「標準化」は生産性を向上させるためにも絶対必要だ
生産性を向上させるためにも標準化という作業は欠かせない、という話です。
生産性を向上させるためにも必要な標準化を進めていますか?
生産性を向上させる3つの要因のうち生産方式効率と作業能率では、標準時間を設定することで目標が明確になります。
稼働率は、現場だけでは解決できない問題点が影響している場合があります。
1.生産性と標準化
生産性は、(1)生産方式効率、(2)作業能率、(3)稼働率の3つの要因で決まります。
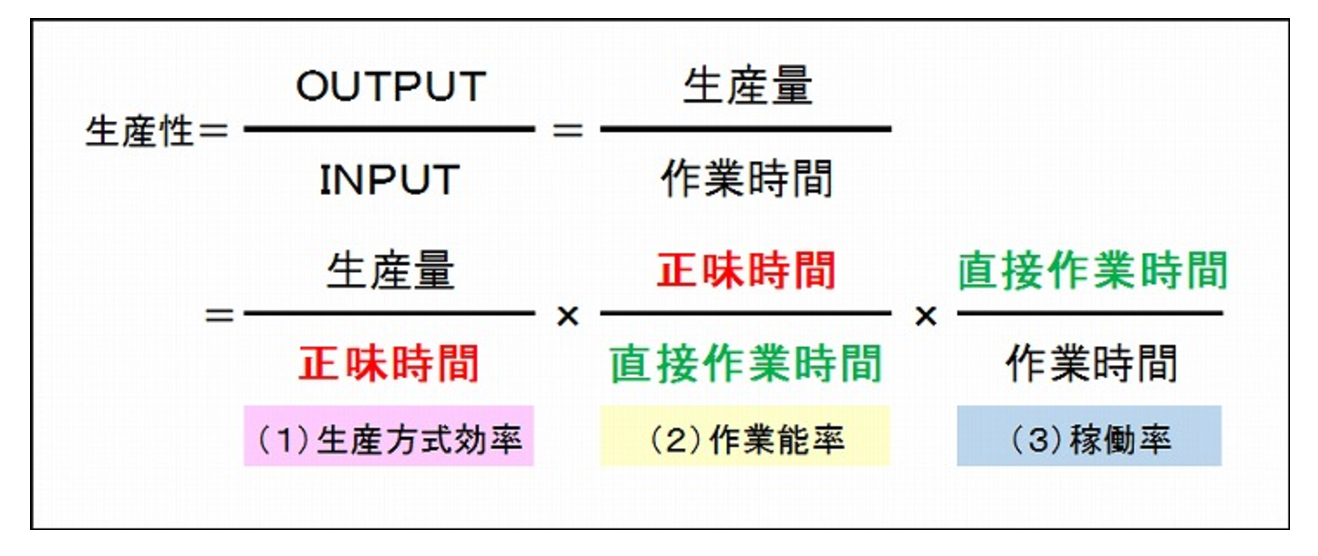
そして、作業時間内訳の図を眺めると、各項目で何をすべきか見えてきます。
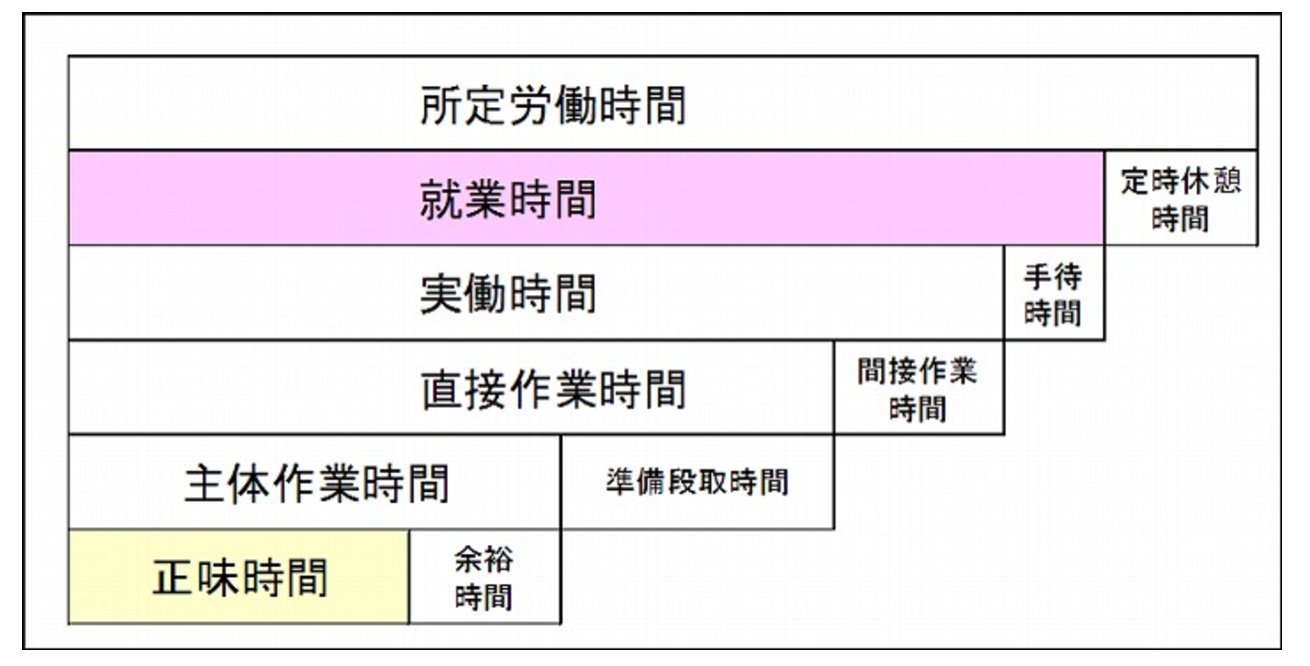
さて、現場へ生産性を向上させるために、現場へ指示を出すケースを想定します。
この場合、各項目の目標値があると、現場の動機づけが図られます。
「現場は、今よりも作業能率をあげるように。」とだけ現場へ指示する場合。
「作業能率は現在◯◯だけど、それを○○まで上げて欲しい。なぜなら、生産性を◯◯から○○へ上げたいから。生産性を上げると……」と全体目標も含め、目標値を加えて指示した場合。
両者の比較します。
