潜入!産業用ロボットとIoTが体験・体感できるセンター”スマラボ”
自社の現場にロボットを導入したいけど、
・どうやって入れればいいんだろう?
・ロボットのシステムって価格はいくらくらい?
・占有スペースは?
・ウチの作業にも使えるのかな?
などなど、よく分からない点が多く、なかなか手を出せないのが事実。
そうした方々に
「まずは実際のロボットシステムを見て体験してもらいたい」
ということでラボ的な体験・体感センターが4月に完成しました。
それが「スマートファクトリーコンダクターラボ」、
通称
スマラボ
です。
今回、そんなスマラボに潜入してきました!!
単にロボットが並んでいるようなショウルームとは違う、現場に近く、とても実践的なセンターになっていて、とても面白く、ロボット導入の参考になると思いますよー。
スマートファクトリー、ロボット、IoTの専門家が仕掛ける体感施設
スマラボを開設したのは、FAプロダクツ、オフィス エフエイ コム、ロボコムの3社。製造現場へのロボット導入や工場のスマート化、IoT化のプロフェッショナルですね。
仕掛人はこちらの方々
ロボコム社長・FAプロダクツ会長の天野眞也氏
東京から1時間超、群馬、埼玉、茨城、栃木など北関東の工場地帯からも良アクセス
場所は、栃木県小山市東間々田3−23−23。
電車の最寄り駅は、JR宇都宮線の間々田駅。そこからタクシーで5分弱。車の場合は、東北自動車道佐野藤岡IC、または圏央道境古河ICから30分強といったところでしょうか。
栃木県にした理由については、栃木県や群馬県、茨城県、埼玉県北部など北関東には工場が多く、例えば栃木県には近くに本田技研などがあります。北関東のロボットセンターの拠点となるべく、この場所にしたとのこと。東京からのアクセスも良いのもいいですね。(オフィス エフエー コムの拠点がここにあるというのは内緒です笑)。
