『改善ぷちセミナー』工程分析について
※当コンテンツは『面白狩り』の提供でお届けいたします。
1.工程分析とは
工程分析はIEの基本中の基本となる手法で、これとナナトヤをしっかりと使いこなすだけで、だれでも簡単にかなりの改善成果を上げることができる伝家の宝刀です。
ゴチャゴチャした堅苦しい説明は抜き。
まず、下のような図を見たことあるでしょう?
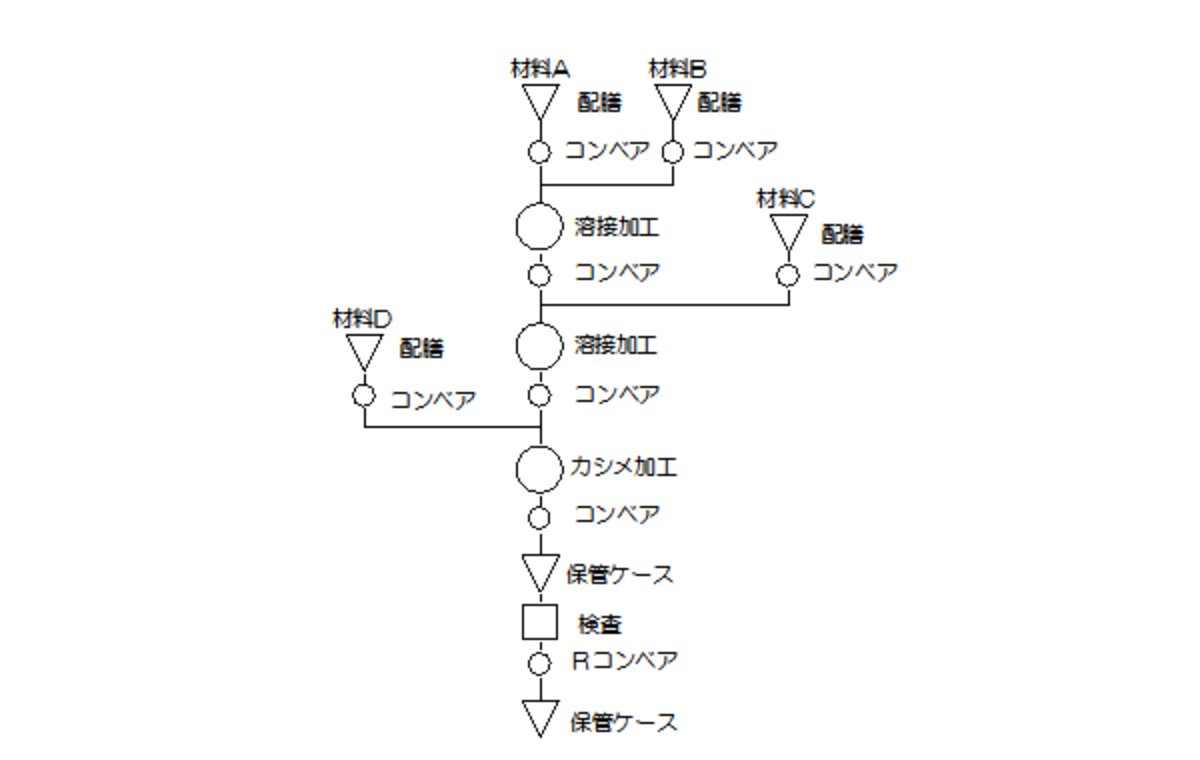
これが工程分析です。
これは、ある電気部品の組立工程を分析した例です。
それぞれの記号の意味は
▽:部品が何もせずに置かれている状態
○:移動している状態
○:加工や組立などで変化している状態
□:検査してる状態
ということです。
材料A、B、C、Dがコンベアに乗って溶接され組立てられてケースに保管された後、検査されて再び保管されるまでの流れを示しています。
組立てラインの工程を逐一言葉で説明するより、このように記号を使ってフローチャートにすれば、だれでも理解しやすくなりますから、みんなで改善を進めるときにはとても便利なツールになります。
