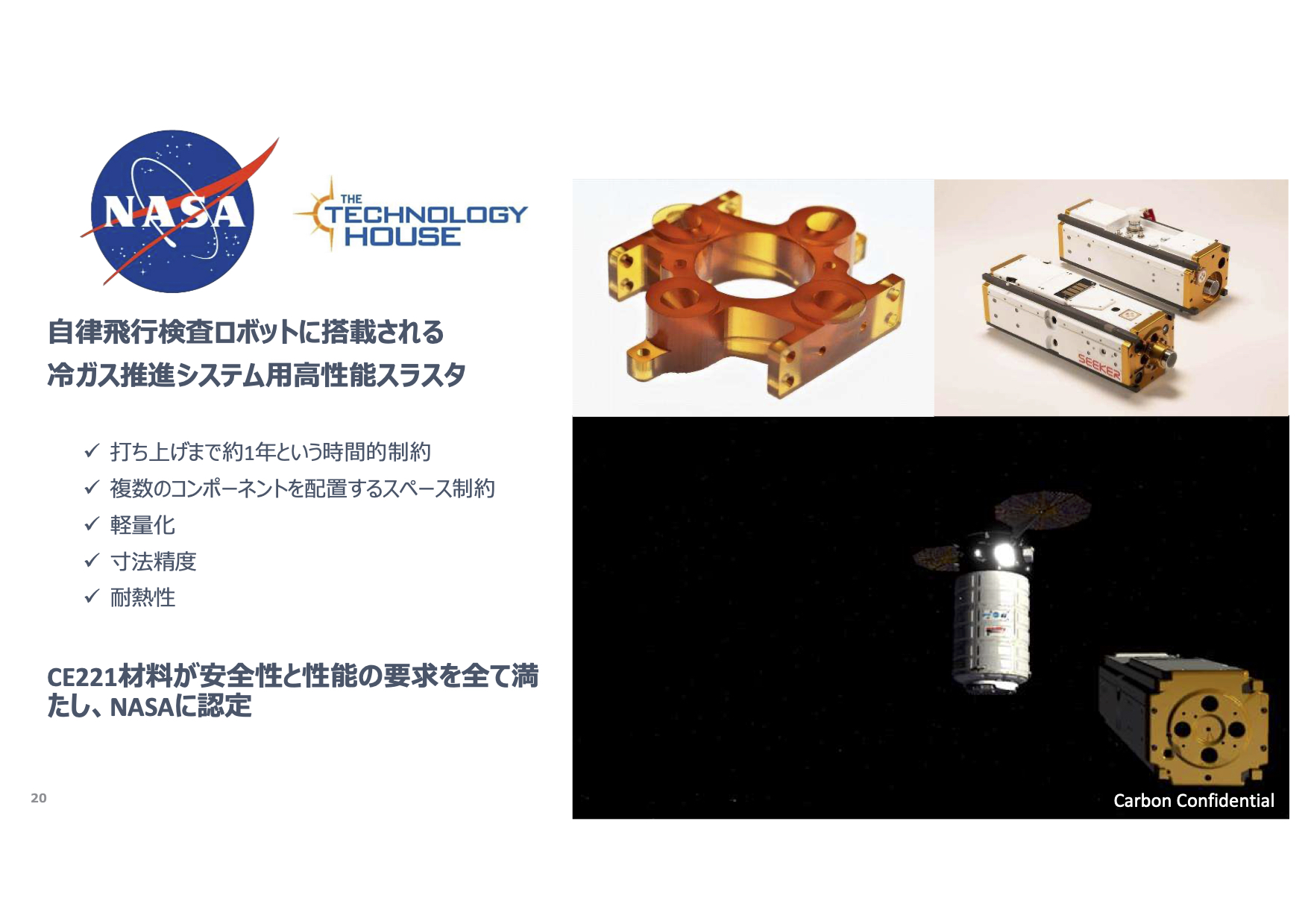
澤田:続いてSPECIALLIZEDという自転車メーカーの事例です。サドルに先ほどの「ラティス」を採用しています。通常は開発工程が24ヶ月くらいなのですが、こちらは10ヶ月で仕上げています。
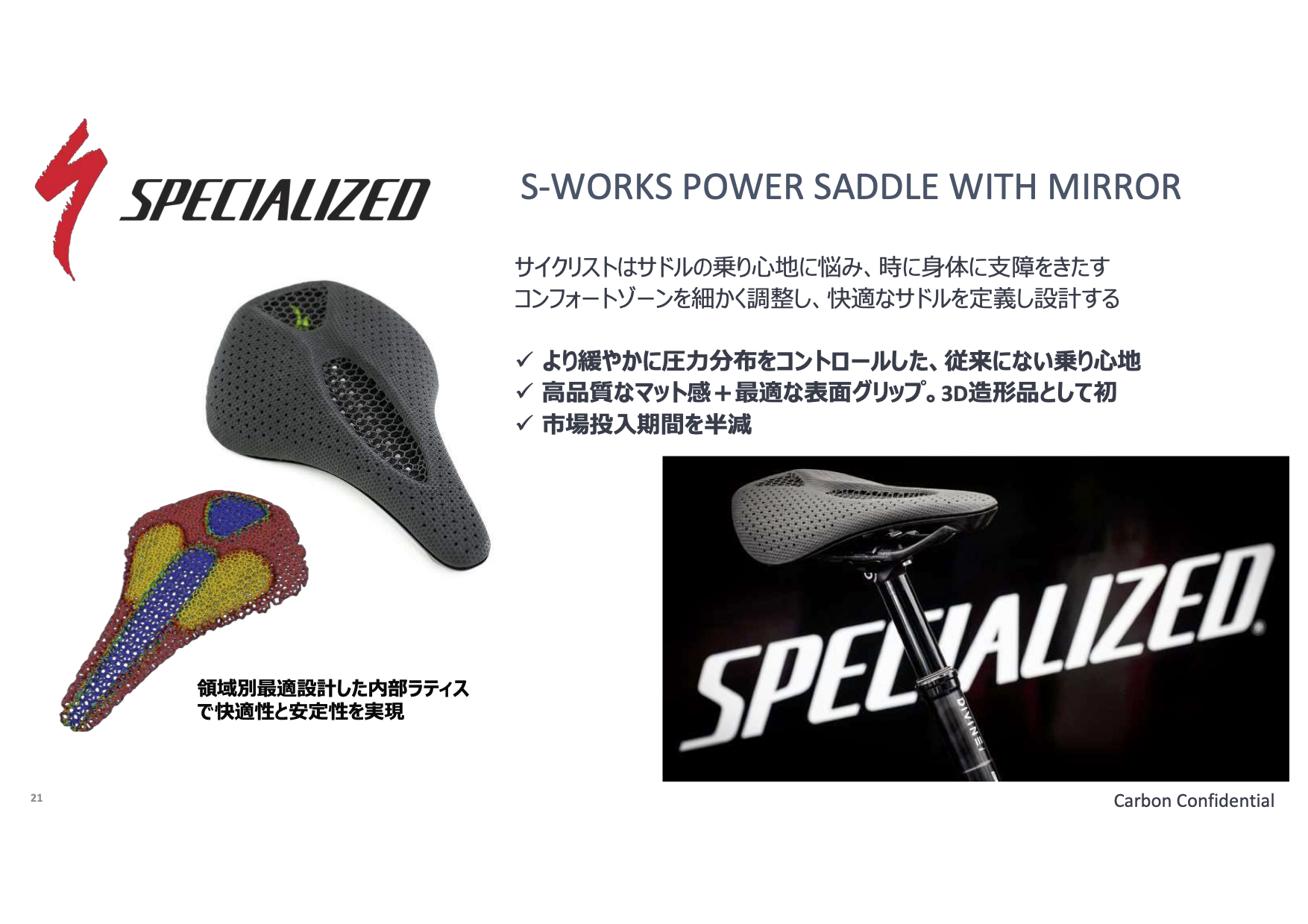
これら2つの事例をご覧いただいて分かったかと思うのですが、このような「開発工程の短縮」というのが結構いろんなところで起こっています。従来は試作・製造で使っている技術がそれぞれ違うために、設計変更をせざるを得ないケースが結構あったのですが、それがなくなるんですね。