また、ロボットをより普及させるべく、昨年、経産省からロボットセンター開設に対する補助金が出されましたが、このスマラボも補助金を受けたセンターの1つです。国からも首都圏、特に北関東地域のロボット普及に対して期待されている施設なんです。
ちなみに私は都内から電車で行きました。
JR宇都宮線で東京から約1時間15分くらいで、料金は片道1320円。贅沢にグリーン車を使ったのでプラス980円でしたが、グリーン車だと快適であまり遠さを感じませんでした。
ポイントは”体感”。リアルな現場に近いロボットシステム
ロボットはそれ単体だけでは何も意味をなしません。手となるハンド、目となるビジョン、頭脳となるコンピュータが必要です。さらに、生産ラインの一部になるので、コンベアなど搬送系とセンサ、モータ等の制御技術と組み合わせることも欠かせません。
つまり、何かの作業や目的に対する生産システムとして組まなければならず、実はそれを考えて、システムを構築するのが難しかったりします。
3社はそこを専門とする人たちなので生産システム構築はお手のもの。スマラボには、まさに現場にそのまま入れても使えそうなロボットシステム、貴田氏の言葉を借りると、これらは「パッケージ」。用途に合わせたものがズラリと並んでいます。実際に、すでに現場で運用されているものもあるとのこと。
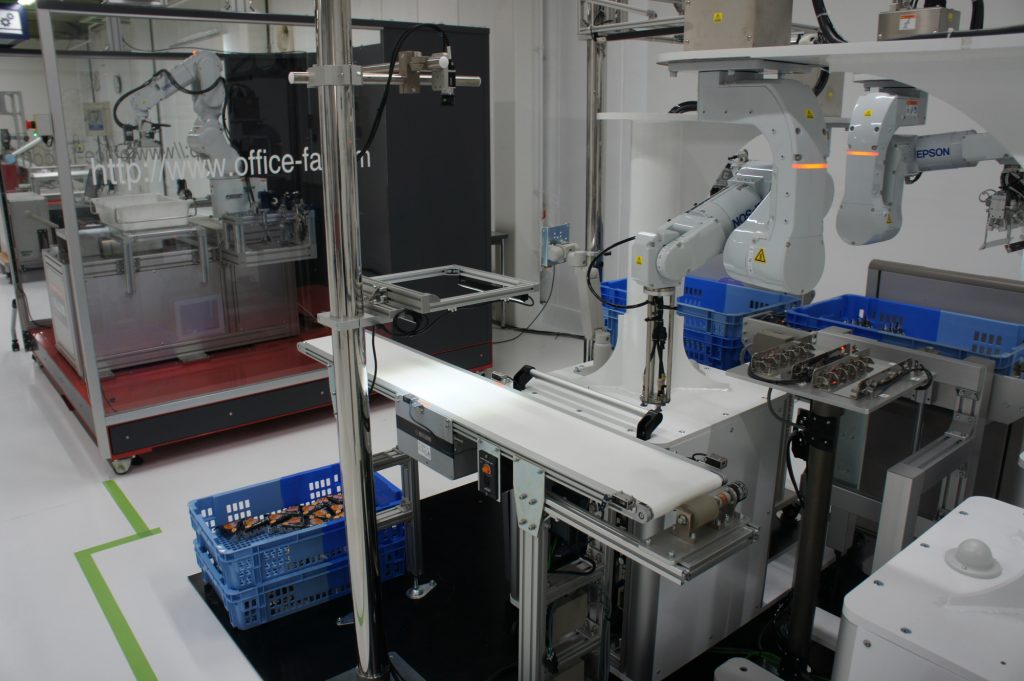
地方で頑張る中小製造業を応援したい!食品工場や物流倉庫などの人不足対策に
これまでロボットが多く使われてきたのは自動車や電子部品業界で、しかも資本力も技術もある大手企業ばかり。
でも、いま悩んでいる、困っているのは各地域にある中小製造業。高齢化でベテラン社員が退職していくなか、新卒や中途ではなかかな補いきれていません。