まず最初は、工程分析ってこんなもんだというイメージができたら十分です。
次の話に移りましょう。
2.製品工程分析と作業者工程分析
ときどき混乱して何を分析しているのかわからなくなってしまう人がいるので、最低限理解しておくべきことを説明します。
きちんと押さえておきましょう。
一口に工程分析と言いますが、分析対象が製品の場合(material type)と作業者の場合(man type)とで大きく分けることができます。
前者を製品工程分析、後者を作業者工程分析と呼びます。
ご覧のように、製品工程分析はツリー状、作業者工程分析はシーケンス状に表現されます。
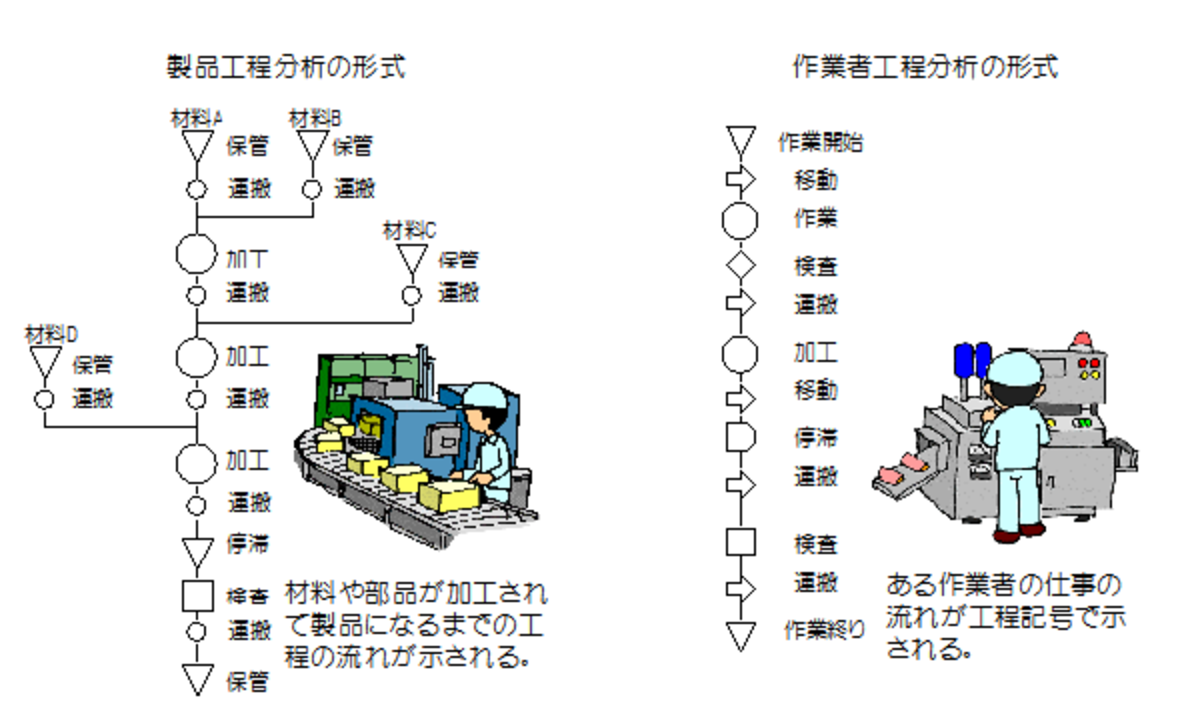
製品工程分析は、主として生産期間の短縮を目的として行われ、ライン編成やレイアウト改善などでは不可欠な手法です。
一方、作業者工程分析は作業のムダ排除や少人化の改善などで使われます。