定量的な指示は説得力があり、納得感が高まります。
現場は指示の内容を納得したいと思っています。
納得感があれば、自発的に取り組めます。
それがなければ、同じ指示でも「ヤラサレ感」たっぷりです。
そして、その目標値を設定するためには、標準化が必要です。
1-1.生産方式効率と標準時間
生産方式効率は生産設備が正常稼働している時の生産量で表現されます。
1時間当たり何個とか、1分間当たり何個とか。
「正常稼働」とは多くの場合、自動サイクル運転している時と言い換えられます。
一般的に、生産方式効率は「要素技術と生産条件」によって決定されます。
技術的な要因で決定され、これが標準値になります。
こうして決定された標準値と実績値を比較して、技術的な問題点を洗い出します。
製造プロセスによっては製造条件が安定しない場合もあります。
現場でトラブった認識は無いのにも関わらず、「自然に」生産タクトが長くなったり、良品率が低下したり。
チョコ停なんかも注意すべき事項です。
現場は、とにかく稼働を停止しないように頑張ります。
チョコ停程度のトラブルならば、現場自ら対応して生産を継続しようとします。
こんなことがありました。金型鋳造で自動車部品を製造するラインでした。
生産タクトが2分程度(120秒)で、毎日4時間(14,400秒)程度稼働です。
