『改善ぷちセミナー』標準化の4つのC
※当コンテンツは『面白狩り』の提供でお届けいたします。
1.標準化とルール化は違う
ここでは標準化についてお話します。
標準化と言うと、みなさんどんなイメージをお持ちでしょうか?
「あるべき姿を標準として、全員に守らせること」
ほとんどの人がそんなふうに考えています。
でも、これは標準化ではありません。
専門家による文献にはこんなふうに書かれています。
「工業製品の品質や形状・寸法・成分などに一定の標準を定めて互換性を高めようとすること」
互換性というのは互いに取り換えがきくこと。
例えば、製品の部品や形状などを標準に合わせて作っておけば、壊れてもすぐ交換できます。
互換性が高まれば、種類が少なくなって量産化が可能になりますから、原価も安く抑えられます。
これが標準化です。
ただルールを決めて守らせるのとは違いますよ。
それから、こんなことを言うと、みなさん、びっくりすると思いますが、標準が正しいとは限らないということも覚えておいてください。
たとえJIS(日本工業規格)に定められているとしてもです。
それは、標準化のプロセスを知ればわかってきます。
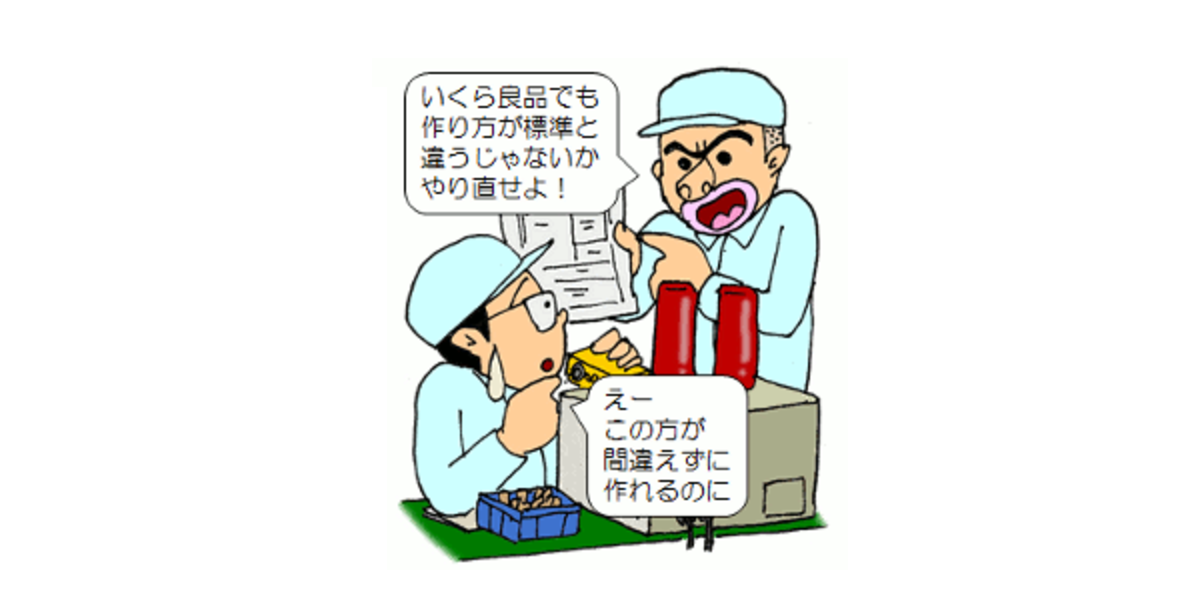
2.標準化のプロセス
標準化は4つのCというプロセスを踏んで進めます。
4つのCなんて耳慣れないでしょう。
それは当然で、これは私が勝手に作った言葉なんです。
