工場(他社)見学にチェック・リストはいらないの?
工場見学には2つの見方があります。
この話はL氏の体験談ですが、筆者と同じ取り組みで各種の成果を企業にもたらしてこられた方法なので、以下に紹介することにします。
①勉強のため1つでも良い点を持って帰ろうとする見学方式
②自分の工場のレベルと比較して他はどの程度であるか、どちらかと言うと批判的な見方のみに終始する方式
L氏の話は、かつて、M社のA工場で「シングル段取りという方式を導入したいと考えている」というご要求に、段取り改善手法の説明会を開催した時の話です。
M社での説明やビデオの撮影内容を紹介したのですが「現在3時間もかかっている段取替えの時間が10分以内になると言われても信じ難い!」という状況に陥ってしまいました。
現実に、近隣のT社を始め多くの企業では、下に示した図の関係から、多種少量生産対応を図るため、既に同種の設備の段取りを10分以内、しかも、あまりお金をかけないで実施している状況でした。
L氏の話は信用されなかったのです。
このため、「近隣に実際に3分程度で2,000トンの大型プレスの段取替えを成功している企業の見学をしよう!」ということになりました。
正直言って、M社の担当技術者A氏は明らかに否定的でした。
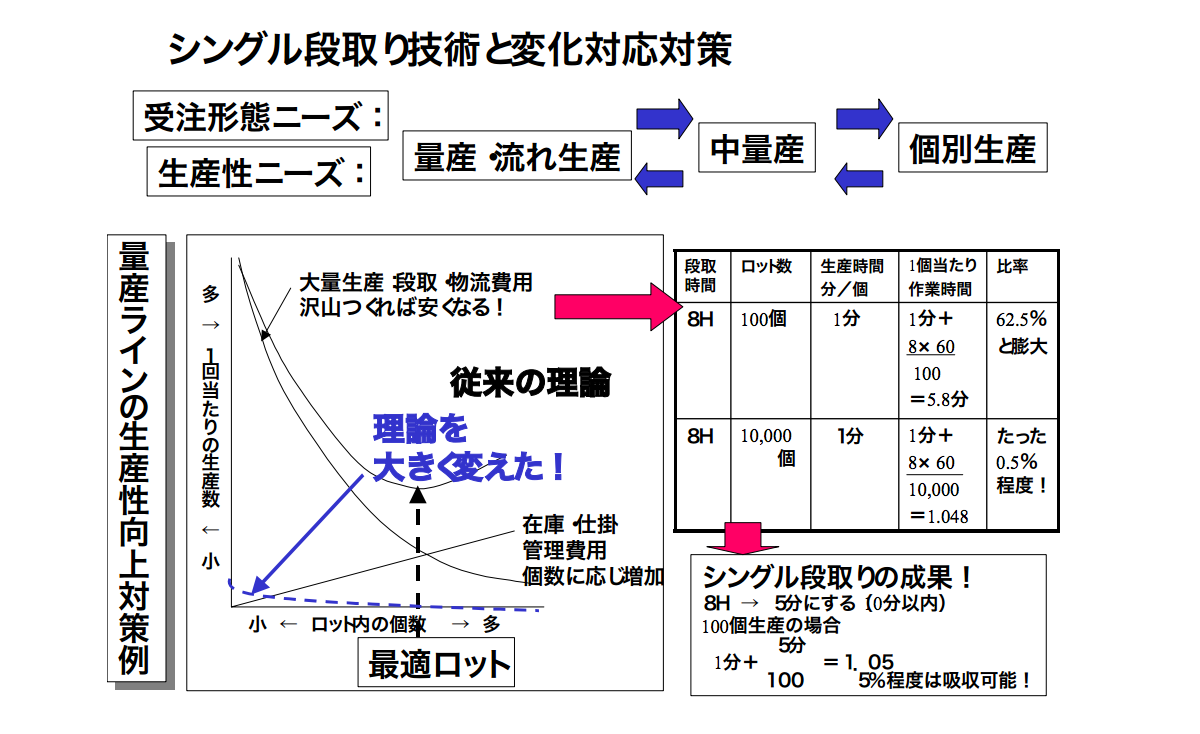
その翌週、L氏の計らいで、シングル段取りを実施している工場見学の調整が取れ、見学となりました。
見学では体験談の後、見学です。
そこでは2トンもあるプレスの金型交換を一人で3分、しかも、苦労なく何度となく行っている状況を見学しました。
その帰り道、バスの中で、M社の見学の話が出たわけですが、最初、当該課長のAさんに「いかがでしたか?」と聞くと、「確かに、Lさんの言う通りだった。しかし、あそこのプレスと製品は簡単だよ、うちの場合は……」と、できない条件を、これでもか、これでもかと並べ立てたわけでした。
加えて、「あの現場はムダだらけだぞ、人は監視作業をしているだけだ! レイアウトが良くない、もう1台を私だったらもたせる!」とか、「設備の5S、棚の整理も良くない……」と、今回の見学と関係ない現場の問題を並べ立てました。
ハッキリ言って、Aさん達を工場見学に連れていった私はガッカリしました。
このように話すと、この話をしたAさんは意欲のない技術者かな? と思われるかもしれません。
しかしAさんの職場の雰囲気、提案件数、改善意欲は高く、5Sなどはいつも工場のお手本的な存在であり、現場管理者としては申し分ない状況です。
設備に詳しいためか? 段取りの改善には否定的でした。
最初から他社の良い点を受け入れることを嫌うことなど、自分の技術・管理のレベルに自信を持っていたためです。
しかし、時のM社・経営トップは懸命でした。
工場長に工場見学の報告をしたところ、
「全く話にならん! どの企業を見ても参考にならないものはない! 私もLさんの紹介で他社を事前に見てきたが、A君、君はなにを見てきたのだ、A君にやらせることはやらせるのでLさん任せてください!」
と言い、私を部屋から出し、工場長はAと話し、「Aさんにお任せ」という話で、この対策はAさんに目標値だけが与えられ、「否定するなら、見学した工場より優れた改善を俺に示せ!」という命令と共に、「Aさん一任!」となったわけでした。