また3品産業と言われる食品、化粧品、医薬品、特に食品と化粧品の製造工場は比較的、地域にある中小規模の企業が担っていることが多く、その地域に住んでいる人をパートで雇って働いてもらっています。そこでは単純作業のキツイ仕事の連続や働く環境が整っていなかったりします。退職者が出ても、少子高齢化の影響もあって新規採用ができず、厳しい状況に追い込まれています。特に地方ではその傾向が顕著です。
このスマラボでは、特にそのあたりにスポットを当てて、そうした中小製造業の支援を目指しているそうです。
と前置きが長くなりましたが、スマラボでは「物流」、「食品」、「自動車/機械」コーナーを設けてロボットシステムを設置。IoTやスマートファクトリーに向けた「IoT」を加えて、4つのコーナーで構成されています。
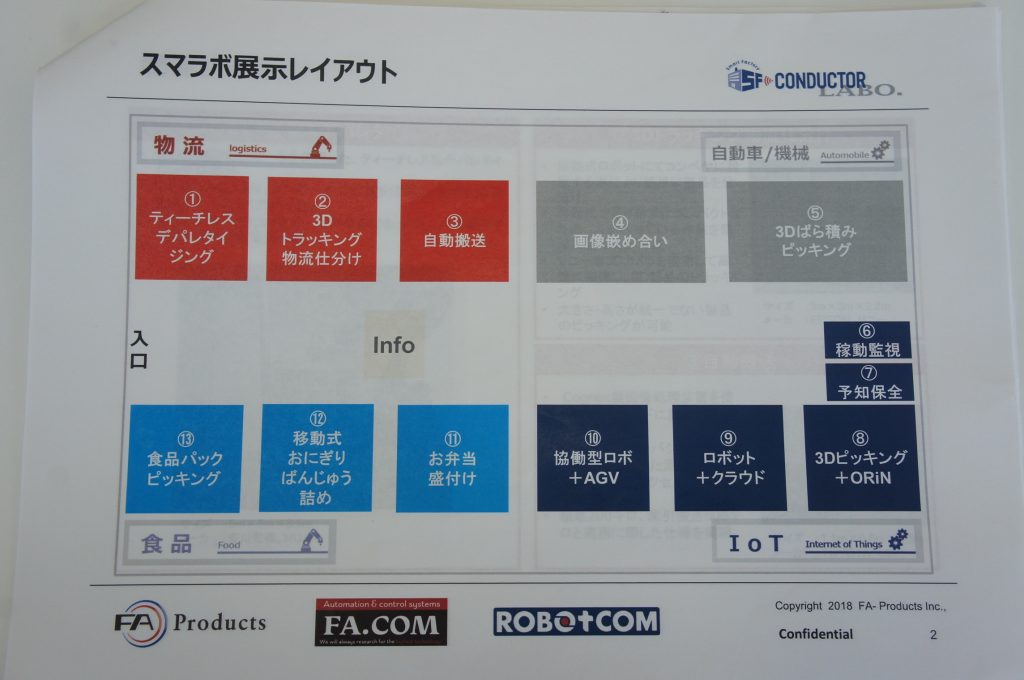
物流ゾーン
まずはじめは物流ゾーン。3つのパッケージが展示されています。
まずは
【ティーチングレスのデパレタイジング&パレタイジング ロボットシステム】
人が重量物を運ぶ作業を代替しようというものですね。
①デパレタイジング
トラックから下ろされた荷物を倉庫内に引き入れていく時を想定したデモで、カゴ車で納品された荷物をコンベアに載せていきます。
②パレタイジング
コンベアで倉庫内に運ばれてきたら、今度は倉庫内のカゴ車に載せていきます
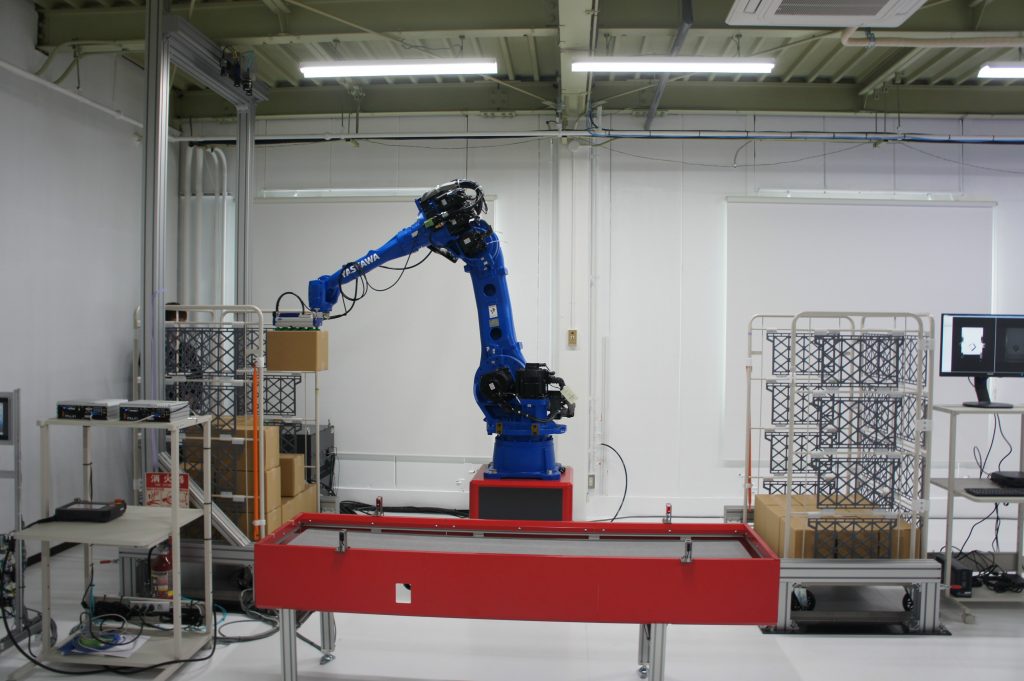
カゴの上の方にある3Dカメラ&カラーカメラでカゴ内の状況を撮影し、MUJINのコントローラでその状況を判別してロボットの動き方を作成。ロボットはその通りに動いて荷物をカゴ車からコンベア、コンベアからカゴ車に運んでいきます。
スペースは5m×5m×3.5m。
ロボットの動き方をわざわざプログラム組んだりする必要がないのでありがたいですね。