なので、一般には全く通じませんから、気を付けてくださいね。
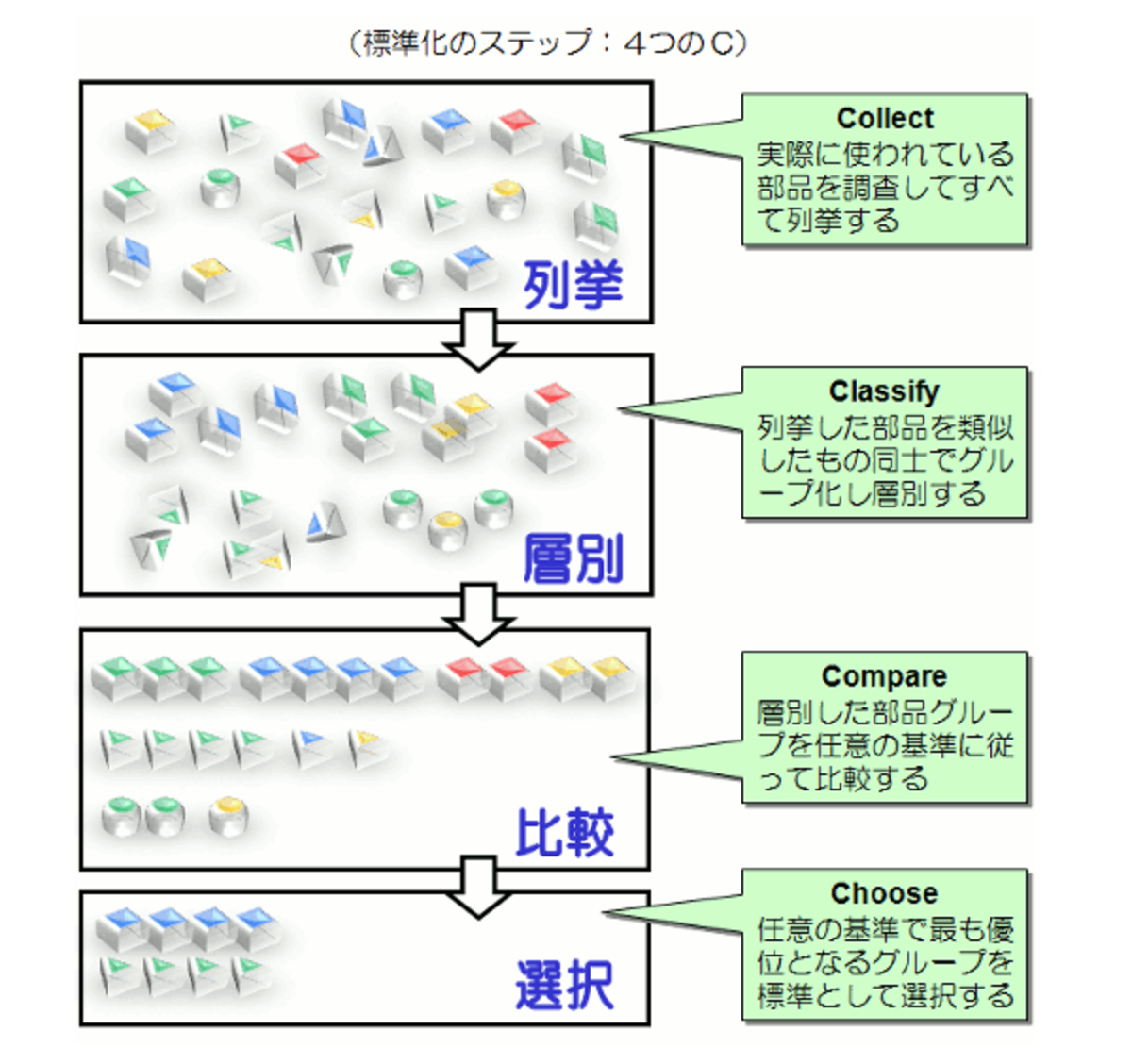
これが標準化という活動です。
ルール化とは全然違うでしょう。
もし、みなさんがこれから標準化を進めようとしておられたり、社内標準を作り直そうとしておられる場合は、4つCで正しく標準化を進めてください。
3.標準化の例
標準化の定義では互換性が効果であるとされています。
でも、最大の効果は、ムダをなくして仕事の見通しを良くするということです。
ここでは、そのような標準化の例を3つ挙げておきます。
1 製品の標準化
製品開発当時に急いで立ち上げた組立ラインが、受注が好調で止めることができず、現在まで何の変更も加えずに流していました。
しかし、停滞が頻繁に発生して明らかに効率が悪く、改めてライン編成を行う必要に迫られていました。
そこで、量の多い標準品のラインと、仕様が特殊な特殊品のラインとに分けて流すことしました。
どれが標準品でどれが特殊品なのかを調べます。
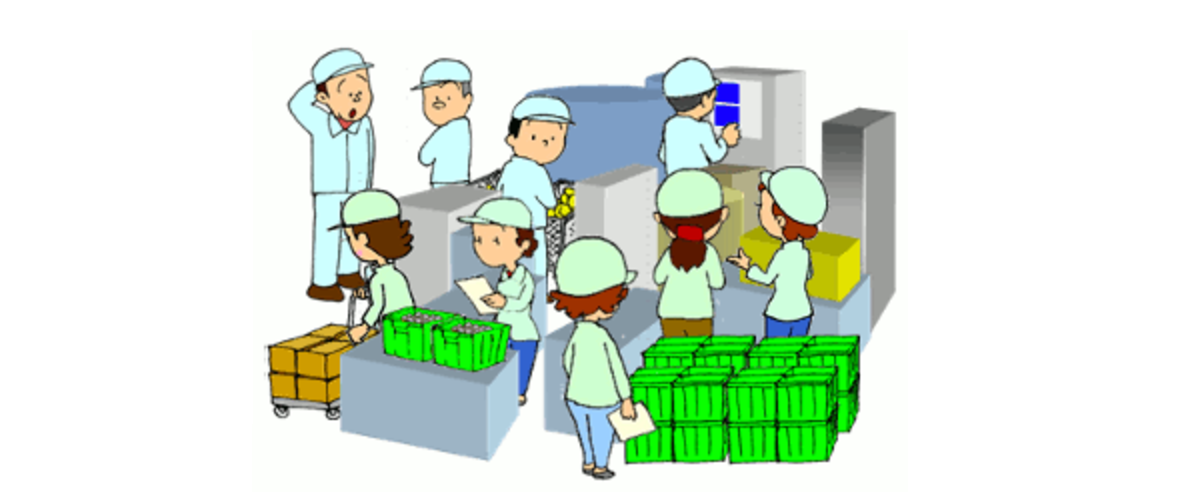
Collect ~列挙する
まず、製品の品種を洗い出します。
過去1年の出荷実績がある品種をリストアップしてみると、約200品目の製品が作られていました。
Classify ~層別する
洗い出した品種を分類していきます。
