技術開発は技術課題を分割して要素技術を探索する
技術開発では「解決すべき技術課題を明確に設定した後、課題を分割して適用すべき要素技術を探索する」という手法や手順を意識する、という話です。
1. 軽量化は今後、ますます求められる技術課題
軽量化は今後、ますます求められる技術課題です。
家電製品のように人が携帯して直接に取り扱う製品の軽量化は、高齢化が進む市場においてニーズは確実に高まります。
例えば……、掃除機は軽い方がイイです。
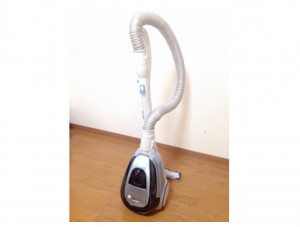
カメラのようにある程度の重量感もないと売れないという製品もあるようですが高齢化と共に軽い製品が好まれる傾向が強まるのは間違いないです。
家電の他にも、自転車、乳母車、介護支援製品……なども頭に浮かびます。
また、クルマ、航空機、列車等の輸送製品はエネルギー効率や環境保護の観点から軽量化が強く求められる分野であることは間違いないです。
さて、軽量化を実現させる代表的な手段は「材料置換」です。
鋼をアルミニウム合金へ置き換えるのが代表的な軽量化手法。
強度部材でなければ樹脂材料の活用というのもありますが、軽量化の話題の中心は強度部材です。
今後は、アルミニウム合金を基準に、さらなる軽量化を求めて注目されているのがマグネシウム合金と炭素繊維強化樹脂(CFRP)です。
技術的な問題、経済的な問題の障壁が高く、広く使われる機会の少ない材料でもありました。
それが、技術開発が進む中、具体的な製品への適用が広がっています。
イイのは分かっているけども、実用化を阻む問題があって使えなかった……。
その問題を技術開発によって解決し実用化の扉を開く……。
こうしたブレークスルーは、モノづくりの醍醐味です。
モノづくりを生業にしている我々にとって技術のイノベーションは欠かせません。
そこで、技術開発、製品開発を進める手法も磨き続けます。
技術開発、製品開発を思いつきや勘、度胸で進める時代は終わりです。
手法や方法論を持つことが必要です。
中小モノづくり工場でも同様です。
中小製造業では限られた経営資源で「確実に」成果を出すことが求められます。
やりました、失敗しました、ということを許してくれる状況にある企業は少ないです。
加えて、技術で勝負する世界での技術展開のスピードが、ますます速くなっているからです。
2. 技術開発でブレークスルー
マグネシウム合金も炭素繊維強化樹脂(CFRP)も技術開発でのブレークスルーがあったからこそ製品への採用が広まっています。
直面している技術課題を分析し、ブレークスルーのためのテーマを設定して新たな技術の実用化を狙います。
2-1 マグネシウム合金
マグネシウムは実用金属の中で最も軽く、比強度や切削性に優れた金属です。
金属であり、リサイクル性にも優れているのでアルミニウム合金に続いて、採用が広まりそうなものですが、燃えやすくて扱いにくいという難点がありました。
マグネシウムは活性であり、切削で生じた切粉が非常に燃えやすく微粉では急激に反応して爆発の危険があります。
また切粉を水中に投入すると水素が発生するので、発火時に水で消火を試みる水素爆発が起きます。
ですから、現場での扱いには細心の注意を要します。
市販のマグネシウム合金(AZ31)は580度で燃えます。
それに対してカルシウムを1〜2wt%添加したものが難燃性マグネシウム合金としても従来からあり、発火温度は810度で強度は従来合金と同等レベル。
ただし、この水準では実製品への展開は限られていました。
燃えやすいという技術課題を解決するには発火温度を上げるしかありません。
ここでの技術課題は「発火温度が高い新材料の開発」です。
この技術課題を解決した新合金が『KUMADAI不燃マグネシウム合金』。
これを開発したのは熊本大学大学院自然科学研究科の河村能人教授です。
新合金の発火点は、1100度前後です。加えて強度や耐食性に優れます。
新たに開発された材料の組成はMg97Zn1Y2です。
地道な研究開発の成果です。材料開発ではベースとなる材料へ添加すべき元素の種類とその配合比を見極めるのが課題です。
候補となる添加元素を決め、狙いの配合比近傍で数十通り、数百通りのサンプルを作製、特性を分析する……材料開発の定石ですが大変な仕事です。
うまくゆく保証もなく、研究開発へ投入した時間が報われるとも限りません。できなかったという結果のみが残ることもある中での成果です。
技術課題は新材料の開発というモノづくりの王道行く極めて難易度の高いテーマです。
2-2 炭素繊維強化樹脂(CFRP)
