すぐ使えない海外研修赴任者用マニュアルを、つくるな!
今回紹介するのは、S社から海外赴任者のためのマニュアルづくりの依頼を受けたMさんの体験談です。
S社に対するMさんの対応例
S社の依頼は
「海外に出た方の技術伝授がうまく行かないので、IE+QC+VEを統合して、スムーズに進むマニュアルを作成したい!」
というものでした。
Mさんのところへこの相談が来た理由は、海外経験があること、海外進出企業を指導していること、そして海外で海外企業の指導をしているからでした。
また、Mさんに相談すると、その応えが実務的だったため、依頼することにしたそうです。
Mさんは、
「私としては、このテーマにそれほどの実力はないので、このご依頼には恐縮した」
と話していました。
「S社をはじめ企業の中で海外経験は多く、現地指導に当たられた方は星の数ほどおられます。
しかし、その効率が最良だったか? となると、判別に困るのが実情です。
また、多くのケースでは、離職率の高い現地でマン・ツー・マン教育が盛んに行われてきました。
このため、自慢話はあっても、定着には問題が多い実情です。
特に、現地に在住する日本人による技術伝承がうまく行かない場合、もちろん、言葉と文化の違いも手伝いますが、現地の方々が学ぶことを逃げるという事態が発生します。
こうなると、なかなか現地では定着しないで、日本人でカバーせざるを得ないことになります。
このようになると、現地での赴任期間は追加~継続となり、日本人の滞在者の期間も人数も増す一方となります。
このような事態を海外の現地工場では、“難しい仕事は現地人が逃げる”と言いますが、現地の方々から見れば、現地の方々ができない仕事が発生すると、日本人がすぐ手を出す。
それでも最初は、難しいけれど何とかマスターしたいと思っていて、学ぶ努力はする。
ですが、この回数が重なると、“もう、いいや! 日本人に任せた方が良い!”となるわけです。
この仕事を日本語と日本文化を持つ経験者でしかできない、すなわち“東洋の魔術”と解釈するのです。
さらに、現地人の間で日本人の赴任者にこの仕事をうまく押しつける技を研究した結果、日本から来た技術指導者を労働力として使うコツを身につけることになります。
また、現地で指導する日本人も、やがて、“現地人には無理、俺が手伝わなければ…”となり、海外の現場で日本人が手を下すことが自分の存在価値であるかのように感じ、結局はその方が現地の仕事から離れられなくなるのです。
本人は親切のつもり、また仕事人間ともなると多少の暇つぶしのつもりで手伝っていても、相手にとっては職業提供程度の扱いとなるのです。
難しい仕事をする日本人も、ほめられると悪い気はしません。
存在価値があるように思えるし、また現地人に任せて、万一トラブルが発生すれば日本人の経営トップから“おまえの指導が悪い!”と言われるのだから、やはり手を出す方が良いということになっていくのです。
“仕方ないから手を出す”という簡単な処置が、やがて現地に技術が定着せず、人を次々送り、送った人の帰りが遅くなるのです。
したがって、海外に出た人達の仕事のアウトプットと伝承方法の中身をはっきりさせて改善させなければ、この問題は永遠に解決しません。
このような状態では、もはや技術移管は遅くなり、現地の人員は減らないままで人件費増加と収益悪化の道をたどることは必定となります……」
とS社のトップに、Mさんは自分の体験と、対策の苦心談などを話したのでしたが、
「まさに当社も同じ問題で悩んでいる。
ぜひ経験のあるところでMさん、支援していただけないか!」
ということになったのでした。
同じ問題に解決策を持たない企業は多いです。
ですが、S社のような疑問すら持たない企業も日本には多いです。
ここでは、「御社もそうですか! 我が社も同じ悩みを持っています」と言ってお互いに慰め合いながら、「○○国へ、飛び回りながらの指導で大変だ!」としています。
ですが、そのうちに人件費の増加や製品ライフサイクルが終わり、10年程度で海外に出た企業の50%が撤退しているという報告がなされています。
特に、現状の製品製造技術者に大精力を注ぐうちに、新製品の開発力の低下を来す未来がここに示されています。