使われている記号が少し異なることに気付いたと思いますが、基本的には上で説明した4つの要素だけです。
ただし、必ずこの記号を使わなければいけないというものではありません。
要するに4つの要素をわかりやすく表現できれば良いのです。
一般的には、JISで示されている下のような記号を用います。
応用記号のように組合せても構いませんが、実際は基本記号だけのシンプルな表現の方が使いやすいと思います。
参照する人がわかるようになっていれば良いのです。

3.工程分析のやり方
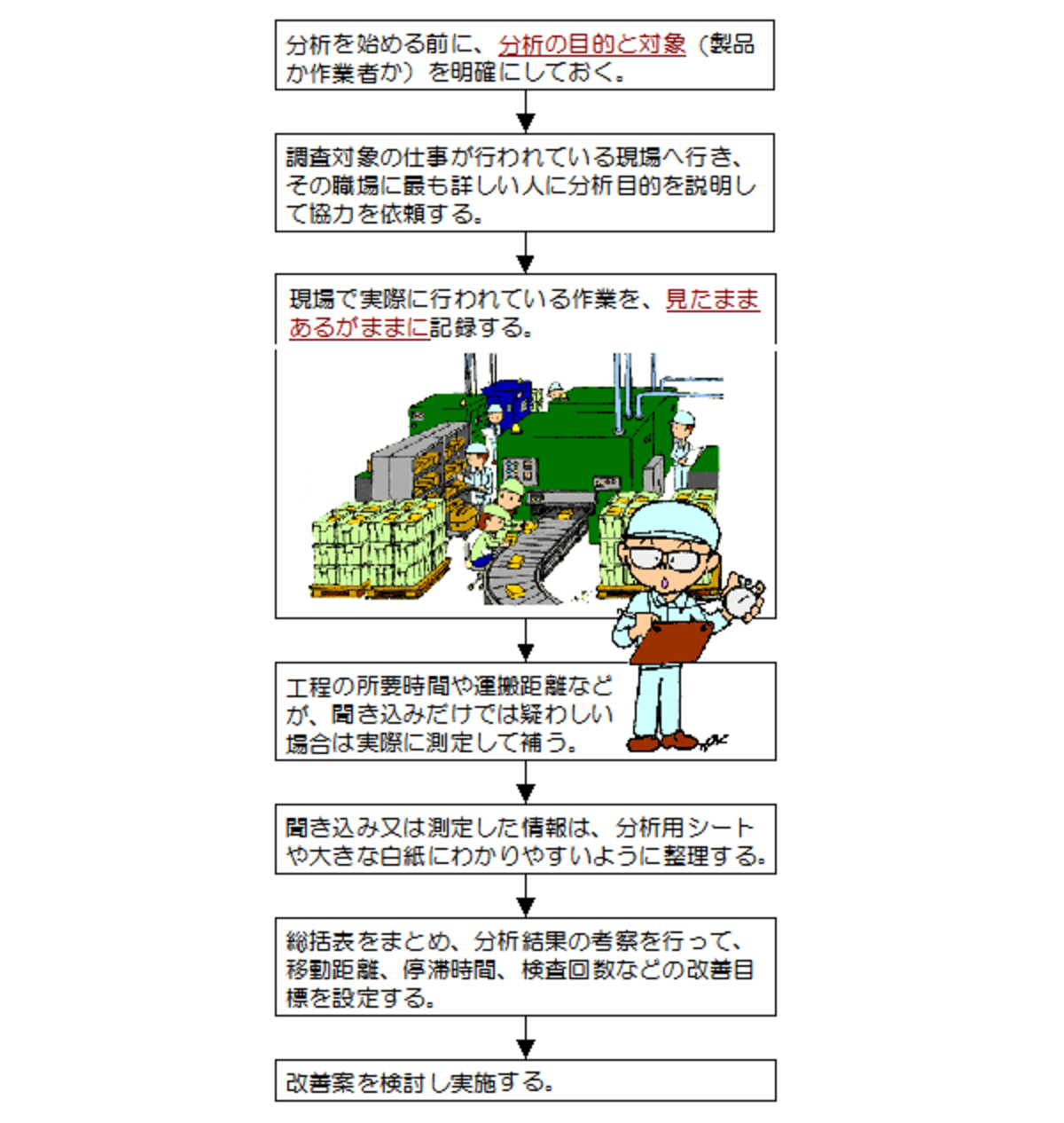
分析する場合に注意する点を挙げておきます。
1.途中で分析対象を変更しないこと
分析の目的さえしっかり押えてあれば間違えることはありませんが、分析をすることが目的になっているとこのような混乱を起こします。
2.区分の大きさを予め決めておくこと
作業の性質から考えて、どの区分に含めるべきか判断に悩むような作業の取り扱いを決めておきます。