また、工場長は「私に任せてください」ということで、この企業では、一旦、Lさんの指導は休止となりました。
その後、半年が経過しました。
この時点で「段取りの時間は半減しましたが、とてもシングルには程遠い状況だった」という報告が、L氏のところへM社の工場長からきました。
この時、会社の方針で「シングル段取り化への見直し」という命令が出ていたわけでしたが、当然のことながら、Aさんの職場ではトップからの業務命令で段取り作業内容の見直しと同時に、再度の計画の提出が求められていました。
時に、Aさんの上司は「前回の工場見学を含めて、発想を変えて取り組むように!」とAさんに命令を出していました。
しかし、Aさんは困惑!
具体策が無いのも事実、実は、大変困っていました。
このため、今度は、Aさんが上司を説得して私のところへ応援を依頼してきたわけです。
L氏の見方では、「先のAさんが行った前回の工場見学の見解は間違っている!」と思っていましたが、「議論をしても、頑固なAさんには通じない」と考えていました。
見学した企業のプレスと形態は違っても全ての技術内容は適用可能だったのに、その点をAさんが無視した点が問題です。
そこで、今回はAさんに、「先の工場で見た内容と当該工場の設備段取りのどこが違っていて、どこが利用可能か?」と質問しました。
新たな分析より、既に先輩がやって簡単に完成している内容を導入することが必要だったからです。
しかし、この質問を詳細にすればする程、Aさんをはじめ、M工場の方々、同行した方々を含めて見学内容が曖昧になってきました。
そこで、「何も、見てこなかった。現場見学は単なる物見ゆさんだったわけですね!」
この言には、「申し訳ない!」という返事だけでした。
反省があれば、もうAさん達を問い詰める必要はありません。
Aさんは経歴も発言力も行動力もあるM社では改善キーマンです。
そこでLさんは対策へ話を切り換えました。
「再度、見学しましよう! しかし、再度の見学は今回限りです。
交渉してみますが、全てを詳細、具体的に見る関係上、何をどのように見るべきか、内容と担当区分を整理しなければ……」と言ってチェック・ポイントと同時に担当者を決めていきました。
再度の工場見学となると、受け入れ側の企業は渋ります。
しかも、お礼や良い印象を言ってこないM社の方々に対して、何もメリットが無い時間つぶしに似た対応に、見学相手のS社が渋るのは当然です。
このためLさんの調整に苦労しました。
だが、幸いにも、「今回限り! Lさんにはお世話になったから……」ということで、再度、先の会社の見学を取り付けることができました。
今度の工場見学は真剣でした。
また、事前に準備した項目と担当毎に分担した内容にしたがってS社の工場見学を進めました。
Aさん、今度は、L氏の指導内容を自ら見直し、活動のためのメンバ-編成、生産上のチェック・ポイント、管理や波及のポイント、Bさんは技術的な改造の中身、金型加工の注意点、Cさんは作業分析の方法、標準化上の注意……といった準備をしていました。
その結果、同じメンバーだが前回とは全く異なる方法で工場見学が具体化、かつ、詳細に行われました。
いよいよ帰社です。そこで、再度、Aさんに質問すると
