工場運営の管理項目と現金のつながりを見える化する
利益と運転資金の処理の流れを把握するとキャッシュ獲得の勘所が見えてくる、という話です。
現場で管理する項目がキャッシュの獲得にどうつながっているか、その考え方が整理されていますか?
月末や年度末に経理部門から報告を受けるから数値自体は分かっているけど。
現場も、ある程度理解してくれたら、仕事の意義を実感してもらえるかも。
現場の管理項目とキャッシュ獲得とのつながりを上手く説明できるだろうか?
図を使って処理の流れを見える化します。
流れを知ることで、付加価値を用いる理由が理解できます。
1.工場運営の目的は現金(キャッシュ)を稼ぐことである
工場運営の目的は現金を大いに稼ぐことです。
利益ではなく、現金(キャッシュ)です。
利益は目的ではなく手段のひとつと考えます。つまり利益は現金(キャッシュ)の源泉ととらえます。
キャッシュという視点を持つと運転資金の規模や増減も気になります。
そして、キャッシュを増やすには5つの正攻法があります。
(1)変動費から付加価値をひねり出し、直接的な利益の積み上げを図る。
(2)固定費(付加価値)から経営資源を生み出し、増産or開発力/営業力強化へ振り向ける。
(3)借金を返済して固定費(支払利息)の低減を図り、直接的な利益の積み上げを図る。
(4)運転資金(特に棚卸資産)をスリム化する。
(5)高付加価値化で単価を上げ、販路開拓で販売数量を増やして売上高を増やす。
現場での生産活動を通じて、この5つの正攻法をしっかりと進めることは、工場運営の目的でもあります。
2.工場の生産活動を鳥の目で俯瞰し現場管理項目を把握する
工場の生産活動を鳥の目で俯瞰すると、下図になります。
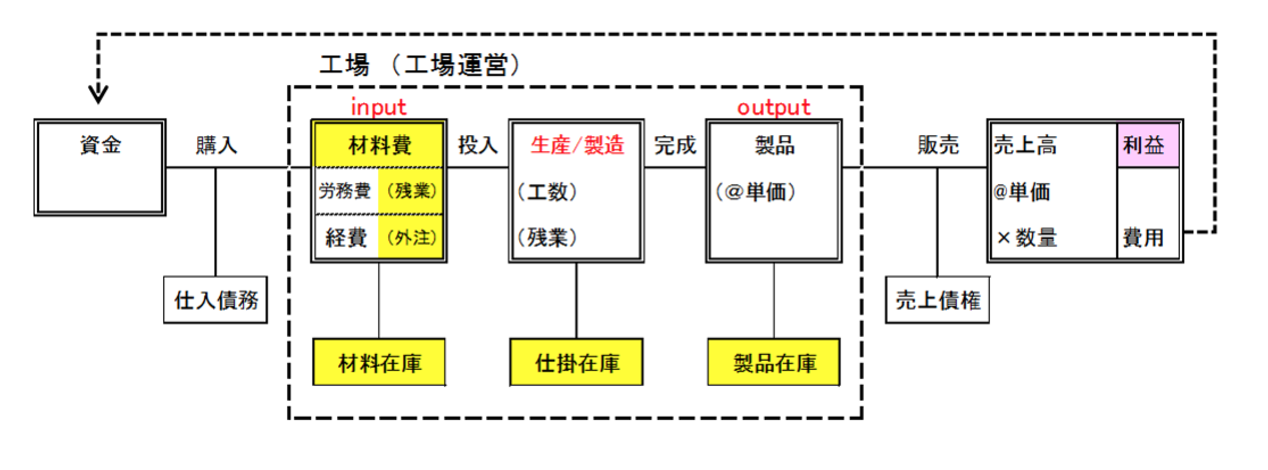
このうち黄色の項目は原則、現場で管理します。
これらは全て利益か運転資金につながる管理項目です。
(1)材料費
(2)外注費
(3)残業費
(4)材料在庫
(5)仕掛在庫
(6)製品在庫
これら6項目が具体的にどのような処理を経て利益や運転資金へつながるのか……。
処理の流れを理解することは、鳥の目を磨くために役立ちます。
処理の流れを把握することで、工場全体のパフォーマンスを評価するのに利益ではなく、なぜ付加価値の方が適しているのかもわかります。
3.製造費用から経常利益を評価する
さて、まず、利益につながる材料費、外注費、残業費です。
製造費用となる「直接材料費+直接労務費+直接経費+製造間接費」の一部を構成しています。