2つ目は
【3Dトラッキング物流仕分け】
ここは仕分け作業のロボット化。大きさの違う箱を3Dカメラで認識して、自動で仕分けるというものです。流れてくる場所もマチマチなので、そちらもキチンと認識しています。
ちなみにロボットはEPSON、カメラはリコー製です。
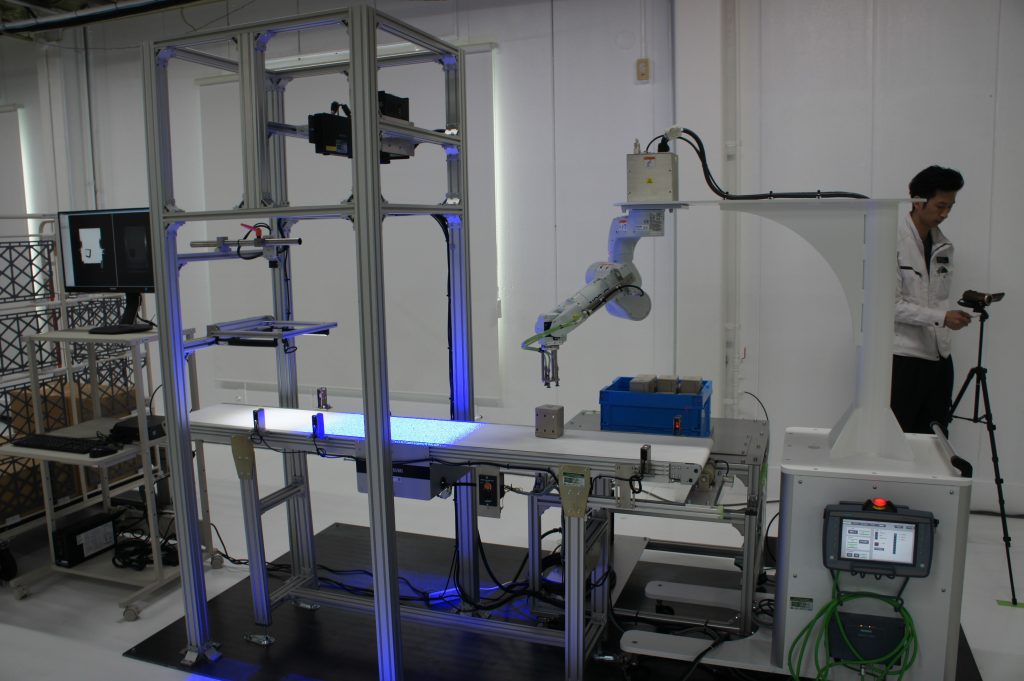
3つ目は
【AGVを使った自動搬送装置】
磁気テープ式のもので、Excelで簡単に軌跡をプログラムできるというトヨタLFのシンプルAGV「キーカート」です。200kgまで積載でき、牽引搬送も500kgまでいけるそうで、小さいながらもパワフルですねー
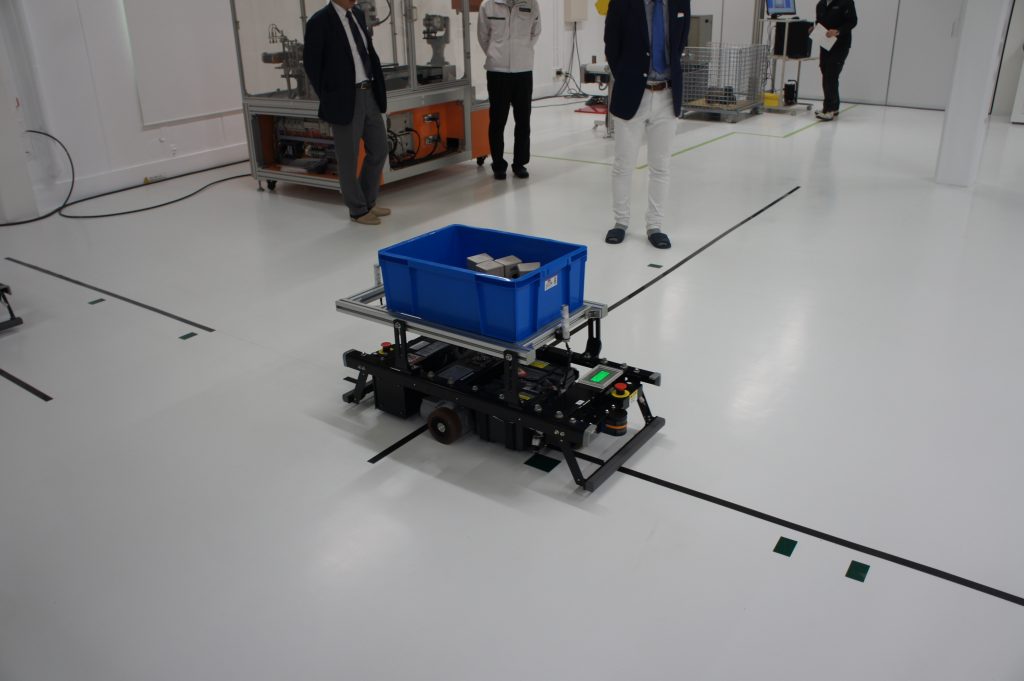
自動車/機械ゾーン
さすがはホンダが近くにあるだけあって自動車・機械のデモもあります。
1つ目は
【2つのロボットを協調させたワークのはめ合い作業】
スカラロボットと6軸多関節ロボットを協調させて嵌合作業をするというもの。普通は、受け側は固定してあるのが一般的ですが、両手が動いてはめ合いをするのはとても難しい技術とのことです。
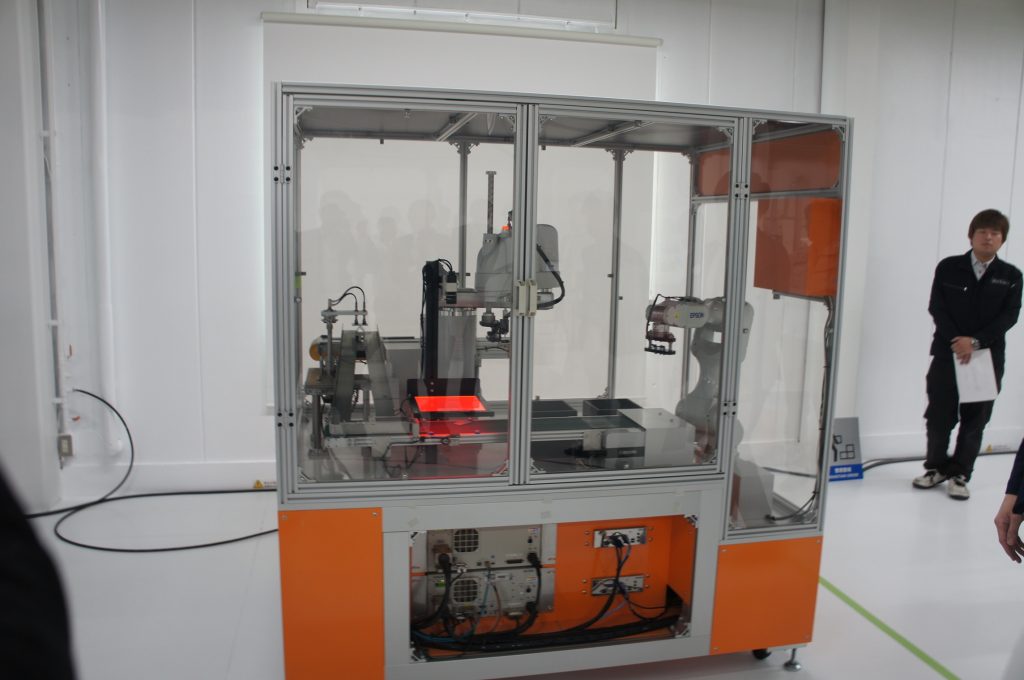
2つ目は
【3Dばら積みピッキング】
ファナックのロボットと3Dカメラを使い、カゴ台車に入って運ばれてくる金属ワークをピッキングして、コンベアに整列して流すというもの。カゴ台車から持ち上げてコンベアに置くというのも重労働ですが、これを使えばそんな過酷な作業をロボット化できるというもの。
これはよくあるばら積みピッキングなのですが、こちらのハンドは磁石になっている特別なものだそうです。こういう工夫もすごいですねー。
食品ゾーン
