品質意識を高めるためにトップが持つべき2つの視点
現場は品質に対してどのような意識を持っていますか?
形だけのQCサークル活動になっていませんか?
品質第一と現場には伝えているけれど、本当に理解しているだろうか?
ウチもQCサークル活動を展開しているし、発表会もやっているから、
ダイジョウブと思っているけど……、イマイチ心配だなぁ。
品質への意識を高めて、定着させるにはどうすればイイだろうか?
品質管理で心へ訴えかけるコト、頭に訴えかけるコト、それぞれをトップ自ら、継続して行うことです。
QCサークル等の小集団活動は、そのやり方を見直します。
1.競争力の源泉は品質であるという見方は依然として強い
「高品質を強みとしてきた日本製品の競争力において、“品質”の位置づけは変わってきているか?」
という質問に対して439名のメーカー等の関係者が回答した結果を下のグラフへ示します。(出典:『日経ものづくり』2015年7月号)
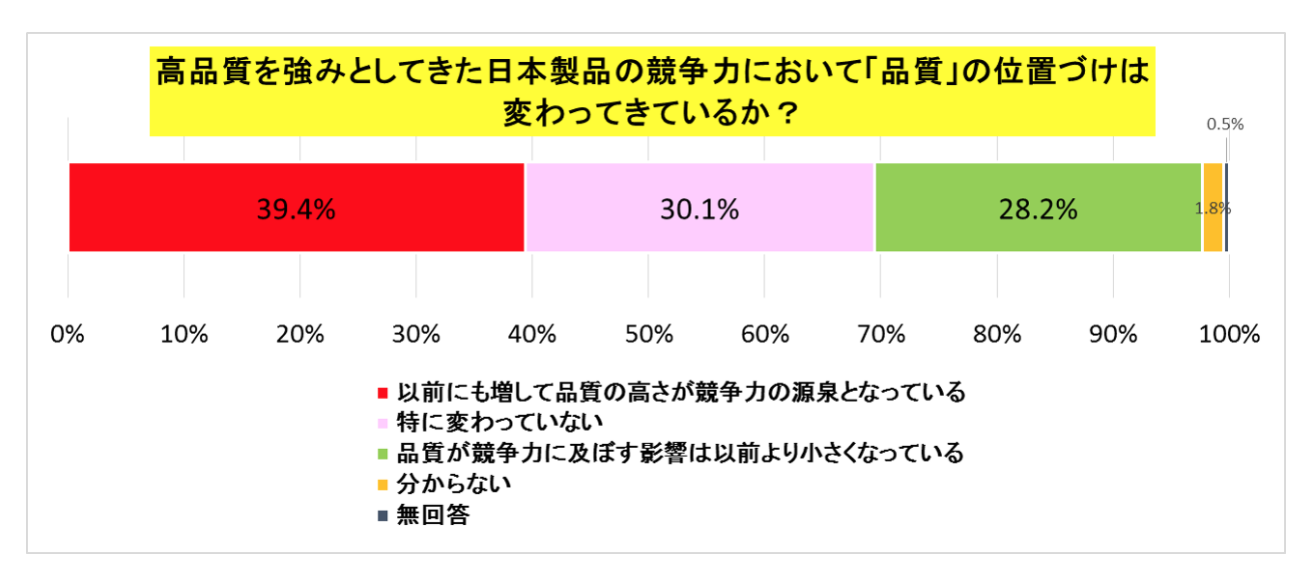
40%の回答者が、今まで以上に競争力の源泉になっているとしています。
変わらず高品質が強みのままだと考えている割合が30%なので、約70%の回答者が、品質は競争力の源泉と感じています。
その一方で、日本製品の品質レベルが低下していると感じている人が多いこと(変化に着目して品質管理の見える化を実践する)を踏まえると、モノづくり工場で「品質」への意識を高め、定着させることは重要な課題の一つであることには間違いありません。
品質が競争力の源泉であるという考えに同感です。
さて、ここでは「品質は競争力か?」ではなくて「品質は競争力の源泉か?」と問うています。
現在、品質がイイから顧客に喜ばれた!! ということはまずありません。品質がイイのではなく、顧客が望んだ仕様のモノを期待通りに提供したから喜ばれるわけです。
かつての日本には安かろう悪かろうと言われた時代があり、欧米の品質に追いつき追い越せと品質管理の手法を一生懸命に欧米から導入し、経営者と現場が頑張っていた頃がありました。
1960年、70年代のことです。
このような時代ならば、品質そのものが競争力になり得ます。
今は、違います。
品質は高付加価値化の土台、前提条件という位置づけです。品質は良くて当たり前で、欠けていたら大問題。
品質自体が表舞台に出ることはありません。
しかし、高い品質を維持できる現場力がなければ、そもそも高付加価値品の事業展開は不可能です。
クレームを連発するようでは論外ですし、不具合品を外部へ流出させないまでも、社内で不合格品ばかりを生産していては利益が出るわけがない。
つまり、品質はモノづくり工場の基礎体力のようなモノであり、その企業の文化や風土そのものです。
したがって、他社とは差別化された、顧客から選ばれる高付加価値製品を市場へ提供できるようになるためには、源泉としての品質が欠かせない。
ですから、品質への意識付けは組織文化を定着させるに等しいことであり、時間をかけて育むモノです。
2.品質への意識を高めるためにトップが持つべき2つの視点
品質は工場経営上、極めて重要な項目ですが、一方でなかなか理解してもらうのが困難な項目でもあります。
したがって、全社的な品質への意識付けのために経営者が持つべき視点は2つあります。
それは、
- 心へ訴えかけるコト
- 頭に訴えかけるコト
