提案制度・評価が部下をダメにする会社
提案制度の運用は、企業の従業員の活性化だけでなく、品質、原価、納期など経営改善要件に大きく作用を及ぼします。
このため、提案制度を活用する企業が多く、中でも改善というのは企業にとっても従業員にとっても、都合の良い方式です。
ですが、目につく改善点が少なくなってくるにつけ、“提案”も“低案”の文字で表されるように低下し、やがては、“停案”という停止の道を歩むことがあります。
それならと、強制的に提案件数の割当を各職場へし始めると、もうダメです。
制度は残るが、提案の向上は一向に果たせないようになるからです。
このような事態の多くは、戦略や管理者側の対応のまずさが関係するのですが、このような悩みを事前に察知したU社からYさんに相談が来た時の話を、今回は紹介することにします。
U社に対するYさんの対応例
YさんがU社に訪問した時、トップの方から、
「提案制度を上手に運用しないと、大変な被害感が現場に残ってしまうことになる」
という話と、
「このところ現場の活性化が進まなくて困っています。
何か良い手はないでしょうか?」
という相談がなされました。
これに対しYさんは、
「活性化ですか、貴社は小集団活動も活発のようですし、自動化も進んできておられますので、活性化という言葉は当てはまらないように思われますが?」
「傍目にはそのように見えるようですが、外部へ発表するのは優秀な事例でして、実情は改善が減ってきて困っています。
何か良い対策はないでしょうか?」
「まず、経営的な重要課題を紹介していただけませんか?」
「そうですな、例えばクレ-ム対策などですか?」
「ハイ!」
「それなら先週もありました。困っています。
先週、製品Aの基準が○○となっているのに量を間違えて、完全なポカミスが発生しました」
「それをテーマに具体的な対策を討論していきたいと思いますが、いかがでしょうか?」
「お願いします。でも、人が関与するポカミス対策は大変でしょう。
対策書は出すのですが、人は誤りを犯すものです。
防ぎようがないように思いますが、何か良い手があるのですか?
組み立て産業では成功したというのを時々見るのですが、当社のような装置産業では手がないように思います。
当社の仕事は特殊なので、他社の例があまり参考にならないのです」
「そうですか、私が貴社の良策を持っているというわけではないのですが、貴社のような装置産業では、次のように手を打つことが打開策発掘に良いのではないかと思います。
なお、人が犯すポカミスの防止には、管理者の姿勢がまず大切です。
不良ゼロは達成可能である! という信念です。
管理者の方々が“人はミスを犯すもの”と思ってしまったら、もうダメです。
“ヒューマン・エラーをゼロ化する技術を何としても見つける!”というような思想を持つことが大切です」
「でも、不良ゼロは不可能でしょ?」
「いや、ゼロは不可能かも知れませんが、不良ゼロへアプローチする行動は不可能ではありません。
ゼロは努力の結果ですから、努力しないでゼロ化は不可能! と決めつける行動はいけません。
このことは、私が言ったのではなくて、不良ゼロを実現したZDの考え方をもとにしています」
不良ゼロを実現したZDとは
「ZD活動は、1960年代に米国でミサイル製造の問題対策と共に生まれた手法です。
企業名はマーチン社、先にお話しされた組み立て産業ではありますが、ここで取り組んだ内容は、装置産業でも役立つアプローチです。
要点は下図のようになります。
