経営革新・戦略地図を作らず、どのように企業革新を進めるの?
この例は、まだISO9001(以降、ISOと省略)の取得が日本では始まったばかりの頃、I講師がP社で対応した相談への対応です。
P社では、ISO取得に際し驚くほどの集中をされ、当時、業界でも1~2を争って取得したことで有名な企業だった。産業界に、取得前の期待は「これさえ取れば、品質管理体制がこうなり、ああなり……」というお話もされていた。
しかし、本音は「当初予定したような効果が出ていない」というお話しと共に、多くの問題をI氏に相談された。
この話に対し、I氏は「あれは紙づくりと言われる方がおられます。また、取得に対し、試験の答案が良ければ資格をくれるのに似て、ECに貿易ができる免許証の機能を持って生まれた、と言う人もいます。
また、ISO取得だけの目的なら、紙づくりの効率化を徹底して考えられてはいかがでしょうか? しかし、それでは家庭の図書の整理と同じです。
それより、ISOをどのように企業内で使うかを、もう一度、原点にもどって見直すことをお勧めしたいと思います。
下図に示したように、企業改善にはステップがあります。人の総意(ベクトル合わせ)が出発点ですが、ISOはまだ、第2段階です。
この図の意味するところは、工場改善に当たって、モノづくりの見直しを中心に製造プロセスを見直し、人の段階から、方法→計測→設備→物(設計)と段階を進めた効率化を図るステップをたどる手順を示唆したものですが、先にお話したように、方法に当たる標準化という種類づくりの段階では、レベルの高い品質と製品競争力の強化に、ISOの実務的活用が図れないのではないでしょうか?」とI氏がP社で話したところから、以降の提案内容に入ることにする。
なお、現時点では下図に示すように、ISO9004:2009年版として品質マネジメント・システムの運用が経営直結型となっているが、単なる書類づくりだけでは会社経営に貢献しないばかりか、企業内に矛盾を抱えることになります。