14,400÷120=120個
稼働率、良品率100%ということは無いので100〜110個の生産でした。
あるとき、設備トラブルの報告が特になかったのに、生産量が90個程度に低下したことがありました。
原因を調べてみました。
ショット毎に、金型に付着したバリを除去する作業をしていることが分かりました。
生産タクトの標準時間120秒に対して10秒の作業が加わり130秒となった。
作業者は何とか生産を続けようとして10秒の作業を加えながらも頑張っていた。
10秒程度なら、まぁ、なんとかなるとの思いもあったが、結果として……。
生産性から判断すると8%のダウン。
標準があって、初めてこのような客観的な判断ができます。
1-2.作業効率と標準時間
現場で付加価値を生み出す時間は正味時間のみです。
それ以外の時間では、作業者自身がどんなに力んでも、汗を書いても、残念ながら、付加価値は生み出されません。
まずは、この意識を現場全体が共有します。
ですから、とにかく生産に関わっている直接作業を磨き上げます。
直接作業時間に占める正味時間の最大化を図ります。
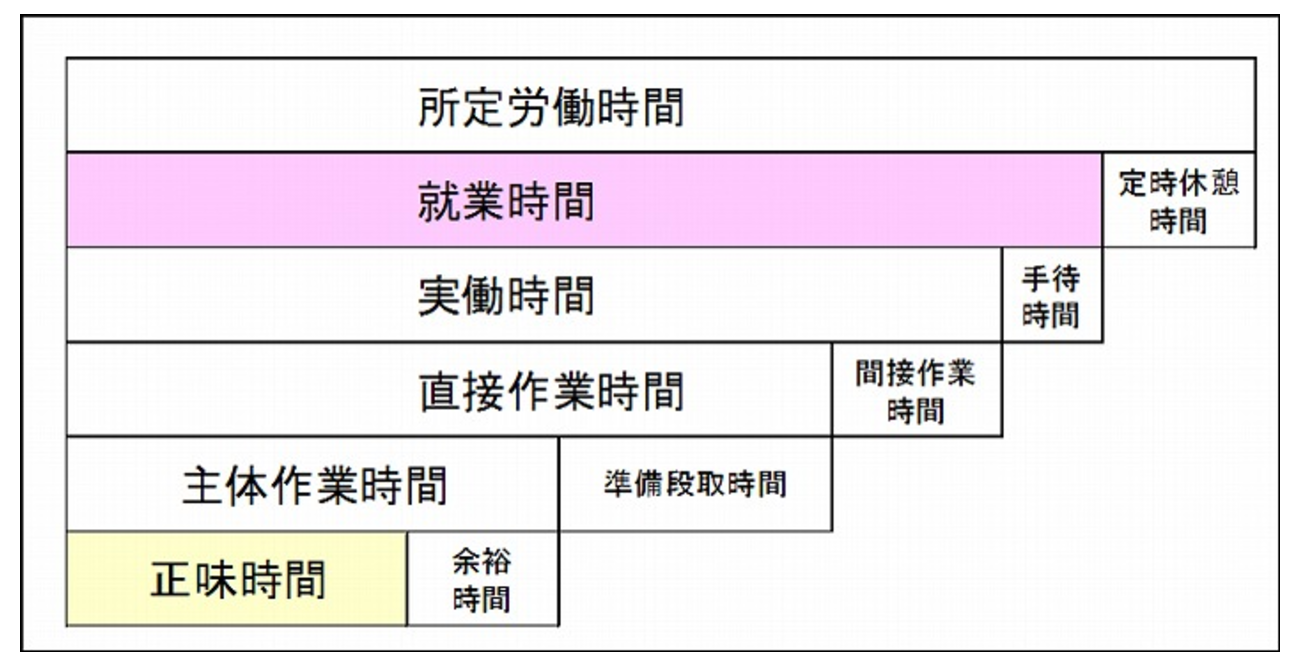
現場の5Sは十分に為されているとして、ここで主テーマになるのは段取り作業です。