食品工場の作業の場合、ピッキングするものの種類が多い上、硬かったり柔らかかったり、サイズの個体差も多かったりして、なかなかロボットが人手作業を上回る生産性を上げるのは難しいと言われます。さらに、室温が低く、マスクや帽子など衛生を保つための苦労も多く、働く人にとっては過酷だったりします。そのため人を採用するのも大変。このゾーンではそのあたりを解決するようなシステムが展示されています。
【お弁当盛り付け】
コンビニ弁当やお弁当屋に最適なパッケージ。3D画像センサで食品の位置や種類をロボットが識別し、弁当箱に詰めていきます。
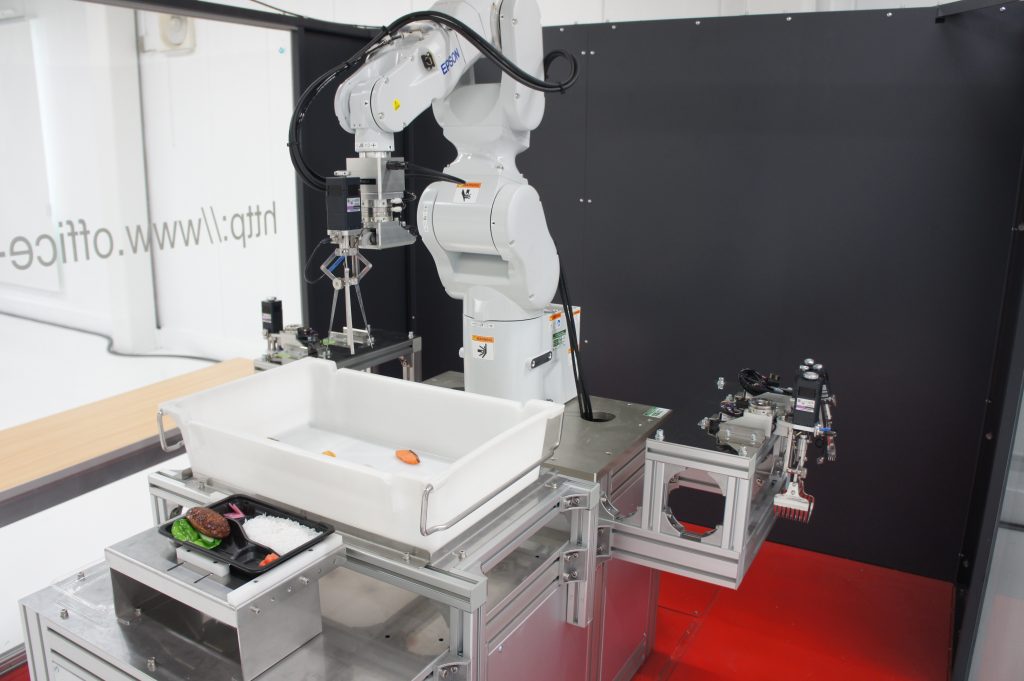
食品によってハンドを変えて、いろんな種類を持つことができる上、さらに食材の重さも測ってくれるので、定量で盛り付けができます。ハンドもお箸のようなものから、フォークやトングのようなものまであるようです。
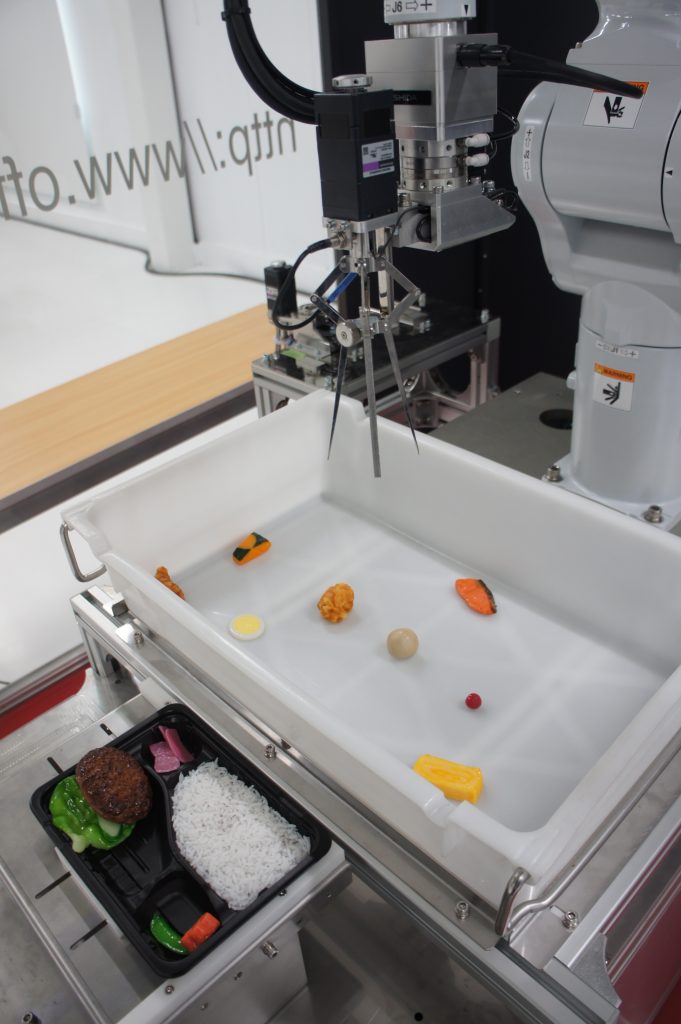
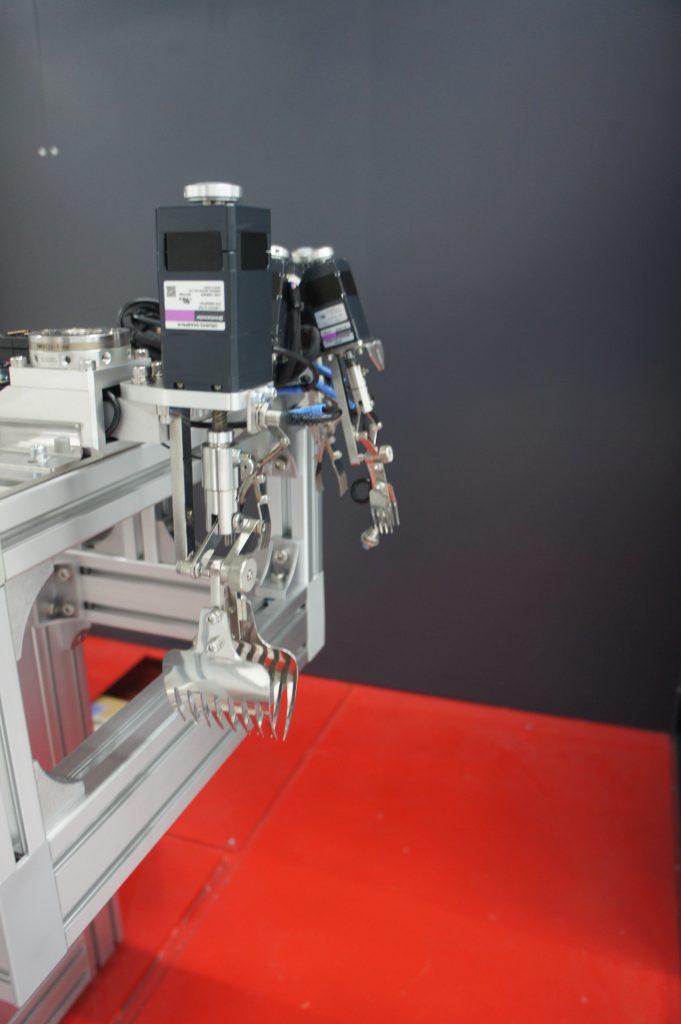
【おにぎりばんじゅう詰め】
3つのロボットが無線でつながって協働作業をするというデモ。
①コンベアをバラバラに流れてくるおにぎりをロボットが整列する治具に置き、
②整列治具が満杯になったら、2台目のロボットがばんじゅうに詰める
③ばんじゅうが一杯になったら、3台目のロボットがばんじゅうを入れ替える
こちらもエプソンの最新製品N2シリーズを使ったものですねー。
ロボット自体は動かせるユニット式で、横に並べたり、組み合わせたりとフレキシブルにラインを構成できます。狭くてスペースの取りにくい食品工場向けにちょうどいいとしています。
【食品パックのピッキング】
こちらは食品センターで、倉庫から取り出した製品にラベルを貼ることを想定したデモ。食品工場では、パッケージにラベルを貼り付けて情報を追加したり、特別感を出したりすることが多いらしいとのこと。
