目標達成グラフはいつも青信号、管理がうまいわけではない!
これはK氏がある大手の通信機器製造、S工場へ研修会の講師で訪問した時の話です。
S工場へのK氏の対応例
ここでは、研修前に時間があったため、事前に工場見学をすることになりました。
最初にS工場のトップから
「今日はよろしくお願いします。当工場では、色別管理が進み、生産性が大変上がったので、是非事前に見学された後で研修をお願いいたします」
というお話があったので、早速K氏は現場見学をさせていただくことにしたのです。
工場にはK氏の前に指導されたY・カリスマ講師の写真と共に、JIT指導のポスターが大きく張り出されていました。
K氏研修の講師に招待された理由は、新しい品質改善の手法を現場の方々へ紹介するという目的であり、演習問題による実務改善指導でした。
これは、今まで進めてきたJIT手法に追加する形で不良解析の方法を現場に指導してほしいという要請でした。
K氏が工場に入った時、現場の表示の派手さに、まず驚きました。
特に目についたのは、個人別に生産達成と不良目標管理のグラフが掲げられており、生産活動をしていると、そのグラフが全て青、すなわち全員目標値を越えているようでした。
わずかに、新人の方だけは目標未達成だったわけですが、それは無視できるほどでした。
現場を案内されたT課長は、
「JITは定着しました。ほとんどの人が目標をクリアーできるようになったからです。
Y先生のご指導のおかげです。
わが社は歴史が浅いのですが、JITの環境はマスターしたので不良対策に進行したいと思っているところです。
不良対策は問題ですが生産性向上対策は充分だと思っています」
と胸を張って話されました。
「そうですか、素晴らしいですね。ところで、意地が悪い質問ですが、この目標値には設定記述がありませんが、いつ決めたのですか?」
と質問したところ、
「この目標か、これは半年前のものです」とのお答えでした。
「それはどのように設定したのですか?」
「昨年の実績平均です。JIT投入前に比べて出来高を見ると30%ほど上がっているので、30%実績時間をカットして目標値にしました。何か?」
「いや、3つほどですが疑問を感じます」
「エッ!何ですか? 我々の参考になりそうなので教えてください」
目標値の設定に潜む問題とは
「はい、まず、生産性ですが、半年も前の目標値を使い続けておりますが、
