セブ工場での「新規量産品のハンドリング」と「量産工程改善」。赴任10か月目の実務と経験。
まえがき
私事ですが、この4月で入社3年目となりました。
2018年8月よりTECDIAの製造拠点であるCMI(Cebu Micro Electronics Inc.)に赴任し、セラミックス回路基板等の①新規量産品のハンドリング及び②量産工程改善のお仕事をしています。
海外での生活はあっという間(個人の感想)でCMIに赴任してから早10カ月が経過しました。
今回はCMIでの私の実務と経験について過去の先輩方の投稿を引用しながら紹介させて頂きます。
TECDIAについて
私の実務に関してお話するにあたり、先ずTECDIAについて簡単に説明させて頂きます。
TECDIAの本社は東京都港区芝浦にあります。
本社にもCMIと同クラスのクリーンルームがあり、事業拠点であると同時に開発拠点という役割も担っています。
本社では短納期で少量多品種のサンプルをお客様へ出荷しており、納期は仕様にもよりますが最短でPO受領から1週間での生産・検査・出荷が可能です。
弊社HP: 製品試作に必要な、薄膜回路基板を最短「1週間」で納品
上記はCMIでの量産の足がかりともなっており、出荷後にお客様にサンプルを評価して頂き、CMIでの量産対応へと展開する場合もあります。
本社での少量生産に際しては関係者間でDR(デザインレビュー)を行い、性能や信頼性、価格や納期、検査基準について、設計・品証・製造関係者等で擦り合せを行います。
私のお仕事は少量生産を終え、新規量産が決まった型番のCMIでの量産展開と量産開始後の工程を維持・改善することです。
業務①新規量産品のハンドリング
・その1-初回生産へ向けた準備
本社での少量生産時のデータを元に関係者(設計・生産・品証 等)
を交えDRBFMを実施します。CMIでの初回生産へ向けた準備です。
DRBFM実施の流れは以下の通りです。
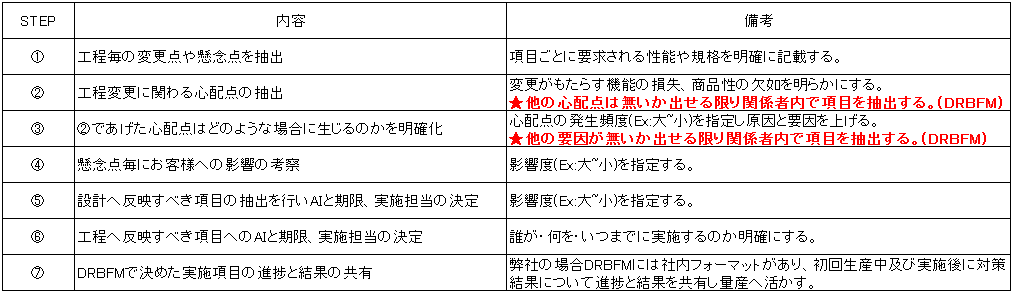
★がDRBFMに重要な要素であり、設計・製造・生産技術・品質保証・検査等の様々な役割を担う人間が出せる限りの懸念点や要因を出し合います。
DRBFMの最大の目的は品質トラブルを起こさないことであり、生産にあたり根幹となる設計及びその後の工程に品質的問題が無いかを多角的に議論するものです。
設計時や工程適用時などもを含め、1つの製品立ち上げのために複数回実施されます。
・その2-量産立ち上げと初期流動管理
量産開始後の初期段階では工程が安定しなかったり不具合が発生しやすかったりすることがあります。
開発・設計段階での見落としが量産後に問題となることもあり、生産状況が安定するまでは工程内での情報を収集し管理・改善する体制をつくります。
初期流動管理時には全数検査の実施や抜き取り検査数を増やす、薬品や治具の交換時期を早める等、工程が安定するまで特別な管理を行います。
工程設計及び変更時にDRやDRBFMなどの会議を設けて机上でレビューし、初期流動での量産立ち上げ時に工程と製品でレビューするというような仕組みです。
計画された品質計画の妥当性を工程と製品で確認し評価します。
生産の仕組みと品質・工程管理について
CMIでの部材の管理や設備管理、工程・検査作業などは現地のフィリピン人達に実施して頂きます。
彼らの仕事には作業標準書というドキュメントがあり彼らはその記載通り各々の作業を遂行します。
私が携わっている製造の現場だけでもドキュメントの種類は膨大です。
少し例を上げると、装置の使用・点検方法や工程の作業内容、薬品の使用方法や廃棄方法、検査規格の説明と検査時の顕微鏡の倍率等々多岐にわたります。
そして、1つの製品の生産に対しても多くのドキュメントが適用されており、製造の現場では作業標準書はQC工程表に紐付けて運用されます。
引用: QC工程表
QC工程表には下記の様な項目と内容が記載されています。
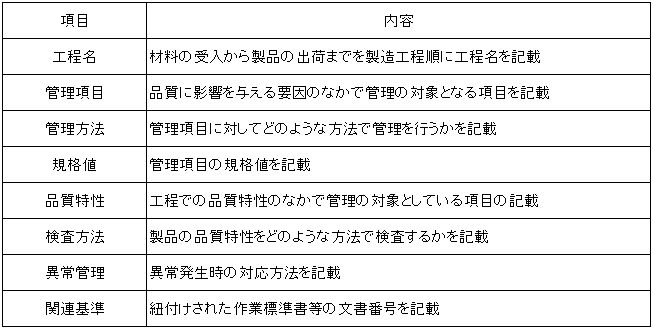
QC工程表と作業標準書は対になっており、QC工程表で工程毎の品質に関わる項目と品質特性の検査・管理基準等を明確化し、作業標準書で作業手順が詳細に説明されています。