事例3:製造プロセス革新
澤田:最後に「製造」の事例です。やはり自動車が一番大きいと思っています。アメリカのFordでも早期より『Carbon』を取り入れています。
Fordでの実績は、「電動パーキングブレーキブラケット」「デリートプラグ」「HVACレバーアームサービスパーツ」の3つがあります。それぞれ少量の部品で、「HVACレバーアームサービスパーツ」は保守部品ですね。一般的にモデルチェンジ後、大体15年は在庫を維持しなければいけないですし、金型もなかなか捨てられないんです。
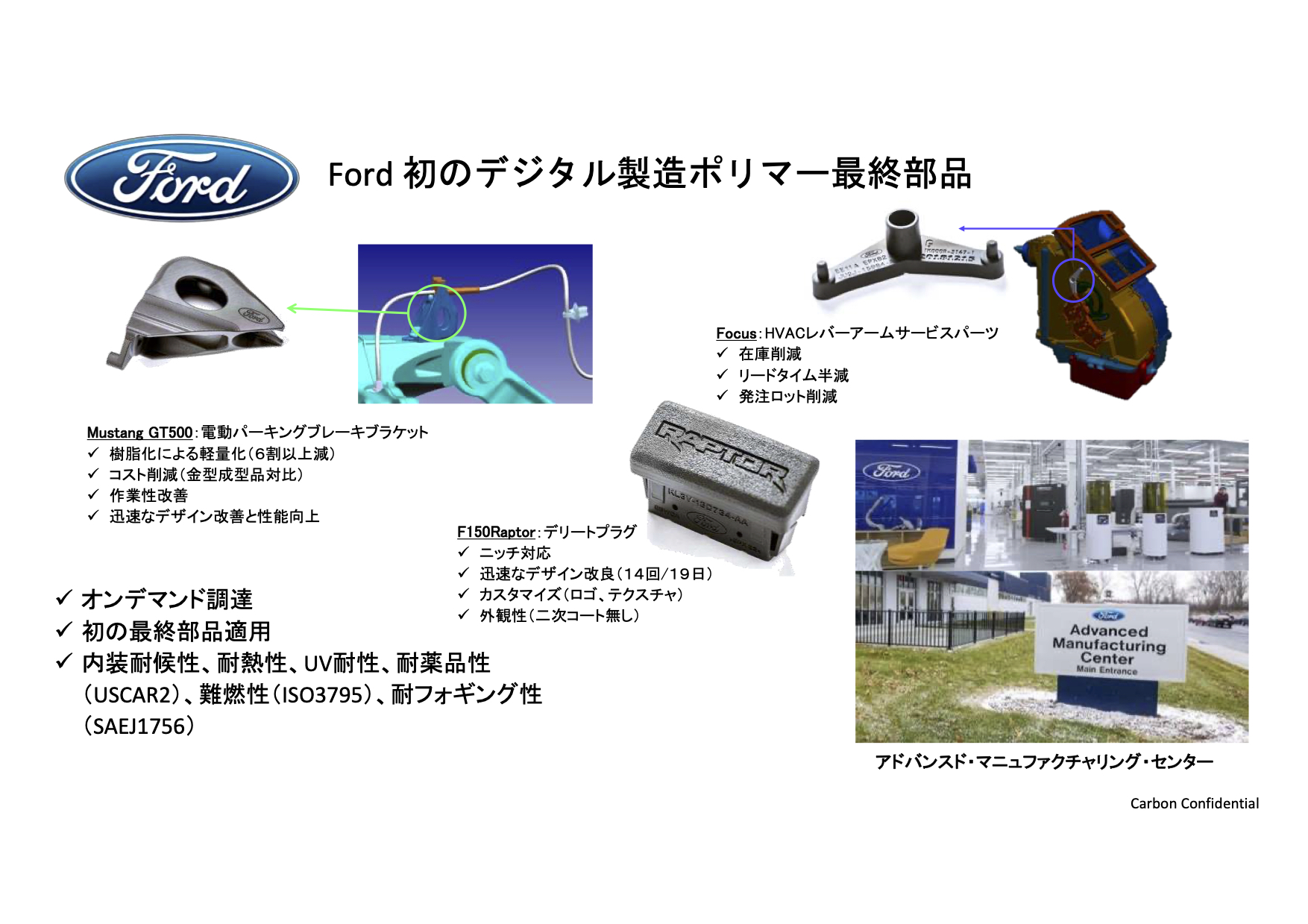