新人を除いて全員が達成しているということは、方法が良くなったことで半年前までとは変わり、今はもはや易しすぎる達成目標になってしまっているのではないでしょうか?
このグラフ自体、何が良くて目標が達成できたのか、また新人の方もそうですが、時々目標を達成したり、しなかったりで、何が問題で達成できなかったかが記載されていないので、その実情がわかりません。
スポ-ツ同様、皆が簡単に達成できるようになったら実力が高まったわけですから、かつての低い目標値を改訂して、もっと高い目標値を用いて生産活動をすべきではないでしょうか?」
「なるほど、道理です。
そのような見方をすれば、10%以上は目標を高くできそうですな!
ですが、今まで、そのの発想は持っていなかった。
早速対策しなければ……。
ですが、今、この製品は売値が大幅に下がりつつあります。
だからこそ生産性向上がさらに必要なんですが。
目標を高め、達/未達の解析は早急に必要ですので、早速、現場関係者に説明して改訂します」
「それは急ぐ必要がありそうですね!」
「では、こちらから質問します。
この目標の設定ですが、実績時間の平均値で良いのでしょうか?」
「次に、その話をしようと思っていたところですが、
答えは、この設定方式は、はっきり言ってバツです。
達/未達の解析の科学性というか、論理性・納得性に欠けるからです。
“時間は仕事の影である!”という名言がIE手法にあります。
作業条件が整備され、作業手順が科学的に決められ、納得いく数字に設定すべきだということを意味します。
これが二つ目の問題点ですが、電機業界ではWF法という動作研究の後、既に国際標準で定められた時刻表を用いて時間(PTS[既知時間見積]法)を算出するのが普通です。
この設定値は習熟したベテランの作業者がやる気の国際ペースで仕事した場合で算定される関係上、時間の遅れが発生したとしても、それが科学的に評価されるので有効です。
この設定は正味標準時間の設定となりますが、その他現場観測により、偶発的に発生すれば、例えば部品を供給する、打合せを行う……などの追加をします。
余裕率という形で正味時間に加算して、標準時間として設定するわけです。
ここまで専門的で無くても、レイティングさえ正確なら、時計観測を利用した標準時間設定でもかまいません。