それで、箱から取り出してコンベアを流す、ラベルを貼った後、コンベアを流れていくものをピッキングして別の箱に移し替えす作業なんかも人手でやっているそうです。
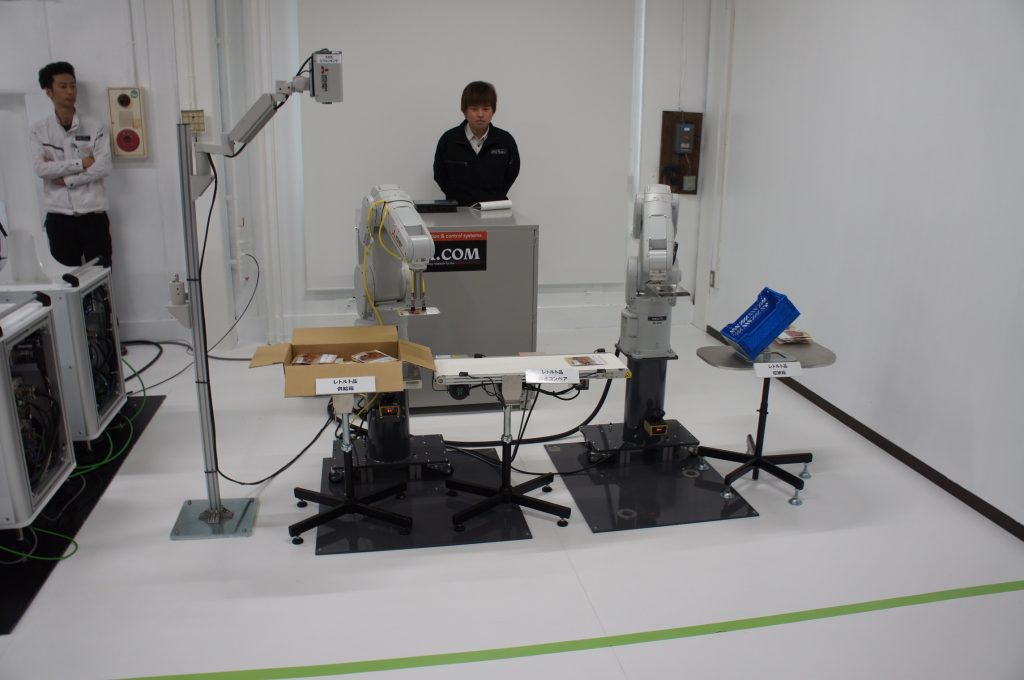
IoTゾーン
こちらは他の3つのゾーンとはまた違った感じのところ。
ロボットも生産管理や製造実行システムなど上位とつながってスマートに動かすなんてのもこれからは必要となってきます。いわゆるスマートファクトリーと呼ばれるもので、それに向けた未来の取り組みなんかを展示してあるゾーンがIoTゾーンになります。
1つ目は、
ORiNというロボットやFA機器をつなぐための言語を使って組んだ3Dピッキングシステム
3Dビジョンとロボット、バーコードリーダ、ビジョンの画像処理を1つのPCですべて制御しています。だからシステムの下の方にある盤がスカスカなのが分かると思います。通常はPLCとかいろいろ詰まっているのに、ORiNを使うとここまで統合できるんですね。
こちらはデンソーのロボットとキヤノンのビジョンを使っています
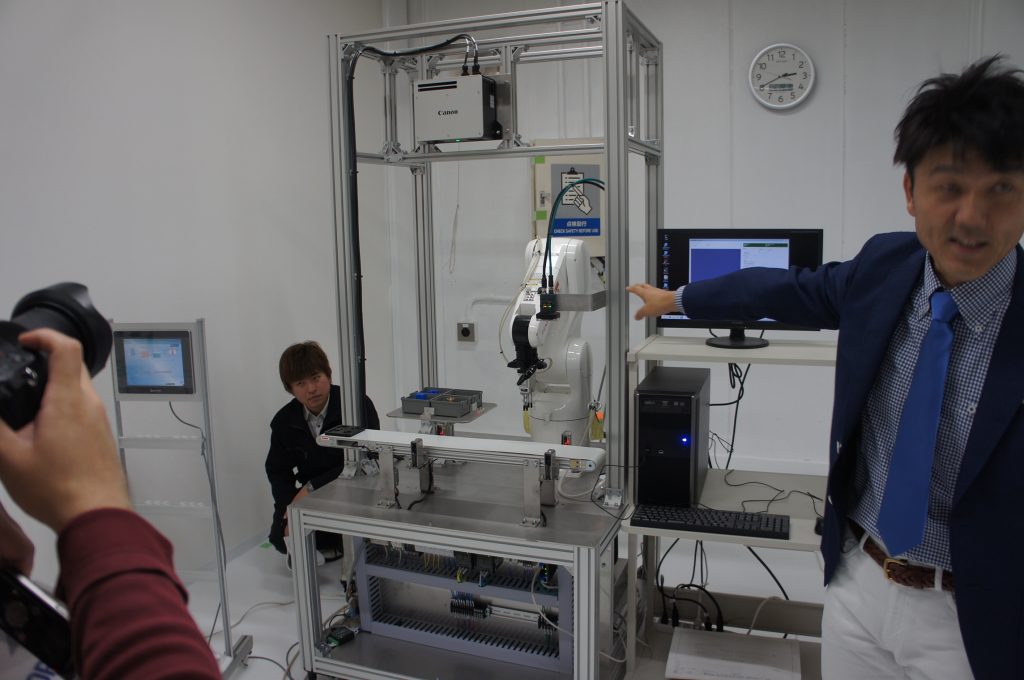
2つ目は
AGVと協働ロボットを組み合わせた自走式ピッキングロボット
MESとAGV+協働ロボットがネットワークでつながっていて、生産指示通りのものが流れてきているかをキチンと検査した上でピッキングし、別の場所に持っていくというデモです。単に自走式のアームロボットだけのデモではなくて、上位のシステムとつながっているというコンセプトです。
ここでのロボットはアーム型がユニバーサルロボットで、AGVは日本電算シンポのインテリジェントなAGVですね。
