でもやっぱり重要な生産性を決める3つの要因とは
生産性を3つの要因に分解すると活動の焦点がハッキリする、という話です。
生産性はどのような要因に影響されるのか整理されていますか?
現場の作業時間の内訳はしっかり定義されていますか?
生産性は生産方式効率、作業能率、稼働率の3つの要因に影響されます。
(インプットを「労働量」としている場合)
インプットになる作業時間の内訳をしっかり定義しておく必要があります。
1.工場のパフォーマンスを「太さ」や「効率」で測る
生産性を向上させても、現金を増やすことにつながらないことがあります。
したがって、事前に5つの正攻法に照らし合わせ、事前に、活動の目的をハッキリさせる必要があります。
インプットに「労働量(人・時間)」を適用するケースでは特にそうです。
インプットに「労働量」を適用した生産性は、しばしば現場で活用されます。
工場のパフォーマンスを評価する指標として現場も理解しやすいです。
なにせインプットが自分たちそのものなのですから。
生産性 = 生産量 ÷ 工数(人・時)
上式の生産性は工場のパフォーマンスを評価する指標として使えます。
現場も理解しやすい指標です。
ところで、工場のパフォーマンスを評価する指標には「付加価値額」がありました。
そして、存続と成長のためには付加価値の拡大が欠かせません。
したがって工場全体でその絶対額をふやしたい!!という気分になります。
この指標はその気分を反映させています。
ただ、それだけでは不十分です。
経営資源には限りがあります。
効果的にヒト、モノ、カネをつかって現金(キャッシュ)を獲得しようという姿勢も大事です。
したがって、工場のパフォーマンスは絶対額と生産性の2つ側面から評価します。
