運搬活性化分析では後工程は神様の精神で問題解決
「後工程は神様」の精神で、運搬作業の積み替え作業発生のムダをなくする。
運搬活性化分析では、少なくとも活性示数2以下を維持する、という話です。
1.運搬活性化分析
運搬作業自体では付加価値を生みません。
ですから常に運搬作業の最小化を目指します。
運搬改善に用いられる代表的な3つの手法は下記です。
1)運搬工程分析
2)運搬活性化分析
3)カラ運搬分析
このうち2)の運搬活性化分析は、運搬作業の前後に発生する積み込みや積み下ろし作業の手間の度合いを分析します。
「後工程はお客様である。」
一般的なことですが、これは現場の習慣として定着させたいことです。
運搬作業では、この「精神」が有効です。
次に運搬する人の手間に配慮をして、運びやすい状態で荷物を置く、適切な大きさのパレットの上に適切な量の荷物を置く。
運搬が必要になった際、特別な手間をかけず、すぐに移動ができます。
こうした運搬にかかる手間が運搬活性化分析の対象です。
工場に置いてある物の移動のしやすさを「活性」と表現します。
活性化されている、つまり移動しやすい状態にあるほど数値が大きくなります。
運搬活性化分析では、運搬で発生する「手間」を4種類に分類しています。
1)まとめる
2)起こす
3)持ち上げる
4)持っていく
下記は5つの状態の運搬活性示数を示した表です。
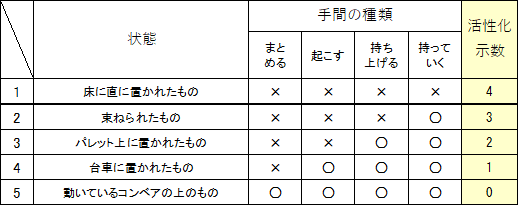
×印は手間がかかること、〇印は手間が省かれていることを意味します。
床に置かれたものが活性化示数4です。
動いているコンベアの上のものは、手を触れずに移動してくれますからゼロです。
〇が並んでいれば手間いらずで、物は移動しやすい状態にあります。
工場内で物を保管する場合、少なくともパレットに置かれた状態、活性示数2を維持したいです。
積み込みや積み替えなく、フォークリフトかハンドリフターを使えば移動できる状態の維持を目指します。
運搬には手間をかけたくないですから。
2.積み替え作業が発生していた現場
以前、お付き合いのあった企業の現場でのことです。
そこの工場では切断、切削加工、溶接等、多様な固有技術が機能別レイアウトで展開されていました。
製品も特注品から規格品、分野も自動車関連から環境関係まで多種多様です。
外部の人間からは、製品の流れが見えず(これ自体に改善の余地が大いにありますが。)生産管理が複雑そうでした。
多様な製品を製造する関係で、外注も頻繁に活用していました。
その現場での役割分担に、外注先への搬送、外注先からの搬入担当がありました。
工程の加工済品を搬送し、また、外注先から搬入された加工済品を、場内へ戻す作業を「専門」に担当する人がいたわけです。
外注へ搬出する直前の工程担当者が、半製品をパレットの上に仮置きして仕掛品として保管します。
その企業の現場へ足を運んだ時、度々目にしたことがありました。
その専門の担当者が、外注へ搬出する際、加工済品を別のパレットに積み替えている姿です。
聞くと、現場で仮置きされていたパレットでは大きすぎて、トラックに積み込めず、小さいパレットに積み替えているとのこと。
トラックで加工済品を搬出する時、他の搭載物の兼ね合いもあり、パレットの形状やサイズに制約を受けていました。
その加工済品を保管した工程担当者も、手抜きをしたわけではないでしょう。
搬出作業を専門に実施する担当者がいるという気安さから、
特別の配慮なく手ごろなパレットに置いていたのかもしれません。
保管場所についても統一した決まりごとがなかったのも一因でした
搬送作業者と工程作業者との役割分担が、重なっているところにムダが生じていた事例です。
次工程で必要とされる状況に、少しでも思いを馳せれば解決できる問題のように感じました。
もし、外注搬出に使われるトラックに適したパレットの仕様や、外注先で搬出入されるときの状況を現場で共有できていれば、さらに一歩進めて、搬出用のパレットが標準化されていれば、少なくとも「積み替え」という作業は発生しません。
情報共有で運搬作業の手間を最小にしたいです。
少なくとも活性示数2以下を維持したい。
積み替え作業をしていては、床に直置きされている品物を扱うのと、同様の活性示数となってしまいます。
3.余談を少々
余談ですが、「直置き」という言葉に触れるたびに、新入社員で現場へ配属された頃、現場管理者(組長と呼んでいました。)に教えてもらったことを思い出します。
工場で生産していた大型の自動車部品を現場に保管しようとした時です。
「ものはパレットの上に保管するものだ」
ということが身についておらず、床に直置きしました。
「何をやっているんだ!!」と背後から組長の大きな声。
「製品を床に直に置くとは何事だ!これで俺たちは飯を食っていることをわかっているのか!」
と、その組長は一喝した後、にこっと笑って
「ということも初めてのことだから、わからないよなぁ。だけど現場で作っている製品ってそういうものだろぉ。」
当時の現場は、今振り返ると、高卒だろうが大卒だろうが、自分たちが受け入れた新入社員を「教育するぞ」という雰囲気があったように感じます。
多くの組長に育てられ、ありがたいことでした。
物の置き方については、その組長のショック療法(?)によって、強烈に印象の残っていることのひとつです。
ですから、今も、工場を訪ねる時には、物の置き方が気になります。
物の置き方で、その工場の現場の風土や文化を垣間見ることができるようになったのも、その組長のおかげと感謝です。
後工程は神様の精神を発揮すれば、運搬に関連した積み替え作業の問題はほとんど解決です。
現場の連携、チームオペレーションで、運搬問題が発生するのを事前に防止するのが結局は安上がりとなります。
後工程は神様という意識が現場に定着していますか?
次工程のことに配慮する雰囲気がある現場でしょうか?
現場での物の置き方をチェックして下さい。
特に先入れ後出しができな置き方をしているところ。
物の移動で現場が困っていませんか?
まとめ。
「後工程は神様」の精神で、運搬作業の積み替え作業発生のムダをなくする。
運搬活性化分析では少なくとも活性示数2以下を維持する。
株式会社工場経営研究所 「儲かる工場経営」メルマガ ご登録ください。
毎週火曜日配信中。
https://48auto.biz/koujoukeiei/registp.php?pid=3