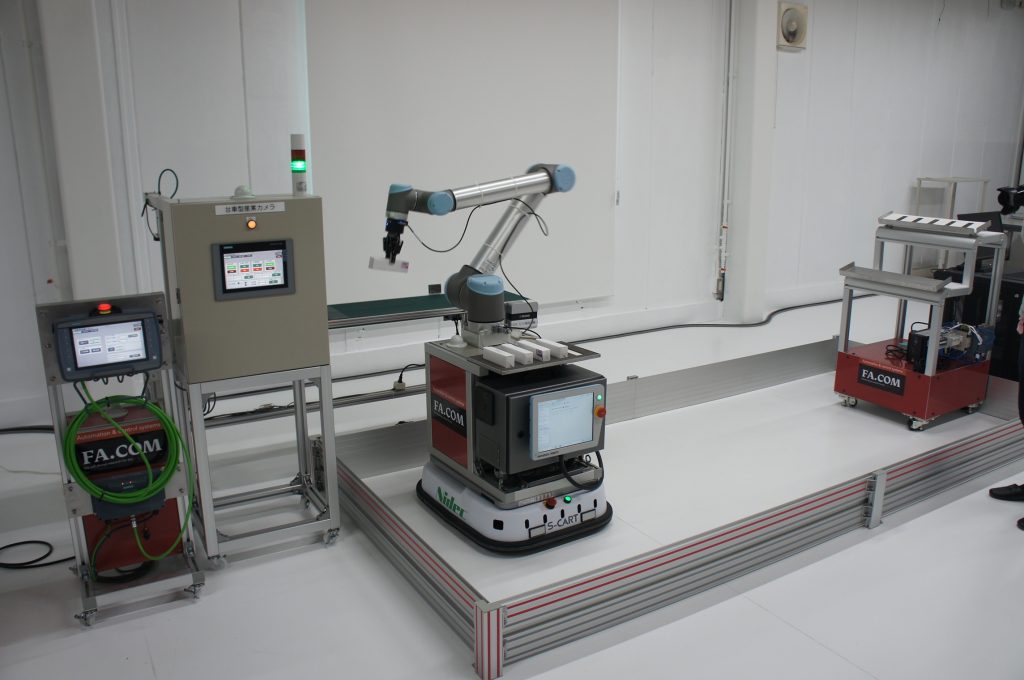
3つ目は
ロボット+クラウドのシステム
ちょっと他に比べて地味に見えますが、こちらも上位につながっているとのこと。こちらもユニバーサルロボットです。
ここからはロボットではなく、IoTツールです。
FAプロダクツでは、スマートファクトリーの第一歩としてかんたんIoTツールを自社製品として展開していて、それらを展示しています。
1つ目は
稼働監視ツール
設備の稼働状態を見るためのツールとして、ゲートウェイの機能を持ち、接続するだけでデータを集めて表示できる表示器と、データを取り出す端子すらない古い機械に対して、配線に巻きつけて電流の流れから異常を監視する「信号横取りセンサ」を展示しています。
もう一つは
予知保全システム
6軸の振動センサで機械の振動を集め、通常運航のパターンを学習させておき、異常な動きが出てきたら故障の予兆をするというもの。加速度センサだけでは検知しにくい偏心や磨耗による異常も検知できるとのこと。またNGデータなしで分析できるので、学ばせる期間も短くて、すぐに導入できるそうです
体感だけの施設じゃない!ロボットSIの教育機関としても活用
これだけ複数のメーカーのロボットが並んでいるところも珍しく、各アプリケーションを搬送系まで含めてここまで作り込んである場所は滅多にありません。ビジョンのシステムも、1社だけではなく、コグネックス、キヤノン、リコー、ファナックなどなど複数使っているのは凄いと思います。本当に「現場のための施設」というのが実感できます。
と言いつつも、実はここはロボットを導入したいというユーザー企業が見に来て体験するだけの施設ではないとのこと。ここでロボットシステムインテグレータが学べる教育・研修機能もあり、ロボットSIを積極的に育成しようとしています