設計で基本仕様に基づく製品コードが付けられていたので簡単に分類できました。
Compare ~比較する
過去1年の生産実績データから、生産量の多い順に品種を並べてPQ分析を行います。
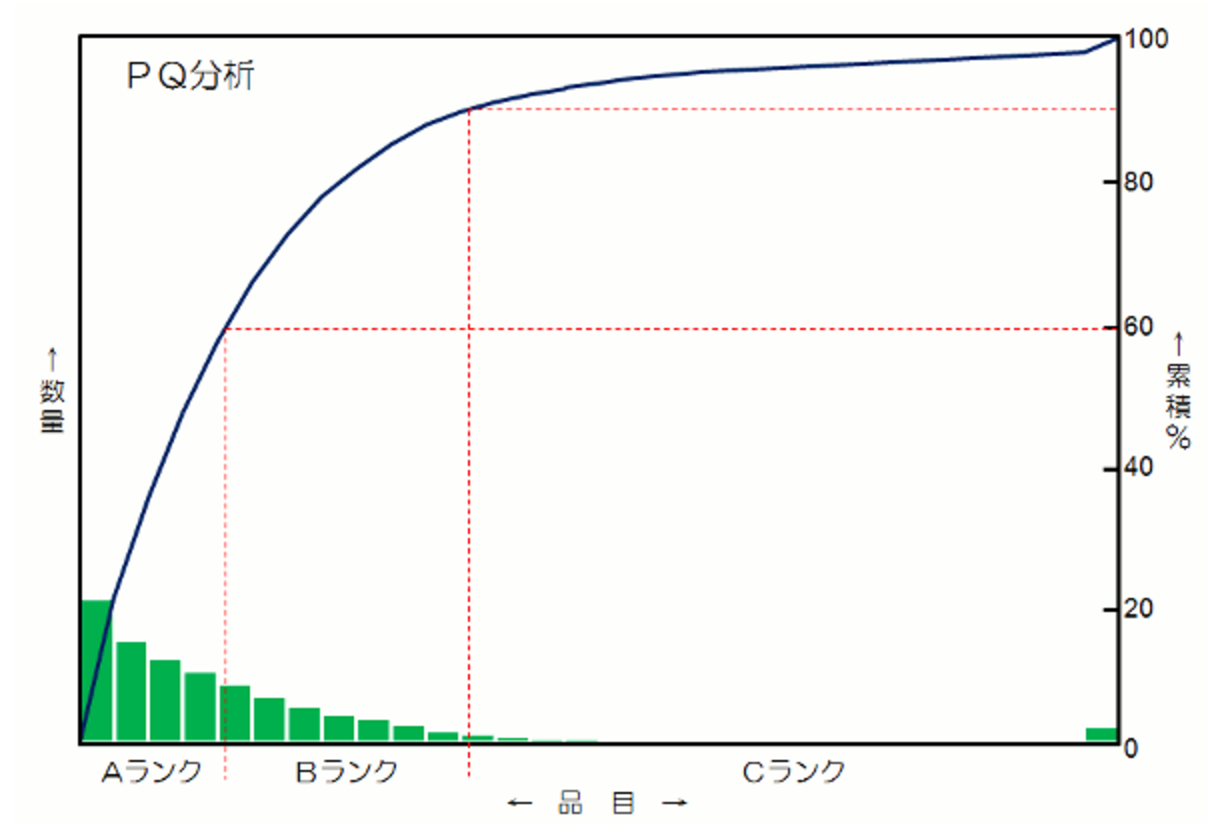
PQ分析とは、品目(Product)を数量(Quantity)の多い順に並べたものです。
考え方は品質管理のパレート図と同じですが、生産管理や工程管理ではPQ分析とかABC分析といった呼び方をします。
全体の60%と90%のところで境界を設定し、それぞれA、B、Cとランク付けを行いました。
Choose ~選択する
Aランク品はよく流れている品種で、これを標準品としてラインを整備することにします。
逆Cランク品は年に1~2回の注文しかないので特殊品としました。
中間のBランク品は、当面は特殊品扱いとしましたが、段取作業を改善すれば標準品と同じラインで流せそうでした。
また、生産工程を調べれば、Cランク品の中にも標準ラインで流せる製品があるかもしれません。
これらは、次の課題として取り組むことにしました。
2 作業の標準化
資材担当者は、生産に用いる部品・材料を取引先に発注し、納期通りに納めさせるための管理を行っています。
この度、生産管理のシステム化を図るために、資材担当者が行っている作業のやり方を標準化することになりました。