「いや-、ありがとう。前回は目を開けて見ていたつもりだったが何も観て(見るではない)いなかったことが、今回の方法で始めてわかりました。
ありがとうございました。
うちのプレスや製品の状況は多種少量の見学工場の状況とはあまり変わっていないこともわかった。
前回の見学を反省すると穴があったら逃げ込みたい!」という話をしました。
この時、同じ人がこうも異なる感想をもつものか? と、当時、L氏は思ったそうです。
その後、3カ月の後、Aさんの工場では4分/回の段取替時間は見事達成し、「成果と共に、横展開も推進できた」という結果です。
また、この事例は、今後の多くの職場の模範にもなったそうです(なお、シングル段取りへ持ち込む手順は下の図の手順で進める対策が手順化されていますので、ご参考ください)。
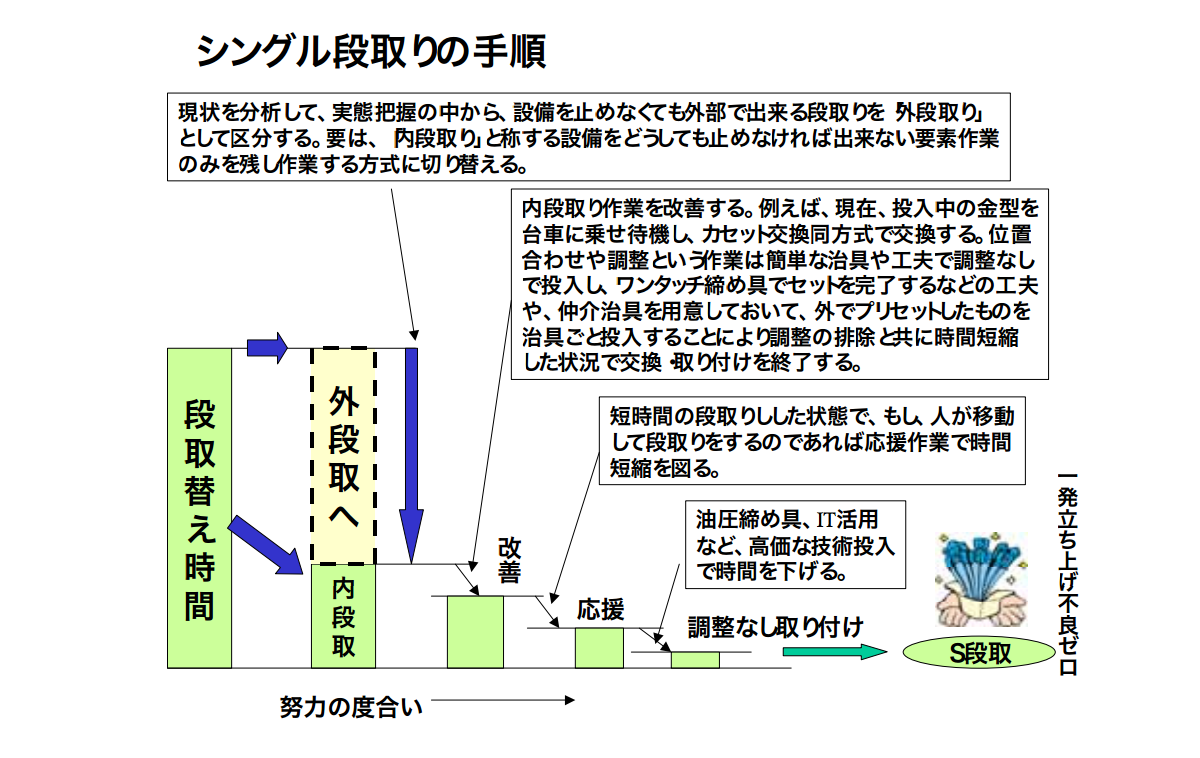
コメント
工場見学はニ-ズと目的をもつと、見方がこの例のように変化します。
L氏が「工場見学にチェック・リストを作ろう!」と言った発想は、実はその前、筆者も若いときに、ドイツVW社の技術陣が日立金属(株)のある工場見学依頼時、付き添いの形で立ち会った経験から学んだ内容です。
1970年代の頃です。
当時は日本のメ-カ-を凌ぐ技術力でアルミ鋳物を生産していたVW社の方々が「日本のメ-カ-を調査して部品の発注を検討したい!」という希望を受けました。
この頃、VWの工場を日本につくるつもりだったようです。
見学者は4名1組でした。
マネジャ-のBさんはレイアウト、他の技術者Nさんは生産管理、技術管理と製品製造のポイントを担当。
技術者Pさんは金型の成分、硬さ、加工方法、温度・表面塗装や寸法管理のチェック担当。
Tさんは設備仕様、作業サイクル、現場作業者のスキルと製品のバリ、不良、難しい形状の鋳造状況(鋳肌、ピンホ-ル、バリなど)のチェックを行い、当然時計とノギスを持参してメモを取っていました。
最後のRさんは材料の購入先、塗型剤の成分、管理状況、エネルギ-の仕様状況と管理や価格……といった内容を事前に用意された項目にしたがって聴取したり、メモしたり、といった状況でした。
見ていて分担が実にうまいので、「どうしてこのようにチ-ムワ-ク良く情報を集めることができるのですか?」とお聞きすると、「チャンスは今回限りです。
したがって、ドイツの自分の工場でシミュレ-ションしてきました。
工場内の比較や協力企業の比較を同じ方式で行い、OK! と判断してから今回の取り組みになっています」とのお話に、筆者は大きな衝撃を受けました。
理由は、『工場見学にも技術手段がある』という内容を初めて学んだからです。
通訳の方のお話では、
「見ていてごらんなさい。彼らは多少チェック項目をダブって集めています。
工場見学の帰り道は全て情報の確認時間です。
メモに書いたものを討論して整理しているでしょ!
日本での観光は休日に集中して行いますが、あくまで付け足しです。
良い観光地があれば、日を改めて来るそうです。
移動時間も仕事の時間です。
ホテルへ帰ると大きな紙を広げてカ-ドに記載した内容をチェック項目にしたがってつけていますよ。
日本における見学企業の技術比較は一覧でわかりますよ!
たいしたものですねドイツの一流陣は。
