作業要領書の作成からすべてが始まる|元トヨタマンの目
1.基本となる作業要領書の作成
これにより大くくりな全体像を万人に把握させることができる。
しかし具体的な作業内容を教えようと思えば、より詳細な説明が必要になる。
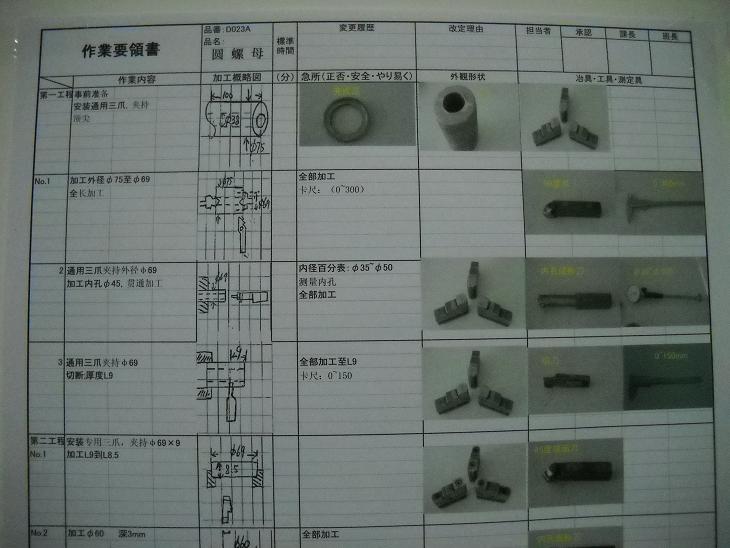
2.加工内容のビデオ撮り
ビデオを定点にセットして加工内容のビデオ撮りを行なう。
3.より詳細な作業要領書の作成
そのビデオを作業者に見せながら、新人に説明する内容を事細かに口頭でしゃべらせる。
そしてそれをまたビデオ撮りしておき、後でその内容を紙に書く。
さらにその紙に書いた内容を作業要領書としてまとめる。
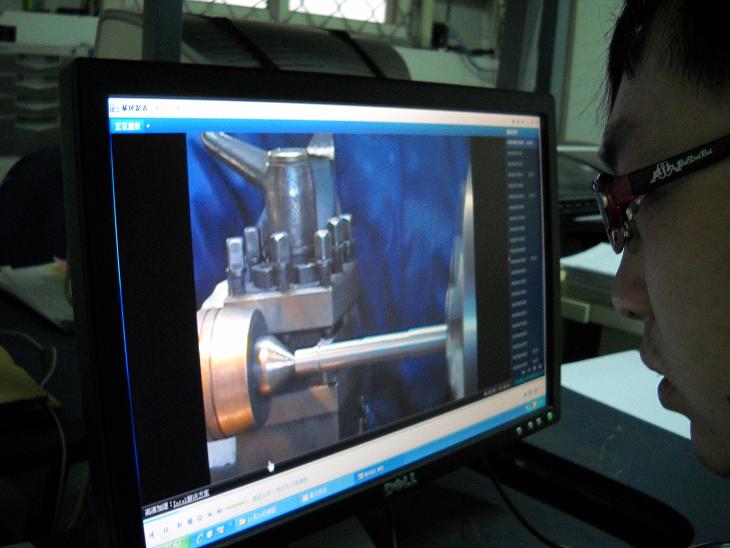
4.トヨタの作業要領書の内容
自動機でもこのように細かく作成しているのだから、手動機の場合はこの数倍細かくする必要がある。
刃具取り替え作業要領書……略図もつける
作業内容(急所……正否・安全・やり易い)
(1)チップ締め付けボルトをゆるめる(ブレーカーを左手で支えながら4ミリのレンチで)
(2)チップを外す(定位置に置く)
(3)チップおよびホルダーの取り付け面を清掃する(油分がなくなるまで)
(4)新しいチップブレーカーを取り付ける(奥まで)
(5)チップブレーカーの締め付けボルトを締める(チップを押さえながら)
部品加工作業要領書……略図もつける
作業内容(急所……正否・安全・やり易い)
(1)パレットから粗材を出す(右手で)
(2)CK239ワーク取外し・取付け(センター浅すぎは後工程FH、GP工程で危険):品質チェック50個で1個、ゲージは目視
(3)HM299ワーク取外し・取付け(両センターに確実に取付けること)
(4)GC143ワーク取外し・取付け(貫通状態を裏側から確認する):品質チェックは全部、ゲージは目視
(5)CJ988ワーク取外し・取付け(取付け面の切粉清掃)
(6)YM123ワーク取外し・取付け(前面が取付け面)
(7)YY114ワーク取外し・取付け(ブッシュは油溝が円周に切ってある方を型に入れる)
(8)YM127ワーク取外し・取付け(前面が取付け面)
(9)CS239ワーク取外し・取付け(光明丹80%以上):品質チェック10個で1個、ゲージはPS
大企業が中国などの外国へ進出する場合、「図面」と「標準作業票および作業要領書」の両方を準備して操業を開始する。
しかし中小企業の進出で、日本では熟練工に頼っていたため、「図面」しか用意できずに操業を開始する企業がある。