以上、このような問題意識でS社では、この問題に対して海外赴任者のマニュアルを作成するニーズというテーマを持ち上げ、全社的な取り組みを開始する決定をして、Mさんへ依頼をしてきました。
Mさんの指導は、S社の海外赴任者が、海外赴任の命令を受けて、まずどの程度の期間で準備をして海外に出ることになるのであろうか? について調査しました。
すると、その答えは、
「余裕を持ったケースですが、2ヶ月程度国内で海外指導の準備に使います。
ですが、急ぐ場合2週間でした。
また、この間に住民票の移動、荷造り、海外赴任のための諸手続きなど、言葉の問題や親戚・友人・仲間との挨拶、送別会を含めて多忙な日々を送ることになります」
ということでした。
したがって、この話だと、たとえ2ヶ月の準備時間を貰っても、個人的にはとても落ち着いて現地に関する実情を勉強したり、指導すべき準備をしたりする時間はないことがわかります。
なお、筆者を含めIEのような科学的解析・改善方法を知っている者なら、次に示す方法で仕事の準備を効率的に進めます。
ですが、この手法の習得やセンス、経験や先任者からの教育や技術伝承、さらには、マニュアルも持たない場合、はっきり言って、ご本人の気質と能力、経験と気合いに頼り、準備に大きな差を持たせたまま丸投げ状態で赴任することになります。
海外生産指導者が科学的手法を駆使する要件
1. 解析技法が定量的、具体的である。
2. 図や表による解析が、問題と対策の方向を明確にする。
3. すでに国際的に流通しているものであり、解析に納得性が得られやすい。
以上が、科学的手法を海外生産指導の方々が駆使する要件です。
また、筆者の経験からすると、科学的手法の駆使は、仕事の指示、伝達、現地の方々と共同して問題解決に当たる場合に納得性が高く、しかもスピ-ド性が高い。
変に通訳を介して長々とコミュニケーションをはかるより、はるかに質の良い内容で意思伝達ができるため、この企業もこのような方法を利用すべきです。
Mさんにこのようなコメントを話すと、
「まさにその通りです。
S社の専務様、この方はJMAの研修を受け、JMAとのお付き合いも深い方ですが、海外工場におけるご経験が深く、今回私が話した内容に同意され、
“自分は、その具体策を『現地赴任のマニュアル』いう具体的な形で体系化させ、日本側から海外指導のため、赴任や長期滞在する者の技術知見として実務に使い、短期間で日本に帰る対策のツール作成をお願いしたい”
となりました。
これを考案したS社の専務様は、2時間も割いてとくとくとこの対策の必要性を私に訴えられ、私としても何とかしたいと思い、今回の対応となりました」
と筆者に話し、以下に紹介するマニュアル作成指導が開始されました。
S社の専務様に対するMさんのマニュアル作成指導例
では、S社専務様とMさんが進めたお話を詳しく記載することにします。
「マニュアルを作成する目的は、現地に行った日本人が帰国できないという問題の対策です。
現地では技術伝承に時間がかかります。
交代要員を要求しても、日本側に投入すべき人材は少なく、もし無理して投入を続ければ、やがて国内の製品・技術開発が手薄になり、まさに空洞化となります。
したがって、今現地にいる方に頑張ってもらうことになるのですが……。
この対策ツールが今回、Mさんにお願いする海外指導者マニュアルです。
仕事を的確、かつスピーディーに伝える方法の確立が今回のニーズです」
「そうですか、海外で技術伝承をするというのは大変難しいです。
技術を伝えても辞める人がいる。
標準書では書き表せない技術の伝授がある。
それより難しいのは、問題があると日本人が手を出す。
したがって、技術が現地に根づかない。
それより問題の事項としては、日本人がぶらぶらしているわけにいかないという貧乏性のためか、仕事を作って抱えてしまうなどがあります」
「そうなのです。その問題の解決に今回IE+QC+VEを利用したマニュアルづくりを進めたいわけです」
「それは多くの企業にも役に立つ良い策だと思います。
私の経験から見ても、マニュアルと科学的問題解決利用による技術伝承と現場管理は変な通訳より有効です。
ところで、日本での教育期間はどの程度にされるおつもりですか?