ですから、段取り作業の標準を設定することが必要です。
ところで、段取り作業は現場ノウハウの塊です。
トヨタもシングル段取り目指して長年強化してきました。
ここに固有技術の強みの一端が現われます。
そこで、作業内容を云々する前に、まず、実績時間を集計することから始めます。
現場のノウハウが詰まった段取り作業の実態を正確に把握するためです。
実績時間の平均値とバラツキから、標準的な段取り時間を設定します。
そして、設定した標準時間で段取り作業を管理します。
状況を把握できた時点で、段取り作業にメスを入れます。
内段取りの外段取り化、内段取り時間の短縮と進めるのが王道です。
ここから、「標準的な段取り作業」の検討に入ります。
段取り作業は現場の永遠の課題です。
そして、標準があって初めて、継続的な取り組みが可能になります。
まず、付加価値を生み出す時間は正味時間のみであることを理解します。そうすれば、現場も段取作業をどうすべきか自然と見えてきます。
1-3.稼働率では経営者の判断も必要
不稼働時間となる手待時間および間接作業時間は、最小化すればイイことに気が付きます。
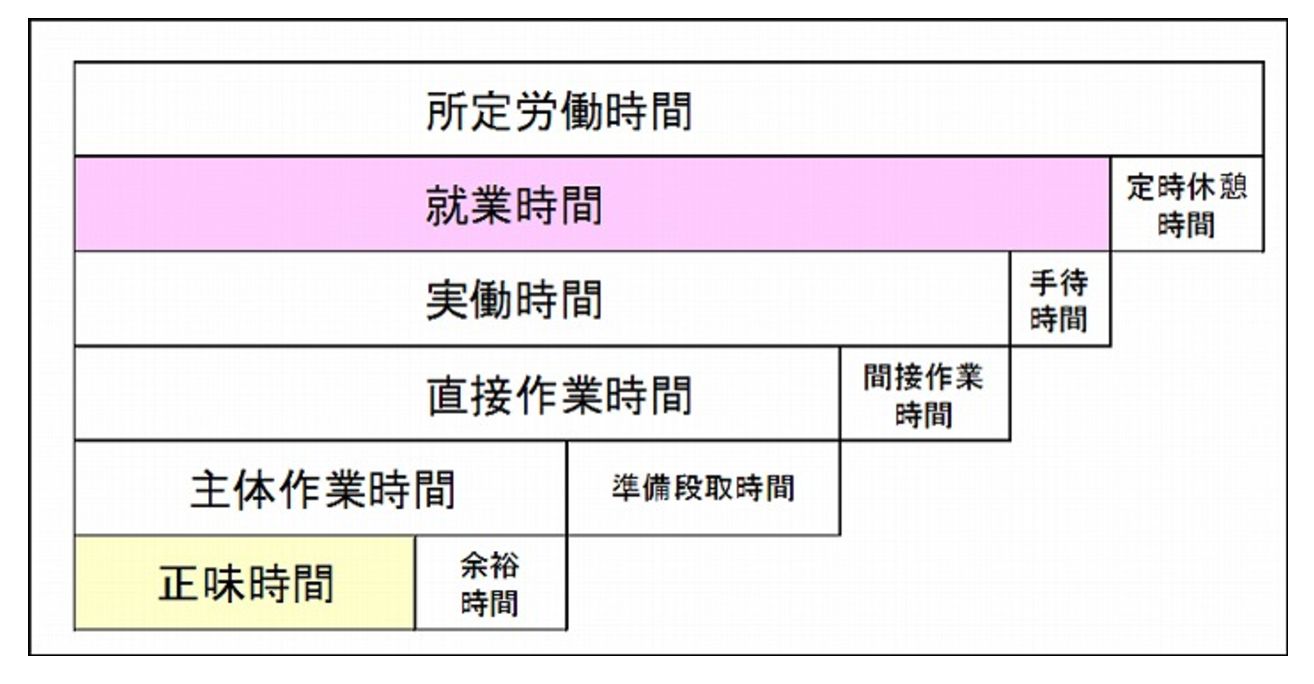
ではどのようにして最小化を図るか?