Collect ~列挙する
資材担当者は6人で、生産ライン別に担当が分かれています。
それぞれ前任者からの引き継ぎで行っているため、やり方はバラバラでした。
とにかく、みんなの作業のやり方を全て出すことにしました。
Classify ~層別する
調べてみると、Fさんだけが単票に発注データを記録するやり方で、あとの5人は一覧表を作って作業していました。
Compare ~比較する
今まで他の担当者のやり方を知らなかったので、みんな興味津々で作業のやり方を見せ合い、それぞれ試してみて長所や欠点を調べました。
Choose ~選択する
一番簡単で使いやすかったのがCさんの表でした。
ただし、そのままでは共通に使えないので、他の表の長所を取り入れて標準としました。
また、発注してから納期までの期間が長いものは、Fさんのカード方式がやりやすいと感じたので、これも標準のやり方として残すことにしました。
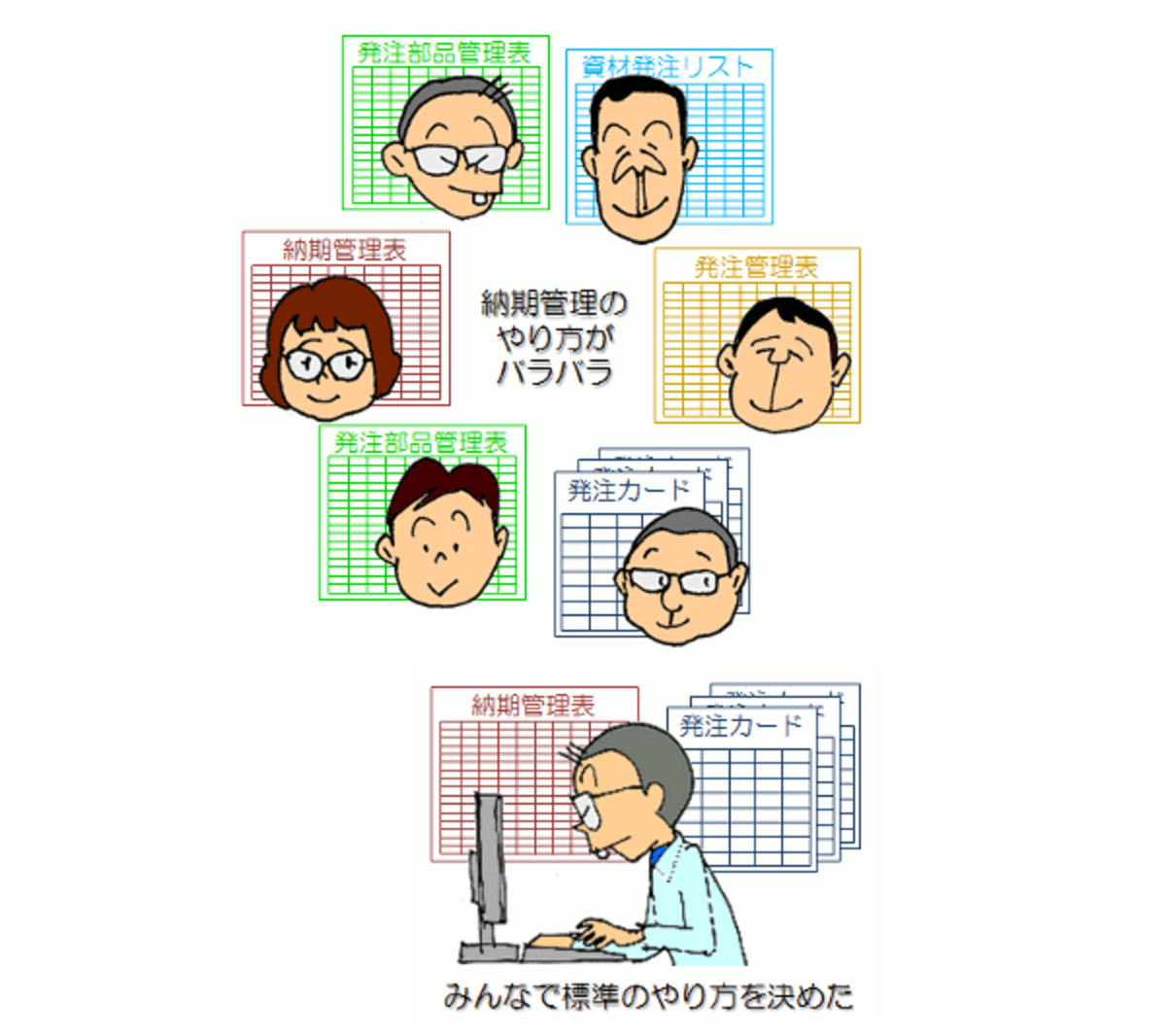
3 工具の標準化
大型機械組立メーカーの例です。
部品は外作が基本ですが、精度の必要なものは社内の切削部門で作っていました。
ところが、組立完成品の高性能化に伴って内作部品が多くなり、多品種少量生産に拍車がかかっていました。
最近は組立に間に合わなかったり不具合品が頻繁に発生して、生産のコントロールができなくなっているというのです。
