新日鉄住金の軽量化技術に取り組む姿勢から学ぶ
軽量化はキリのない顧客ニーズ。自社製品や自社技術の軽量化で付加価値を高める可能性を探る。
自社の軽量化技術開発の方向性や扱う材料のトレンドを把握して5年先、10年先の見通しを立てる、という話です。
1.軽量化技術
自社のコア技術を深耕させる方向性は明確になっているでしょうか?
イノベーションへ至る技術開発や商品開発は時間がかかります。
時間がかかるだけに、開発の方向性は極めて重要です。
開発スタート時点で見逃した小さなズレは、5年後、10年後、取り返しのつかない大きなロスとなります。
ですから開発の方向性は、顕在的ニーズと潜在的ニーズの両方を睨みながら、現状対比で修正作業し続け、将来の顧客の「コト」に届くことを目指します。
「今」目論んだ開発の方向性が、必ずしも5年先も10年先も正しいとは言えないことに留意します。
こうした、不確実性の高い市場において、今後も確実に要求され、それもキリなく求められ続ける技術課題があります。
それは……、軽量化技術です。
軽量化技術と言えば自動車業界がいの一番に思い浮かびますが、船舶や航空機産業ロボットや工作機械、ウェアラブル機器や携帯端末、携帯機器……。
CO2排出量規制強化、省エネ強化、高齢化など、様々な外部環境の変化に伴って直面する社会問題を解決する技術課題のひとつに軽量化があげられます。
したがって、自動車業界に限らず、多様な市場からの軽量化要求はどんどん高まり、軽量化技術による競争も激化することが予想されます。
自社技術、製品における軽量化技術はどの程度の付加価値を生み出すポテンシャルを持っているのか整理しておきたいです。
2.自動車業界での軽量化技術
自動車業界では世界のCO2排出規制に対応するため軽量化技術の進化が加速しています。
そうした業界の技術動向は今後の軽量化技術を考えるうえで参考になります。
軽量化の取り組みは2段階で考えます。
第一段階 : 従来と同一材質で考える
求められる機能を維持できる鋼で最も軽い構造を設計する。
現行の加工方法を改良、あるいは新たな加工プロセスを考案して、その構造を生産できる製造技術を確立する。
具体的には鋼の薄肉化や熱処理の工夫による材料強度アップ。
従来材質の性質を極限まで引き出します。
究極の加工方法を検討することになります。
ここでの軽量化の水準は現行対比5%~30%程度
第二段階 : 従来と異なる材質も考える
第一段階を卒業して、さらなる軽量化を模索する段階です。
ここでの軽量化の水準は従来対比30%以上。
狙いは半減!!、ドラスティックな成果を目指します。
柱は材料置換です。
鋼 ⇒ アルミ合金 ⇒ マグネ合金 ⇒ 樹脂(ガラス繊維、炭素繊維強化)
まずは、第一段階を極め、引き続いて第二段階へ進むのが望ましい開発の方向性です。
- 第一段階 : 従来と同一材質で考える
- 第二段階 : 従来と異なる材質も考える
取り扱う材料の特性を知るには時間もかかります。
まずは自社のベースとなる材料技術を持つべきです。
自動車部品工場で売上規模数十億円規模の新技術開発プロジェクトに携わっていた時の技術課題が軽量化でした。
従来扱っていた材料を極限まで薄肉化する加工技術の開発でした。
上記の表現では第一段階です。
新聞・雑誌では、自動車業界における多くの軽量化事例が取り上げられています。
米フォード・モーター
同社で最も売れている看板車種ピック・アップトラック「F-150」のボディーにアルミを全面採用し300kg以上の軽量化に成功し燃費向上につながった。
米テスラ
発表後1週間で30万台以上の予約を集めた米テスラモーターズの廉価車種「モデル3」はアルミを多用している。
独BMW
高級セダン「7」シリーズ。
高張力鋼板を炭素繊維強化(CFRP)骨格で補強する新ボディー構造を開発しボディー単体で40kgの軽量化を実現した。
CFRPを組み込んだマルチマテリアルボディーを量産車で実用化したのは、同社が世界初。
高張力鋼板とCFRPの接合は接着剤とリベット。
独Audi社
多目的スポーツ車(SUV)の「Q7」。
ボディーでは、全体の質量の41%にあたる部分にアルミ合金を使用し、強度が求められる骨格部分に熱間プレス鋼板を使用。
素材の使い分けで300kg軽量化。
ダイセル・エボニック
ヘッドライトなどを搭載する大物部品、フロントエンドモジュール。
従来、鋼板と樹脂をボルトで締結していた。
それを、①鋼をアルミ合金に置き換え、さらに②アルミ合金と樹脂との締結を接着剤にして従来対比で20%の軽量化。
アルミ合金を成形してから樹脂と接着するのではなく、アルミ合金と樹脂を接着してから成形する技術。(←これはスゴイ!)