では、多少、説明を加えることにします」
▼米国マーチン社におけるZD運動
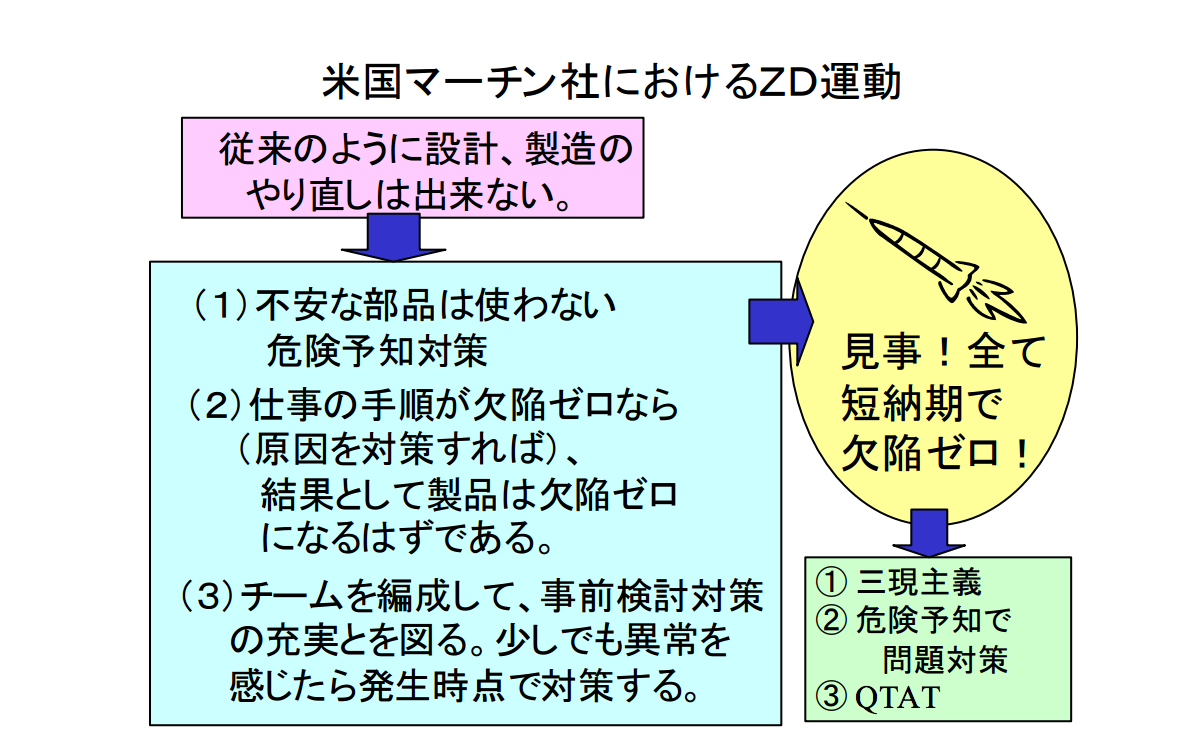
「1961年当時、米・旧ソ連の冷戦状態でした。
この時、軍事均衡が破れると第三次世界大戦になる危険がありました。
その理由は、既に旧ソ連は敗戦で確保したドイツの技術者達が、大陸間弾道弾というミサイルを実現していたのですが、同じように米国が確保したドイツ技術者の図面はあったのですが、製品化ができなかったからです。
そこで、緊急に米・国防省は米国の各社に製作を依頼しました。
依頼内容は短納期、かつ欠陥ゼロでつくるというものでした。
当然、各社は平和協力したい。
ですが、この要求に応じる力が無い。
そこで、各社が断る中、米国の国防省はマーチン社を指名しました。
当時、品質管理部長を担当していたハルピン氏は大変に悩みました。
そして、“どうしても、やらなければならない!
そのためには、今までのようなやり直し生産方式、すなわち問題が起きてから対策するのではダメだ!”
と発想を変えました。
そこで、この事情を従業員の方々に話し、欠陥ゼロの取り組みをしていただいた結果、全く欠陥なしの製品が短期間で出来上がりました。
これがZD活動の誕生です。
そこには、技術的に3つの対策が光っています。
ヒヤット30の1件が不良として顕在化するハインリッヒの法則はまだ無かったのですが、どうもハルピン氏の頭の中にはこの考えがあったようです。
彼は以下の3つのルールを決めました。
①不安な部品は使わない。
②手順が原因で不良が発生するならば、不良が出ない手順を現場関係者で事前に決めておき、順守する。
③ヒヤット段階で、もし異常になりそうな製品の兆しを見つけたら、発生元に現物を持参(フィードバック)して、不安な部品使用によるものか、標準化の中に残余の問題があるのか、標準化は正しいが、守り方に欠陥があるのかをはっきりさせる。
ポカミスが発生するのを待つのではなく、ヒヤット段階の問題を撲滅することを現場・現物で早急に行ったのです。
後にこの手法はQTAT(Quick Turn Around Time)と名が付けられましたが、以上、ここまでの対策をひとつの現場管理技術として進めました。
その結果、最初に製作したミサイルは見事欠陥ゼロでした。
1つの製品ならマグレです、しかしその後、更に3週間の期間短縮要求をされたにもかかわらず、次々と製作するミサイルの欠陥はゼロ記録を更新しました」
「あれは精神論ではないのですか?」
「当時、確かにその面はありました。
しかし、大切な点は、
“仕事の手順の中に欠陥がなければ、不良は絶対に発生しない!
たとえ部品の不良があっても、QTATの利用と共に、それを作業手順の中でチェックすれば良い!”
というように対処した点です。
ZDマネジメントの良さがありました。
事前検討段階で不良を防ぐ手段を具体化させたのです。
過去、小集団活動や提案活動は、“事後的に統計データ解析で不良問題を解析して、何とか不良発生を食い止めた”というものでした。
しかし、この方式では火事が出るのを待って火消しや火元の対策を進めています。
ZDは事前検討で不良を防ぐ対策ですから、それとは全く違います。
事後対策のまずい点は、現場の方々がこのような行動をしていると、指導者である上司が認めている点です」
「いや、大反省です。
正直言って、我が社の提案活動は火事を起こしてからの対策であり、予防重点では無かったからです」
「そうですか!