例えば、運搬前後に現れる荷造りなどを分けて記録するか、運搬の中に括ってしまうかです。
3.必ず事実を確認して記録すること
あるべき姿や標準類に書かれてあることを記録したら分析にはなりません。
また、現場の人に聞いた情報でも、事実確認を怠ってはいけません。
4.目的に応じた情報収集を行うこと
参考書に載っている例を見ると、記号の横に事細かい補足データが整然と書かれてあるので、これをまねてきれいに書こうとしがちですが、やりすぎると、途中で分析目的が見失われてしまいます。
目的を踏まえた最低限の情報で十分です。
5.初めからきれいにまとめようとしないこと
分析はあくまで分析です。
ノートになぐり書きの分析表でも、目的に合っていれば良いのです。
きれいにまとめるのは、報告とか発表の際に必要と思ったらやってください。
6.必ず総括表を作成して考察をする
分析のやりっ放しが一番いけません。
工程分析表を清書するようなヒマがあったら、すぐに総括表を作成して考察を加えてください。
この方がよっぽど大事です。
下の例を見れば、やたらに運搬回数が多く、停滞時間もバカにできないことがよくわかります。
これらのムダの削減で相当の生産性向上が見込めます。
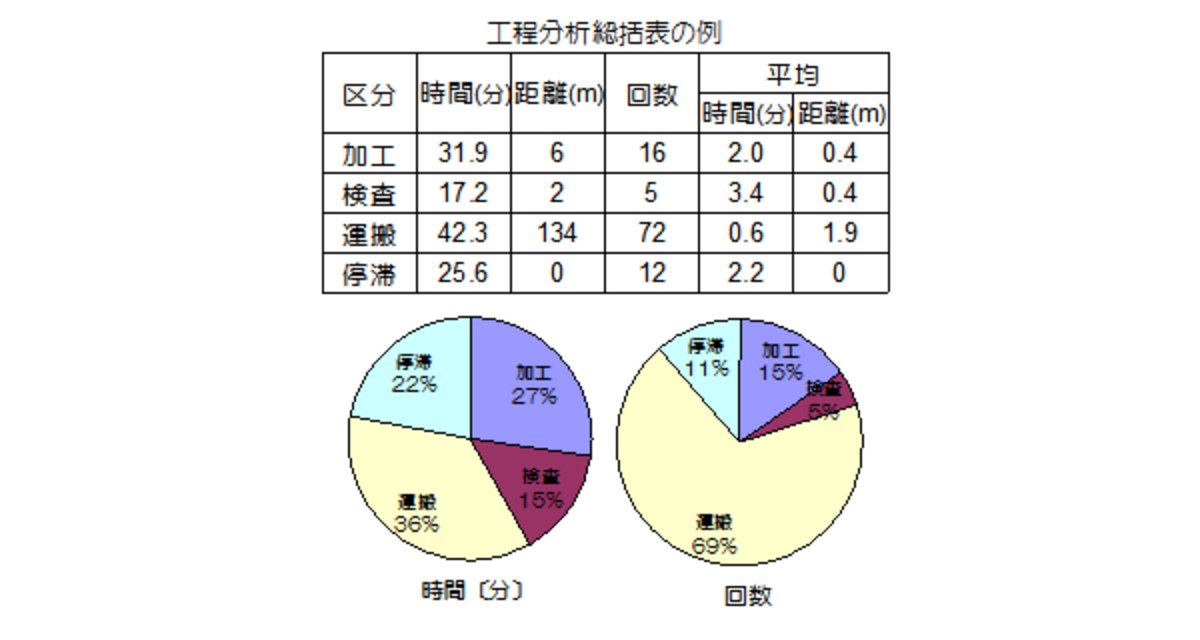
7.一度の分析だけで終わりにしないこと
同じラインでも、人員配置やレイアウト変更、新規設備の導入などのタイミングで、チェックし直してみると、新しい改善点が見つかります。
1回やったから良いというものではありません。
4.工程分析を基にした改善の考え方
1.付加価値を生んでいる割合を大きくする
4つの要素の中で実際に付加価値を生んでいるのは加工だけです。
残りの3つは削減すべきムダな要素ですから、いかにしてこれらをゼロにするかを考えなければいけません。
ただし、検査は品質保証上の理由でやむを得ず行わなければならない場合があります。
したがって、最初に取り組まなければいけないのは、まず、運搬と停滞を必要最小限までいかに削減するかということです。