製造現場では製品毎に作成されたQC工程表を基に品質と工程を管理し、作業標準書の運用で作業者が正しく工程作業を実施します。
*作業標準書 = 初めてそのドキュメントを見た人でも、参照すれば全ての作業が実施できるように詳細な記載がされている。作業者は教育と研修を経て各工程のライセンスを所持しているが、ドキュメントの内容に不備や曖昧な表現があってはならない。(不良につながるため。) 工程に変更があれば改版を実施し、関係者の承認を経て内容が刷新される。
業務②量産工程改善
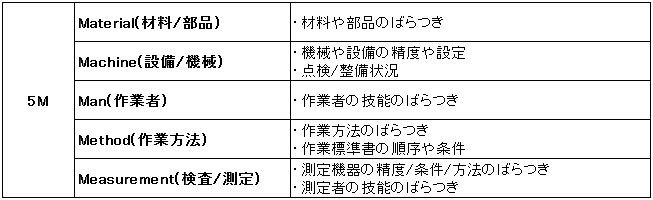
量産が開始され初期流動管理が終了してからは生産性や歩留りの向上を図り原価低減(利益向上)を行う必要があります。
今期、CMI1年生の私は現地のエンジニアと協業し幾つかの歩留まり改善に取り組みました。
未熟な私が現地で改善を行う中で大切だと感じたことが幾つかありますが、今回は3つに絞り記載します。
1. 改善活動(プロジェクト)の明確化
改善を行う主担当が私自身であっても、現地エンジニアやスタッフに作業やデータの取得・アレンジを依頼することが多々ありました。
私個人で不良に対する問題の定義や、これから行う調査及びデータ取り等の内容が明確になっていても、彼らに上手に共有しないことで認識の不一致や効率の悪さが露呈しました。(言語の壁も赴任当初はありました。)
改善を行う時には資料を作成し、関係者に対してプロジェクトの定義と目的、内容を明確にすることが大切です。その際にも工夫は必要で、一般に言う5W1Hが重要となります。
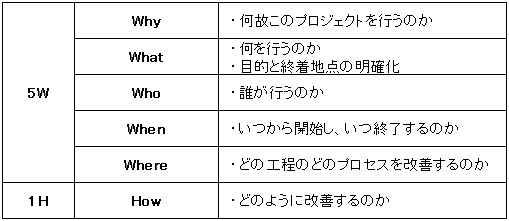
ざっくり上記の項目は活動開始前に共有すべき項目ではないでしょうか。
ただ業務を依頼するだけ、依頼されるだけの関係では良い改善活動は行われません。
依頼された業務に趣旨や目的が付随していないためです。依頼される側のやりがいが見出せないと感じます。
彼らの目線に立ち、協力を仰ぐことが必要不可欠です。
5W1Hの工夫とプロジェクトの定義付けにより活きた情報が多く自分の下へ集約されることを実感しました。
2. Phase毎のレビューと定期的な進捗共有
5W1Hの工夫を凝らしてプロジェクトのタイムラインを作成し関係者間へ共有します。
大切なことは各Phaseで結果をレビューし、関係者からのフィードバックを得ることです。
プロジェクトの進捗や得られた結果からスケジュールの遅延や前倒し、追加調査や新たな取り組みが必要となる場合があるからです。
Phase毎のレビュー以外にも毎朝行うプロジェクトの進捗確認等の実施で無駄無くプロジェクトが遂行していくように感じました。
3. 多角的視点で現場を見る & 様々な変化点に着目
現場でのNGの要因には多くのファクターがあり何か1つ変化することによって現象が変わってしまうものです。
品質管理などについて述べる時に「5Mを管理する。」という言葉を耳にしますが、製造でも現場の変化点には常に注意を払わねばなりません。
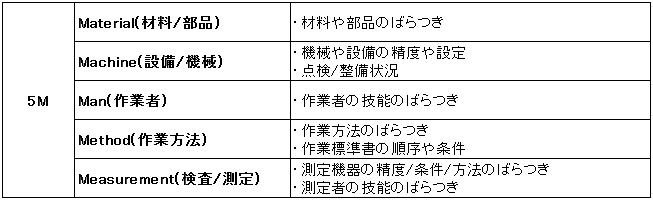
上記以外にも環境の変化などに注意し、現場の温度や湿度等の環境が材料や機械・設備、または作業条件や検査・測定条件等に影響を及ぼしていないか確認する必要があります。
現場に身を置き、現場を観て、現象を確認することが大切です。
そして、現場での現象の把握や変化点の分析、対策の立案にはQC7つ道具の活用が効果的でした。
引用: QC7つ道具
例を上げると、CMIでも製品の検査に基づく測定データに管理図が使用され、規格に対しての工程安定度合の管理に用いられています。
また、パレート図はNGを項目ごとに多いものから並べ、影響が多いNGと割合を一目で判断できるため便利です。
QC7つ道具は製造に留まらず多くの分野・業界で活用可能なのではないでしょうか?
おわりに
今回は製造現場での業務と経験について紹介させて頂きました。
次回はCMI1年目に経験した工程改善活動について実際のストーリーを交えつつ紹介できればと思います。
■テクダイヤ技術向上ブログ
テクダイヤの開発・生産に携わる、若手エンジニアによる公式ブログ。技術情報はもちろん、失敗談や体験談など有益な情報を幅広くお伝します。