下宮:ちなみに事前に視聴者の方からいくつか質問をいただいています。そのうちの一つが「国内外の自動車や航空機などモビリティへの3Dプリンタ適応事例を教えてください」というものでした。
澤田:今回ご案内できるのは『Carbon』の事例になってしまいますが、他も含めると例えば自動車とか航空関係は欧米で先行して採用が拡大しています。特に航空関係の場合は軽量化を図れば燃料コストで大きなメリットが得られます。しかも、元々生産量も少ない。なので採用が進んでいるんですね。
下宮:自動車とか航空機関連って求められる精度がすごく高くて3Dプリンタの導入は難しいんじゃないのか? なんて思ったりするのですが、そこでも実用化が進んでいるのはどのような背景があるのでしょうか。
澤田:コストダウンの他にもいろいろあると思いますが、一つはカスタムへのニーズですね。あとは先ほども出た保守部品。経産省も進めていますけども、金型も不要なものは減らし、負担を減らしていこうという動きもあります。そういった中で3Dプリンタは有望なテクノロジーだと思っています。
あとこちらは日本の事例になるのですが、NITTOKUさんというRFIDのパーツを製造されている企業で、比較的日本では早い時期から活用されています。
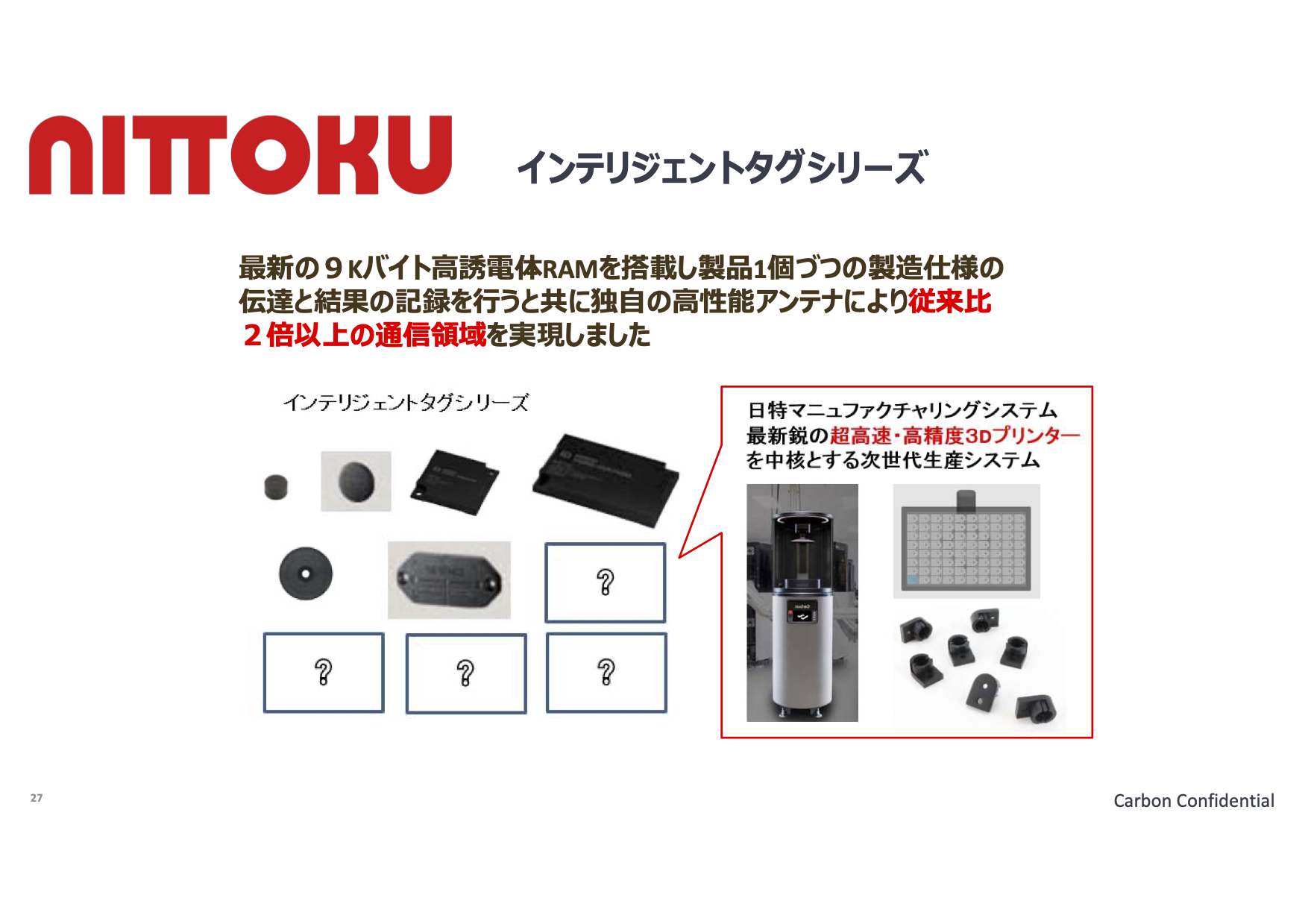
澤田:次は製品ではなく治工具の事例です。
中島:治工具は便利ですね!