要は、工場見学内容は個人の知識ではなく、会社の財産にする! という考えで命令を受けて行動しているようです。
さすが、一流のエリ-トのやる内容は違いますね。
このようなことは日本の企業こそがやるべき内容だと思います。
日本の企業はVW社のチェック項目で、下手をすると裸同然に全貌がわかってしまうのではないでしょうか?」ということだった。
日本でも工場見学は多種多様、多人数で行われています。
しかし、私は、当時、ここまで徹底している例は聞いたことも、見たこともなかったので驚きました。
この後、1986年に、筆者はJMA主催による生産革新視察団に参加させていただく好機を得ました。
30名の集団です。この時、見学内容はレポ-トにしようと考えました。
幸い、見学者の事前打合せでも実施が決まりました。
このため、視察団の団長から「60の目でアメリカの超一流企業の取り組みを見学し、日本に役立つ情報を全て持ち帰ろう!」という内容が合言葉になりました。
私は、ドイツVW社の見学内容を紹介した関係上、チェック・リストを事前に作成する任に当たることになりました。
チェック・リストは、見学対象の企業に事前に質問上を送り準備いただく内容や、過去-現在-将来に対して項目を定め、表を埋めるスタイルの作成を準備しました。
また、工場見学時、レイアウト、設備、作業手順、検査基準と方法、設計の要点、仕様機材や材料の状況、オペレ-タ-の育成、金型などキ-技術の列挙を行い、見学時、質問時に行う区分や担当を決め、チ-ム編成を行うという企画を担当し、事前見学会議にかけましたが、視察団の団長にはその内容を大いにバックアップしていただいきました。
このため、チ-ム員の協力、役割の設定のみならず、全員が仲良く、情報も決められた様式にメモで集まりました。
見学団は異業種の方々との編成チームでしたが、個々にその特長を生かす形で、いろいろの情報が私達レポ-ト編集メンバ-のところへ集りました。
私の印象だが「総々たるメンバ-が集まると実に見方の異なる内容が集まるものである」
「私一人では絶対にとらえることができない内容や見方と意見が得られた!」といった印象でした。
この内容は、その後、JMAでCIM研究会(Computer Integrated Management)など研究の基になった項目が多数ありました。
例えば、CADの内容や、ロボット、情報ネットワ-クの事例と技術の探査技術ですが、これらの内容は全て、GE、TI、GMの新技術開発の担当者が先進的に進めていた内容でした。
これ等の内容を報告書にまとめたわけですが、JMAで報告会が臨時に開催されました。
当時200名程度の会場は満杯となりましたが、思い出深い内容は、時間を過ぎても、多くの企業の方々が今後の日本の生産革新のあり方を討論した講演会だったことを記憶しています。
今、インタ-ネットの活用法や3Dと共にCADは各社で当たり前となっています。
この時の報告内容を基に多くの企業の方々が内容を検討される題材にしていただいたと、後にJMAで教えられました。
当然のことですが、視察団に加わった一流企業の方々は、「あの時の見学内容は我が社でもCAD~CIM早期具体化に大変に役立った!」と言っておられたことは、この見学方式が有効だったことを示しているように思います。