逆に日本における訓練は貴社でどの程度の期間をかけておられますか?」
「そうですね、IEは時間分析、方法改善、レイアウトや事務の改善への応用、ORという数学的な解析を含めて、少なくとも1週間程度です。
QCは各種の統計手法と応用を含めて、最低3日程度。
ISOの標準化を含めるとあと2日ほどです。やはり、1週間となります。
VEは実務研修で、やはり原価分析から製品の分析、アイデア発想、アイデアの評価と実務テーマを含めて1週間程度です。
これで全体は約3週間程度となります」
「海外赴任者にその期間は取れないでしょう」
「確かに!」
「せいぜい3日、2日は研修、1日は伝授すべき技術や現地における問題の一部を国内で対策して赴任されるのが良いと思います。
たとえば、定着しにくい技術のポイントの解析、ビデオ撮り、標準書の作成など現地の問題点を事前に把握されて、準備を国内で行ってから現地に行く。
現地に行く準備と共に、教えられたことを使う。
単なる知識教育でない方が良いように思います」
「実務的ですね!」
「ええ、海外に赴任された方が信頼を受けるのは、短期間に成果をあげ、技術伝授した時です。
仕事を早く終え、ブラブラしていて帰りを待つ状態を早くつくることが大切です。
今回のマニュアルは勉強や知識ではありませんから、最初から使う。
同時に、社内事例と共に情報を持参することが大切です。
もう一つ、マニュアルの中身は現地でそのまま使用できるフォーマット集とし、ルーズリーフ式のものが良いと思います。
私もそうしてきましたが、海外で、たとえば時間分析、要点を書き、分析シートを英訳したものを持参していました。
品質改善と故障対策の用紙化もそうです。
事実分析と問題の原理が簡単に現場で記載できて、問題の原因と結果が、1問題-1原因-1対策で記載できる様式を作成して持参しました。
この準備で現地の方々には、この様式を渡すだけで仕事が進みました。
このシートには、問題の原因となる原理図と共にメカニズムを挿絵で記載する方式をつけました。
また、故障や不良の解析と検討、特にコミュニケーシュンにも役立ちました。
VEも同じです。
あるテーマに関して、アイデアの得る方法、評価表の作成法と評価の仕方を示し、表の形式を作成しておけばそのまま使えます。
もし、社内にそのようなもの、またはかつて改善に取り組んだ時に有効だったものがあれば、そのものを題材に様式化されると良いでしょう。
さらに、会議などで意思決定を必要とする内容。
生産の指示や連絡をするものも様式化しておくと便利です。
これらのものを含め、全体で200ページ程度にされてはいかがでしょうか。
バインダーにする理由は、日本側でのサンプルを挟む。
また、現地で行ったことをサンプルとして綴じることで、使った手法や方式にサンプルを蓄積することができるからです」
「それは実務的ですね」
「はい、私自身がやって、便利だったので、実務的だと思います。
現地語に翻訳しておけば、マニュアルと事例集として残り、人が変わっても技術習得が早くできる資料になります。
ただし、会社保管の(秘)書類の扱いをすることが大切です」
「では、早速この話を進めたいと思います」
「少し待ってください。
私がマニュアルを作るのではなく、今回は貴社の方々で作り、使うでしょ」
「ハイ」
「本当に使っていただく項目に対してマニュアル化を図る必要があります。
私が作っては海外で仕事する方は“押しつけや金儲けを目的にマニュアルを作った”と思うでしょう。
また、別の問題として、貴社の海外の事情が私の経験と異なるかもしれません。
さらに、全員参画の意味合いからも、どうでしょう、マニュアルに期待するテーマ、今まで学んだ管理・改善手法で役立っているもの(サンプルも添付)、そして現在困っていること(問題解決したいこと)や、海外から帰ってきた方々が、これだけは必要である! という思いなどをアンケートされてはいかがでしょうか?」
「それは名案です!
使う側に立ったマニュアルになりそうです」
「そうです。
今海外に赴任している方々の問題解決に役立たないことを纏めても、これから海外に赴任する方々には何も役に立ちません。
マニュアルは貴社のもの、販売するのではなく、使って、実務に役立てるものですから、どうしても使う側に立って必要な情報を網羅することが必要になります。
次回お会いするまでにちょうど3週間程度あります。
今の時代はFAXやEメールを利用すれば意見はもらえますから、アンケートを現地から集めてはいかがでしょうか?」
「帰国者はいかがでしょうか?」
「当然、アンケートをいただく対象になっていただいて良いです。
しかし、帰国された方の問題は、当時のことを忘れているという点です。
これだけは考慮に入れてアンケートする必要があります。
昔、苦労したことも“ノド元過ぎれば熱さ忘れる”の原理です。
あえて、何かの引き金があれば思い出していただけますが、アンケ-トに全てを期待するのは多少無理がある点はご配慮ください。
でも、自慢話を含めて、事例と共に情報を集めれば役立つものも多いと思いますので、一応、収集をお願いします」
「ところで、今回はトップ/中間管理者/スタッフ/現場の4つのマニュアルを作りたいと考えていますがいかがでしょうか?」
「その通りです。
ですが、海外の場合、中間管理者の方々は、現地でトップと同じ責務と内容で仕事するケースが多いと思います。
販売戦略などの外部的な仕事を除いては同じだと思われた方がよろしいのではないでしょうか?