炭素繊維強化樹脂はマグネシウム合金対比で比強度、比剛性が優れており、軽量化の切り札のような材料です。
ただし、量産性と価格がネックになっており製品への採用は一部の上級グレードの自動車および航空機に留まっていました。
技術課題はネックとなっている量産上の問題解消です。
炭素繊維強化樹脂は母材が熱硬化性樹脂と熱可塑性樹脂の2種類ありますが、いずれも成形工程で「加熱」が欠かせません。
この「加熱」のために生産性が低く、製造コストを押し上げる要因になっています。
技術課題は「加熱」に関連して、生産性を上げて、製造コストを下げること。
この技術課題を解決する2つの事例があります。
- 成形工程を簡略化した事例
- 加熱の原理を根本から変えた事例
です。
東レは成形工程簡略化技術を考えました。
従来、中間素材を高温・高圧で硬化させるために加熱圧力釜が必要でした。
東レは新たに「真空圧」を活用し、炭素繊維へ樹脂を注入・浸透させてからオーブンで加熱・硬化させる成形技術を三菱重工業と共同開発しました。
これで、設備投資がかさむ加熱加圧釜が不要となりました。
具体的な技術課題は高温で加圧することに替わる要素技術の見極めでした。
それが減圧、真空圧であったということです。これで設備の簡略化を達成しました。
(出典:『日経ものづくり』2015年12月号)
産総研は低コスト量産手法として加熱の原理を根本的に変える検討をしました。
ヒーターを使って「外部」から加熱する方法に変えて、マイクロ波を照射して炭素繊維を発熱させ「内部」から加熱する方法を考えました。
技術課題は「外部」からではなく「内部」から均一、かつ高速に加熱させる要素技術の見極めでした。
外部からの加熱では加熱対象物の容積、熱容量と熱の伝わる速度の影響から全体が均一温度に達するのに時間を要します。
そこで、逆転の発想で内部から均一に加熱する方法はないかと考えた。
電子レンジで加熱するイメージです。
そして、マイクロ波照射による加熱技術を開発するため、さらに2つの技術課題を解決しています。
1)母材となる樹脂での熱の伝わる速度を早くする。
2)成形品を抱いた型の熱の伝わり方を遅く(低く)する。
前者は成形品全体が短時間で均一に温度上昇するためには欠かせないことです。
成形品の内部に無数に存在する発熱した炭素繊維を起点に樹脂全体へ熱を伝えるためです。
外部から一方向に熱を加える今の方式へ適用しても効果はありますが、内部に分布している無数の炭素繊維から熱が伝わってくる新たな方式では、その効果がより大きくなります。
そこで、母材となる樹脂の熱伝導率を向上させるためにはと考えた。
そして、添加物によって熱伝導率の向上を図った。
樹脂に熱伝導率の高いセラミックスである六方晶窒化ホウ素を添加しています。
また、後者はヒーターで外部から熱を加える時とは真逆の発想です。
外部から熱を加える場合、外部の熱を内部の成形品へ早く伝導させることを考えます。
したがって型の材質は金属(鋼)です。金型ごと加熱して内部の成形品を硬化させます。
それに対して内部から発熱する場合、成形品を抱いている型の役割は、熱を伝えることではなく、熱を保持、閉じこめておくことに変わります。
したがって、型の材質は熱伝導率の低い材質を選びます。
セラミックス焼結型を開発しました。
(出典:『日経ものづくり』2016年1月号)
3. 技術開発では工場独自の手法や手順を磨く
技術開発では解決すべき技術課題を明確に設定することが大切です。
そして、技術課題を分割していくことです。
先のマイクロ波照射による加熱では、母材の熱伝導率と型の熱伝導率を技術課題として挙あげていました。
分割することで適用すべき要素技術が見えやすくなります。
多くの技術課題は従来の要素技術の組み合わせで解決できる可能性があります。
従来技術+従来技術=付加価値の発想です。
燃えにくいマグネや熱伝導率の高い樹脂を開発するために添加すべき元素を見極める材料開発では、さすがに専門的な知識がなければ手も足もでません。
しかし、成形品を抱いた型の役割が熱伝導ではなく、熱を閉じ込めることになることからセラミックス型を発想することは我々でも行けます!!
困難は分割して考えよ、です。
技術開発では、
- 解決すべき技術課題を明確に設定する
- 設定された技術課題を分割して、適用すべき要素技術を探す
技術開発では工場独自に開発手法や手順を磨いていくことも大切です。
手法や手順を意識して技術開発を進めれば、思いつきやなんとなくや勘による開発はなくなります。
まとめ
技術開発では「解決すべき技術課題を明確に設定した後、課題を分割して適用すべき要素技術を探索する」という手法や手順を意識する。