改善の優先順位を示すと下のようになります。
ただし、実際の改善活動は必ずしもこの順番で進められるわけではなく、コンカレント(同時進行)に行われるのが普通です。
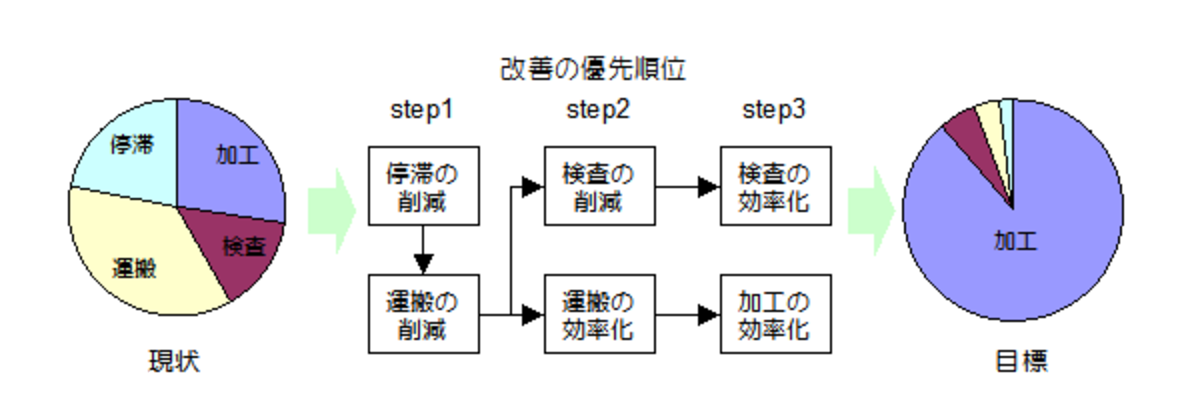
2.ナナトヤ(ECRS)を使って問題解決を進める
改善の定石として知られているものがECRSです。
問題解決のヒントになるので覚えておくと便利です。
英語が苦手な人のために勝手にナナトヤという名前を付けています。
ナ:ナクス作戦(Eliminate削除)=まず、なくせないか? を考える
ナ:ナガラ作戦(Combine結合)=結合できないか? 連続してできないか? まとめられないか?
ト:トリカエ作戦(Rearrange再編成)=交換できないか? 作り変えられないか? 視点を変える
ヤ:ヤサシク作戦(Simplify簡素化)=簡単にできないか? 治具にできないか?
3.各要素の改善ポイント
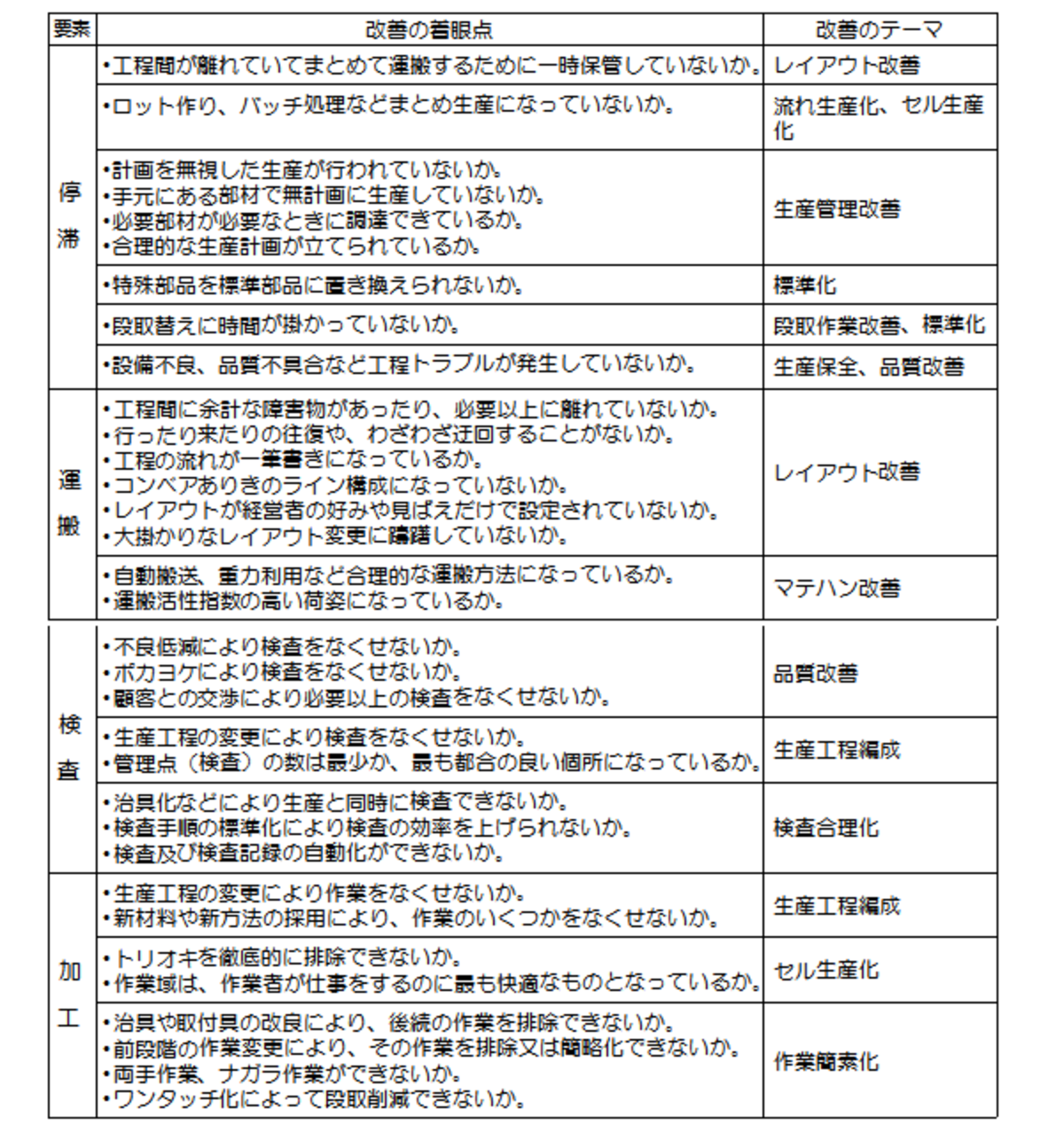