このような中小企業は千載一遇のビッグチャンスと捉え、徹底的な「標準作業票および作業要領書」の作成に努力しなければならない。
5.新人の現場実習
熟練工の育成には何年もかかる。
そのような工場では、新人を教育として受け入れたら、その新人はまったく戦力にならないため、その新人の工数は損失にしかならない。
そればかりか、熟練工の工数を割くことになり、その部分も大きな損出となる。
しかし工程化しつつ、その工程を分割し、標準作業票や作業要領書を作成していけば、新人の育成が非常に短期間でできるようになり、受け入れた新人が戦力になる。
さらに時間を割いて口頭で説明していたことが、あらかじめ文章化されているため、教える方の工数もかからない。
これにより新人の現場実習が、会社の損益に影響しなくなり、工場の拒否反応もまったくなくなる。
私はトヨタに入社して、3ヶ月の現場実習を経験した。
しかし当時、ホンダでは1年間の現場実習を行なっていたと聞いた。
この会社も、新人の現場実習を組立工程1年、加工工程1年にしてほしい。
そうすれば、営業マンの質をセールスエンジニアに向上させられる。
この会社の場合は、製品の機構がIT制御までの複雑化はないため、工場のつくりさえしっかり経験させれば、事務屋でも十分優秀なセールスエンジニアにすることは可能だ。
このように改善を進めていけば、会社全体に改善の効果が波及していき、すべてが良い方向に向かっていく。
その際、一番うれしいことは、従業員が成功体験ができることだ。
改善効果で、自分の仕事がうまく回っていくことを経験することは、従業員に強烈なイメージを与える。
それにより従業員が活性化する。
6.更なる発展
作業要領書には各作業の主要時間も記載し、作業の標準化・基準化を進める。
これにより各工程での所要時間が明確になり、これが1個流しのベースとなる。
ある程度のベースがそろった段階で、製品を選定して1個流しのトライをしたい。
3つぐらいの機械をベルトなどでつなぎ、1つ加工したら次の機械へ送る。
それを目の当たりにした作業者はきっと考え出してくれると思う。
ロット生産を続けていく限り、考えはまったく発展しない。
7.外注部品メーカーにも
中国では外注部品メーカーに対しても、図面を渡して説明するだけで、「後はよろしく」状態だ。
結果として不良が多発する。
この場合はその部品メーカーへ出向き、不良を発生させた作業のビデオを撮ってくる。
それを自社の現場作業者や管理者に見せて、正規の方法を事細かにビデオを見ながら語ってもらう。
それをまたビデオ撮りしておき、後で担当者がそれを基に作業手順書をつくる。
そしてそれを部品メーカーへ持っていき、遵守させるようにする。