新たに生み出される付加価値をベン図で見える化する
技術開発では、ベン図をイメージして、既存技術(コア技術)、組み合わせる技術、新たに生み出される付加価値の3領域を明確にする、という話です。
1. トヨタのTNGA
既存技術でも他の既存技術と組み合わせることで新たな付加価値を生み出します。
顧客へ届ける「コト」視点でコア技術の深耕を図ります。
新たな「コト」を生むために、白紙の状態からスタートして、試行錯誤している余裕はありません。
技術で戦う世界はスピード勝負です。先手必勝です。
まず、自社工場が持っている強みに注目です。
ヤマザキマザックは、既存の切削加工技術と摩擦撹拌接合技術を組み合わせました。
摩擦撹拌接合 + 切削加工 = 付加価値。
福井県福井市に本社がある松浦機械製作所は、既存の切削加工技術と金属光造形技術を組み合わせました。
金属光造形(3Dプリンティング) + 切削加工 = 付加価値。
コア技術を深耕、強化して付加価値を生み出すときには、
既存技術 + 既存技術 = 付加価値
既存技術 + サービス = 付加価値
で考えます。
トヨタは、2015年に「TNGA(TOYOTA NEW GLOBAL ARCHITECURE)」を発表しました。
開発の効率化を進めるために、部品、ユニットの共通化を進め、搭載するユニットや配置、ドライビングポジションなどを設計思想に定めたトヨタの新しいクルマ作りの方針です。
この新プラットフォームは2015年に販売された新型プリウスαに搭載されました。
トヨタの強みでありコアの中のコアであるトヨタ生産方式に基づく生産技術や製造技術と欧州発の効率的な設計手法「モジュラー設計」を組み合わせて生み出されました。
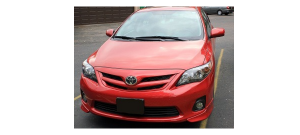
これによって、トヨタでは開発工数を20%以上削減する考えです。
その分、顧客ニーズにより一層合致した付加価値の高いクルマの開発に経営資源を回すことができます。
(出典:『日経ものづくり』2015年3月号)
2. ベン図で技術開発の方向性を見える化する
ベン図で表すと新たな付加価値を生み出す戦略が見える化できます。
(出典:『日経ものづくり』2016年3月号)
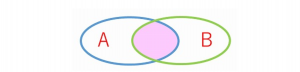
一つの集合(楕円)で付加価値を生み出す原動力、経営資源、外部資源を表現します。
Aは既存技術(コア技術)です。Bに何をもってくるか。
Aと組み合わせて、交わるピンク色の領域でどのような付加価値を生み出すか。
トヨタのAはトヨタ生産方式です。
ジャストインタイムであり、自働化です。
徹底したムダの排除による、利益を生み出す現場です。
Bがモジュラー設計です。
部品の大幅な共通化、開発リソースの削減、開発スピード向上です。
1996年、97年ごろからドイツの自動車メーカーで活用されてきた設計手法で、欧州メーカーに一日の長があります。
両者が交わるピンク部分に「生産と設計の効率化」の付加価値が生まれます。
ここから生み出される経営資源を、将来の付加価値を生み出すために投入する。
豊田社長が繰り返し語っている「もっといいクルマ」を実現させる具体的な方法がTNGAです。
トヨタの2016年3月期の決算は売上高28兆4031億円、営業利益2兆8539億円で過去最高益でした。
営業利益率10%の稼ぐ力を、ますます磨こうとしています。
コア技術から確実に成果(利益)を生み出そうとする姿勢がハッキリしています。
会社の規模に関わらず現場には必ず強みがあります。
コア技術をまず見極めます。
これがスタートで、ベン図のAの見極めです。
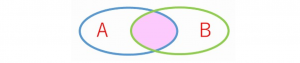
そしてBに何を入れるかです。
- 自社にはない他社の強み、新たな技術
- 自社で提供できる新たなサービス
- 人財活用の最大化を目指した新たな人財活性化策
- 自社内の異なる分野にある要素技術
Aと組み合わせることで「化学変化」を起こせるものを持ってきます。
インダストリー4.0やインダストリアル・インターネットでは、Bに情報通信技術(ICT)や人工知能(AI)が入ります。
この場合、Aが自動車なら、AIとの組み合わせで自動運転です。また、Aが工場の生産設備なら、ICTとでスマート化です。
特に後者は中小製造業でも大いに活用するべき組み合わせです。
ピンク色の領域でどのような付加価値を生み出しますか?
あるいは、ピンク色の領域に、新たにお客様に届ける「コト」を設定してから、Bの領域にもってくるべき既存の原動力、経営資源、外部資源を考えます。
技術開発では3つのことを明確にする必要があることに気が付きます。
- Aの既存技術(コア技術)
- Bの既存の原動力、経営資源、外部資源
- ピンク色の領域にあたる新たな付加価値(コト)
3. 技術を単独に深掘りしても行き詰まる
薄利多売で儲ける時代は終わりました。
請負型の事業形態を脱却して、自社ブランドを有して自立型の事業形態を目指すならば、自社のコア技術の深掘りのみに依存した技術開発はやめます。
お客様に喜んでいただくことはできます。が、革新的な技術開発からは遠いです。
技術を単独に深掘りしても、既存技術に延長線を引いているだけ。
そのうち同業他社も時間をかければ追いついてきます。
競争が激しくなり、コモディティー化が進み、早晩、価格競争に陥ることが目に見えているからです。
自前の技術にこだわった、自社のコア技術のみの深耕では、ピンク色の領域を生み出すのは難しいです。
シャープの事例から理解できます。自前の液晶技術だけを磨き上げても韓国、台湾、中国のメーカーに勝てなかった。
コア技術を見据えて、ピンク色の領域で生む新たなコトを考えます。
まとめ
技術開発では、ベン図をイメージして、既存技術(コア技術)、組み合わせる技術、新たに生み出さる付加価値の3領域を明確にする。