付加価値を拡大し続けるためには絶対に○○が必要
1.判断基準が明確な現場はやる気に満ちて元気がある
工場の使命は会社が存続・成長に向けて付加価値を生み続けられるようにキャッシュや人財、それにノウハウといった経営資源を獲得すること、あるいはそのような機会を作り出すことです。
そして、その工場の使命を果たすためにいかに上手く人に働きかけるかが重要です。この「人に働きかける行為」が工場運営であり、人に動いてもらうことが本質です。
「人はパンだけで生きるのではない」という言葉がしばしば引用されます。
たしかに人は生活していくために仕事をして糧を手に入れる必要があります。ただ、それだけで十分なのだろうか。身体の健康とともに「心」の健康も大切なのではないか。
この言葉は、こうした考え方を私たちに投げかけています。工場運営や工場経営のキモもこのあたりにあります。
さて、下記の2つどちらの仕事に現場はやりがいを感じるでしょうか?
- 選択性を持って自発的に取り組む仕事
- 背景や目標が不明確な状態で一方的に指示されて取り組む仕事
選択性を持って自発的に仕事に取り組みたい現場にとって必要なのは、実績の良し悪しを判断するための基準、つまり判断基準です。判断基準は客観的であり、数値で表現されます。
トヨタの標準作業書には、以下の3つが明記されています。
- サイクルタイム
- 作業順序
- 標準手持ち
トヨタではこの3つが、現場作業実績の良し悪しを判断する客観的な基準です。工場全体の目標にそって、現場自らがこれらを作成し実行しています。
こうした判断基準のおかげで現場のベクトルは揃い、取り組みが加速されます。客観的な判断基準に経営者の想いが反映されていれば、経営者は都度現場へ指示する手間から解放されます。
また、判断基準を設定するということは、経営者のぶれない判断軸を現場へ提示していることにもなります。
一方、現場にとっても判断基準に従った業務では自律性が促されます。その結果、やる気が醸成されます。やる気が醸成される現場の若手はみんな元気です。
2.上手くいかないほとんどの原因は仕組みが無いこと
さて、客観的な判断基準が設定されると仕組みを構築しやすくなります。仕組みが構築され、それが現場へ定着すれば活動の継続性が高まります。やるべきことが明確化され、PDCAサイクルを廻しやすくなるからです。
「仕組み」の意味を、辞書で調べてみると、『仕組まれた全体の構造や各部の有機的関係(出典:三省堂 新明解国語辞典第4版)』と書いてあります。
“仕組まれた”というところがポイントです。意図が存在して、目的を持ってそうする、ということです。ですから、仕組みとは「経営者の想いを反映させた“仕掛け”が組み込まれた仕事上の枠組み」と言い換えられます。
工場経営が上手くいっている工場には、必ずといっていいほどその工場に適した仕組みが存在しています。ですから、工場経営で上手くいかないほとんどの原因は、仕組みが無いことです。
仕組みによって、