実際の作業を調査していくと、同じ部品でも作業者によって加工方法が異なり、使われている工具もバラバラでした。
工場の中に様々な種類の工具が散在して混沌としていました。
とにかく、作業者の周りを整理して、見通しの良い工場にしなければなりません。
Collect ~列挙する
まず最初に「工具の棚卸し」を行いました。
使用中のものから、棚や台の上はもちろん、作業者専用の棚の中まで見せてもらって、工場内にあるすべての工具を調べ尽くしたのです。
仲間と手分けして調べた工具は5000種類に及びました。
丸3日かかった棚卸しも大変でしたが、ノートの記録もかすれた文字が油で汚れて、データのまとめに気が滅入ったものです。
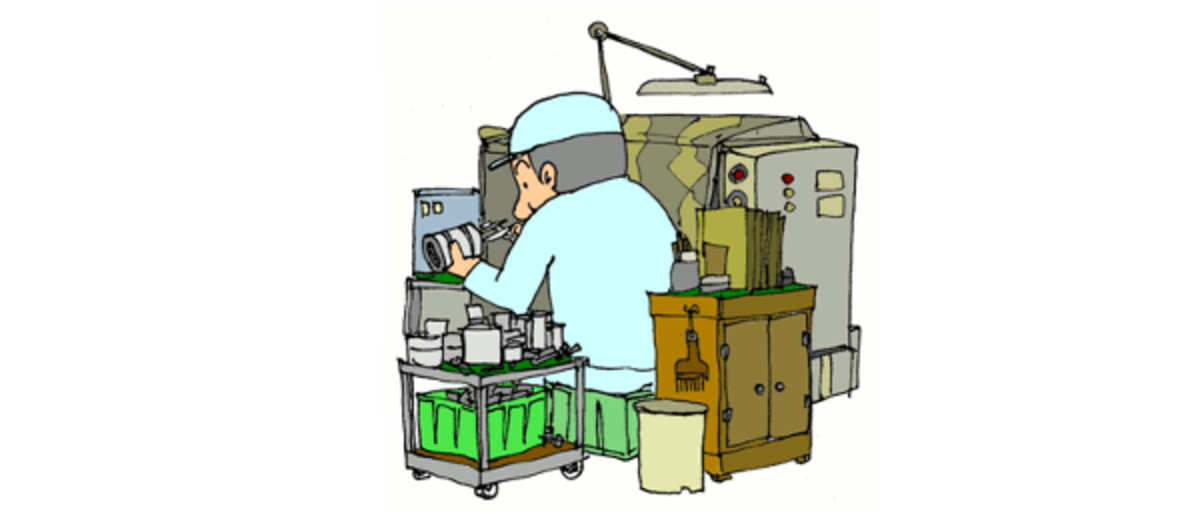
Classify ~層別する
次に、洗い出した工具を分類しました。
ほとんどの工具はJISの標準品が使われていましたが、治具はすべて作業者の手作りで、数もたくさん作られていました。
また、難しい形状を削り出すために、刃先を変形させた異形刃具もよく使われていました。

分類ができたところで工具一つ一つに社内用のコードを付けました。
工具の分類をしただけでもかなり見通しが良くなりました。
Compare ~比較する
JIS標準の工具だけなら、工具係が員数管理やメインテナンスをすることができます。