その意味でも、ここに示す内容は既に、その当時からこの種の問題を扱った内容として価値がある話しです。
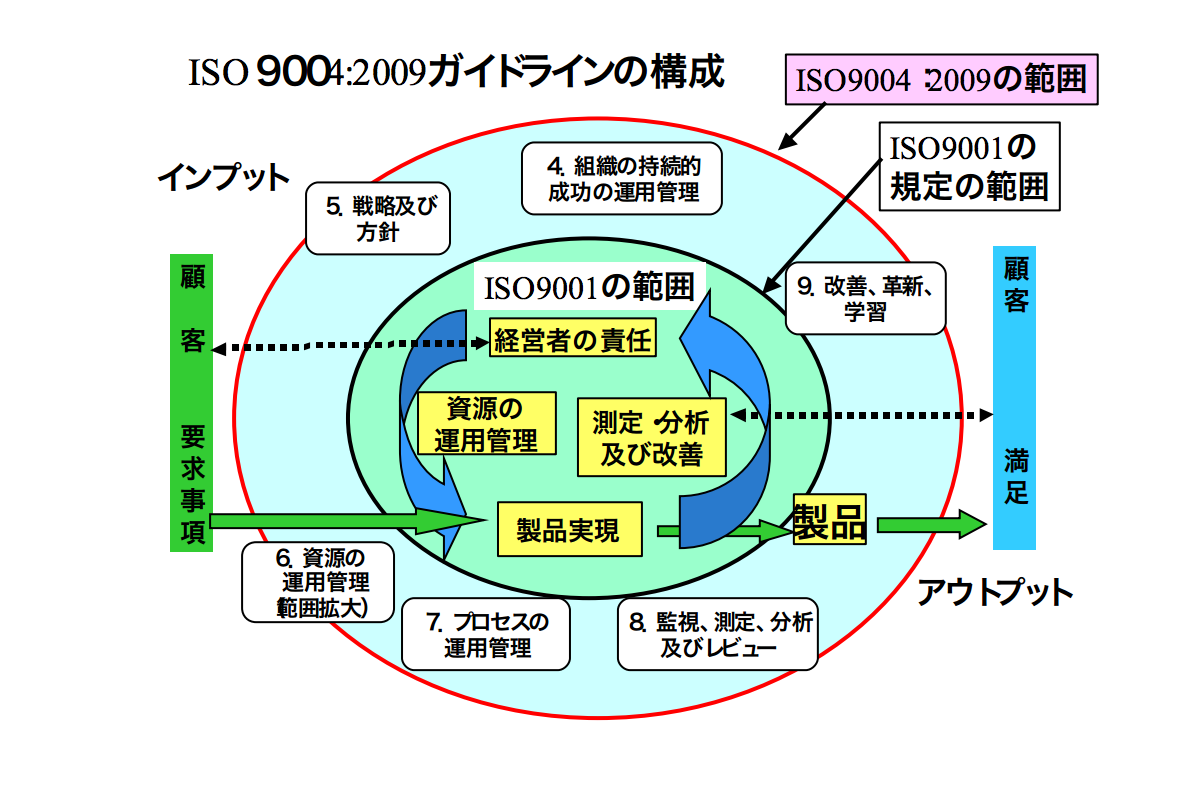
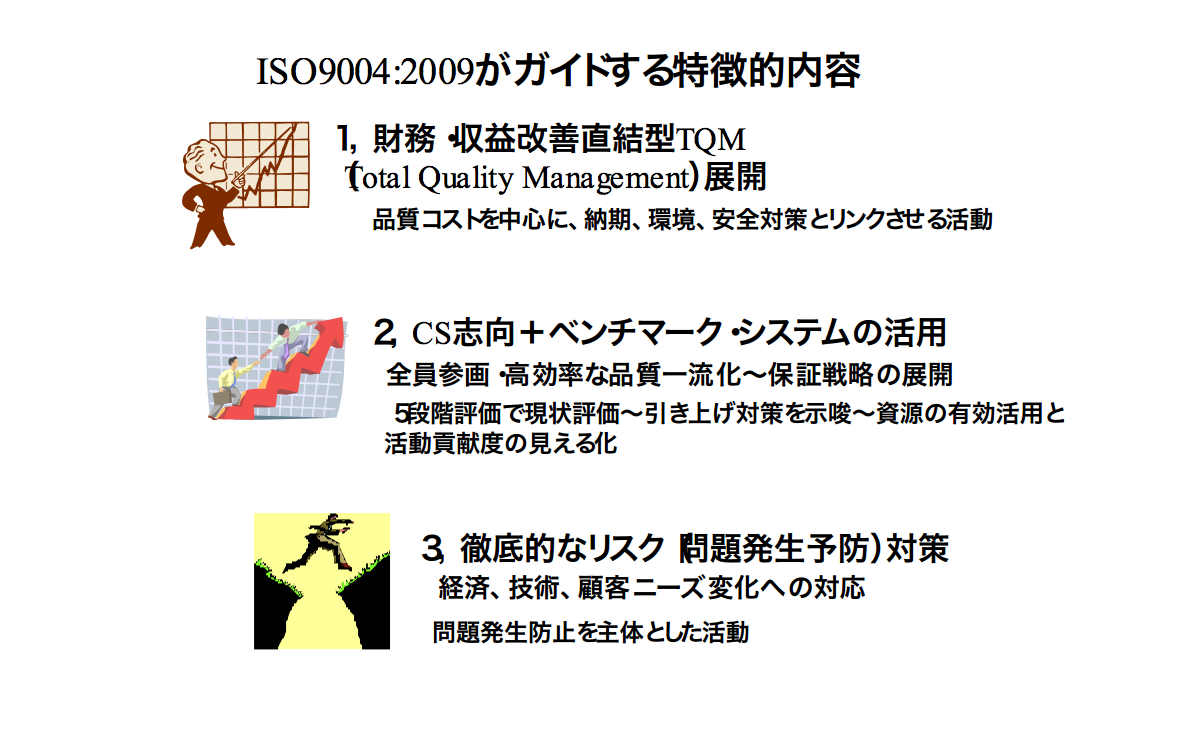
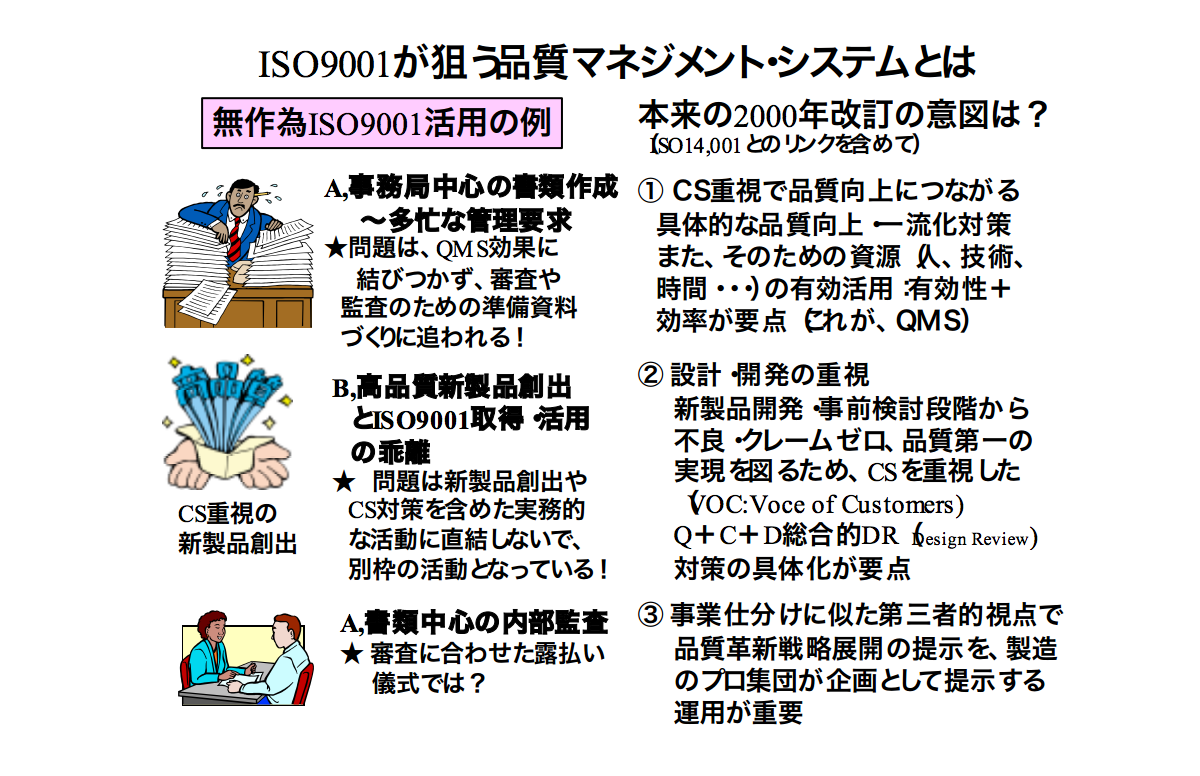
【注釈】
人の段階から、方法→計測→設備→物(設計)と段階を進めた効率化を図るステップは次に示す図となります。
I氏の話によると、I氏をP社に呼んだ理由は、P社のトップの方が「かつて研修で受けた中に、この話があったことを覚えていた」ということがきっかけでした。
「イヤー、Iさんが当時話されていた、まさにこの図の標準化の段階で留まり、困っています。
ISOは品質だけを対象にしていますが、経営的に見ると品質はともかく、生産性、納期、原価……を総合的に対策しないと、それに次には環境対策のISO14001が出てきますし、それに当社のような分野に関係する企業では安全衛生が続く状況でしょ、一つ一つやっていては大変だし、ここだけの話ですがトップが変わる度に方針が大きく振れる状況も、と考えると、これからが不安です。
弊社は業界で有名な○○賞も取りました。しかし今見ている限り経営効果はなく、行きづまりの状況です。そこで……」という話しだった。
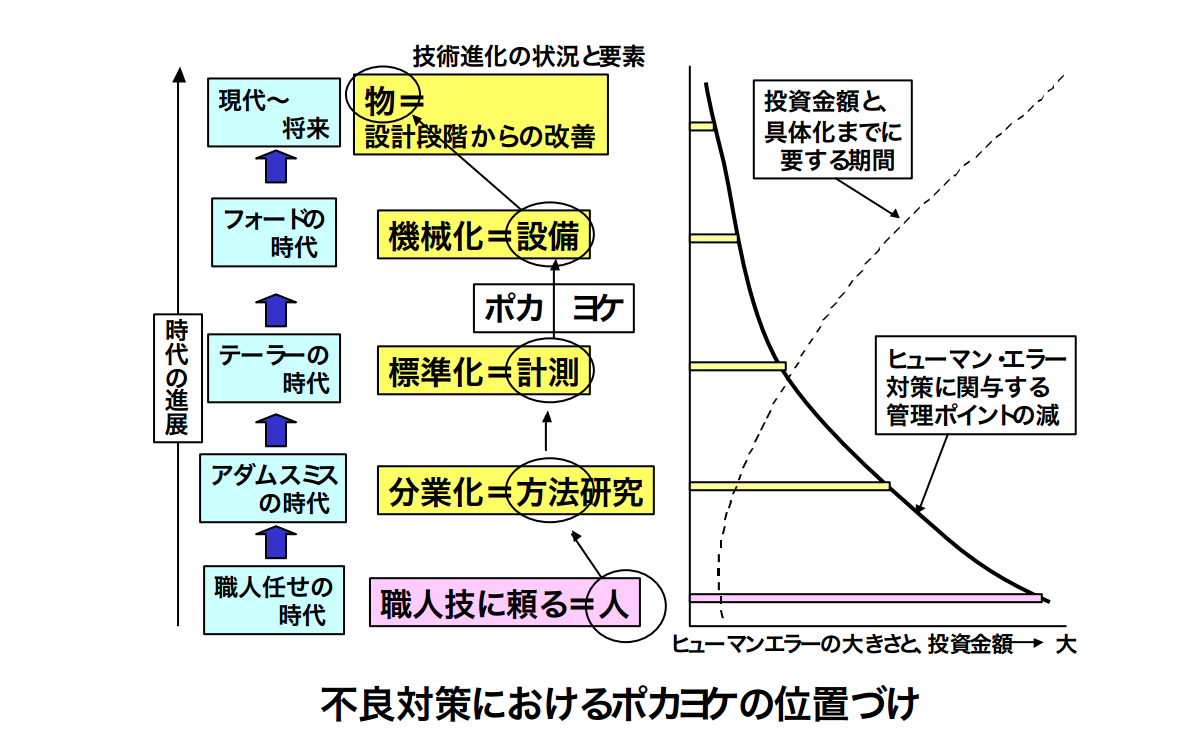
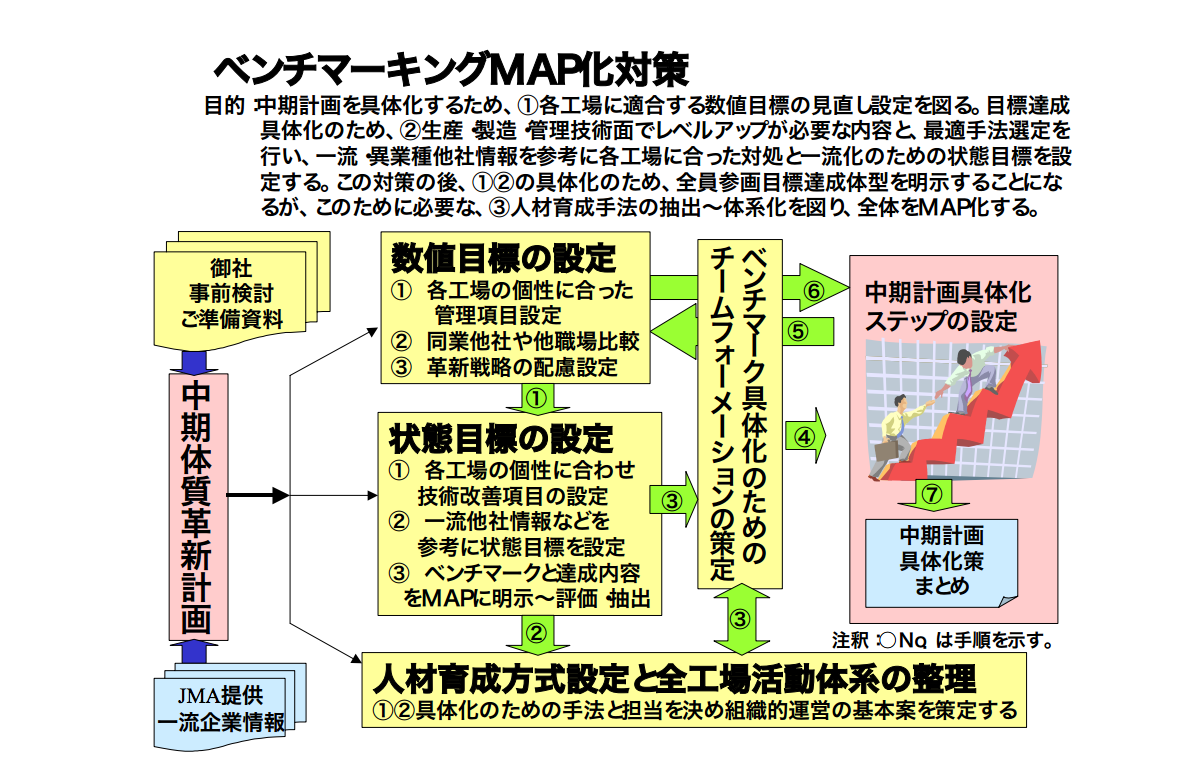
上図はその概要だけを示した図だが、手元に用意していた、また昔から活用してきた工場体質強化地図を紹介した。
「これは工場の立案から軌道に乗せた時に活用した体系図です。戦略づくりには地図がいると思います。
昔、このような考え方から、先ず原価分析・経営シュミレーションを行いました。それがその時のものです。