5.工程分析の応用
1.作業者工程分析用紙
下のような分析用のフォームを用いて、分析をしながら所定の欄に記入していくやり方です。
予め記号が並べられているので、筆記用具で該当する記号をたどるだけで良いようにしてあります。
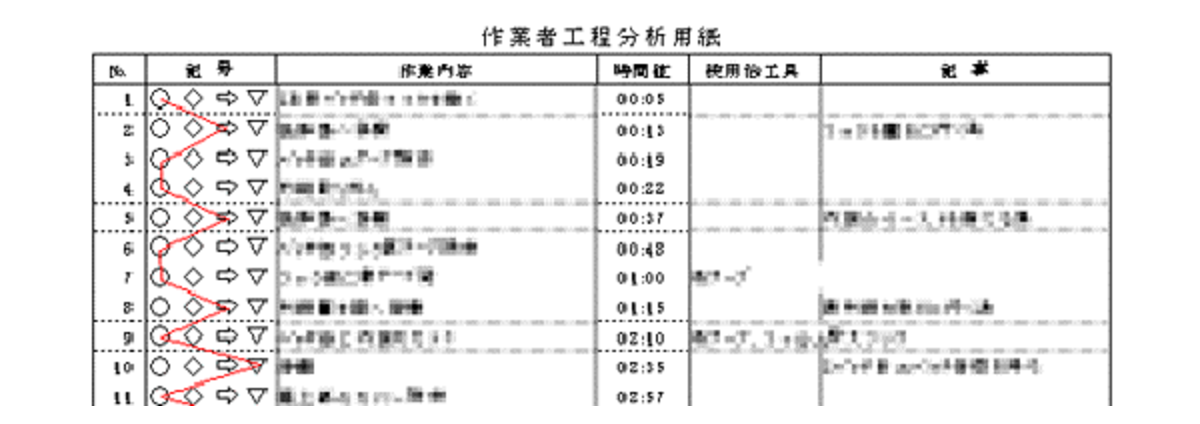
2.流れ線図
レイアウト図の中に工程記号を書き込んで分析するやり方です。
移動経路や距離まで一目瞭然なので、そのままレイアウト改善に使えます。
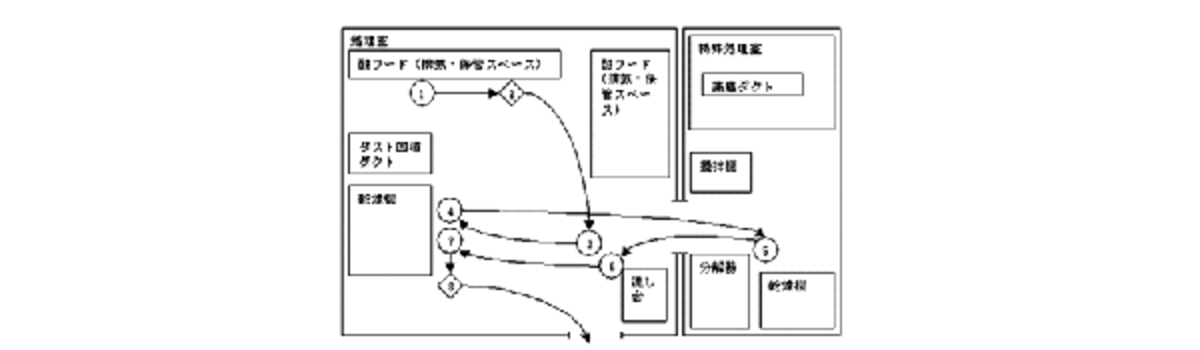
3.多品種工程分析
異なる製品でも生産工程が類似していれば、同じグループの製品として生産する方が管理しやすくなります。
このような標準化を行うために、工程分析表を並べて比較できるようにしたものが、多品種工程分析です。
生産管理改善や工程編成、レイアウト改善などに広く活用されます。
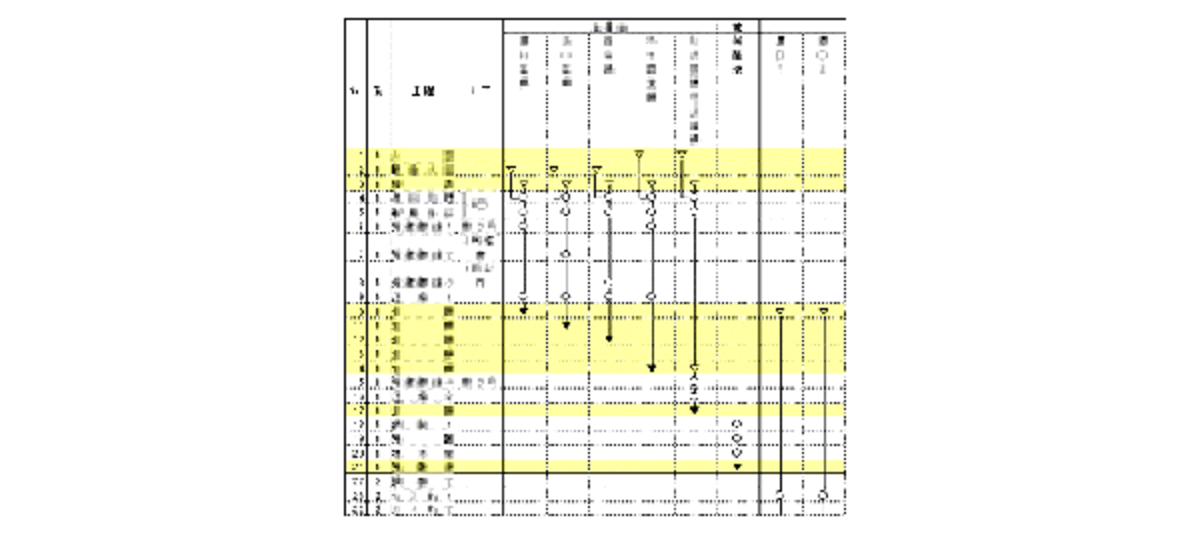