少ない日本人管理者で仕事をこなす中身は日本と異なります。
そこで管理者/スタッフ/現場指導者の3つに分けて、貴社の中で役割を決め、先のアンケートをもとにマニュアル化を図られてはいかがでしょうか?」
「なるほど。
では、アンケートをどのようにまとめるのですか?」
「アンケートはコピーします。
そして、はさみで切ってカード状にして、要求をグループ化します。
問題や改善要求を示すグループができたら、次に対策後のアウトプットを決めます。
これを、問題+改善要求グループごとに行います。
要求を満たすようにつくるのです。
これを、先の3つのグループに対し、管理者/スタッフ/現場担当者の誰が行うべきか色分けします。
そして、ストーリー化していきます。
そうしないと、現地の問題解決に即応しないマニュアルになる恐れが出るからです。
このようにして、問題解決をストーリー化したら、今度は問題解決手法の割り付けを行います。
すなわち、IE、QC、VEの原理や細かい内容を勉強するのではなく、短時間の研修で様式を活用できれば良いのですから、一番早くて楽な手法の適用法をここに示していくのです。
たとえば、時間分析や作業手順のノウハウ分析は液晶ビデオを活用した手法の適用が好ましく、分析用紙の書き方より改善の見つけ方、改善後の標準化の仕方、現場への提示の仕方を示す方式です。
PCとプリンターを活用し、要点をビデオフィルムから提出し、要点は音声で吹き込んだものから取り出す。
時間分析が必要ならビデオのカウンターの数値を活用する。
細かい早い動作はスローモーション解析を使って訓練するといったようなことを示し、社内の事例を添付しておけば良いです。
セオリー&プラクティスで記載して現地で指導に使うわけです」
「なるほど!
もう一度お聞きしますが、カードに海外工場側の問題や改善したい課題をアンケートという形で記載し、それを現状海外工場がかかえる問題として整理した後でストーリー化するんですね!」
「そうです。
海外では実務的に問題が解ければ良いです。
IEやQC手法の専門家をつくる狙いではないので、問題解決に一番効果的な方法を整理し、使っていただくことを主体にマニュアル化すれば良いです。
もし、専門的なことを更に勉強する必要があれば、社内の専門家と文献をマニュアルの隅に記載しておけば良いでしょう。
また、マニュアルのストーリー化にも問題~解決に至るプロセスと要点を対策カードという形で並べながら進めていけば、貴社の海外工場の問題解決に一番役立つ解決手順の明示という形になります。
私たちが書を作成するときやっているストーリー化の技術、研修のテキスト作成は、要求をならべ、それに合う資料を集め、全体と中身を見た後で記載の要点をハッキリさせ、書やマニュアルにしていくという方法です。
今回もこの手法を使おうと思っています」
「大体、進め方がわかりました」
「ところで、ですが、管理者/スタッフ/現場担当者の各グル-プごとに担当者の設定が必要になります。
1グループ4~5程度が良いでしょう。
2人だと上下関係ができてしまいますが、3名以上、最大6名だとグループ活動となり有効です。
一般論ではなく、実務論で今回の実務を進めていますから、グループに任用される方々は多少とも問題解決手法に詳しく、海外の経験や、経験がなくても事情が詳しい方々でグループ編成することが必要です」