過去、多くの企業が実施してきた不良統計をまとめてから討論をするTQCは、QCの本質を誤って運用しています。
ですが、ZDは不良やトラブルを未然に防ぐ活動である点が違います。
もし、事後に起きた問題がゼロなら統計を使う必要は全く無いです。
これは1994年型のISO9001・規定4.20で“統計の扱いを明確にせよ!”が注意しています。
結果が出てから問題をまとめるやり方はZD思想や本来のQCとは全く別物です。
しかし、“品質改善の活動は論理的で、ビジブルでなければいけない”と考えた方がおられたようです。
また、ZDに対しても疑いの目で見られていました。
そこで、安易ですが、素人向きの方式をZDに結びつけた結果、『ZD=統計処理解析』として、研修会や発表会を開催していました。
もっとも、“ZD自体、QCに対応する具体的な手段がなかったので、精神論だ!”という評価に対応できなかった責任は誰かにあったかもしれません。
しかし、それは過去のことです。
私たちは、現在このような歴史を知っていますし、活用やQC手法の間違った活用が生んだ『死亡診断書的活用』を知っています。
たとえ、問題を事後で解決する手段であっても、今はQCストーリーという、問題解決アプローチを駆使して『原因の除去』をすべきです。
これは是正処置=事後対策、したがって、問題が起きそうな予備軍段階、しかもヒヤットの発生時点で問題をとらえて対策する方式です。
ですが、残念ながらZDとは事前検討と事後処理の差です」
「そう考えると、マーチン社は組み立て産業ですが、我が社のような装置産業でも、ZDの考えが利用できそうだ!」
「そこです。
御社では既に安全面では長期に渡ってケガはゼロです。
このやり方をそのまま品質に転用すれば、ポカミス・ゼロ化はできると思います」
「なるほど、対象は違うが確かに危険予知の手法を品質面に応用すれば良いだけだ!」
「ぜひ、お願いします」
ということでU社はY氏の話を聞き、活動を変えることになりました。
Yさんの追加支援の要点
また、その後、Yさんの支援が追加されたのすが、その要点は次のようなものでした。
1.担当責任基を決める
(1)不良を出したら、本人の給与に関与するような責任体制をつくる。
(2)不良を出したら、発生基の担当者が顧客のクレ-ムを聞き、対策案づくりに参画する。
(3)ポカミス発生の動機的な原因を探り防御策をつくる。疲れ、家庭の不安……による集中心の欠如も対策に含める。
2.標準化手順をつくり守る仕組み
指示-行動(手順をフォロ-する)-結果の中に含まれる問題も対象に含める。
3.ダブルチェック・システムの活用によりヒヤット問題の発掘とQTAT対策を図る
4.ポカヨケ装置の利用を進める
5.設備自動化の工夫を図る
「以上、このように不良対策は大きく5つの項目に分けられます。
これは安全、設備故障、エコ対策や情報管理などにそのまま適用できます。
では、説明します。
この項目は、上から順に費用が掛からない対策法を並べたものです。
番号が若い順に再発の心配が残ります。
これに対して、下の項目ほど一般にはお金と時間が掛かるが確実な対策です」
「なるほど、もう少し詳しく、その5項目の解説をお願いします」
「では、もう少し詳しく説明します。
1番目ですが、こういう話をよく聞きます。
製造工程を3工程、検査工程まで通過し、各々の工程で不良をチェックしているはずなのに、不良品が外部へ流出する! といったものです。