下図で示しますが、これが、科学的な標準時間の設定です(なお、PTSの場合、動作とその難易度を作業に対する時刻表としているため時計観測より信頼性が高い)」
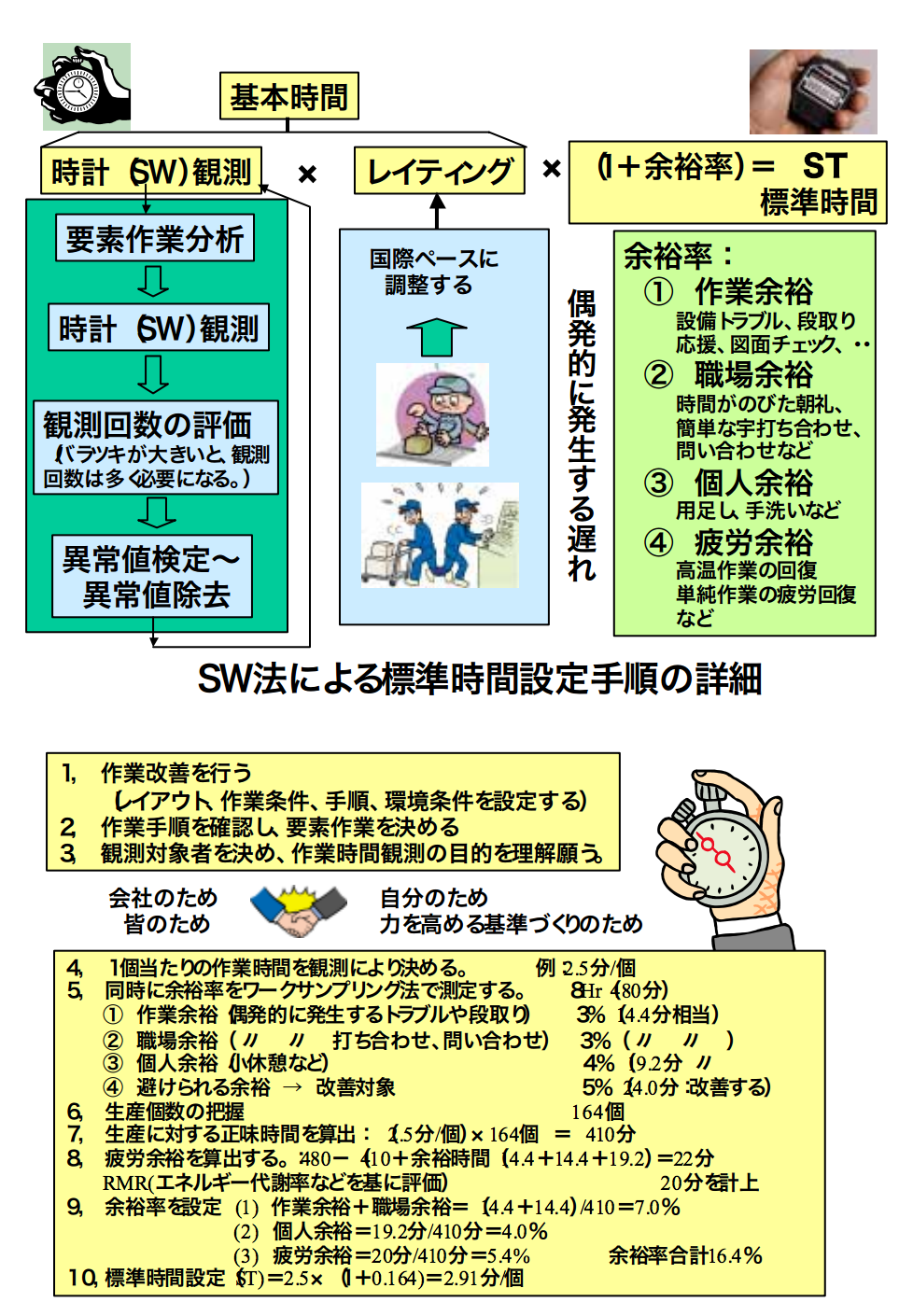
「このような作業時間設定の手続きが科学的な標準時間設定法ですが、実績時間では、手順がどのようになっているのか、余裕率の中身がどのようになっているのか、そして作業ペースが国際標準に比較してどの程度なのか、がわかりません。
ですから、仕事を終了した後、なぜ遅かったのか、早く仕事が終わったのかがわからないのです。
このため、何が良くて何が問題なのかがわかりません。
したがって、仕事の正しい評価や改善点の発掘だけでなく、目標とすべき対象になり難いわけです。
スポーツでもそうです。
あまり良くないコーチにつくと科学的練習にならず、気合い中心になるため実力向上の理由がわかりません。
したがって、選手強化には不向きです。
このような話は今やスポーツ業界では常識です」
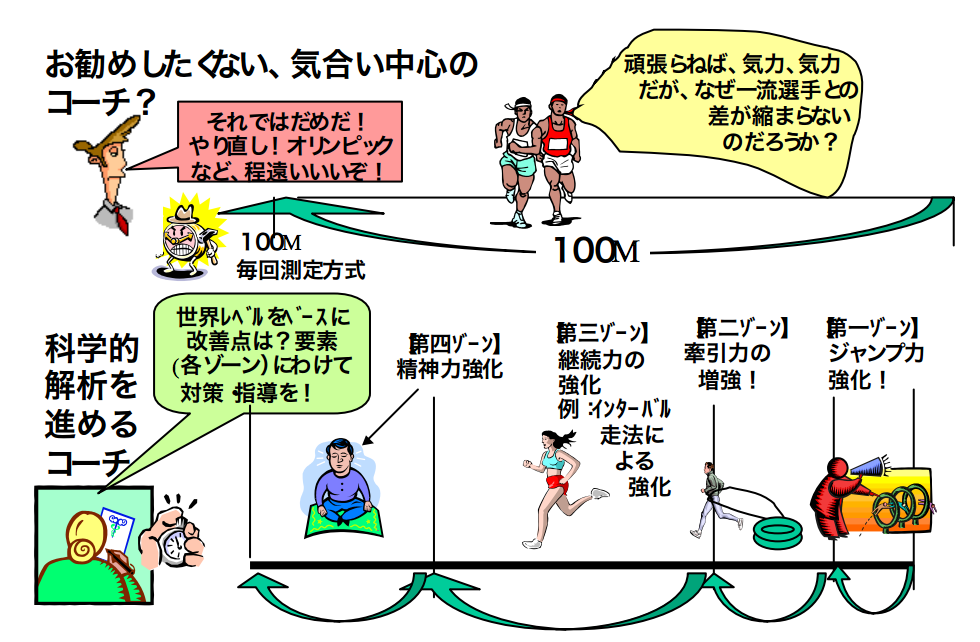
「現場作業も同じです。
作業者としては、標準にすべき対象の構成がわからないので、仕事が早くできても、その理由が頑張ったためなのか、あるいは部品の到着、作業指示のスムーズさによる効果なのかが説明ができないのです。
対象にする時間の中身がわからないから、改善の程度や努力目標もわからない。
このことは、ある方がどこかへ出掛ける時、列車の時刻表を持っていなかったり、地図の距離を知らずにハイキングをしたりすることに似ています。
作業ペースは2種類あります。
ノルマル・ペース(MTM)と、やる気のペース(WF)です。
また、その差は25%もあります。
御社はどちらをお使いになるかをお決めになる必要がありますが、
少なくとも、このような時間解析はネック工程を中心に算出することが経営上大切です」
「なるほど、その話は聞いたことがありますが、この現場での実務的活用についてはそこまで発想がいっていなかったことは事実です。
Y先生から“JITはIEを越える手法”と聞いていましたので、気にもしていませんでした。
では、3つめは?」
「標準時間と関係しています。作業手順を見てください。
このラインにおられる10名の方は、一人1個流しU字ラインですね。
それはそれなりの意味があると思います。製品の品質責任上の対策として有効だからです。