澤田:EIZOさんは医療用モニターをメインで製造している企業で、もともと製造現場で治工具を作っていました。そのうち樹脂関係のものについては3Dプリンタでつくられています。また耐熱性が必要なものは金属を採用し、外注していたのですが、これを『Carbon』でつくることによってスピードアップとコストダウンを図りました。
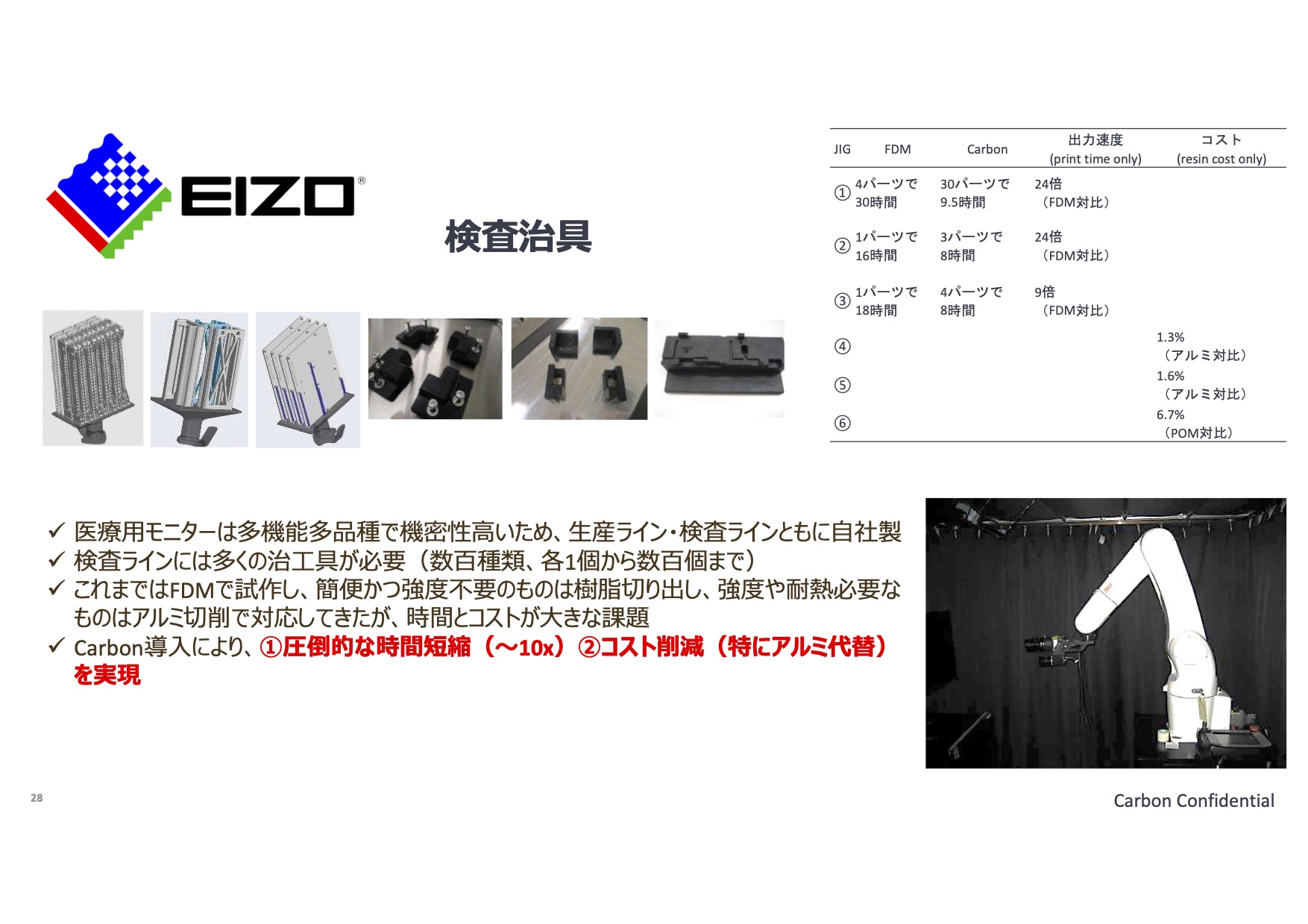
中島:製造現場に行くと、作業台、受治具、検査治具などを手間をかけながら準備されているのをよく見かけます。そこに3Dプリンタが入るのはいいですね。
澤田:3Dプリンタの技術が治工具でも使えるようになってくると本当におもしろいと思います。
ここまで一通り『Carbon』の技術を紹介してきましたが、カスタマイズ、オンデマンドなど、さまざまなシーンで使えるようになってきていますよね。おそらくものづくりのサプライチェーン、それぞれのプロセスがさらに大きく変わっていくんじゃないかなと思っています。
中島:先ほど保守部品、自動車だったら15年という話もありました。装置、金型、場所を残しておいて、受注が入ったら少量を一生懸命つくって、納品して、片付けて、というのが今まで普通だったんですもんね。
冒頭の話でもありましたが、金型がなくてもつくれるということは、金型が残っているからここでつくる、ではなくどこででもできるようになるということですよね。
本体価格や維持費、材料など費用感は?――視聴者からの質問