1)やるべきこと、やってはいけないことがはっきりしている。
2)問題発生の判断基準とその時の対応策がはっきりしている。
3)取り組みで目指すべき目標が定量化されはっきりしている。
これらは全て経営者の想いをベースにした、仕事上の枠組みです。経営者しか決定できない事項です。
やるべきこと、やってはいけないことがはっきりしている
1)項は自律性を促す上では重要なことです。
役割分担がはっきりしていることで業務のフィールドが明確になります。
現場で自分が担当する工程の業務、前後工程と連携する業務、工場全体に共通な業務。こうした業務上の識別が明確になってこそ、現場は自発性を持てます。
工場でのモノづくりでは“連携”が重要です。実際の業務では多くのメンバーがラップし合ってこそスムーズにモノづくりが進みます。ラップし合うということと、役割分担を曖昧にすることは違います。業務の分担を明確にしてこそ、ラップし合う意識が生まれます。
役割分担を曖昧な状態で放置しておきながら、問題が発生した時に「その業務は、あなたの業務のはずだ」と現場を責める管理者がいたら、経営者は正しい方向へ導く必要があります。
これはモチベーションを維持する上でも、とても大切な論点です。
問題発生の判断基準とその時の対応策がはっきりしている
2)項は“チーム”で仕事をしている意識を持たせる上でとても重要です。
その工場が持っている“強さ”は、特にこの2)項に表れます。トヨタ生産方式でのアンドンや自働化がそれです。
モノづくり工場では、基本的には淡々と“稼働”しているのが望ましい姿です。その状況から逸脱した状態に陥った際、チームでどう動くべきか。こうしたことを事前に明確にしておいてあげることは、経営者の重要な役割です。
問題発生の判断基準も対応策を考える仕組みも無い状態で問題が発生した時、勢いで現場の担当作業者“個人”へ責めがおよぶケースが見られます。
これは最も避けたい対応です。仕事はあくまでチームで進めるモノであり、仕組みで行うモノです。
賞賛する際なら“個人”に焦点をあてても構わないですが、問題発生の原因を追究する場合は、あくまで“仕組み”に焦点をあてるべきです。
改善すべきは望ましい対応ができなかった“仕組み”であって、現場作業者ではないということです。
会社の情報的経営資源は人財から得られますが、最終的には“仕組み”に蓄積されていきます。
ですから焦点を“仕組み”にあてた方が経営上、長期的にはお得です。動機付けの点から考えても大切なことであり、仕組みがないことによって発生する問題点のうちでも無視できない大きな論点です。
取り組みで目指すべき目標が定量化されはっきりしている
3)項は達成感を感じさせる上でポイントになる項目です。
目標ですから、現場メンバー向けの経営者が描く未来像の一端を示します。現場活動の成果が足元のキャッシュを稼ぐこと、あるいは未来像に対しどのような貢献をすることになるのかを示しています。