私自体も、海外工場赴任になった時これを活用しましたが、当時は系統的に、しかも、客観的に企業の体質を強化する上で大変役立ちました。
ほとんどの戦略と、戦術、体質強化の手段はこの地図で結論づけ、皆が理解し、それぞれの役割と責任で、重要課題を個々に進めてくれたからです。
ただ、生産主体の工場だったので、ここには新製品開発や販売戦略の対策はありません。ではこの図を簡単に説明したいと考えます」と言って、I氏は中期計画を側面的に客観評価するために作成した上図の解説に入った。
「この図表作成にあたっては、当時日本中にある有名な手法約3,000件を棚卸ししました。
その使用目的と効果を例記し、当工場で使うには何の役に立つかについて機能(目的)系統図化した結果、3つのカテゴリーに分類されました。
3つのカテゴリーの最初の内容は、まず①『経営指標をどのように定めるべきか?』という、近々また、段階的に達成すべき数値目標の設定です。原価・品質・納期・生産性を中心に収益性を評価するための各種手法や評価式がここにあります。
②次のグループは体質強化の手段と状態目標を示すグループです。状態目標は数値目標を高めるための技術レベル強化内容ですが、例えば改善力があがれば生産性があがる、事実解析と評価技術のレベルがあがれば不良撲滅や品質向上になるといった要件です。
従って、IE、QC、VEを始めとして、自動化、生産管理、コンピュータ利用技術など各種の改善手法が関与します。
なお、ここにはその中から、当工場に活用可能な手法を選定し、その意味づけと共に対策を系統図で示しました。
最後に、③あるグループは経営指標を上げ、手法という道具の使い方をマスターして効果をあげるための人材育成が必要になります。モノづくりや企業革新は人の活動によって左右されるからです。
なお、集合教育も大切ですが、自己育成の基本は自ら学ぶ活動が85%です。その他、OJTやOFF・JTもありますが、この種の研修は自己研鑽に対しては補完的な内容です。