モノづくりを生業としている自分の会社にとって品質がどのような位置づけにあるのか、経営者自らが語ることです。
品質にまつわる創業時の苦労話や経営者が抱いている品質への想いについて語ります。
さらに、
- 品質が欠けたら工場がどのような状況に陥るのか
- 品質がモノづくり工場で事業を展開する上で、いかに重要な役割を果たしているのか
こうしたことを現場へ直接伝えることが大切です。
「ウチの会社にとって、存続と成長の果たすための地力みたいなモノである。そして、常に磨き上げていかねばならない文化のようなモノである」
という経営者の品質への想いを、繰り返し、繰り返し語ります。
繰り返し語る経営者の言葉が心に届き、共感を生みます。
繰り返し語ることが重要です。
繰り返し語ることで、ジワジワと現場の心に染みわたり、経営者の想いが浸透し定着します。
こうした心へ訴えかけるコトと同時に、仕事のやり方を変えて、頭(理性)に訴え、理解させることも必要です。
ですから、一連の業務フローの中に、今までやっていなかったコト、例えば設計開始時のデザインレビュー、生産開始時の初期流動管理、変更点発生時の工程変更管理等の品質管理に関するイベントを新たに加えます。
仕事のやり方を具体的に変えることで、品質に対する考え方を変えるキッカケになります。
J・フロントリテイリング相談役の奥田務氏は、社内の改革を進めた頃を振り返り、次のように語っています。(ちなみにJ・フロントリテイリングは大丸と松坂屋が合併してできた企業で小売業です)
「営業、外商、人事の諸改革を一気に進めた。
よく意識改革が必要と言われるがそれを進めるには仕事のやり方を変えることが近道だ。
仕事のやり方が変われば働き方も変わる。
お客様に求められるサービスもわかり、それがお客様を知ることにつながる」(出典:『日本経済新聞』 私の履歴書)
品質の重要性を知ってもらいたい場合に、仕事を通じて実感できるやり方にするのが近道だということです。
形から入ることも大切ということです。
心と頭に地道に訴えかけることで、品質への意識を現場へ定着させます。
3.QCサークルを形骸化しないための2つのポイント
世界有数の建機メーカーであるコマツは1960年代という国内ではかなり早い時期から、熱心にQCサークルに取り組んできたメーカーとして知られています。
このようなコマツでも1990年代品質管理の取り組みが弱まった時期がありました。
「漫才のような演出を競い合う一方、中身のない発表をするチームが目立つようになってきた」(出典:『日経ものづくり』2015年7月号)
そこで、2001年に社長に就任した板根正弘氏(現相談役)が品質を重視する経営に再び舵を大きく切りました。
多くのモノづくり工場では、QCサークルのような小集団活動が展開されています。
ただ、この活動自体が形骸化されていませんか?
毎年、活動開始時に号令をかけるけど、あとは現場任せ。
最後、締めとして、なんとなく年度末に1日かけて全社発表大会をヤッテいる、ということはないですか?
せっかく定着したQCサークル活動です。その活動自体を品質意識の向上に使わない手はありません。
QCサークルを活性化するためのポイントは2つあります。
やはり、頭と心へバランス良く訴えかけます。
- グループ目標と全社目標を関連付けさせる:頭へ訴えかける
- 経営者のフォロー:心に訴えかける
グループ目標と全社目標を関連付けさせる
各グループの目標はどのように設定していますか?