ですが、全員で仲良く検査! という思想を実践すると、具体的に誰が何を見るか、またその責任はどうするかがわかりません。
したがって、“皆で見る”というムード的な取り決めが、結果として誰も何も見ていなかったということになりかねず、当然見つけるはずの不良を見逃すことになります。
『もたれ合い』という現象です。
確かに、“全員で監視する”という取り決めは、見た目は良いシステムです。
ですが、実際には何も検査をしていない方式になるのです。
次の図はリンゲルマン効果ですが、このような問題発生を示した理論です」
▼リンゲルマン効果
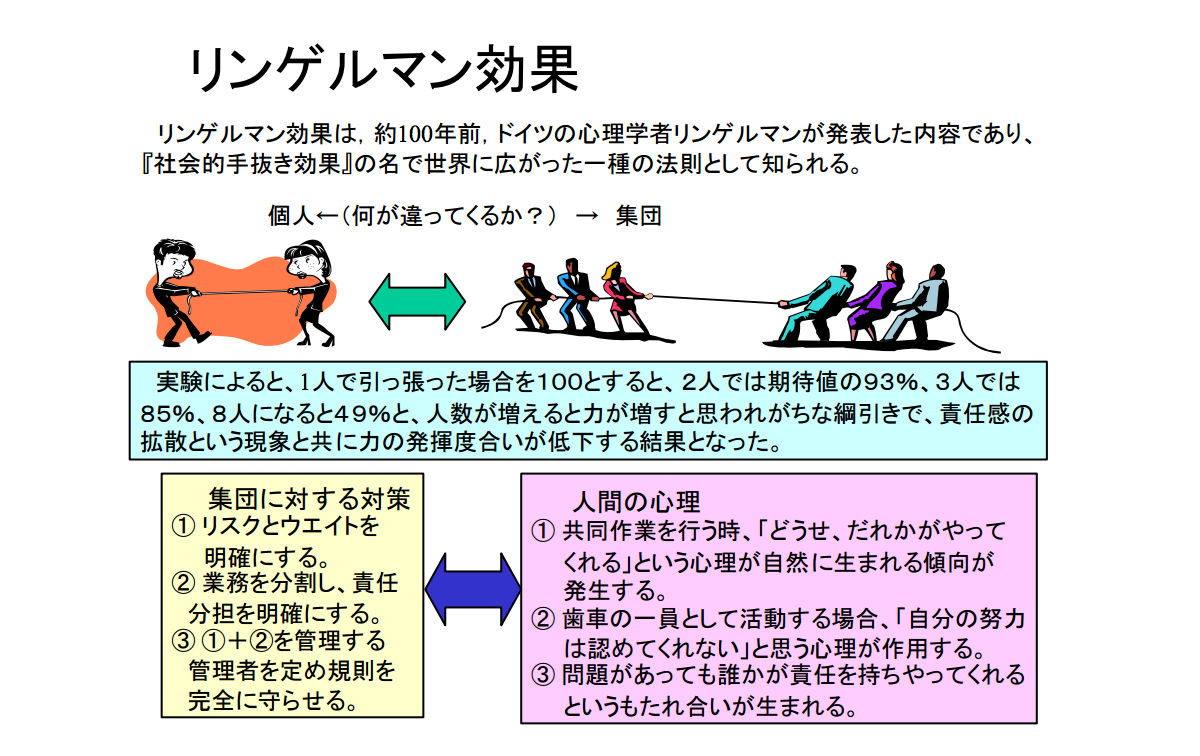
「したがって、先に説明したように、このような場合には検査項目に従って責任体制を決めることが重要です。
給与に響くと真剣になる! という原則があります。
逆に、仕事を一生懸命やって不良を出さない方や、担当工程からもれた不良を他の工程で発見された方は、提案と同じように賞をいただく、発見賞や年間で不良流出のない方を褒めるシステムも、品質管理上の重要な対策です。
これは、仕事そのものを通した問題発見~改善法ですが、維持の面で効果をあげた方々の優遇も提案活動と同じくらいに大切です。
以上が『ボ-ナス・ペナルテイ制度』の実務的な運用法です。
性善説だけでは取り扱えないポカミスはこのような方式で対処すべきです」
「なるほど!」
「次に、ものをつくる方の品質に対する意識・製造責任を、ものづくりに直接あたる作業者の方々一人一人が身につける対策について解説します。
こういったことは口でいくら説明してもダメです。
不良発生の時に不良を出した現場関係者に、顧客のもとへ行っていただきます。
具体的には、製品を直接作った方、作業をしている担当者を、品質管理や製造課長と共に、顧客のところへ訪問していただく処置です。
この対処は、毎回ではなくても、特に厳しい不良の際には、当然のこととして実施すべきです。
部下の方々にとって、上司からの注意は慣れっこになっています。
しかし、直接に受ける顧客からの厳しい叱咤はそれとは全然違います。
注文が二度と来ない恐れを感じる、という製造上の責任だけでなく、企業イメージの失墜が作業者個人の行動に大きく関与していることに対し、改めて強い印象と共に頭に残るからです」
「上司からの説明では駄目ですか?」
「まず、弱い! と考えてください。
私の経験ですが、昔、ある企業で改善班という組織をつくったことがありました。
この方々は現場の改善専門業務を3ヶ月ほど経験していただくために、現場から事務所のプロジェクト室に一時的に集まった方々です。
ですが、このような時に、クレームでお客様が工場を訪問されました。
工場長が、先のプロジェクト室の隣で、クレームのお叱りを受けたのです。
工場長という偉い方が、顧客から叱られ、タジタジになった。
しかも、その製品は改善班の方が先に生産した製品だったのです。
工場長が叱られる様子は隣の部屋まで聞こえてきたのですが、この担当者を含めて3名の改善班の方々は涙を堪えてこの話を聞いていました。
このことを、私は後で聞いたのですが、
“不良を出すことで、どのようにお客様に迷惑を掛け、工場が影響を受けるかが痛いほど身にしみた!
先に、上司から話を聞いてはいましたが、あれほどまでに凄まじいとは知らなかった!”