目標を持って自ら学ぶ行動が人づくりの基本です。
したがって、このような内容も意味づけをし系統化して、ここに経営改善との関係で何がどこにどう役立つか? を図上に示しました。
この図は私が企業に在勤の時代に作成して活用してきたものですが、このように作戦地図をつくり公開した結果、はじめて関係者が、私がいた工場では何の手法が何に役立つかが明確になりました。
手法の中にはハヤリ病のように出て消えて行くものがあります。しかし、この整理をしてからは、新手法もここにある手法の組み合わせでできていて、適用範囲や内容、その効果までがよく評価できるようになりました。
次に、各種の手法を使って何をすべきかが大切になります。手法偏重的、底辺的なの使い方や、誤った素人的な活用ではなく、一流であり、わが社にお手本になり効果が高い活用例を、世界中から情報を集め、異業種の取り組みを含めて調査して、ここに記入しました。
なお、特別な費用がかかり当社では実現性のないものは外しました。
逆に、異なる業種でも当社で到達可能な内容は取り上げ、事例と共にこの地図に登録しました」
「この段階で、当然のことですが一般的レベルから一流レベルの間に段階があります。
そこで各改善要素に対し、一流企業が取り組んできた内容を最高レベルと定め、以下、5段階のステップを設定しました。
また、5段階に至る内容は、一流企業の状態と、その企業の活動経過を見直せば、歴史として整理することで5段階を基本にその下のレベルを決めました。
なお、この判断が仮定では空想的な内容になります。そこで、重要な事例については、その経験者にインタビューしたり、文献で判断したり、工場見学と共に取り組みの実態を教えていただき、そこで得た内容を参考に、この5段階の内容を再整理しました。
更に、単に事例任せでは我々が取り組む意志のようなものがないため、先の5段階レベル改善法の考えもここに含めました(人→方法→計測・治工具→設備→物=設計の順に対策し、管理ポイントを減らし、レベル向上を図る対策です)。