「今、その点を質問しようと思っていました。
しかし、今の説明で理解しました」
このような会話でS社ではM氏の支援で海外赴任者用のマニュアル作成がスタートしました。
MさんがこのようにS社の専務様にお話した理由は、次のような心配があったからだそうです。
「海外赴任者のマニュアル作りですが、私が実際に過去行った経験をお話ししつつの討論でした。
ですが、S社の専務様は、このようなマニュアルを理解され、早急に作り、現地への技術移転を早急、かつ確実にしようとお考えになったようです。
一般に、IE、QC、VEは現場・管理改善の効果ある手法として活用されています。
ですが、海外赴任者は全てを知っているわけではないです。
また、他社の取り組みを見ていると、自己流、問題解決の遅い珍妙な方法を用いて苦労しながら仕事を進める方式が多いです。
たとえば、時間分析に紙と鉛筆、時計を使う方式です。
この方法は基本であり、IE手法を最初に習う時には良い方法です。
ですが、実務ではビデオ+ビデオに内蔵した時計機能の利用で十分ですし、早くわかりやすいからです」
以上のようなS社とMさんの討論で海外工場指導マニュアルが出来上がり、海外指導効率が5倍以上になったそうです。
また、「管理者/スタッフ/現場担当者という項目にグループが編成され作成されたマニュアルの項目は以下の内容となった」というお話でした。
〔管理者研修のメニュー〕
国や管理者の差異なく管理システムを具体化するため
1. TQM(顧客志向の文化、弛みなく改善を進める方式)思想と実践を明示する
2. 工場管理、運営について
CS(顧客志向の意義と用件)/継続的改善の意義と用件/全員参画のための方針展開をベンチ・マークと共に示す
3. 工場運営の要点管理
改善項目の内容、運用、評価について
4. 品質管理と改善
CS/他社比較と動向/日本優良他社(異業を含む)との比較
5. コスト分析と改善の要点
損益分析/経済計算(B/S、P/L分析)/評価項目/管理資料とその機能(様式の設定と活用)/P-D-C管理の要点/中期経営計画策定法とチェックポイント
6. 納期改善対策と生産管理
生産計画と評価法/工場内生産管理システムと運営の要点/協力工場運営/異常処理
7. 人材育成と教育
体系-アウトプット-能力評価-カバー率
8. コミュニケ-ション
会議/問題解決手法の活用/コミュニケーション手段と効果
9. 人事と組織(責任体制)
10. 安全と環境対策
11. 日本人に対する現地のトラブル・不満の事前解消対策
〔技術スタッフマニュアル〕
現地への技術移転をスピーディーに行うための要件
1. 技術スタッフ育成の目的
TQMにおける役割と機能、投入技術手段の位置づけの明確化とトラブル・シューティングの的確化・スピード化
2. 技術移転
赴任者のアウトプットを決め、海外赴任とする。なお、本人/教えられたスタッフ/現地マネージャーの承認を得て技術移転を完了とする
3. 技術問題
死亡診断的な対策は適用しないで、スピーディーな問題解決とレベル向上を主体とした方式を投入する。IEQC/VEの総合的活用を図る
4. 現地設備導入
立ち上げチェックリスト