と改善班の皆様は痛感しました。
また、彼らの話は工場内に火の勢いで広がりました。
当然のことながら、工場の品質意識が急激に高まりました。
それまで、工場長だけではなく課長からも不良対策の重要性は聞いていました。
ですが、顧客からの直接の声、
“不良を出せば、あのように偉い工場長までが顧客からこっぴどくお叱りを受けることになる!
このようなことは、口でいくら話をしても現場で直接ものづくりをする方々には伝わらないことを、私たちは改めて知った“
というわけです。
このため、私は、先に紹介した5項目を定め、皆と共に早急に不良対策を進めました。
また、提案は不良対策の前のヒヤットの発見~対策に集中しました。
当然、これで不良は大きく減りました。
なお、この対策以降、現場の方々が顧客のところへ同行することは全くなくなりました。
私は品質改善・技術的対策が進んだ背景に、現場でものづくりに直接当たる方々の品質意識の高まりがあったように思います」
「勉強になるご体験談です。
我々が制度や教育、指示や標準化をどんなに進めてもできないことをやる!
製造責任の意識の大切さを改めて意識しました」
「管理者の方々の一部には、先に話したように、ポカミスに対して、“人間である以上は仕方ない”と考える向きがあります。
しかし、ポカミスが起きる要因がわかっていて、作業する方々が手を打つことができれば、これは素晴らしいことではないか? と思います。
このようなことを言うのにはわけがあります。
先に紹介させていただいたZDの取り組みがあるからです。
先のお話は、作業者自身の製品責任意識ですが、ZDには、もうひとつの運用面の工夫がありました。
歴史的には過去のお話ですが、不良発生の要因の事前察知対策です。
直接モノづくりに携わる作業者の方々がチームを編成して、自主的に品質管理を行うという品質保証システムです。
ここでは、工程内で品質を保証する。
後工程はお客様の考えで、品質をダブル・チェックするという運用です。
この方式を聞くと、手が掛かるように思えます。
しかし、手を掛けずに行う工夫をZDの思想で考案していったのです。
これは、後工程の方が、作業に着手する前に、前の方の不具合の有無をチェックする方式ですが、短時間で行う工夫があった点がZDの運用の妙味でした。
ただし、後工程の方々が注意をする。
前工程の方が仲間に注意されたように思うかもしれません。
そうなると人間関係の上で問題となることがあります。
したがって、ここに、この手法を運用する目的と運営に多くの工夫が必要になります。
ひとつは顧客志向の思想です。
また、人を責めるのではなく、手順を責めるという考え方が重要です。
なお、この方式が正しく理解され、運用が円滑になされていくためには、現場管理者が現場に常に思想を伝えることが重要になります。
“人がミスを犯す、このことは、あなた以外も同じだ。
そうなると、失敗したあなたがその原因や理由を最も知る方だから、ぜひ、主役になり、ポカミスが起きない手を考えてほしい。
あなたが、問題を起こさない技術手段を見つける研究が成功すれば、他の方の教材や標準化作成のもとになる!”
と説得をします。
この方法は、多くの企業で採用されてきました。
実績のある、お金の掛からない方法です。
このため、今は人のチーム・ワークを強くし、不良を発生時点でとらえ、対策する方式として活用されています」
「なるほど、罪を憎んで人を憎まずという言葉はそのように運用するのですか!」
「そうです。
しかし、技術革新が急速に進展する時代においては、いつまでも、先の1から3の方法だけに頼っているというのは問題があるように思います。
もし、技術的な対策が取れるのであれば、その対策に移っていくことも大切です。
気(神経)を遣って生産することから人が解放されることは、人を創造的な仕事へ導きます。
このことは金で換算できないです。
話は違いますが、仕事の安全性を高める対策、FAXやEメール、携帯電話のように連絡をする道具を購入するメリット計算はどのようにするのでしょうか?