ここまでの対処と当社の現状把握で、客観的な現状段階のレベル把握が、概略的ではありますができ、何をすべきかが整理できました。
このような工場革新地図をつくってわかったことですが、どのような世界一流企業を例にとっても、この図表の内容全て満たした一流を満たす企業はない状況です。
また、ここが我々の狙いどころであり、限られた人、時間、資金…を駆使して特徴的な企業を具体化していくことが大切であることがわかりました。
企業には個々の特性と文化があります。そして、それより何よりも「限られた人、時間、金、資材、技術力や設備の制約の中でこの5段階を上手に登ってゆくわけで、全てを一流にはできない。それなら、限られた資源をマネジメントして、強みを伸ばし弱みを消す対策を指向すべきだ!」という戦略展開内容が明らかになってきました。
この種のチームの強化にあたる取り組みには、必ず組織的な活動が必要になります。
また、全体を良くするには、誰が、どの分野を担当するか? も明確にすべきです。
産業の種類や範囲が限られると、進む道と内容はほぼ決まり、この内容をいかに効率よく進めるか? が企業競争力強化になることがわかります。
また、このように取り組むべき課題や問題、達成レベルなどを整理すると、今まで振り子のように方針をトップの方が変更したロスと言うのはかなり無駄なマネジメントであることがわかります。
逆に、このような地図を題材に皆に嘱望され、しかも当社の人、技術を上げたトップの行動も良くわかります。
特に、客観的に5段階の状況に色塗りしてゆくとその状況がわかります。
要は、管理者の能力差で企業の体質改善の進歩が左右されるのではなく、加速させるに足る人材の選定に此の地図が活用すべきであると思います。
実際のマネジメント活動においては、個性を重んじた一つの技術と言う形をここに示すべきです。
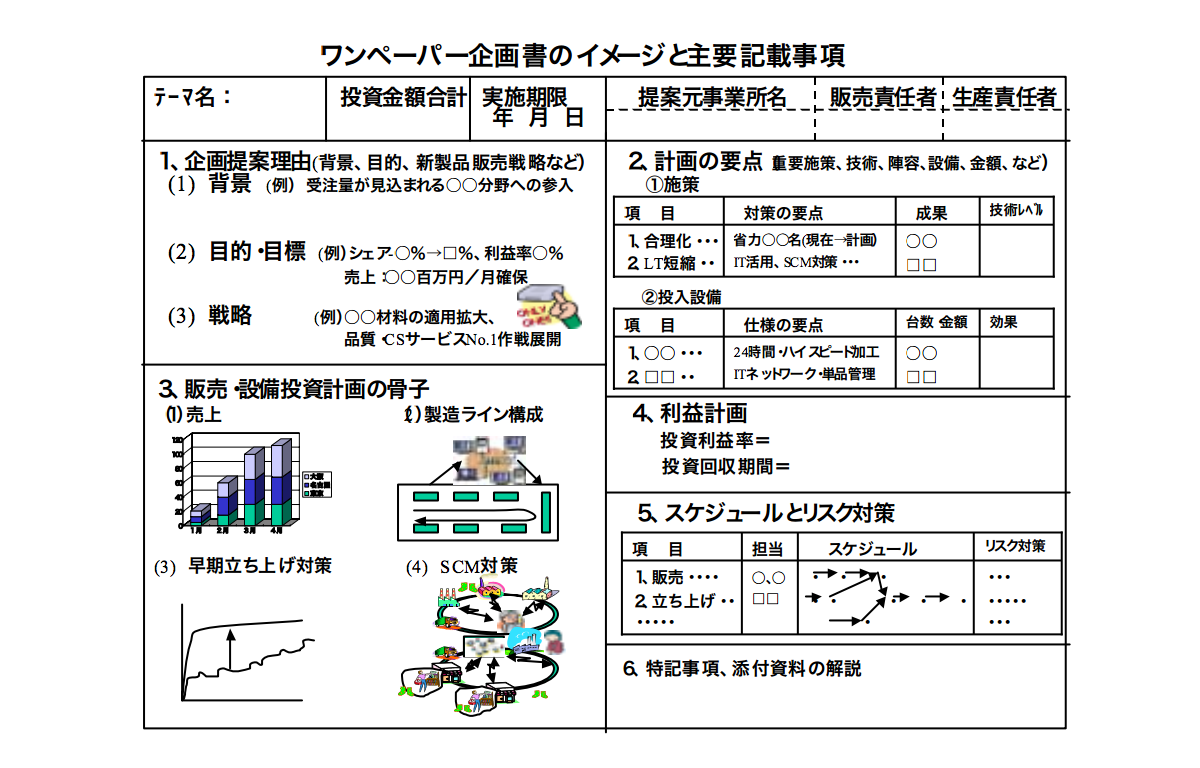