ところが、実態がよくわからなくて、工場の中を煩雑にしているのが治具と異形刃具でした。
特に治具は、同じ形状のものがいくつも作られて埃をかぶっており、中には錆びているものもあります。
そこで、これらのどんなものがよく使われているのかを調べることにしました。
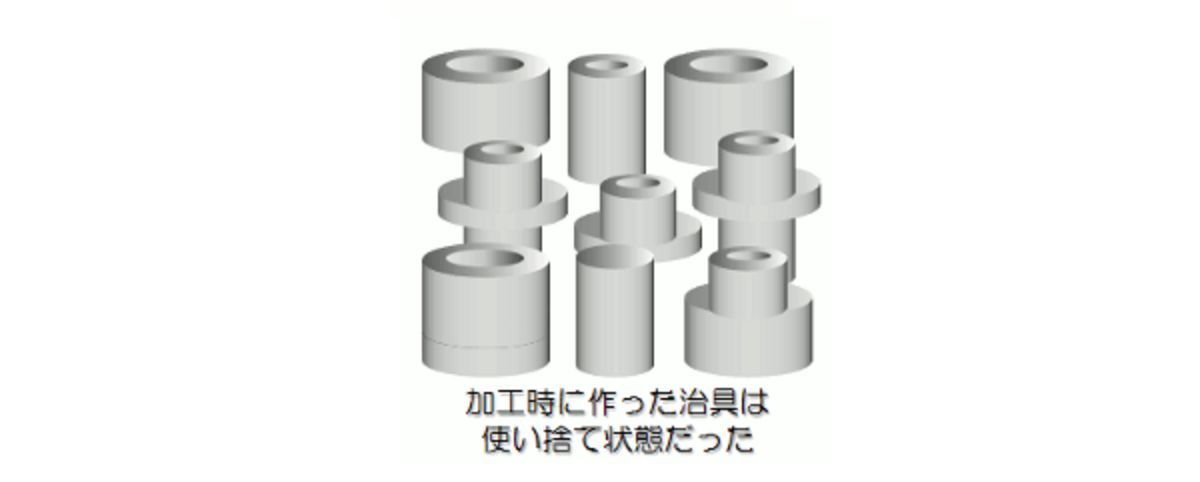
Choose ~選択する
同じ材質・形状のものが複数ある治具は、よく使われていると考えることができます。
これらは、以前作られたものを再利用すれば良いのですが、いつも作りっ放しで適当な場所に放置しているため、探すよりも作った方が早いという理由で、こんなに増えてしまったのです。
そこで、よく使われる治具と異形刃具は社内標準として工具室で管理することとしました。その他の特殊工具も履歴を残して再利用できるようにしました。
この結果、新しい治具が作られなくなって材料費が軽減できました。また、加工方法の情報交換がされるようになって、作業の個人差が少なくなり品質が安定してきました。
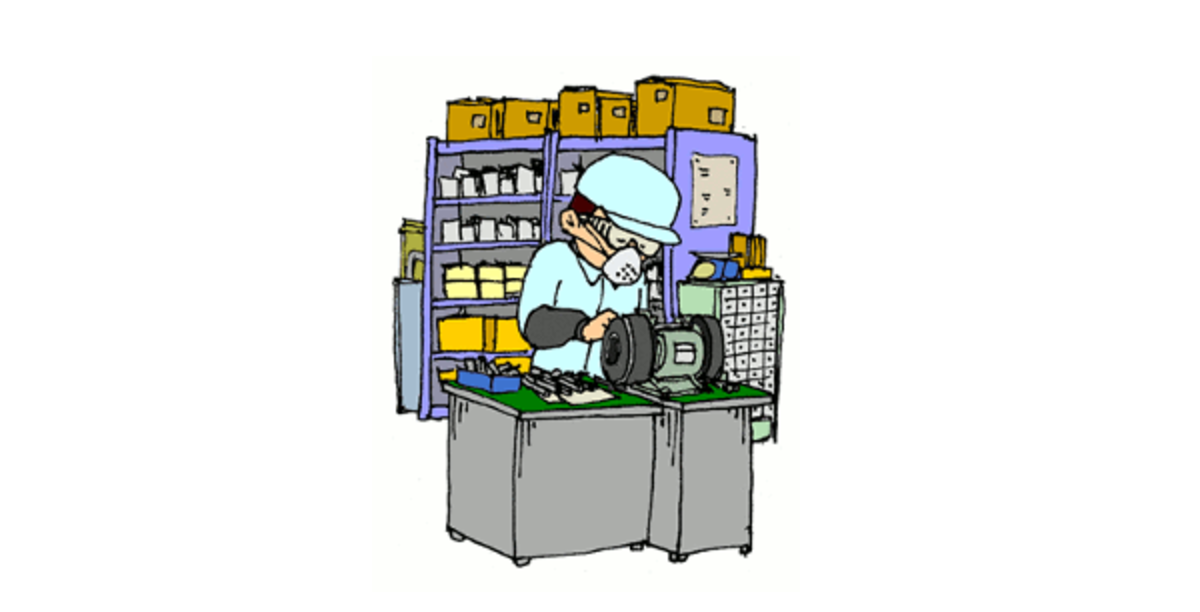
4.標準化後の3つのプロセス
4つのCで標準化を進めた後、標準を有効に活用するために、作る・守る・変えるという3つのプロセスが必要です。
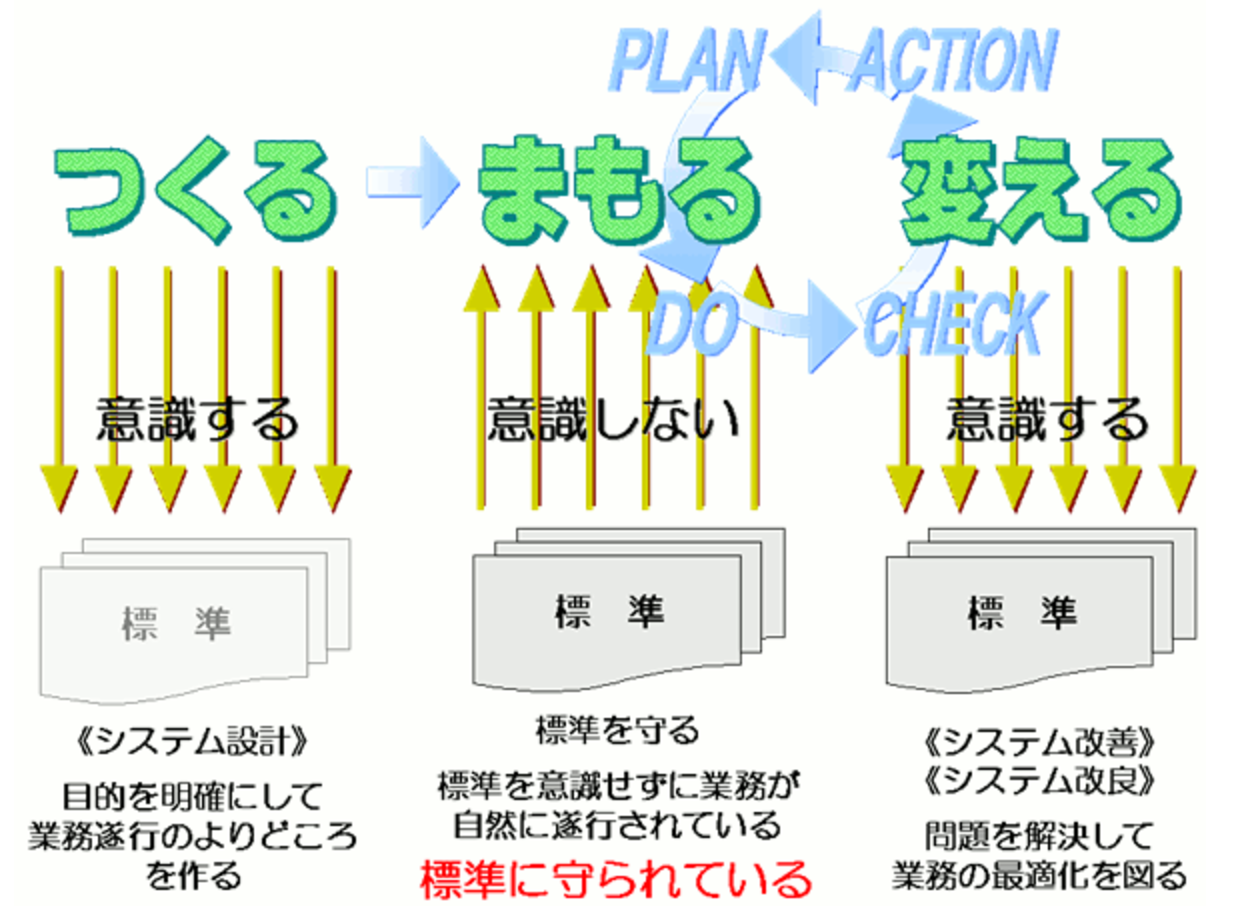
1.作る