グループ任せになっていませんか?
各グループの目標は全社目標とリンクさせなければなりません。グループ目標の重要性を実感させるためです。
たとえば、現在、利益率がイマイチの製品Aを取り上げるとします。
この製品A、利益率は低いのですが、生産量は場内でもトップレベル。
そこで、利益率を20%向上させる全社目標を立てました。
成果が出れば、全社として利益額が増えます。
それを達成するためには、
- 加工工程では材料歩留りを20%向上
- 塗装工程では直行率を10%向上
させる必要がありました。
このような全社目標が掲げられていれば、加工工程がグループ目標「材料歩留り20%アップ」を掲げた時の意義がはっきりします。
全体目標を与えられなくて、さぁ活動せよと言われても、その成果がどのような貢献に繋がるのかわかりません。
現場が会社に貢献したいと考えても、そもそもその業務の重要性を感じる機会がありません。
経営者が設定した全社目標と自職場目標との関連を把握できれば、現場は自分たちの頑張りがどのように利益に貢献し、それがどれだけ重要なことなのか理解できます。
頭でしっかりと理解できると、やる気が引き出されます。
経営者のフォロー
QCサークル活動では、取り組みの最後に半日、あるいは一日かけて全社表会を行うケースが多いです。
全社発表会自体を否定しませんが、それよりも重要なのは、経営者による活動へのフォローです。
経営者が活動の途中経過に興味を抱くことです。
現場は自分たちが頑張った成果を経営者に見てほしい、知ってほしいと思っています。
活動の途中で、経営者が現場から話を聞く場を設けるのは動機づけに繋がります。
やる気が引き出されます。
経営者も、品質への想いや全社目標の意義、そのための現場目標の重要性を現場へ直接に語ることができます。
双方の情報交換により、現場は、経営者が現場に寄せる期待感に触れて頑張ろうという思いを強くし、会社への信頼感も増す。
経営者の言葉が心に響くことで、現場の各人は自らの有能性を感じ、やる気が引き出されます。
加工部品の生産現場の管理者時代に現場の作業者からこんな話を聞いたことがあります。
現場を巡視していると、その現場作業者は、自分が担当している作業が終わった後、自ら選別した部品の手直しをしていました。
よく見つけてくれたね、とねぎらいの言葉をかけた時の言葉です。
「作業をしていたら微妙にキズが付いている部品が前工程から流れてきた。
それは作業指示書にはない類のキズであった。だから、これをこのまま流したところで自分に責任が及ぶわけではない。
けれど、最終製品になった時点でその不具合が見つかったらF係長(その時の現場責任者の職位は係長でした)も追及され、F係長は困るだろうから」
その作業者の目の前にキズがついた部品が流れてきたとき、自分の上司であるF係長の顔がふと浮かんだのだと思います。
いつも気にかけてくれるF係長の役に立ちたいと思っていたその作業者は、
「自分の上司が困る事態は避けたい」と“自然に”考えたわけです。
予期せぬ品質トラブルを未然に防ぐことができたのは、日頃、F係長が現場作業者としっかり意思疎通を図っていてくれたお陰です。
と同時に、品質管理では、こうした“属人的”な側面も重視すべきだ、ということにも気が付かされました。
取り組みの途中、経営者が現場をフォローすることによる効果はとても大きいです。
しっかりフォローができれば、最後の発表会は不要なくらい十分な成果を共有できます。
そのためには、経営者自身が現場の日頃の活動も熟知していなければなりません。
全グループのフォローのための時間をどのように捻出するかが、多忙な経営者の課題になりますが、他の時間を削ってでも実行する価値のある仕事です。
経営者にしかできない重要な業務です。
存続と成長のためには付加価値を拡大させる必要があります。
しかしながら、高付加価値品を生産できる地力が現場になければ、経営者の想いも画餅にとどまります。
経営者の想いを実現させる地力、基礎体力が品質です。
基礎体力を育むには時間がかかります。
戦略的な視点に立った工場運営の中で、現場を育てる意識が欠かせません。
まとめ
品質管理で心へ訴えかけるコト、頭に訴えかけるコト、それぞれをトップ自ら継続して行う。
QCサークル等の小集団活動のやり方を見直します。
中小モノづくり工場で品質への意識を高めるためには、経営トップが同じ言葉を言い続けると同時に仕事のやり方を変え、心と頭へ訴えることが必要である。