さらに、バランス感覚、という言葉がありますが、その意味はこの図で段階を登る方針を決めたら、その評価自体がバランスとして良いのだろうか? ということを示しています。
となると、先に示した手法とその機能には当然のことですがウエイトをつける必要が出てきます。
その結果、下の図のような経営計画を策定し、その1段階として予算を定め、達成しつつ5段階のレベルを上げる、という対処が重要になり、逆にこれこそが、目的と目標を定めた中期計画の展開になります」
「ここまでの内容を地図で評価し、丁度、山を登る時に手法を登頂ルートや道具のように道つけ、さらにはアウトプットを決めると、この地図の3段階程度は達成し、我が社の中期経営計画とこの内容を融合させる必要が生じます。
このためには、先の経営計画シュミレーションとこの内容を結合させる必要が出てきます。
この解説は別の機会にさせていただきますが、いずれにせよ、対策手段とアウトプットを参考にして、将来の予算をつくる必要が出てきます。以上お話の内容は企業の将来を企画する筋道としては理の当然の流れではないでしょうか?」
「なるほど……」
「この図を用いると、中期経営計画を技術改善項目と同時に、手段と共に目標数値付きで整理できます。一般に、目的と手段、期待効果がわかって企業が持てる資源の投入と人材育成を集中的、段階的に投入する効果は大きいことが示されています。
改善内容を担当者のスケジュール、期待されるアウトプットと共に表現した内容を戦略と呼ぶ! と私は定義して活用してきました。
この例は私の米国で用いてきた経験談の例ですが、他社が同じ地区でアルミ鋳物の工場を5年稼働し、悪戦苦闘したにもかかわらず、残念ながら撤退しています。
しかし、私たちは同じ地区では2年で軌道に乗せました(’88年に工場建設、’90年には収益を出し、’95年現在2倍の規模で順調に体質を伸ばし、販売も伸ばしている実情)それも素人ばかりの集団を訓練してのことです。