工場の生産活動を「鳥の目」で俯瞰し、お金の「太さ」と「効率」で考えました。
2.管理者や経営者の方が目を光らせるべきはインプット
仕事の成果として、アウトプットへは目が行きやすいです。
華々しい“成果”ですから、まずは喜びたくなります。
ただ、同時に欠かせないのが、インプットの増減への認識です。
同じ成果を得ても、そこへ投入した経営資源が100の時と80の時では工場のパフォーマンスが当然、違ってきます。
工場のパフォーマンスを見る時、絶対額である太さをまず意識します。
それと同時に生産性で表現される効率に注目します。
効率が悪化した時には、特にインプットの規模を確認しなければなりません。
自社工場へ投入された貴重な経営資源の規模が適正なのか否かを判断します。
3.生産性を考える前に、投入する経営資源(工数)に目を光らせる
現場の生産性を下記で定義します。
生産性 = 生産量 ÷ 工数(人・時)
アウトプットとなっている生産量は出来高と考えます。
ここでは1個、2個とか1台、2台と数えられる製品をイメージします。
一方、インプットの工数を計測するには、作業者の作業時間の内訳を定義することから始めます。
作業者の作業時間の定義は、当然、工場によって異なります。
あくまで、その工場で「継続して」計測できること、管理ができること、が重要です。
ここに作業者Aさんがいます。
Aさんは現場のNC旋盤加工機の担当者です。
Aさんの所定労働時間の内訳を下図で示します。(岡本清著 原価計算 六訂版p.138参照して作成)
所定労働時間より昼休みや午前、午後の定時休憩時間を除いた時間が就業時間です。
そのうち、停電や機械故障、会社都度等で生産活動できなかった時間が手待時間です。
就業時間から手待ち時間を除いた残りが実労働時間です。
