品質問題の未然防止はどこまで叶うか
製造業の品質課題
ずっと以前からモノづくりで取り組まれてきたテーマ ~品質問題の未然防止~
信頼性保証、源流管理、なぜなぜ分析、FMEA、DRBFM、SQC、デザインレビュー、ゼロディフェクト活動、TQM、ISO9001、シックスシグマ、…など
製造業では、過去からいろんな試みがなされてきた。
で、品質事故はなくなったか?
否、なくなっていない。
むしろ、一般的に品質事故が増えている。
経験値が蓄積されてきたにもかかわらずである。
製品システムの複雑化、開発期間の短縮、コスト削減や人手不足によって誘発されたもの、等、理由はいろいろある。
では、当社の場合はどうか
確かに経験が蓄積されて、同じ類の事故は減った。
しかし、新たに発生した事故もある。
最近あった顧客の使用条件とのマッチングの問題。
当社の主力製品セラミックコンデンサーでの話。
ディスコンによる原料メーカーの変更。
技術者によって、新たな原料メーカーの原料を使って配合~混合~焼成と製造条件の最適化が行われた。
これに対する製品評価として、材料特性、電極を付与してメカニカル特性、電気特性、信頼性試験と一通りのパフォーマンス試験を経て、DRBFMを通過し、製品化された。
当社未然防止手順のフルコースである。
顧客にPCN(生産条件変更)申請して承認を待った。
数ある顧客評価の中で一社だけ、耐湿負荷試験で問題が生じた。
当社のスペックは、MIL-PRF-49464準拠の85℃x85%RHx1.3Vx240Hrで所定の特性変化量に抑えること。
問題が生じた顧客の電圧と試験時間が当社のスペックを超えていた。
スペック外なので、保証できないと言えばそれで済む話なのだが。
顧客の言い分は、変更前のコンデンサーはクリアした、である。
これを未然防止することは難しい。
評価時点でスペックを超えたデータ取りが必要になり、しかもどこまで範囲を広げればいいのかわからない。
顧客の評価まで含めて未然防止手順と考えれば、量産事故には至っていないので最悪なケースは回避できているが。
だが、開発段階で発見しないと後戻りが難しい。
今後どうすべきか
品質評価のデータベースにこの経験が蓄積される。
同じ轍(この条件のNG)は踏まないが、顧客が変われば別のマッチング問題が生じるリスクは残る。
変更しないことが一番のリスク回避なのはわかるが、変更せざるを得ないことがままある。
変更リスク対策はトライアンドエラーしかないのか。
品質問題の未然防止は、神のなせる業なのかもしれない。
それでも次の手を考えるしかない。
立ち止まらないことこそが未然防止への道と信じて。
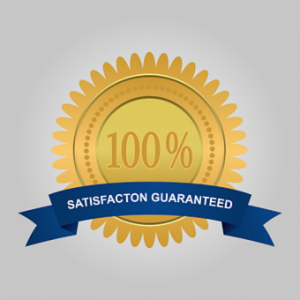