そして、製造費用に仕掛在庫を考慮して、製造原価が評価されます。
さらに、その製造原価に製品在庫を考慮して、売上原価が評価されます。
そして、売上原価は損益計算書の勘定科目のひとつです。
最終的に利益が、
経常利益=売上高-売上原価-営業費-支払利息
と評価されます。
製造費用 → 製造原価 → 売上原価 → 経常利益
の順に評価をします。
4.棚卸資産から運転資金を評価する
次に、運転資金につながる材料在庫、仕掛在庫、製品在庫です。
運転資金は、主に材料在庫、仕掛在庫、製品在庫、売上債権、仕入債務で構成されます
なお、材料在庫、仕掛在庫、製品在庫は一般的に棚卸資産とよばれます。
5.全体の処理の流れを見える化する
文章の内容を見える化します。
そこで、処理の流れの概要を下図に示します。
(細長い図となってしまいました……)
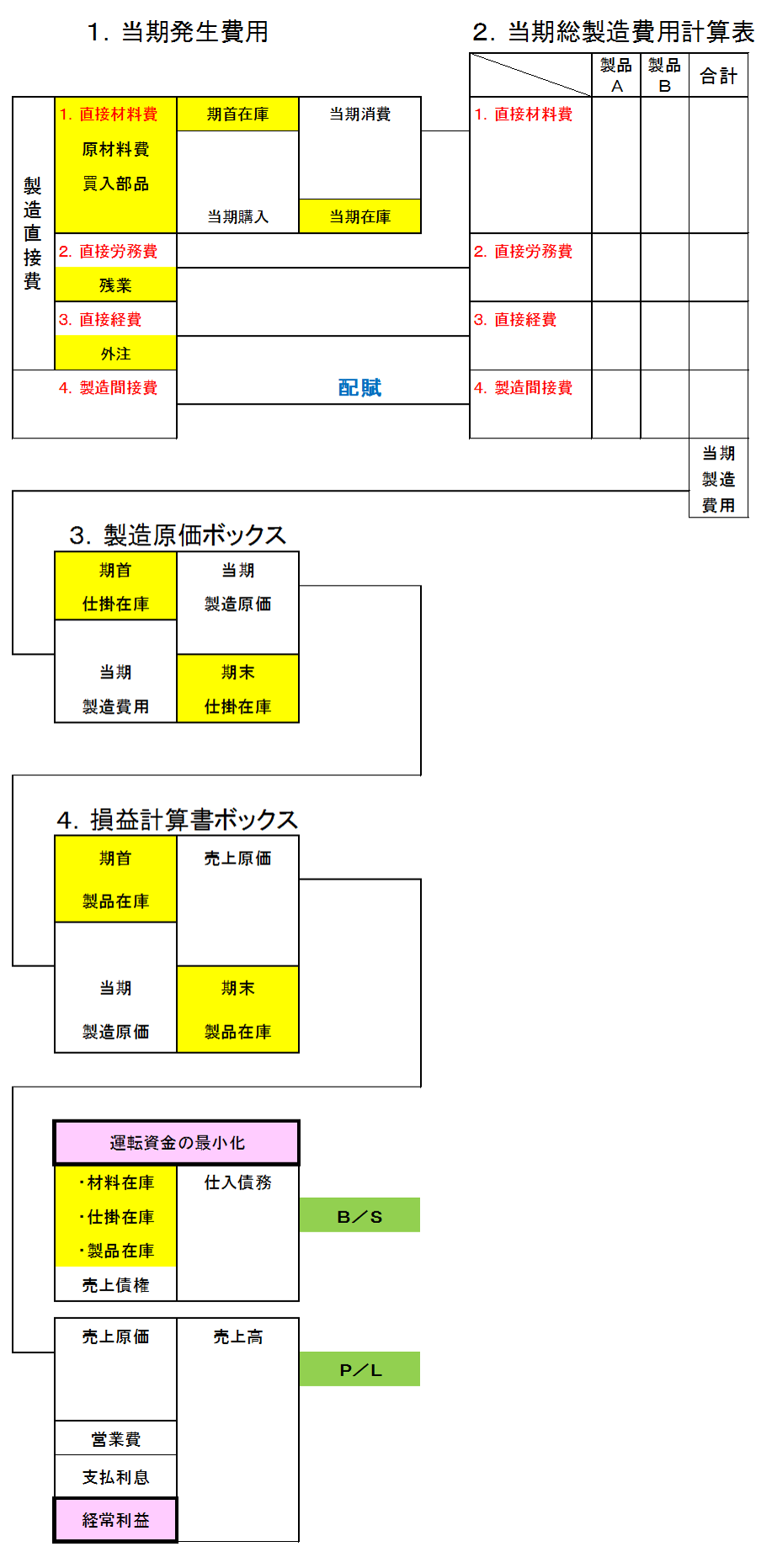
1.当期発生費用
2.当期総製造費用発生計算表
3.製造原価ボックス
4.損益計算書ボックス
それぞれのつながりを示しています。
図中のピンク色項目が狙いです。
経常利益の獲得と運転資金の最小化です。
それぞれ、緑色の項目の損益計算書(P/L)と貸借対照表(B/S)の中の項目で表現されます。
そして黄色の項目が原則、現場で管理をする6項目です。
当期発生費用からスタートして、一番下の緑色のP/L、B/Sがゴールです。
なお、原価計算を分類する時、
・受注生産形態において採用される個別原価計算
・大量生産形態において採用される総合原価計算
の2つに分類する方法があります。
上図は個別原価計算での表現です。
当期総製造費用発生計算表で製品個別に原価を評価しています。
総合原価計算でも基本的に処理の流れは同一です。
発生原価を直接材料費とそれ以外の費用(加工費)に分類し直接材料費の製造原価ボックスと加工費の製造原価ボックスに分離して考えます。
(このあたりは参考まで)
理屈はこのようになり、複雑だという印象は拭えません。
利益等を厳密に評価しようとするとかなりメンドウナコトになります。
ですから、細かいことは気にせず、処理の「流れ」を把握します。
全体を眺めると、いくつか気が付くことがあります。
・付加価値は工場全体のパフォーマンスを評価するのに適している
・モノづくり工場で、付加価値を高める機会は現場にある
さて、付加価値の定義は次式でした。
付加価値額 = 売上高 - 工場の生産量に比例して出費される費用
この付加価値への理解を深めることができそうです。
5-1.付加価値は工場全体のパフォーマンスを評価するのに適している