このように、機械化を進め、表面的にはメリットは少ないが、技術的に可能、波及効果や現状の現場環境などを考えた場合、品質対策面で自動化を進める環境整備が目に見えない効果となって出てきます。
道具の改善や設備の設置が仕事を楽にするのです。
安全対策や情報管理や連絡面で役立ちます。
ただし、当然この用件に大金を掛けたり、全く見通しのない投資を要求したりしているのではありません。
ですが、このような対策も時には重要です。
この対策の効果はすぐに出なくても、アイデアや情報だけは常に探っておくのです」
「先の不良対策の4と5ですね?」
「そうです」
「このように品質問題の対策を聞いていくだけで、多くの改善提案が生まれるように思います」
「なるほど!」
「では、ご質問の本筋であった、提案の活性化対策についてコメントをしたいと思います。
教育を受けたり、職場間競争で行ったり、グル-プ討論など、職制の改善環境づくりも大切ですが、提案は提出者の意思に関与しています」
提案を活発化させる条件
普通、提案が活発になされるには次のような条件が必要です。
1、提案の判定が早く提出者にフィードバックされる方式を取っている(提案書提出者に上司の感謝の念が伝わり、指導もある点を含めて)。
2、実現の約束と評価を受けた内容の実施が早い。
3、提案賞金と提案の評価が本人も納得いくものである。
以上の項目の内、1と2は貴社ではすでに対策済みかと思います。
そこで、残った3番目について話を進めたいと思います。
提案に対して、提案を出す側はどのように考えているか? ということです。
次に示す要件は、提案を出す側に対して、管理者が注意すべき点です」
提案を評価するにあたり注意すべき点
1、現場関係者が提案する動機のひとつに、賞金を狙ってきている、ということを忘れないでほしい。
2、コメントはまず、提案=要求の評価、実施の是非を前提にする。
3、現場管理者は点数をあげるためのポイントを教育のチャンスと考えて、出てきた提案を題材に指導する。
「最初の賞金ですが、お金で提案を奨励するのは現場だけではありません。
技術者の特許提出も同じだと思います。
良いアイデアを権利として会社に売る取り決めが、契約書と共に交付されます。
この契約で特許権が会社に移るわけですが、権利発生と共に評価がなされ、企業への貢献度の高さに応じて褒賞金が毎年払われます。
仕事をしながら、給与やボーナスとは別にお金が貰えるのは、技術者には大きな励みとなります。
開発した技術が企業や社会のお役に立っているのだから当然の対処です。
現場の改善提案の評価も同じです。
提案したことに対して正しい評価を受ける。
このことは、企業への貢献度を示す行為(感謝)ですし、ご本人の努力の結果を認めています。
グループで提案しても同じです。
仲間で話をする時に、大きな歴史的な取り組みと成果が金額と共に記録されるから、グループ活動の価値があります。
このことは、同時に企業の他のグループに比較して実力の高さを示す結果になります。
同時に、提案した方、グループの方々の誇りと将来の士気に大きく関与します。
したがって、評価は早くすべきです。
正当な評価を早く行うことが、提案活性化に大きく関与してくるからです。
提案には評価と共に、上司がコメントを書きます。
このコメントが大切なのです。
コメントを提案者は厳しく見ています。
コメントを書く上司は、この面では部下の方が試験官に当たるのだと思って記載すべきです。
また、これはそのまま管理者の能力を示し、この良否と活動の熱心さが、その管理者が受け持つ現場提案の差になります。
したがって、現場管理者の方々が提案の指導技術を管理~部下育成技術のひとつとして研究~錬磨すべきです」
「なるほど!
では、実例で教えていただいた方が良いので、すぐサンプルを持ってくるので、コメントの書き方をご紹介願えないでしょうか?」
「はい!
もし、皆様が私のコメントを聞かれてご質問があったり、違うご意見があったりすれば、おっしゃってください。
私がコメントをするということは、私が皆様に試験を受けているということです。
決して、教わっているという精神で話を聞かないようにお願い致します」
「ハイ! 早速」
「先にお話したように、提案に対するコメントは、私たちが部下に試験を受けているようなものです。
すでに、皆様は日常で多くのことを考え、行動されてきた経緯を持つからです。
したがって、補足する分野はほとんどないのが実態です。
相手のためになるコメントをどの程度私の方から提供できるかが勝負です」
「企業支援の商売も厳しいですね?」
「そう思います。
お金をいただいているから言うわけではありませんが、当たり前の、知っていることをお話するだけでは、時間とお金がお客様のムダになるからです。
もっとも、ご自身がやってきたことの正否の確認だけにコンサルタントを利用する方もおられますが、そのようなケ-スは産業界の5%位の企業だと思います。
さて、事例が届いたところでコメントの書き方に解説を加えたいと思います。
これは、5Sという整理・整頓ですね?」
「ハイ!」
「よく書かれています。
整頓のために棚を改造し、作業性を高めたことが明確に記載されているからです。レベルが高いです。
日頃の上司のご指導が反映されています」
「ありがとうございます」
「しかし、コメントの書き方にもうひとつ工夫されると良いのではないでしょうか?
“大変に良い見方と改善です。
このようなものの見方で他の準備作業に関してもぜひ見直しをしてください”
となっています」
「ハイ!」
「少し文学的です。
初段はこのようなものでも良いかもしれません。
しかし、貴社のように企業改善の目的をハッキリと定めて活動されている場合には、これではまだ不足、と見るべきです」
「それは?」
「では、具体的に説明します。
間違っていたら意見をお願いします。
私の考え方を紹介し、討論を戦わせたいと思うからです。
まず、先に紹介させていただいた“賞金を相手は狙ってきていることを忘れないでほしい”というルールに照らしてみましょう。
この改善では毎回5mを200回程度歩く手間がゼロになるようですね」
「その程度に見積もれます」
「そこです、改善は小さいが、大切な点をついています。
評価はCです。
これについて異論はありませんが、まず、この定量的な数値と共に、この職場で上司が示している5Sの方針の関連を説明し、Cという評価基準に上司として意思決定した理由を示すべきです。
たとえば、
『5m×200回は1日1,000×0.3秒=300秒/日=5分/日の改善である』
ということをコメントに書くべきです。
さらに、これに加えて質的な効果を伝えます。
貴社では『0.1%×25日×12ヶ月=30%』の大きな改善になるので、社内の賞金の基準から見てCとします。
ですが、Cといえどもこのような小さな改善が大きな生産性向上につながるので、この見直しが必要であることを記載されても良いのではないでしょうか?