住友ベークライト
独BMW社の2輪車に搭載する排気量650cc水冷1気筒エンジンのシリンダーを覆うシリンダーブロックの一部(ハウジング)をアルミ合金から樹脂へ置換。炭素繊維強化タイプで28%、ガラス繊維強化タイプで16%の軽量化。
住友化学
オイルコントロールバルブをアルミ合金から樹脂へ置換。50%の軽量化と10%のコスト削減。150〜180度の高温度域で使用できる樹脂を開発。(従来は120度が上限だった。)
新日鉄
高張力鋼板は590MPa、980MPa、1180MPaと強度を高め、現在、1470MPaの技術も確立された。
硬くても加工性を高めた材料を開発、加工方法もセットで自動車メーカーを支援する。
(出典:日経ものづくり2016年9月号)
3.新日鉄住金の意気込みで自社技術を極める
自動車の軽量化で目立つのは材料置換です。
そうした事例が多い中で、最後に上げた新日鉄は、コア製品である鋼を極める方針です。
「完成車メーカーの開発担当者が鋼を使うのは難しいと思っている部品でも、構造や工法を工夫すれば、鋼で軽量化が実現できて、コストも安くなるケースがある。
気の利いた提案がどれだけできるのかが大事で、そうしないと鉄は生き残れない。」(新日鉄住金自動車鋼板商品技術室長の水口俊直氏)
(出典:日経ものづくり2016年9月号)
「われわれはまだ鉄の能力を10分の1しか利用できていない。
極限まで鉄のもつ潜在力を引き出す。」(新日鉄住金副社長の高橋健二副社長)
(出典:日本経済新聞2016年8月5日)
軽量化技術の開発対象範囲は、市場に対する自社製品の位置づけ次第です。
自動車メーカーの立場では、材料を置換した上で、その加工技術や接合技術を考える必要があります。
一方、自動車メーカーへ材料や部品を供給する立場であるならば自社で得意とする材料を極めた上で加工技術や接合技術を磨く。
さらに、自社で得意とする材料が、下記の軽量化トレンドのどこに位置付けされているかも、高める付加価値の度合いを知るためには重要な情報です。
鋼 ⇒ アルミ合金 ⇒ マグネ合金 ⇒ 樹脂(ガラス繊維、炭素繊維強化)
軽量化技術開発の方向性を模式的に下記へ示します。
自動車メーカーが、現在→2→3と考えるのに合わせて、部品や素材を供給するメーカーは、現在→1で考えます。
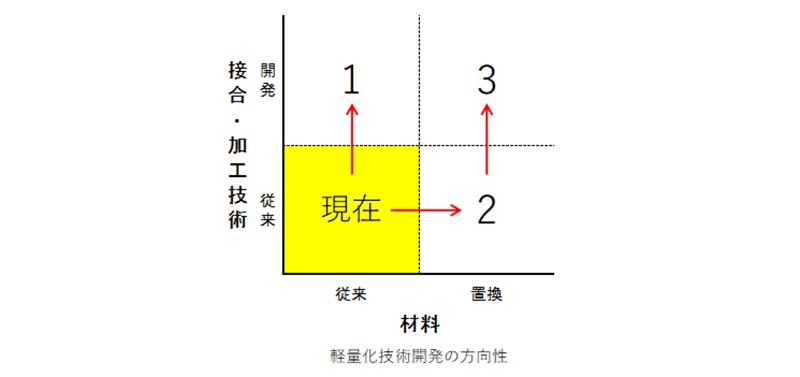
自動車業界にかかわる中小モノづくり企業ならば、現在→1と進むことになるケースが多いでしょう。
軽量化トレンドから考えて、このタイプの軽量化技術開発で汗を一番書いているのは新日鉄住金かもしれません。
なぜなら、軽量化トレンドから見ても決して有利な立場に立っているわけではないからです。
上記の水口氏のコメントにもあるように、「気の利いた提案」が大事になるほど従来技術の延長では真新しさはない……、必死の度合いは他を上回っていると推測されます。
私が新技術開発プロジェクトに携わっていた時の軽量化技術開発では、現在→1でしたが、アルミ合金を扱っていましたので、若干、軽量化トレンドでは、「鋼」よりも前へ行っていました。
新日鉄住金の軽量化技術開発が置かれた立場は、中小モノづくり企業でも参考になることがあるかもしれません。
「コアを極める」という姿勢や考え方においてです。(規模では全く手本にはなりませんが)
こうした軽量化技術へのニーズは自動車業界のみならず、他の業界でも同様です。
工作機械で精度向上を図ろうと思えば、可動部分を構成する部品の軽量化は慣性の点から考えて必要です。
航空機でも従来のリベット止めに代わる摩擦圧接技術が開発されています。
船舶用プロペラで従来の銅合金をCFRPに置換して質量半減を目指している事例(ナカシマプロペラ)もあります。
さらにはウェアラブル機器での軽量化にも多様な要望が出てきそうです。
(出典:日経ものづくり2016年9月号)
軽量化はキリのない顧客ニーズとなりそうです。
自社製品や自社技術の軽量化で付加価値を高める可能性を探ります。
自社の軽量化技術開発の方向性や扱う材料のトレンドを把握して5年先、10年先の見通しを立てます。
そこでは、コア技術を深耕し極める姿勢が大切であると思います。
新日鉄住金の鋼を極めようとする姿勢から学びませんか?
まとめ。
軽量化はキリのない顧客ニーズ。自社製品や自社技術の軽量化で付加価値を高める可能性を探る。
自社の軽量化技術開発の方向性や扱う材料のトレンドを把握して5年先、10年先の見通しを立てる。
株式会社工場経営研究所 「儲かる工場経営」メルマガ ご登録ください。
毎週火曜日配信中。
https://48auto.biz/koujoukeiei/registp.php?pid=3