何とかやってこられたのはこの図が一つの大きな役割を果してくれたからです」
「なるほど、お聞きしていてわかりました。我々が求めていた通りの内容を目の前に見たような気がします」
「そうですか、ご期待に添えて何よりです。このプロット・タイプは既に私の工場時代に適用してきたものですが、米国赴任の5年前、関係者の説得を得ながらある会社の記録をヒントに自分なりに改良を加え、6カ月かけて今まで蓄積した調査資料と共にまとめたものです。
その時も、管理者とスタッフのアウトプットを正確に決めた内容として評価を得ました。
企業革新には、個々個人の力量と思想で活動する自由さと意外性も大切ですが、人材育成とその効果を示すアウトプットの記載、工場の体質改善の目的を明確にした取り組みの方がシステム的です。
各種対策が明確となるからです。勿論、A社の体質強化の際、各種の職制や組織の改正をこの地図をもとに行いました。
やがて、そのことを行ったトップも途中で交代しました。しかし、方針はこのような内容を早める努力はあっても、振り子現象や、アドバルーン的な対処はなかったし、また、内容がオープンにされていただけに多くの知恵が集まり、外部からの風評や間違った指摘も評価しながら改善を進めたことが、A社の体質強化を進めた次第です。
このためか? ものすごい円高不況の時にも他社、同種企業が赤字転落になっても、A社は黒字を維持することができました。もちろん楽々ではありませんでした」
「そうですか? 確かに戦争でもそうですが、地図、ワンペーパーを目の前に戦略を練り、戦術を検討、駆使していますネ!」
「そうです。山登りもそうですが、地図なく日程計画は決めないはずです、一番良いルートを地図上で決め、その後に行動しているはずです」
「そうかIさんが最初に言われた地図なく戦略は決められない! との内容は、企業体質向上に体質改善の道具を使う地図が必要、という内容だったわけですね?」
「そうです。ご理解いただきありがとうございます。地図なき彷徨は誤った、客観評価ができない戦略です。
