付加価値工程が埋もれている状態を工程分析で知る
工程分析を使うと、加工工程が価値を生み出さない運搬工程に埋もれている状況が実感できる、という話です。
1.カイゼンの対象の範囲を設定する
「人」視点のIEでカイゼン対象は生産工程、付加価値作業、要素技術、動作の4つです。
生産現場を大きく見るところから始め、最後は動作のレベルに焦点を当てます。カイゼンの対象が、どのレベルに属するか把握することは大切です。
カイゼンの対象が森なのか、木なのか、幹なのか、枝葉なのか。カイゼンの結果、効果がどこまで及ぶのかをあきらかにするためです。
そして、それがどのような成果、変化へつながるのかを見極めます。この見極めのためにカイゼンの結果、効果が及ぶ範囲を特定します。
例えば、生産工程の工程順序の変更は生産ライン全体へ影響を及ぼします。
一方、動作のレベルでのカイゼンは例えば作業者の負荷の軽減であり、作業者へ影響を及ぼします。
なお、対象の範囲の広さや大きさと成果とは関係ありません。対象範囲が大きいからイイわけではありません。
動作のレベルでも、作業者の負荷軽減のお陰で、現場のやる気が向上し、現場独自のカイゼンが促されPDCAが廻る仕組みができ上がったりします。
こうしたケースでは、カイゼンの対象の範囲は狭く、小さくても成果は絶大です。
カイゼンの対象を把握するというのは、言い換えると、カイゼンの対象をどこまで掘り下げる必要があるかを知るということです。
カイゼンの目的を達成するために、適切なカイゼンの対象の範囲を設定します。
2.生産工程に着目したカイゼン:工程分析
生産工程に着目した時には工程分析で現状を把握します。
『生産管理用語辞典』では、「工程」を以下のように定義しています。
「入力を出力に変換する、相互に関連する経営資源及び活動のまとまり」
工程のアウトプットは、次工程のインプットになります。ですから、工程を設定する時は、区切りを意識します。
工程が技術的な順序の関係にしたがってつながるイメージです。区切られた、それぞれの工程へは目的とする結果を出すために経営資源が投入されます。
以上より、「工程」でイメージすべき項目は3つです。
1)その工程のインプット
2)その工程のアウトプット
3)その工程の目的
工程を説明するための3要素です。これら3つで簡潔に各工程を説明できます。
さて、生産工程を構成する「工程」を分類するといくつになるでしょうか?
4つに大別できます。
1)加工工程
2)運搬工程
3)検査工程
4)停滞工程