4つのCで選択された標準を、テーブルやマニュアルのような様式を決めて、マスタ化、文書化を行います。
これによりみんなが標準を共有することになります。
2.守る
業務を遂行するときには標準を遵守し、標準と異なることをしてはいけない。
ルール化であればこれで正しいと言えますが、標準化とは違います。
標準を意識しなくても標準通りの業務が自然に遂行できている、とするのが標準化の考え方です。
そんなことできるわけないと思うかもしれません。
でも、4つのCをちゃんと行えば、現状で最も合理的で楽な方法が標準になります。
それはみんながやっている方法ですから、特に意識する必要がありません。
迷ったときに参照すれば良いし、新入社員のように慣れていない人は教育訓練でできるようにすれば良いのです。
この「守る」というのは、むしろ標準がみなさんを守っているという意味なんです。
3.変える
通常、作業者は標準と異なるやり方をしようとはしません。
なぜなら、いつもと違うことをしても、結局標準よりも良い結果は得られないからです。
ところが、いつも通りにやっているのに正しい結果が出ないとか、経営方針で現状より高い結果が求められるというような場合があります。
前者の場合、その原因を突き止めて、標準を変える必要が出てくるかもしれません。
また、後者の場合は、現状を改善して標準を変えなければなりません。
冒頭でお話した標準が正しいとは限らないとは、このことを言います。この標準を変えるプロセスは、4つのCと同様にみんなで協力して行います。