特に企業見学の仕方が「内容にプラスする形で有意義であった」という点は大きな内容です。
今も視察団仲間の方々にお会いすると、思い出話が出ますが、私自体がこの内容を大変役立てたことを考えると、単なる自負とは言えないと思います。
要は、工場見学の手法をVWから学んで活用したことが、ここまでに紹介した成果を生んだわけです。
当時のアメリカ視察団の報告内容には、工場見学以外に、ホテルのコンピュータ・ネットワーク・システムがありました。
この内容は見学団に取っては異業種だったホリデイ・インというホテル・サービスのIT化でした。
また、その内容は、旅を進める我々から見ても顧客志向の情報とサービスを的確に示す内容でした。
要は、見学地が変わる度に、我々が好む食事や見学地や部屋の設定まで、次の宿泊地へITネットで伝わっていて、心ゆくまでのサービスがあり、当時、日本人が感じるニ-ズの把握~提供に大きく役立っている内容を見たからです。
当時、「このサービス形態はやがて日本でも顧客管理にきっと参考になるシステム化である」と思ったわけですが、OECDで『個人情報管理』が検討され、個人情報保護法と共に、ITによる顧客管理~ニーズ把握~新製品創出という、プロセス全体を中心に活動する現在のITネットワーク活用をいち早く想像させる内容だったのです。
当時の我々には衝撃的だった内容です。
具体的な内容として、今は、日本でも当たり前ですが、当時のホリデー・インの宿泊は、宿泊先の確認、我々の移動に合わせて、行く先々での情報の準備、料理の好みを知っての準備などには関係者は感謝と同時に舌を巻いた次第です。
30人と人数が多い顧客でしたが、サ-ビスは満足のいく内容でした。
コンピュータで一元化したリアルタイムの情報、事前連絡アラームシステムの活用が顧客サービスに大きく貢献していたわけです。
21世紀の現在、この種の分析は、当たり前です。
だが、1986年に現在のIT活用によるホテルサービス・システムが実現していたわけです。
この点も「企業内でコンピュータ・システム構築の際に取り入れるべき重要な点である!」と、当時は皆と話しました。
同時に、21世紀は「情報を制するものが世界を制する」というニューニュー・フロンティア精神を察知したわけです。
ちなみに、アメリカ大陸では西部開拓史をフロンティア精神、その後の海外(グローバル展開)をニュー・フロンティア精神というそうですが、我々は、一早く、その次に来る内容を、1986年の視察団で学んだわけです。
米国視察団では、将来の産業のあり方を話し合ったことは、今も意義深い体験だったと思います。
工場見学をプラス思考で見る見方のもう一つの例を示すことにします。
今も、産業界ではJIT導入が盛んです。
トヨタ生産方式が発祥になり、各社でスタートしたジャスト・イン・タイム生産です。
トヨタ自動車がこのシステムを構築するとき「アメリカのスーパー・マーケットを参考にした!」という逸話が残っています。
この話は、当時、製造部長だった大野耐一氏(後の副社長)が1950年頃、赤字で苦しむトヨタ自動車の立て直しに欧米を視察した際、メーカーからは何も学ぶものがなく、帰国に際して何を持ち帰ってトヨタの立て直しに役立てるかを悩む中、
「アメリカのスーパー・マーケットでは棚の商品がなくなりそうになると発注をかける。