下宮:最後に、視聴者の方からもリアルタイムで質問をいただいておりますので回答したいと思います。「3Dプリンタを導入するとなった場合の本体価格や維持費、汎用材料の価格について参考程度でよいので教えていただけますでしょうか」ということで、ストレートな質問です。いかがでしょうか!
澤田:弊社は3Dプリンタという装置を販売しているわけではないんですね。サブスクリプションでの提供になります。材料は有償です。
先ほどのアディダスの事例のように、格子構造を使った製品を開発する工程だとか、実際に導入に際してデザインをさらに最適化して、最終的には量産の条件を整えていくとか、そういったサービスもすべてパッケージされているサブスクリプションとなります。
お値段なんですが、日本では年間725万円。最初は3年間のご契約をいただくことになります。初期はユーザーさんの環境によって必要な工事を行ったり、周辺装置も揃えます。初期費用としては1000万円から1500万円くらいあればセットアップして、導入ができますね。2年目以降はサブスクリプションの年間費用と材料費用のみとなります。
中島:ぴったりくるものがちゃんと見つかれば、非常にメリットがありそうですね。
澤田:「なんでもできる」という印象を持たれているような気もするのですが、やはり向き不向きはありますね。でもやっぱりこの技術でつくりやすくて、利益が出せるっていうものを選んでいくと、比較的導入は早いかなと思います。
下宮:ありがとうございます。あっという間の40分でした。澤田様、本日は本当にありがとうございました。
澤田:ありがとうございました。
※PDFでもお読みいただけます。こちらからダウンロードください。
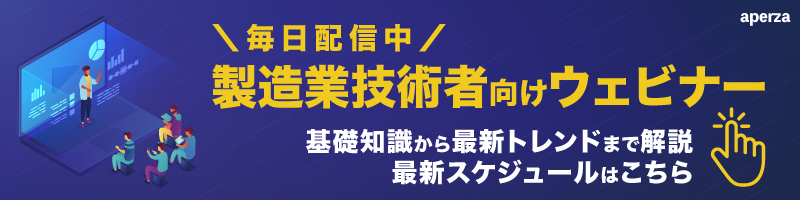