(競合やライバル企業を育てることになるんじゃないかと心配になってしまいますが。。。)
いま日本のロボット産業のアキレス腱となっているのは、ロボットをシステムとして組み上げて納品し、立ち上げまで行うロボットSIの不足だと言われています。ロボットを導入したいという企業は多いのに、システムとして組んで正常稼働させられる技術を持った企業が少なく、今後ロボットを普及させて市場を大きくするにはロボットSIを増やすことが絶対条件となります。
3社はそれに対し、ここでロボットSIの教育を行い、増やしていこうとしています。飯野氏によると、1年間で外部で30〜60人くらい、社内で30人ほどは育てたいとのこと。実はすでに栃木県によるロボットSI育成事業にも取り組んでいる実績があり、これからさらに加速させていくつもりのようです。これは心強いですね。
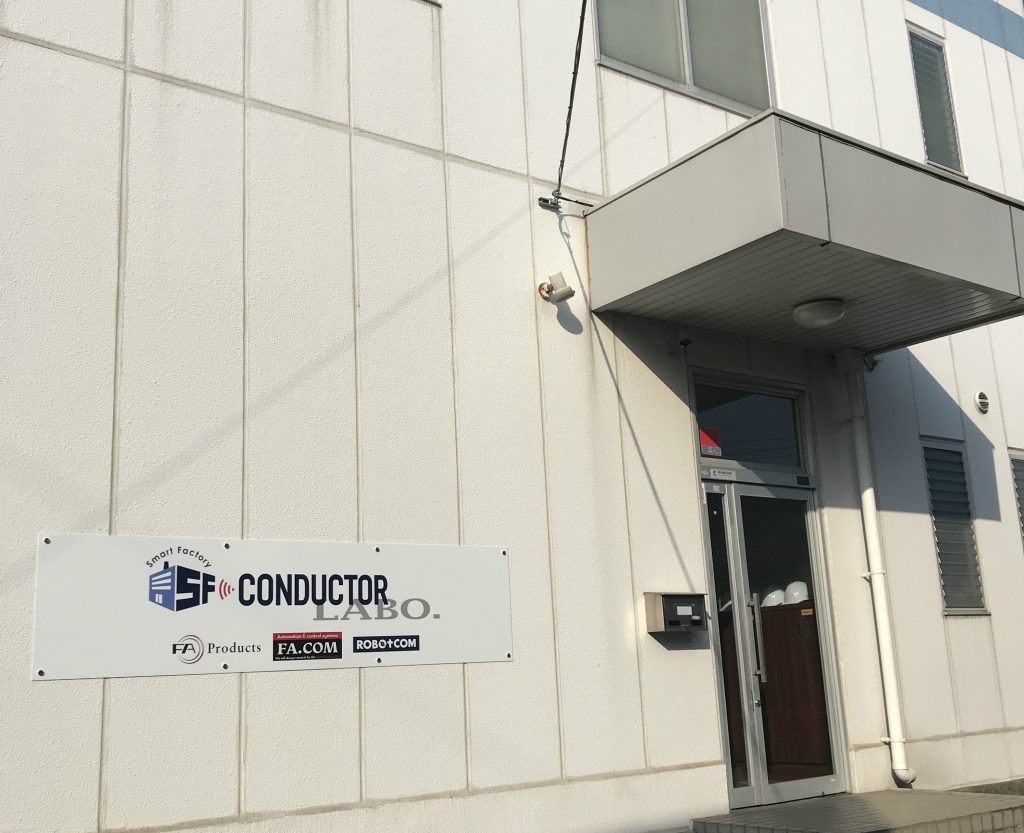
まとめ
ということで、ロボットを今以上に普及させていく、現場での人不足を解消するためには、もっと多くの人がロボットを知り、触り、体験することが大事です。その意味では、このスマラボはすごくいい施設で、多くの人が来て欲しいと心から願います。アプリケーション展示が素晴らしいですし、一見の価値は十分あります。
ちなみに、
来場者数の目標や見込みは、月に100人くらいとのこと。一般のお客さんがフラリと入れるところではなく、製造業でロボットを導入検討している人が予約をして訪れる形になるので、このくらいという回答でした。
ロボットを検討している、入れてみたい、導入イメージを作りたい、自社のワークで使えるかどうかなどなど、ロボットに興味がある方は、ぜひ一回相談してみてはいかがでしょうか。
参考:スマラボ(スマートファクトリーコンダクターラボ)
参考:FAプロダクツ
参考:オフィス エフエイ コム
参考:ロボコム