先の計算ですが、『5分/日は年間22日/月×12ヶ月=22時間』という膨大な数値になり、これを教える記載、すなわちコメントでこのように書くことが、小さい改善の積み重ねの大きさを提案者に認識願うことになります」
「なるほど、納得です」
「加えて、コメントはまず、提案=要求の評価、実施の是非を問うてきています。
この案が良いのであれば、いつまでに誰がやるべきか? に答えを出すよう指導されることをお勧めします。
ですが、この案は実施されているのではないでしょうか?」
「ハイ、実施済みです」
「それなら、実施の速さに対して褒めることが重要です。
自分の職場を自ら改善した点です。
そして、標準化を示唆すべきです」
「そうか!改善には歯止めが必要だからか!」
「そうです。
提案の実施で効率良い仕事になったのですから、この面のサゼッションが大切です。
次に、更に点数をあげるためのポイントを指導という形で記載してあげることが大切です。
この場合、
“他の準備作業に関する内容も是非見直しをしてください”
と書かれているのをもう少し具体的にして、テーマ発掘を促すことが大切なように思います。
先程、“文学的な表現はいけない!”と言いましたが、気持ちの面ではOKです。
上司の気持ちがこの表現には言外に含まれています。
しかし、それだけでは不十分だと思うわけです。
この表現にもう少し具体的な言葉が必要です。
次の行動につながって、しかも次の提案が出せるよう促す記載が必要です。
先程この職場を拝見しましたが、事務処理関係の書類、治工具や計測機器の配置は作業しやすいでしょうか?」
「まだ改善の余地があります」
「それならコメントが書けます。
その内容は指摘ではなく、自らこの面に関心を持っていただくため、
“このアプローチは仕事の準備に関する研修を実現したモデルです。
お手本としたいと思います。
さらにこの方法を広げ、職場のモデルとして……”
と、先の対象を暗示する記載方式をお勧めしたいと思います。
このようなサゼッションは提案用紙に追加の用紙をつけても構いません。
このような対応で、コメントを貰った方が、新しい対象にアイデアを考え、試し、その結果として出来上がる。
次の提案を書類としてまとめ、提示していただくことになるからです。
このような処置には手間が掛かります。
したがって、全てにこのような方法でコメントしなさい、というのではありません。
あなたの課の重点部門に限って、しかも対象者のバランスを見てコメントをするのです。
同じCでも、数で提案者の方が賞金を稼いでいただく方式です。
また、別なコメントとしては、設備の清掃・点検といった新たなテ-マへ発想を広げていただくサゼッションも一つの方向です。
提案を仲介に、日々の現場指導を提案システムという題材を用いて、通信教育の添削的な内容に利用していく対処です。
現場作業をされる方々が、日々の生産以外にじっくりと一人でものを考え、提案書にまとめる時間は大切な自己練磨の場です。
そして、ご指導された歴史がご本人に残る。
このことを知って行動することが上司の“人材育成”を意味するように思います。
提案書はこのように位置づけると、この提案者の方の活動が今までと変わってくるのではないでしょうか?」
「なるほどね! そのような発想は確かに欠けていました。
対応を考えたいと思います」
「要は結果を活かし指導されることであり、提案の評価だけに追われないことが大切です。
いたずらに件数競争を進めるより、仕事をしながら改善を考える。
考えて良くしたことを提案する。
提案すれば、上司達から勉強になるコメントが返ってくる。
このような対応を実施すれば、提案件数も質も向上していきます。
企業には多くの改善が必要なことは事実ですから、提案の活性化といわなくても、テーマはたくさんあります。
どのように作業者の方々が気づき、改善に参画していただけるか? という提案マネジメントの適用こそが大切ではないでしょうか?」
「そうですね!