5. 技術レベル達成評価と苦心談(適用の要点、問題と対策)
6. 現場への技術移管P-D-Cの内容と管理表、終了承認書
7. 日本から持ち込んだ設備の立ち上げ-軌道に乗りメンテナンスまでの用件
〔現場S/V(管理者)の育成〕
現地管理者が行う管理という仕事の内容を明確化し、早急に現場管理~改善指導が出来る力量を身につけるための項目
1. 方針管理と役割と具体的な活動への展開の理解
2. 労務管理
離職率リスク対策/スピーディーに仕事の管理が要点の理解と習得/スキル・アップのコツと管理/査定(ボーナス・ペナルテイ制度)
3. 生産管理
P-D-Cの理解/計画-実績差異のスピーディーな対処
4. 原価管理
1個いくらの理解、¥/分の理解と活用、目標未達事項の予知対策、問題発生時の即時対策
5. 品質管理
不良・ヒヤットの減/指示書の作り方と運用/標準化対策
6. 設備管理
設備の点検・整備/トラブル・シューティングの進め方(標準化、フローチャート)
7. 現場管理の方法と現場診断
現場管理項目の実践とレベルの時間管理(日報管理)/異常発生時の対策
8. 語学力対策
日本語/現地語の対比表準備
9. 現地文化の理解
10. 現場実務伝承について
項目/内容/計画/実績/承認(本人/被研修者/現地マネジャー)
コメント
MさんがS社を指導され、マニュアルを作成し、海外指導という漠然とした仕事を明確にして、効率化を図る対策は国内空洞化対策でした。
海外への技術移管・伝承というグローバル対応問題をムード的に行う企業と、科学的に進める企業とでは、投入人件費と時間など多くのムダの軽減に違いが出るはずです。
筆者も同ニーズから同対策を実務で行ってきたため、S社で今回の取り組みが大きく歓迎され、効果が発揮されたのを理解した次第です。
海外生産には指導、すなわち人材投入の戦略が必要です。
次の表はその一例であり、アルミホイル工場の海外生産スムーズ化に実施した内容ですが、このように中長期にわたる人材育成に対しては、各局面で何が必要かというと、アウトプットを明確にした人材投入を図るべきだと考えます。
▼日本からの技術移管を系統的に進めた例
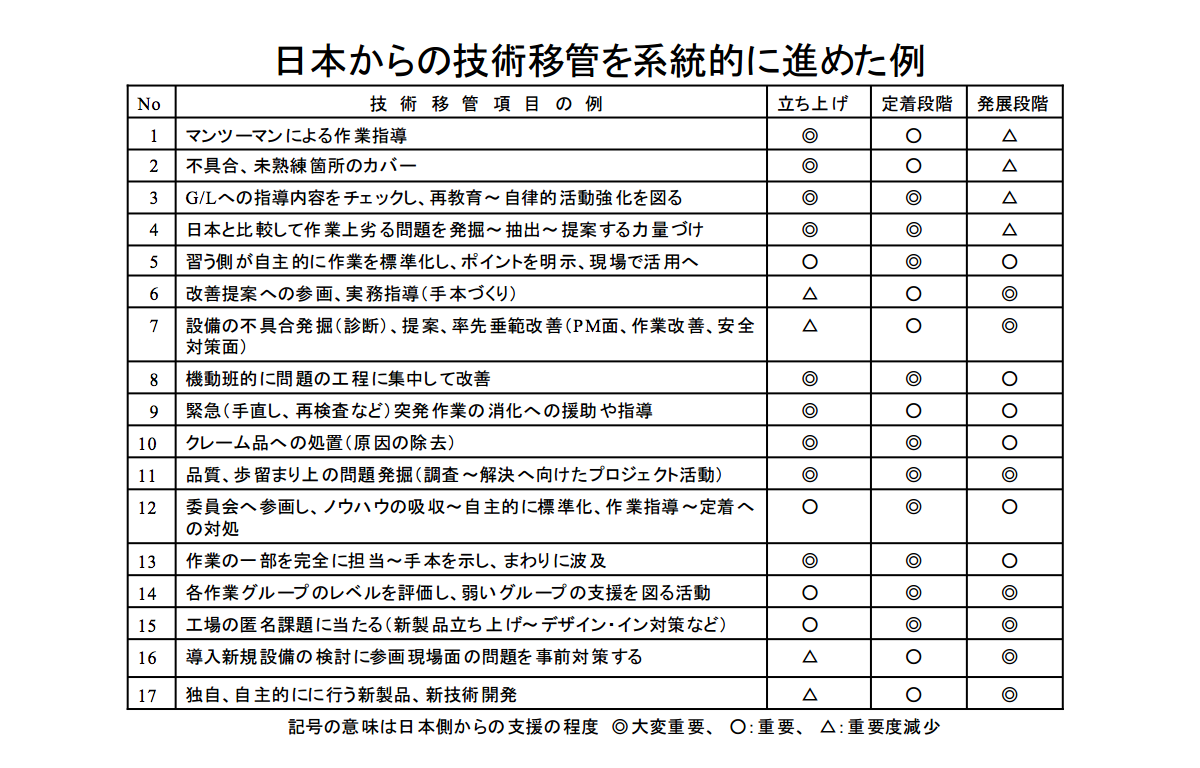
「頑張った」という言葉は海外赴任者や指導者、誰でも言います。
しかし、確実に海外工場でモノづくりが図れるかがテーマです。
この面の事例や自慢話は多くの著書や文献に見るのですが、それが効率的か否か、が同問題に当たる方々にとっては重要な課題になります。
また、少子高齢化が激しく進む中で、あえて名をつけると、この『海外指導仕事術』に対して科学的手法の活用と良否を評価した技術知見の投入が必要です。
現在のようにこれだけ国際化が進み、既に多くの方々が海外経験を持つ環境下にあっては、ご本人にこの対策を丸投げするのではなく、同問題を抱える皆様には、ぜひ、MさんがS社を支援したような実務的な内容を実施され、海外指導仕事術という局面から実際に役立つマニュアルを作成していく方式を、お勧めしたいと考えます。
また、海外工場への早期技術伝承はひとつの技術です。
海外指導仕事術は効率と有用性が高く求められるテーマですが、その問題の把握と効果的な解決法の利用こそが重要と考えます。