「Aさんの管理責任以外の理由」で発生した出来事分を、まず除いています。
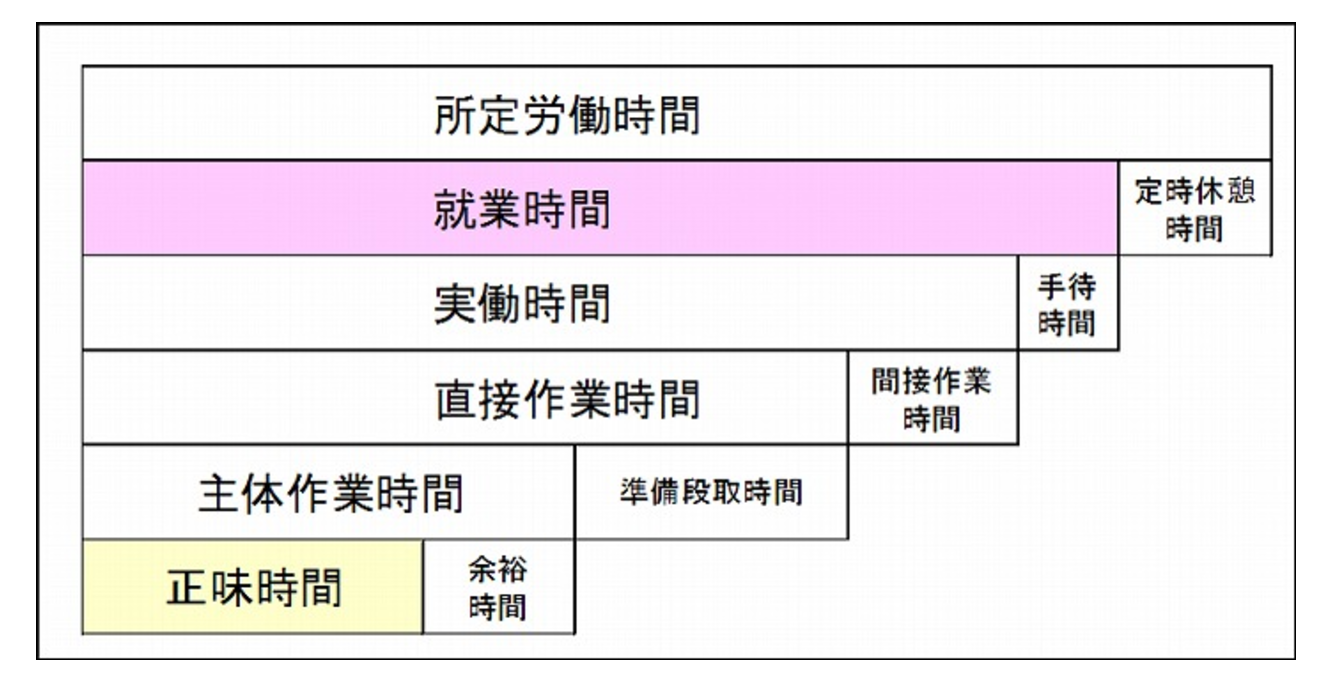
ここから先は、Aさんの管理責任内の時間です。
実働時間は直接作業時間と間接作業時間に分けられます。
直接と間接を切り分ける判断基準は、Aさんの本業であるNC旋盤加工作業と関係しているか、していないか、です。
本業をするためには必要だが、生産活動とは直接には無関係な修繕作業や運搬作業、清掃作業等は間接作業です。
さらに、直接作業は主体作業時間と準備段取時間で構成されます。
そして、主体作業時間は、正味時間と余裕時間に分かれます。
余裕時間は、作業開始の準備や図面確認、作業中のトイレ、水飲み等です。
これらの分類に絶対的な定義はありません。
狙いや目的を持って定義・分類します。
ここでは、NC旋盤加工機が自動運転で原材料を実際に切削加工している時間が
正味時間です。クリーム色の部分です。
また、工数(人・時)は就業時間で計測するのが一般的です。
定時休憩時間を除いたうえで、NC旋盤加工機を稼働させようと思えば、稼働させられる時間、と考えます。
ピンク色の部分です。
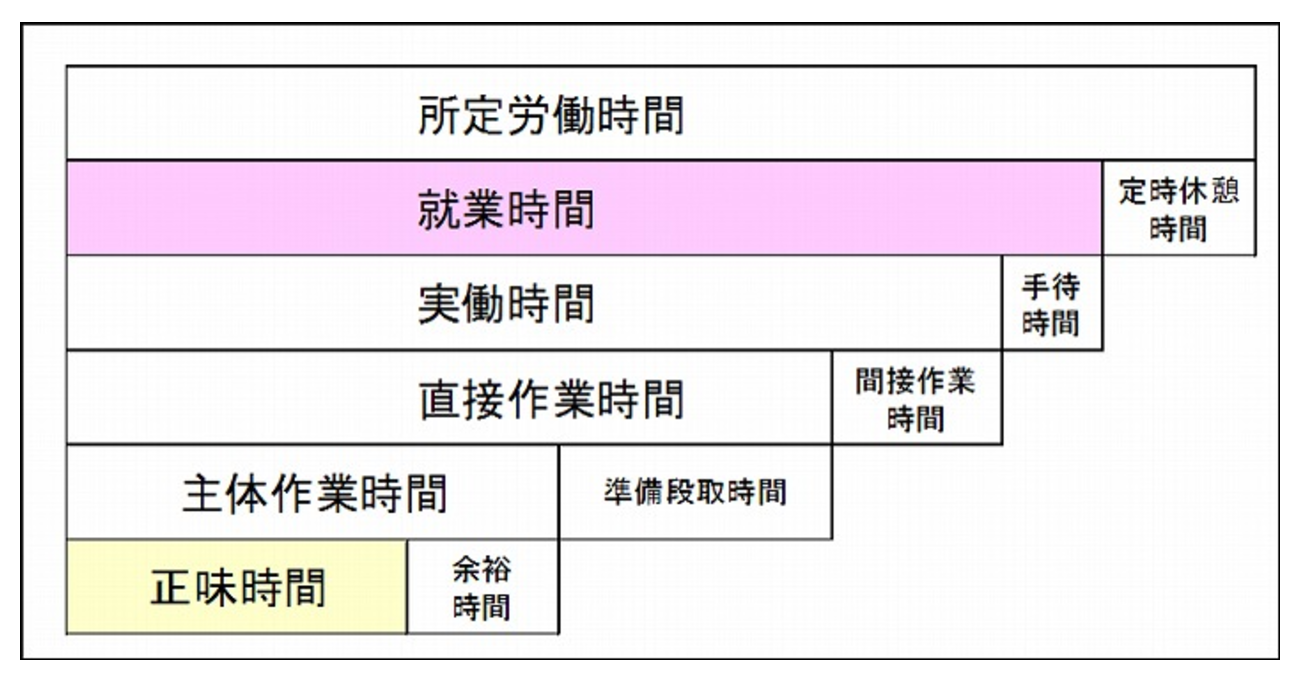
インプットを「労働量」した生産性では、作業時間の内訳の分類・定義が大切です。
生産性の結果を受けて、具体的なアクションを考えますが、適切な判断ができるか否かは、この分類・定義の適正さ、わかりやすさ次第です。
Aさんの仕事は、NC旋盤加工機を自動運転させてナンボノモノです。
上図を眺めて、不稼働要因が色々あることに、改めて気が付きます。
就業時間に占める正味時間を最大化することが、経営者の重要なテーマのひとつであることにも思い至ります。