標準を変えたら1.に戻って標準を改訂します。
この作る・守る・変えるの繰り返しで、標準のPDCAサークルが回転し、業務がレベルアップしていくのです。
5.標準化が望ましい事項
現在では、日常生活で利用される工業製品のほとんどについて標準がJISにまとめられています。
このような公的規格を利用することによって、安く品質の良いものを作ることができますが、それだけでは差別化ができません。
個々の会社が持つ技術は公的規格を超えた固有のものです。
そこで、会社の中でも標準化を進め、固有技術やノウハウを社内標準にして利用しているのです。
社内標準が社外秘としての扱いになるのはこのためです。
一般に、次のような事項について標準化しておくのが望ましいでしょう。
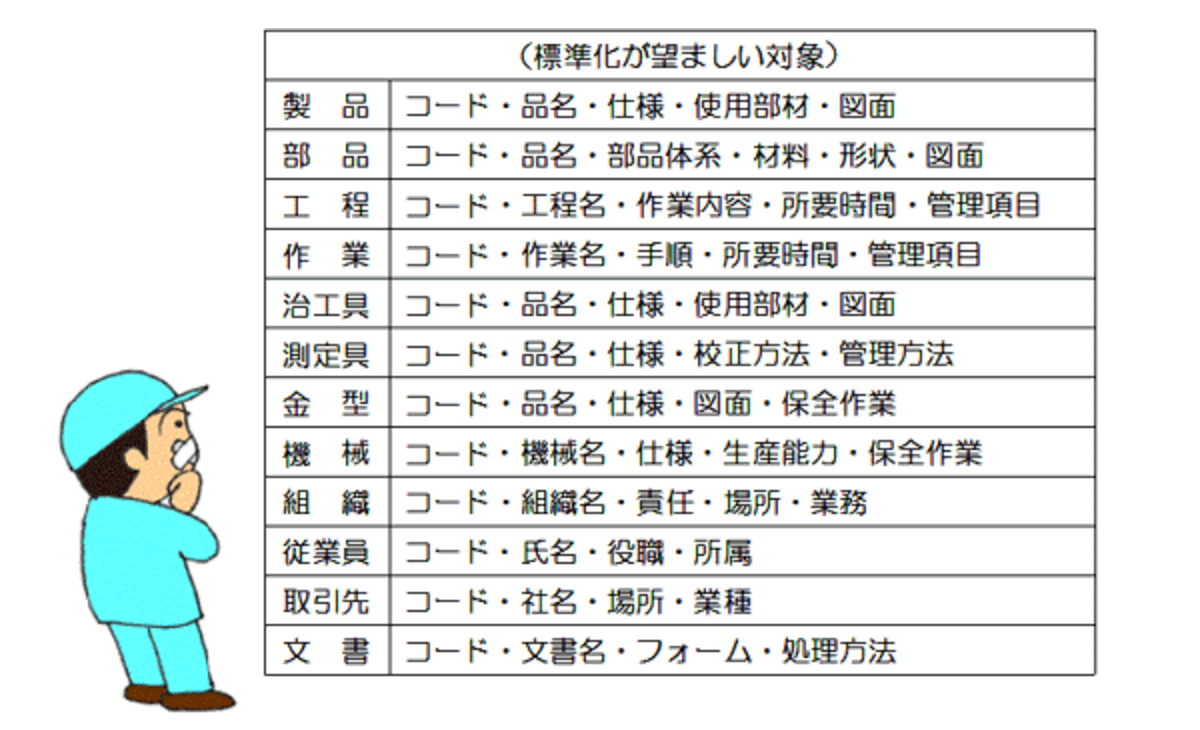
例えば、生産ラインや管理システムを立ち上げたり、オートメーション化を図るというような場合には、標準化は不可欠です。
ところが、標準化は根気よく地道に進める活動ですから、どうしても結果を急いで端折りがちになります。
これは間違いなく挫折しますから、胆に銘じておくこと。
公的規格や社内標準を、みなさんは普段なにげなく使っていますが、それらはすべて、たくさんの人の長期にわたる苦労の末に確立したもの、ということを忘れないでください。