この項目は標準化とは少々違った視点が必要です。
この項目では、主に現場担当者の管理外で起きる出来事が起因しています。
工場全体に関係する事項、あるいは上司からの指示に関係する事項です。
ですから工場全体を取りまとめる現場リーダーの出番です。
仕掛品や製品の置き場所の確保、あるいは仕掛品や製品の搬送、こうしたことに多くの時間が、割かれていることがあります。
機能別にレイアウトされた工場で多くみられる事例です。
原因は仕掛品、製品の保管、搬送に関するルールがないこと、そもそも工場のスペースが不足していること。
これを現場で解決することは不可能です。
現場リーダーから状況を十分にヒアリングした上で経営者自身が解決方法を指示します。
経営者でなければ絶対に解決しない問題も現場にあるからです。
工場のスペース問題は工場の大小を問わず必ずあります。
管理者の仕事にスペース問題に関することは意外と多いです。
ですから、工場スペースを確保する取り組みは大いにあります。
全社一斉に取り組めば、期待以上の効果が得られます。
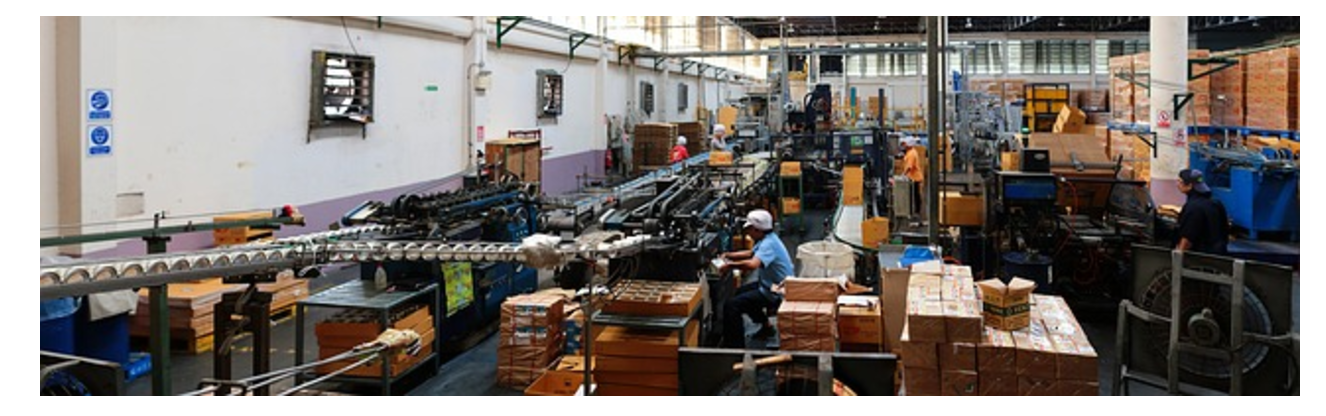
また、上司から現場への指示に関係して、注意を要するコトがあります。
それは、現場に対して新たな作業を指示したら、その分、なんらかの現場業務を省くことをセットで考えるということです。
こんなことがありました。
新たな生産ラインが立ち上がった頃の話です。
新たに立ち上がった生産ラインでは、まず体制を構築する必要があります。
生産実績、品質、設備稼働、等々多岐にわたる管理項目を設定します。
このラインでは新生産プロセスが導入されたこともあり、従来にはない管理ポイントが多数ありました。
また、立ち上がったばかりで、様々な実績を記録して様子を観ることも必要でした。
そこで、現場責任者へドンドン指示を出しました。
ある時、段取り作業の開始が遅れていることに気が付きました。
現場の作業者が手持無沙汰で立っているので、「何やってんだ?」と聞くと、いっしょに段取り作業をするはずの現場責任者がまだ来ないから、との答え。
そこで、現場詰所へ足を運ぶと、当の本人は何やら資料をまとめているところでした。
なんてことはない、私自身が、今日までにまとめておいてと依頼をしていた不稼働要因実績の整理を、一生懸命にやっていました。
「こっちはイイから、早く段取りを」と指示した次第。
管理者として反省でした。
必要だからとは言え、本業に影響を及ぼす程まで、現場へ指示を加えてはダメです。
マーケティングの品揃え戦略と同じです。
増やしたら、何かを減らす。
店舗における商品の展示スペースは一定です。
限られたスペースをいかに有効に使うかというのが品揃え戦略。
現場への指示も全く同じです。
管理者として十分に配慮しなければならないことです。
現場の不稼働時間で、こうした生産に直接関係のない指示によるモノがないか。
そして、それを省くにはどうしたらイイかを考えます。
稼働率に関しては、不稼働要因を整理し、必要な手を打ちます。
ただし、不稼働要因の中には、将来生み出される付加価値への種まきもあります。
ですから、その可否は経営者も考えます。
まとめ。
生産性を向上させるために必要な標準化を進めていますか?
生産性を向上させる3つの要因のうち生産方式効率と作業能率では標準時間を設定することで目標が明確になる。
稼働率は現場だけでは解決できない問題点が影響している場合もあるので配慮する。
生産性を向上させるためにも標準化という作業は欠かせない。