形式的な提案制度より、現在の制度の中身充実の大切さがよくわかりました。
本日は、ありがとうございました」
コメント
提案制度は各社が運用していて、歴史のあるシステムです。
このシステムは現場改善ムードの活性化だけでなく、現場における品質・原価・納期の改善に大きな役割を果たしてきました。
これからも日本の現場・経営改善に欠かせない重要なシステムです。
このため、提案の位置づけは下図とされてきました。
▼改善=良く改めることの必要性
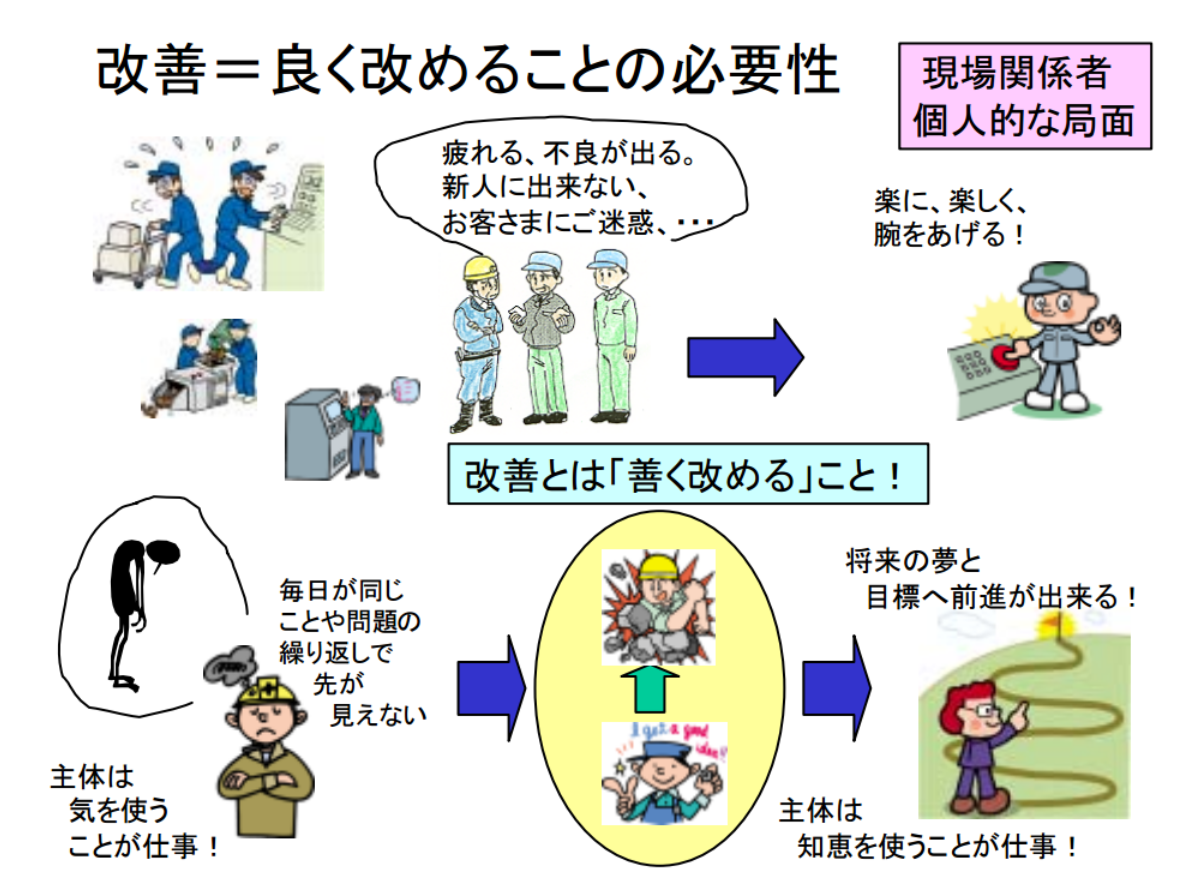
今回のYさんがU社を指導された内容のポイントは、この話にあるように、人材育成、ものの見方を育成するために重要なコミュニケーション・レターとしての意義を示した点にあります。
Yさんは実際に現場を持ち、提案をもとに部下育成を実践された方なので、実務的な指導をされていました。
この対応、すなわちコミュニケーションが形式的・強制的になると、従業員は“意味のないことをやっても仕方ない!”といって止めてしまいます。
提案作成は、多くの場合、仕事時間の外で自主的に行う活動です。
また、提案書は、一般に書くことを不得意とする現場で活動する方々にとっては苦痛を伴います。
特に、評価に値しない提案書の作成努力はムダになることを知っています。
昔から提案の多い職場には、必ず良い上司の熱心な活動があります。
制度に関係なく、提案を現場活動の重要な要素と考えて活動された方々です。
当然、改善活動は同じことの繰り返しではやることが尽き、マンネリ化します。
このようなことから、提案の運用・テーマ発掘の切り口に対して、管理者は戦略を立て、情報を集めていく努力が必要です。
この玉が尽きた時、提案は低下し、提案システムは名ばかりのものとなるからです。
「提案は出す方の努力と、その方々を指導する上司の行動が反映されたものである!」と言われるのは、こういうことです。
当然のことながら、今回の話は提案活性化の対策の一部であり、提案活性化対策の全てではないですが、この話が提案の活性化と人材育成が各社で育つきっかけになることを願う次第です。