生産管理システム導入の現場 ~お客様は何に苦労し、どう乗り越えたのか~
こんにちは。テクノアの間野です。
弊社では、生産管理パッケージシステム「TECHSシリーズ(以降、TECHS)」の導入を通じて、中小製造業様のコスト削減・業務改善活動を支援しております。
今回は、TECHS稼働後2年が経過し、改善効果を出されたコーセーエンジニアリング様を訪問しました。その際に伺うことができた、導入時の苦労や体験談を生産管理システム導入の現場レポートとして、ご紹介いたします。皆様にも参考にして頂ければ幸いです。
新システム導入では、導入前のお客様の状況などにより多少の差はあるものの、乗り越えなければならない課題が必ずあります。コーセーエンジニアリング様のシステム導入の取組み姿勢からその課題解決のヒントを頂きました。
コーセーエンジニアリング様はもともと、独自の基幹システムを使用されていましたが、会社規模の拡大により、その運用に限界を感じていらっしゃいました。また、独自システムならではの便利さはあるものの、度重なるシステムの追加改造によって、システムに統一性がないという問題も抱えていらっしゃいました。
そこで、個別受注型の中小製造業において導入実績No.1の生産管理パッケージシステム TECHSをご検討頂き、ご導入されました。
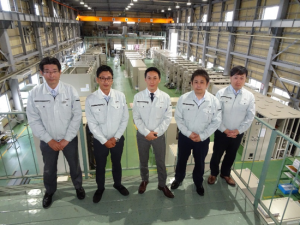
部分最適ではなく全体最適を
コーセーエンジニアリング様では、TECHSの導入は「今やっていることの継続」ではなく、「会社の業務見直し・改善のきっかけ」という認識のもと全社で取り組まれました。
各部門が自部門のことだけを考えて意見を言うのではなく、会社全体でどうすべきか、どうすることが会社全体として効率的なのかを意識し、「部分最適ではなく、全体最適」を念頭に、議論を進められました。
その具体的な事例の一つが、「部品表の取込みをどの部門が担当するか」です。以前は、別システムで作成した部品表データを購買担当の方が取込みされていました。
しかし、設計からの連絡ミスや、購買での取込み漏れが多くあったことから、TECHS導入後は、設計担当の方が部品表の取込みまで行うように運用を変更されました。
設計担当の方に「仕事が増えると感じませんでしたか?」と伺ったところ、「確かに自部門だけを見ればそうですが、会社全体として手配業務を早く確実にするためには設計が取込みをするのが合理的であると納得しました。
TECHSにデータが入れば、後はTECHSが部品表データの手配進捗状況を教えてくれますから」との回答を頂きました。まさに、「部分最適」ではなく、会社としての「全体最適」を意識されての業務変更だったと思います。
また、設計の方がTECHSで原価を確認することでコスト意識も強くなったと、副次的な効果についてもお話しくださいました。
最後に、今回の訪問の中でコーセーエンジニアリング様の強みとして感じたのは、「トップの強烈なリーダーシップと各部門長の調整力」です。
システム構築のうえで、目標に向かって全社で進むことができた組織力こそが、生産管理システム導入成功の秘訣であると感じました。
継続する力
まずは無事に本稼働することが重要ですが、稼働後に新しく決めたルールを徹底することも重要なポイントです。気が付くと元に戻ってしまっている、ということもあったりするものです。
その点、コーセーエンジニアリング様では、「どうあるべきか」をトップが描き、そのためのルールをリーダーが決め、メンバーに周知徹底・運用定着することにも成功されています。
特に運用定着では、運用を見届ける、いわゆる「うるさ方」の存在が重要だと教えてくださいました。見られていないとメンバーは手を抜くかもしれませんが、逆にちゃんと見られていることを知り、更にそれが評価につながると分かれば、メンバーは一生懸命になるものです。
このリーダーの「見届け」こそが「継続する力」に繋がっていることを教えて頂きました。
お客様の現場には、私どもがまだまだ気付けていない、改善のヒントやポイントがたくさんあります。今後も、そういった現場の「生の改善」を教えて頂きながら、皆さまにフィードバックしていきたいと思います。
<紹介工場>
◆コーセーエンジニアリング株式会社
・高圧受配電盤、低圧配電盤の設計製作
・制御回路設計 及び制御盤の設計製作
・計装回路設計 及び計装盤の設計施工
・電気設備工事 及び計装設備工事の設計施工
・電気制御計装に関する現地調査 及び現地改造
・コントロールセンターの設計製作
<生産管理システム発売元>
◆株式会社テクノア