私が持ってきた、この方のグラフを見てください」
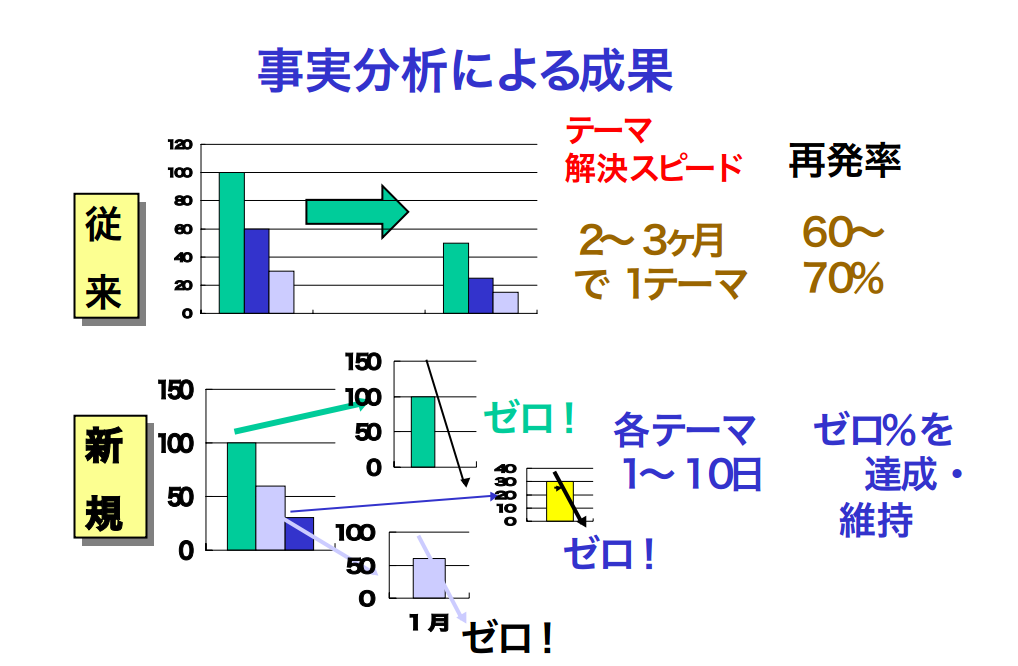
「不良ゼロ化への対策工数は少なく、また、対策から現時点で半年になりますが、その間は不良ゼロのままでした。
ここで重要な点は、時々不良を出している方の作業時間は変わりないように見えますが、手順が全く違っていました。
このような視点が改善には必要です。
なお、不良ゼロ達成者は、仕事のチェックをしっかりやる分、時間が余計にかかっています。
しかし、部品の置き方を工夫していたので、他の方と比較してもトータルは同じでした。不良が出ない、良い手順を確実に取っておられます。
このような部品組み立て工程の場合、我々は職業柄、どうしても仕事の手順を見てしまう傾向が発生します。
一般に、多くの現場管理者の方々は“○○さんは今日も頑張っている”というように、人間的局面を重視する傾向は強いですが、手順の中身は見ていない。
また、結果だけを云々してしまう傾向があります。悪い場合には人の能力の差にしてしまうこともあります。
さて、手順分析に当たってはビデオを用いたスローモーション解析が有効ですよ」
「そうですか、ただ仕事を見ていてもだめなのですね。
確かによく見ると、作業手順が皆ちがう。なるほど」
「そのようですね。
いずれにしても、現場の問題がよくわかりました。
研修の場でリーダーの方々とこの問題をつめることにしたいと思います」
と言って、研修のスタートとなりました。
KさんはS工場でたった2日ほどの研修を行っただけでした。
ですが、現場作業(人でなく作業手順)をビデオ撮りした解析で、生産性の向上ばかりでなく、不良を出さない手順の検討が大きく進みました。
コメント
現在、『目で見る管理』は工場生産のコミュニケーション・ツールであり、多くの企業での活用が盛んです。
ですが、このの手法は、単にお飾りの『見える化』に留めず、「できる化」~「できた化」対策を図り、改善活性化の題材とさせることが重要です。
Yさんが担当された研修会の前段として工場見学なさったのは、この点、すなわち、「見える化は良いのですが中身が作業レベルの向上に直結していますか?」という点を突いたためであり、管理側が注意すべき重要なことをコメントしたのです。
このことをお聞きした時、各社で『見える化』が盛んに行われていました。