世の中が変われば、この地図に修正を加えて前へ進ことではないでしょうか? 代替案を即座に検討できる内容も地図があっての始めてできる技と考えます。
マネジメントの世界には未だ自動車に最近搭載されて便利なナビゲーターのような技術はないようです。
一般的な情報処理の世界にはナビゲーターは研究課題になるかもしれません。しかし、人の個性を重んじる産業の
世界でこのような手法を開発するには時間がかかりそうです。
私も暇ができたら研究してみたいとは思っていますが、私の能力上で限界を感じる次第です」
「いや、それは夢の世界のように思います。とにかく、当面は我々も同じ手順で地図を作っていきたいと考えますので、援助をお願いいたします」ということでP社でも戦略地図づくり〜活用がスタートした。
俗に「5%の改善は不可能だが、半減はできる!」という言葉があるが、この企業ではそのような内容にチャレンジと具体的な対策施策が作られていった。
できない理由を挙げるのではなく、地図をもとに職場間の壁を潰し、制約を取らねば革新などは起きないことが地図を見て皆に理解されたからであった。
なお、この種のガイドはこの種の地図が最も得意とする分野です。
コメント
工場生産の改善〜革新に応用する地図を生産技術MAPという。
数値目標をあげるため、状態目標の質とレベルをあげることが必要になり、この種の内容は次ページの図に示す3つの革新軸を仲介に、未来から現在を見直して現在と未来をつなげる活用をすると効果的です。
また、先の経営企画書は、そのためのマイル・ストーンのような位置づけをして、経営予算に組み込んで進めるべき内容です。
この種の対策には、次に示した経営面の解析を併用すべきことは、読者の方々には言うまでもない内容であると考えます。
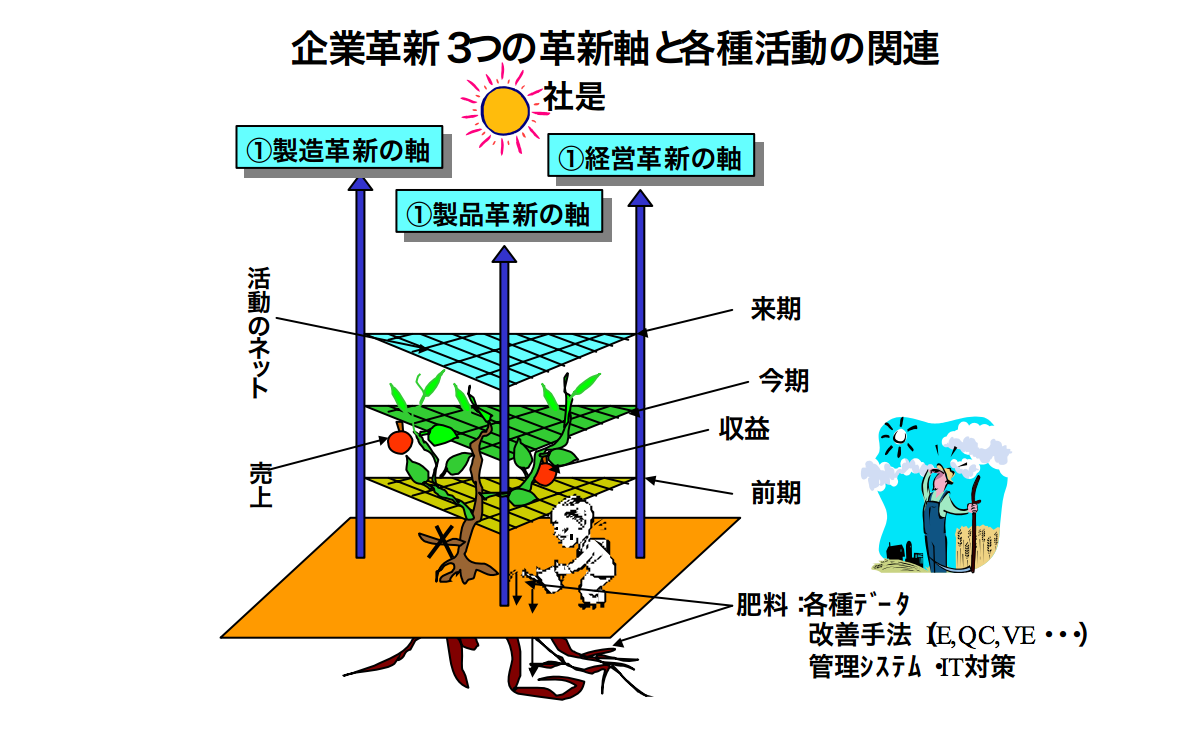

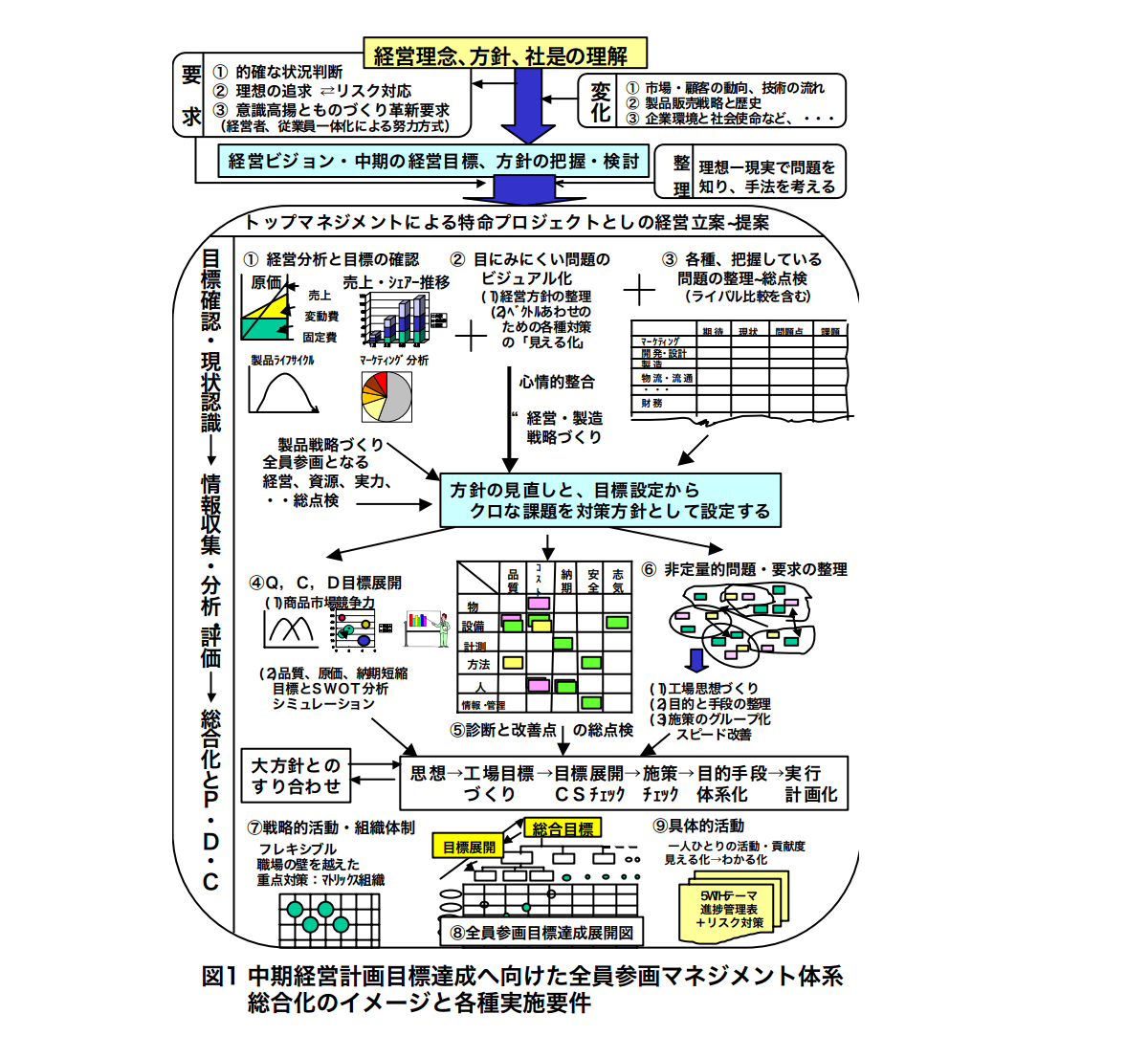