4.生産性を決める3つの要因について考える
Aさんが担当しているNC旋盤加工工程の生産性を定義します。
定義を単純化すためにNC旋盤加工工程はAさん1人で設備1台とします。
工数は下記のように定義されます。
工数(人・時) = 1(人)×就業時間(時)
所定労働時間が8時間で定時休憩時間が1時間あれば就業時間は7時間。
したがって、この場合、工数(人・時)=7(人・時)です。
Aさんの仕事上の持ち時間です。
1人分の労働量(工数)に注目しているので、ここでは表現上、分かりやすく「作業時間」と表記します。
生産性 = 生産量 ÷ 工数(人・時)= 生産量 ÷ 作業時間
となります。
そして、この式を「正味時間」と「直接作業時間」で分解します。
3つの項に分解できます。
(1)生産方式効率
(2)作業能率
(3)稼働率
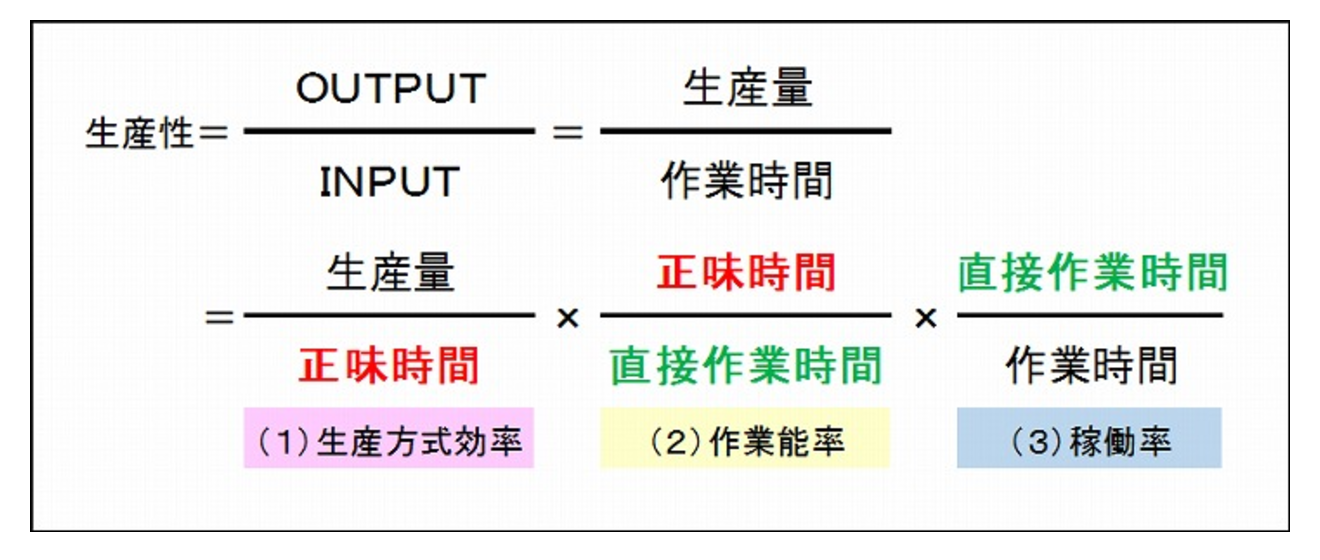
投入する経営資源として「労働量」の作業時間に注目した場合、生産性は3つの要因に影響されることが分かります。
そして、それぞれの要因をどうすればイイでしょうか。
(1)生産方式効率
自動運転開始後、加工機にはサクサク動いてもらいドンドン加工してもらいます。
生産法方式によって決定される効率です。
技術的な要因によって決まります。
Aさんがこの効率を上げるには、送り速度を早くする、空転時間を短くする等の
技術的課題への対応が必要になります。
技術者の支援が必要であり、Aさん1人で対応するのは難しいです。
(2)作業能率
直接作業時間に占める正味時間を長くすることです。
具体的には、主に段取り時間の短縮です。
治工具交換時間を短くしたり、内段取りの外段取り化などが考えられます。