生産工程で起きていることは全てこの4つで表現されます。ですから、工程分析とは、現場の活動をこの4つに分類する作業です。
さらに、分析目線は「製品」と「作業者」の2つです。
工程分析の目的によって分析目線を使い分けます。
「製品」目線では、各工程は下記のように表現されます。
- 製品は付加価値を加えるために加工され、次工程に移るために運搬され、数量及び品質を検査される
- そして、生産ラインで停滞している製品には計画的なモノと計画的でないモノがある
一方「作業者」目線では、各工程は下記のように表現されます。
- 作業者は付加価値を加えるために加工をし、数量及び品質を検査する
- 作業者は製品を持って場所を変えることで運搬し、製品を持たずに移動する
- 作業者は何も無い時は手待ちや加工待ちで待つ
どちらの目線にしても、生産工程は、必ず大別された4つの工程、「加工」「運搬」「検査」「停滞」で表現できます。
製品目線と作業者目線での4つの工程を下表にまとめます。
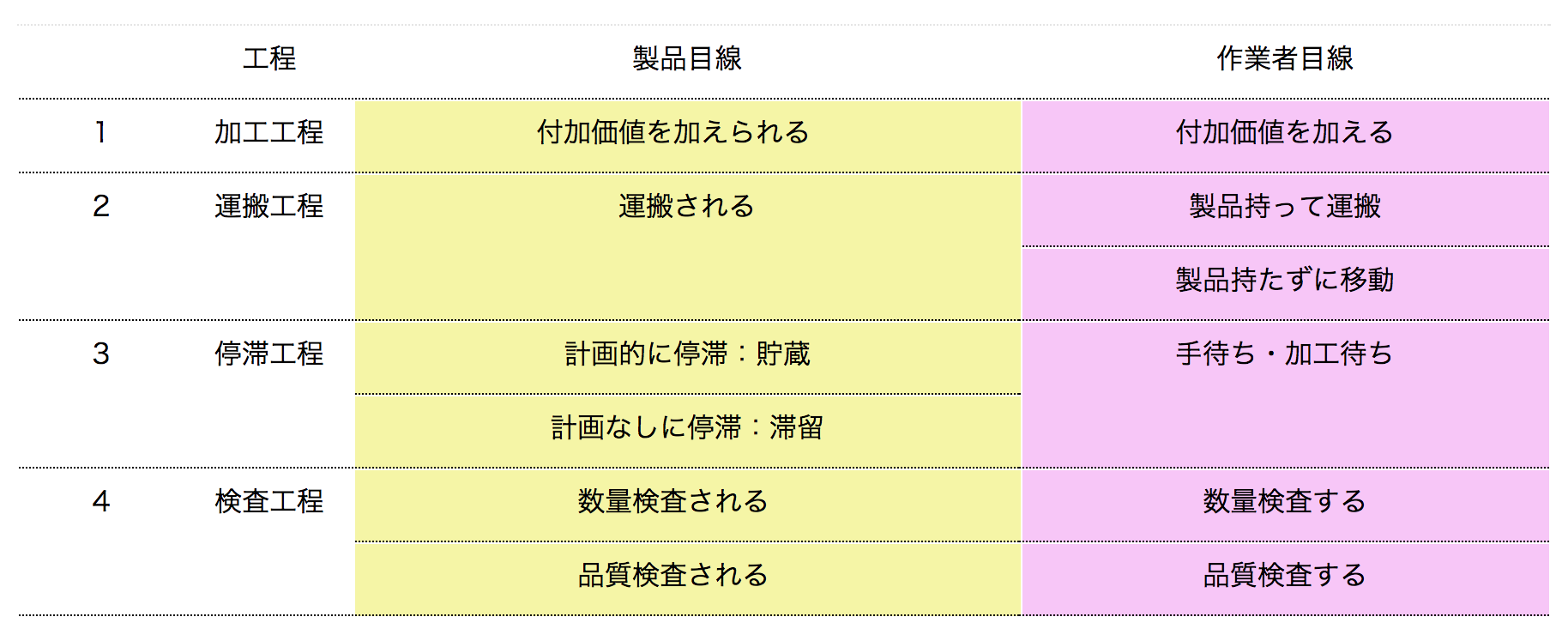
製品目線、作業者目線、各々6つの欄で構成されます。
それぞれの欄を記号で表現します。工程の流れを見える化して「今」を知ります。
3.工程分析の目的
生産の目的は価値の低い財の価値を高めること、つまり付加価値を加えることです。
ですから、大別された4つの工程で付加価値を加えることに直接貢献しているのは加工工程のみです。他は価値を生みません。
工程分析をすることで、加工工程以外の工程を把握できます。
そして、付加価値を生むことに関係のない工程がいかに多いか、気が付きます。この気付きこそが、工程分析の目的です。
中小製造業の工場では機能別に設備を配置したレイアウトが多いです。
このレイアウトでは、「運搬」工程が目につきます。
運搬はトヨタ生産方式の7つのムダのうちのひとつでもあります。
運搬自体から価値を生むことはありませんし、工具を取るために作業者が移動しても同様です。
よく言われますが、忙しそうに“作業者が動き廻っている”状態はヨクナイ。
儲かっている工場の現場は、一見すると“動き”がなく、整然としています。目指すべき工場の雰囲気はそんな感じです。
工程分析を使うと、価値を生み出す加工工程が、価値を生み出さない運搬工程に埋もれている状況が実感できます。
なんかマズイナ、と目で見て理解することからカイゼンを始めます。
まとめ
工程分析を使うと、加工工程が価値を生み出さない運搬工程に埋もれている状況が実感できる。