経営者が設定した目標値に至った時の現場メンバーの達成感は、とても大きいです。自分たちの頑張りが、何にどう貢献されるのかがわかるからです。
仕組みがなければ、こうしたことが全てにわたって曖昧です。通常業務が淡々と流れる時には、それほど重大に感じないことでもあります。
ただ問題が発生した時、あるいは新たな取り組みを始める時、仕組みの必要性を痛感するのではないでしょうか。
3.上手くやっているところとそうでないところの格差が拡大
“仕組み”は変化に対応する、経営者が現場に仕掛けた仕事上の枠組みです。
中小モノづくり工場が直面している経営環境は、常に変化しています。存続と成長のためには立ち止まってはいられません。
変化する経営環境に合わせ、自社工場も変化させなければなりません。そして、付加価値を拡大し続け、キャッシュの源である利益を稼ぎ続けなければならないのです。
ここに、中小企業が過去に直面してきた経営環境の変化について解説した興味深いデータがあります。
製造業の企業規模別に見た1社当たり平均の実質付加価値額の推移です。(出典:2015年版中小企業白書)
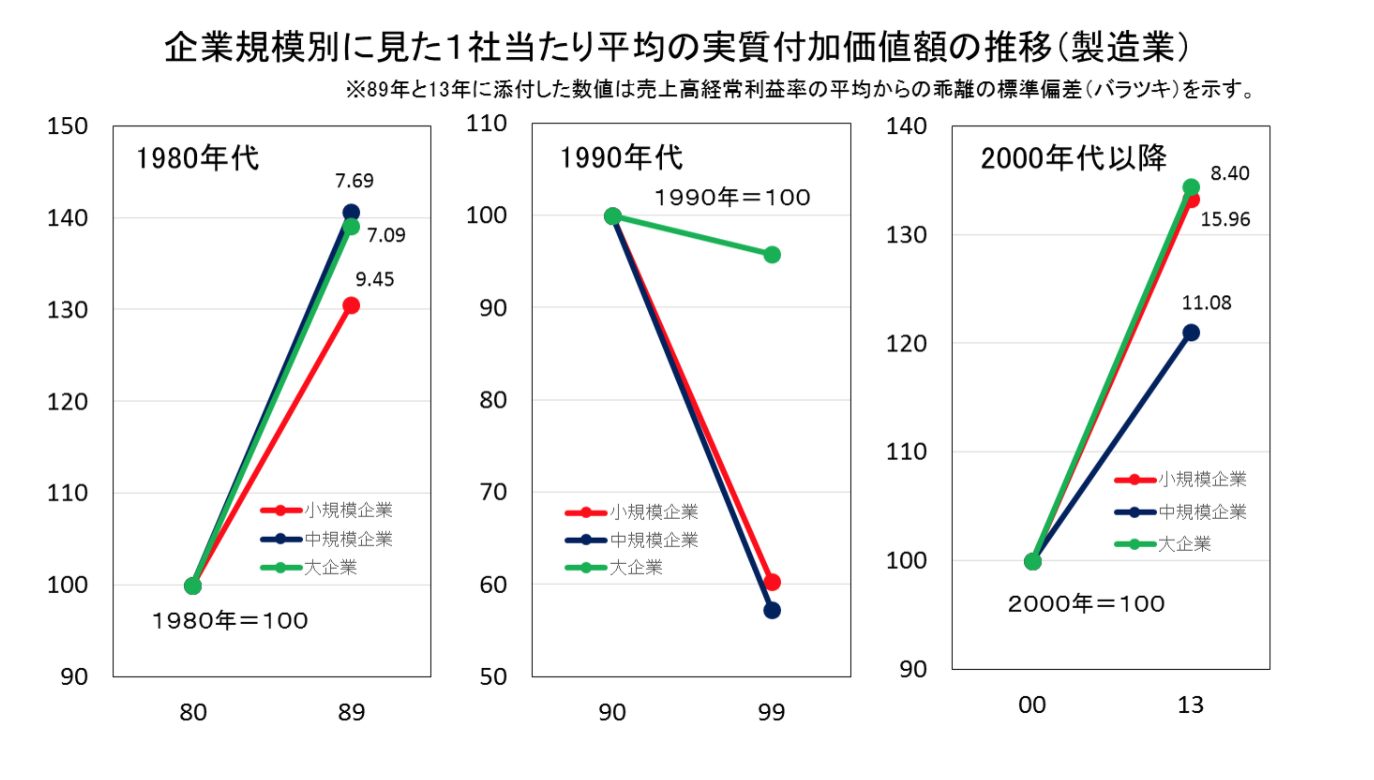
1980年代、1990年代、2000年代以降の3つの期間のデータです。指数化して数値の変化を年代ごとに比較しています。
また、89年と13年に添付している数値はその年近辺での売上高経常利益率の平均からの標準偏差を示しています。数値が増えればバラツキが大きくなったと相対比較して下さい。
これらのグラフを見ると興味深い傾向が見られます。
1980年代は大企業も中小企業も共に成長していました。
1990年代は大企業が底堅く推移する一方、中小企業は大きくマイナス成長でした。
2000年代は再び、大企業も中小企業も共に成長しています。
中小企業は、1980年代に下請け構造の下で大企業と共に成長できました。
しかし1990年代には大企業との取引関係の希薄化が進んだ結果、マイナスに。そして2000年代以降、中小企業の自助努力で付加価値を拡大させています。
ただし1980年代とは異なり、大企業との取引希薄化が進み市場と直接向き合う必要が出てきています。
その結果、市場の不確実性のもと高収益率を達成する企業とそうでない企業との格差は1980年代に比べて拡大しています。格差の拡大は、売上高形状利益率の標準偏差(バラツキ)増加によって確認できます。
つまり2000年代に入って国内中小企業モノづくり工場では、市場構造の変化に対応するために自助努力で付加価値拡大を図っているのです。
しかしながら、上手くやっているところとそうでないところの差は広がっています。すでに市場は変化しているのです。変化に対応し、付加価値を拡大していくためには仕組みが不可欠です。
皆さんの工場では仕組みを構築・定着させ、変化への対応を図っていますか?仕組みを構築・定着させるため、工場運営や工場経営のやり方を見直しましょう。
まとめ
経営環境の変化に対応し、付加価値を拡大させるためには仕組みが不可欠である。