主体作業で“流れるように”仕事を進めるため、5Sを徹底するのも手です。
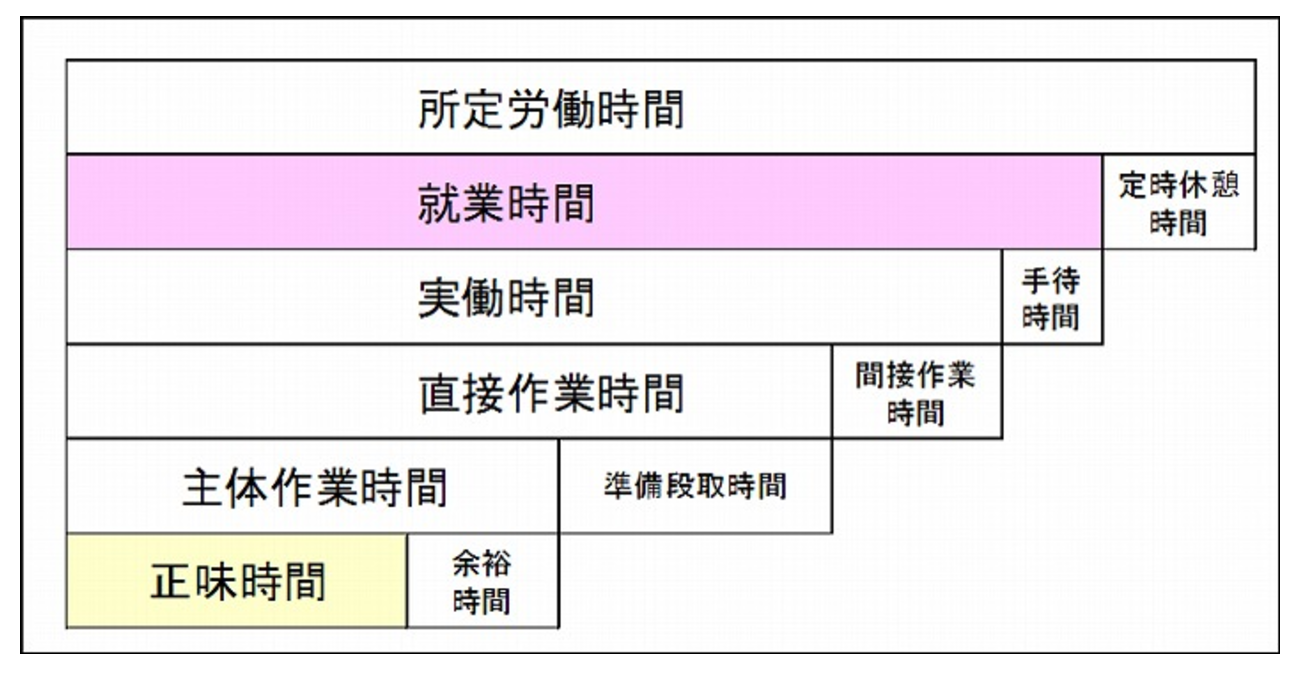
(3)稼働率
手待ち時間や間接作業時間を最小化することです。機械故障や材料運搬等、生産に無関係な時間をなくします。
起こってから対応! ではなく、起こる前に対応! する(すべき)事項が中心です。
問題は未然に防ぐもの、という発想になるかどうかです。
5.生産性を工場パフォーマンスの指標に使う
生産性を決めるのは3つの要因です。
よって、生産性が悪化した場合、3つのうちのどれかが悪化したことになります。
指標の変化に気づくことで、原因の特定もしやすくなります。
付加価値の絶対額と生産性の両方で工場全体のパフォーマンスを評価します。
効率にも目を光らせます。つまり、適正なインプットになっているか否か、判断します。
また、カイゼンで「労働量」をインプットに定義した生産性を取り上げ、その生産性の向上を狙った場合でも、役に立ちます。
この3つの要因のうち、どれを向上させて生産性を良くしようとしているのか、事前に、はっきりさせられるからです。
その結果、取り組みの位置づけを、現場と管理者で共有することができます。
判断基準が明確になっていると、現場の成果を客観的に評価できます。
評価の納得性が高まります。つまり、現場のやる気を引き出すことができます。
工場運営の本質は人に働きかけること。
現場のやる気を引き出す工場運営が、もうかり続ける工場経営を可能にします。
まとめ。
生産性は、生産方式効率、作業能率、稼働率の3つの要因に影響される。
(インプットを「労働量」としている場合)
インプットになる作業時間の内訳をしっかり定義しておく必要がある。
生産性を3つの要因に分解すると活動の焦点がハッキリする。