後工程引き取り、必要な注文だけ、必要に応じて前工程に生産のオーダーを出す方式である。
日本では後工程におかまいなしに作るから、作り過ぎのムダが発生するのだ……」という話がありますが、この話は先のM社の企業見学にLさんも話した内容ではないか? と推察する次第です。
その理由は、筆者がトヨタ生産方式の見学のためトヨタ自動車へ訪問したとき、講演会でトヨタ生産方式の創設の師、大野耐一氏のお話でもこの内容を、直接お聞きしました。
しかし、筆者が’88年から3年間アメリカのオハイオ州に在住、米国内のスーパー・マーケットのどこでこの話を確かめても、後工程引き取り方式の特徴的な話は確認できません。
したがって、ここからは筆者の憶測です。
「あの話は上手な作り話ではなかったのではないだろうか?」と考えたわけです。
このように考えた理由は次のような理由からです。
①大きなトラック単位で大きなスーパーの棚に物を置くにはかなりの管理システムが必要になるが、棚の管理ではなく、売れ行きの集計を基に発注者が注文を出している形態を見て、いまからトヨタで進めたい後工程引き取り、造り過ぎのムダ排除の話とドッキングさせたのではないだろうか?
発注内容を調べたが、日本の商店のそれと何も変わらなかったからです。
②米国出張は当時赤字に苦しんでいたトヨタ自動車の中で大変な負担であった。
何がなんでもアメリカからトヨタの収益改善に役立つお土産となる情報をひねり出しても帰国しなければならない事情が海外視察に出された大野耐一氏達にはあったのではなかろうか?
③当時は今と異なり、海外の情報は極めて少なかった。
1ドル360円の時代には海外に行く人はほとんどいないので、もし、大野耐一氏達の内容に反論したいと思っても、そのことのために海外にわざわざ行く人はいないであろうし、今、トヨタ生産方式で進めたい内容をみつけたことになれば、会社の関係者の刺激と牽引力になる。
ましてや、会社の方針になりかけている方針と事例に反対はないはずである、と判断しても良いと考えるのは自然のことではないだろうか? よしんばウソでも害毒は皆無です。
以上が筆者の仮説です。
だが、もはや、大野氏には何回かお会いしたのですが、故・大野耐一氏に確かめるすべはない状況です。
だが、もし、このような内容であったとしたら、やはり、大野氏を始めとする関係は経営直結型で問題解決技法を上手に企業へ投入された師であると思います。
筆者はトヨタ方式とスーパー・マーケットの関連の話を「ウソだ!」と言っているのではありません。
「何でも役立つ見学の内容は持ちかえり活かす!」ということをやってのけた点に、大野氏の偉さを想像するわけです。
これは、アメリカの地でフ! と思った話を記載してだけですが、私ならそうしたかもしれない! と、思ったわけです。
このように思っていた時、たまたま、故・大野耐一氏の話をトヨタ自動車見学時、コーディネータ役で大野氏に同行された重役の方にお聞きする機会を得ました。
そこで、この話をすると、「中村さん、よく気がつきましたね! その通りです」というお話でした。
また、この時、「やはり、実務者は同じ考えで、他所から何かを持ち帰る」という行動様式を筆者は再確認しました。
以上、「どのような見学も良い点を盗む見学をすべき」を、ここに紹介しました。