ですが、その中には不良や機械故障統計を死亡診断書形式で示すものもあり、このお話をYさんからお聞きした時、筆者も同じ経験を持っていたので、この指導に共感した次第です。
今回の事例は、「何の目的で記録や活動を表示しているのですか?」という注意です。
そこで、以下似たような体験談を紹介することにさせていただきます。
A社への筆者の対応例
A社へお邪魔した時のです。
A社から筆者へのご依頼は『改善の活性化』でした。
ですが、下図に示したように、ここでも数多の表示がなされていました。
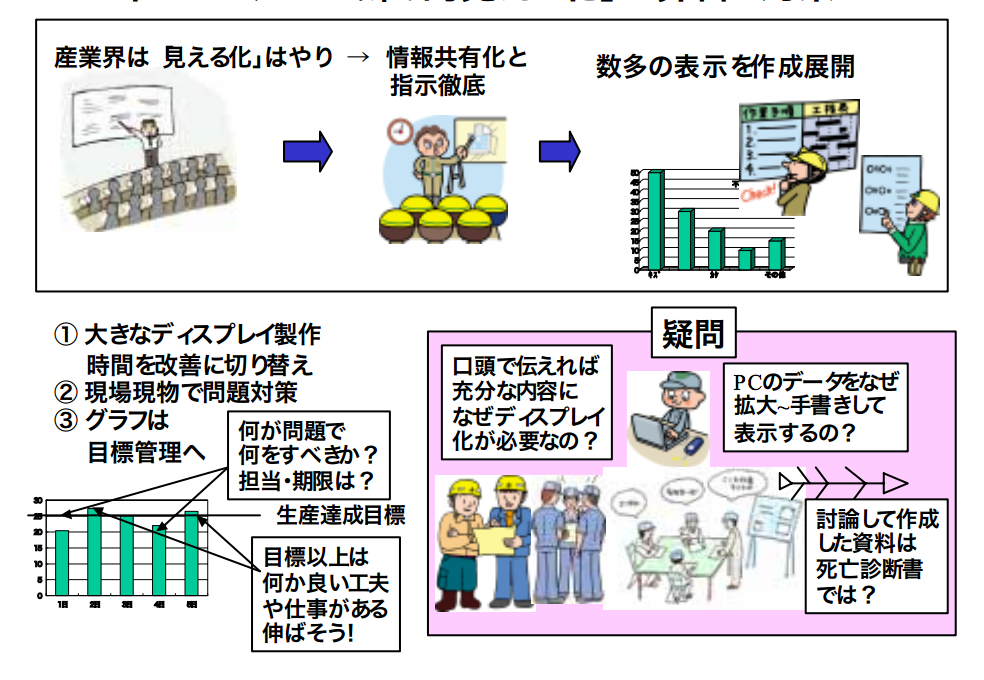
そこで、「表示は良いのですが、このようなビラを1枚作るのに、誰がどれほどの時間をお使いになっておられますか?」とお聞きしました。
すると、「PCから提出されたものを貼るだけのものを除き、1枚のビラに2名で1時間!」ということでした。
「では、6枚ほどあるので6時間×2名=12時間ですか?」
「ハイ、仕事の合間を見ながら作成していますが、PC資料もコメントを付けたり、周りのデザインを付けたり……ということを考えると、15時間/月程度が必要です」
「では、その時間を私にお貸し願えませんか?」
「どういう意味ですか?」
「このビラづくりの中身ですが、結果と問題は書かれています。
ですが、何が問題で、誰が、どのように何をするかが記載されていません」
「早速、書かせたいと思います」
「いや、そのお願いではありません。
1ヶ月ビラを書くのを止めて、この15時間を不良対策と生産性向上に使いたいというお願いです。
このビラに書かれた不良は、ゼロになればここへグラフを書く必要はないからです。
設備故障もゼロ化すれば記載不要です。
生産性も目標を達成すればその最終値を書き、次の目標へ向かう課題と進み具合がわかれば良いわけだし、
PCをこの表示の近くに持ってくれば、必要データは見ることができるので、それを先にお進めになる方が有効だと考えるからです」
「なるほど……」
ということで改善を進めたわけです。
改善は枯れ葉やワラの束を燃やすかのように進みました。
その結果、見える化対象は1/10以下になり、改善の活性化にも大きく貢献しました。
「何のため?」という目で『見える化資料』を見直した結果です。
読者の皆様には、投入費用や工数と、見える化資料の有効性を評価する対策に、この話がお役に立てば幸いです。