当期発生費用から当期総製造費用計算表へ分析を進める際に、製造間接費は配賦(青色)処理されています。
全体の共通費用という性格を持つ製造間接費は、事前に決めたルールで製品別に分割します。
これは、工場の生産活動と直接には関係がなく、また、こうした処理は時間がかかります。
工場運営上の各指標は定期的にチェックされ、変化があるかないかを見ます。
大きなトラブルの前兆をとらえるためです。
損益計算上の利益は評価に時間を要するので、こうした役割を担えません。
数値の評価が出た頃には、現場ではすでにコトが起きてしまった、となりかねません。
コトが起きる前に、前兆をとらえられないと指標にはなり得ません。
したがって、現場担当者でも簡便に算出でき、かつ生産活動を的確に反映した数値を用います。
そこで、工場のパフォーマンスを評価する場合、製造間接費は除きます。
生産活動には無関係である上に、簡便で早い算出が可能になるからです。
さらに製造直接費でも工場の生産量に比例して出費される費用を中心に考えます。
ですから、直接労務費でも固定給部分は不要です。
したがって、材料費、外注費、残業費を主に考えます。
付加価値額 = 売上高 - 残業費 - 外注費 - 残業費
これなら、すぐに評価ができます。
また、生産量に応じた工場のパフォーマンスを上手く表しています。
5-2.モノづくり工場で付加価値を高める機会は現場にある
上図は製造業での流れです。
これがもし小売業だったらどうでしょうか?
当然、製造原価ボックスはありません。
損益計算書ボックスの製品在庫を「仕入在庫」に、製造原価は「仕入費用」に置き換えます。
小売業は商品を仕入れ、販売するまでです。
それ以上の処理はありません。
逆に言うと現場で付加価値を生む余地が少ないと言えます。
つまり、仕入れた時点でコスト上の勝負は、ほぼ決まる。
一方、製造業では上図に見るように現場の管理項目(黄色の項目)があちらこちらに登場しています。
それだけ、現場で付加価値を生み出す余地が大きいということに気が付きます。
キャッシュを増やす5つの正攻法も上図で説明できます。
どこをどのようにしてキャッシュを拡大させるのかイメージが湧きやすいです。
目で見て理解することで、キャッシュ獲得の勘所が見えてきます。
まとめ。
現場管理項目とキャッシュ獲得との繋がりを上手く説明することはできるだろうか?
図を使って処理の流れを見える化する。
流れを知ることで、付加価値を用いる理由が理解できる。
利益と運転資金の処理の流れを把握するとキャッシュ獲得の勘所が見えてくる。